
- 3DConfigure
- Wet Lab Gallery
- Tech Lab Gallery
- Industrial Furniture Gallery
- Products Gallery
- Verticals Gallery
- Design Workbenches
- Submit Custom Request
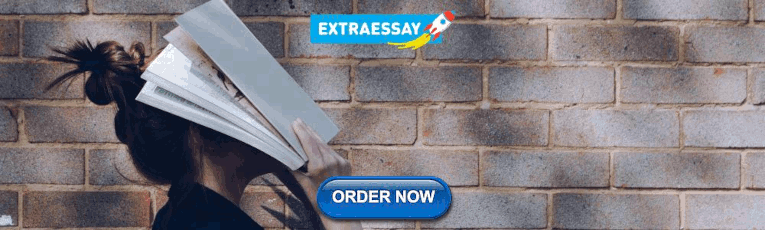
How to Start a Laboratory Business from Scratch
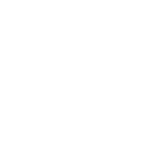
9/30/2020 | 16 Likes | Verticals & Applications , Casework , Chemical Resistant , Cleanroom , ESD Environments , Healthcare , IT & Computers , Monitoring Applications , Pharmaceuticals , Sample Processing , Tech Lab , Wet Lab ,
What can you do to make your new laboratory startup venture a success? We take a look at the top 10 questions everyone should ask themselves before green-lighting a new laboratory venture.

1. What is the Business Case for Your New Laboratory Startup?
Take the time to create a detailed business plan upfront — one that addresses the difficult questions — before expending scarce financial and human resources .
A good place to start is by researching the market demand and identifying the business case for your new venture.
Here are a couple of business case examples – but yours will need to be more detailed, backed up by solid technical and market research.
- To take advantage of new research/testing opportunities, such as those created by the Covid pandemic.
- Use new lab technologies to serve unmet demand in the market by out-competing/displacing other laboratories relying on older technology.
2. Who Needs Your Laboratory Services, e.g. Who is the Customer?
The next step in creating a solid laboratory business plan is to identify “ who is the customer? ”
In reality, there are often multiple answers to this question, so perhaps we should rephrase the question as “ who are the stakeholders? ”
Startup laboratories will need to identify what products and services they are offering to prospective customers in the market place.
But they will also need to treat their investors (e.g. the angel and VC firms making substantial upfront investments) as key stakeholders by delivering on the promises they have made in terms of project milestones and product and service deliveries.

3. What is the Funding Model and Return on Investment (ROI) for Your New Laboratory Project?
In normal times, commercial laboratories with a recurring revenue stream would find answering questions about funding sources and return on investment (ROI) to be fairly straightforward.
However, we don’t live in normal times right now.
The current Covid pandemic has shifted demand across many sectors of the economy, including the lab sector, which makes these economic models and investment calculations more difficult.
For example, demand for clinical healthcare testing (including Covid virus and vaccine trials testing) is up, while demand in other areas (such as petroleum well testing) is down.
This puts additional pressure on lab startups to identify viable funding sources to support the business after the initial funding runs out — by signing long-term customer contracts, obtaining multi-phase government research grants, or pursuing direct sales opportunities, such as direct sales of home testing kits sold to consumers over the internet.
It also puts greater pressure on controlling costs and justifying expenditures.
Fortunately, there are clever, cost-effective solutions available, such as efficient storage and flexible furniture options (such as mobile carts) that can help you get the most use out of your available square footage — while maximizing ROI at the same time.
Some lab startups may also benefit from taking advantage of local startup accelerators, which offer shared workspaces during the early venture stages.
4. Which Regulatory Regimes will Govern Your Laboratory Operations?
Every business is subject to some form of federal, state, or local regulations.
Broadly speaking, most of these regulations have to do with public safety; for example, does your facility meet fire regulations? Is it structurally sound? Are there enough emergency exits? etc.
In contrast, laboratory facilities tend to be highly regulated, often falling under one or more regulatory regimes that are either mandated by government agencies or set forth by industry trade groups that issue “certifications.”
The intended use of your laboratory will determine which sets of regulations or certification guidelines apply.
For example, laboratories designed for pharmaceutical or food manufacturing testing will need to comply with the FDA’s Current Good Manufacturing Practice (cGMP) regulations.
Laboratories designed to handle potentially dangerous materials are subject to even more stringent regulations. Facilities handling radioactive materials must comply with the Department of Energy regulations, while labs handling potentially dangerous biological pathogens fall under CDC biosafety regulations, which classify labs according to four biosafety levels, BSL-1 through BSL-4.
(Only a few laboratories around the world qualify for the BSL-4 rating, designated for handling the most dangerous pathogens. These labs must incorporate highly redundant safety systems, including isolated clean room chambers where lab personnel wear special PPE, such as “spacesuit” type protective garments.)
5. What Kind of Lab Facilities Do You Need to Achieve Your Goals?
Now that we’ve identified the business case, the customer, the funding sources, and the regulatory regimes that govern your new laboratory startup, it’s time for the facility project managers to begin working with the architects and designers to develop a list of “architectural programming requirements“ for the new laboratory.
One useful piece of advice: avoid “reinventing the wheel.”
There are many well-documented laboratory designs that can provide inspiration for your projects. Evaluate as many as you can to identify what would work for you and what you’d like to do differently.
Another useful resource is the publication Forensic Science Laboratories: Handbook for Facility Planning, Design, Construction, and Relocation , published by the National Institute of Standards and Technology (NIST). While (as the title suggests) its focus is forensic science laboratories, it clearly documents a set of best practices for managing laboratory construction projects.
From a design perspective, laboratory facilities generally include one or more of these components:
In the language of laboratory design, wet labs are the areas that handle liquid chemicals. Designers need to pay particular attention to specifying chemically resistant surfaces, a sufficient number of wet sinks (often with their own special waste handling drainage system), as well as fume hoods to protect workers from potential exposure to noxious gases or dangerous particulates.
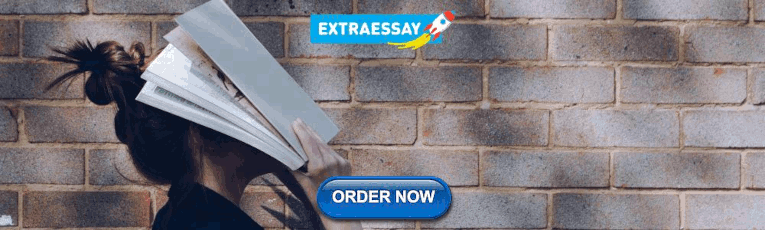
Dry Labs / Tech Labs
The term “dry lab” traditionally refers to laboratory zones that handle dry chemicals in small amounts.
Thanks to the revolution in scientific computing, however, the role of dry labs has expanded tremendously over the past few decades to incorporate computer systems as well. This has led to the rise of the “ tech lab ,” where lab researchers access and manage computer workstations or provide IT services to the organization. The computer systems can be a major source of heat, so these areas will usually need beefed up HVAC systems. Redundant power systems (such as backup generators or batteries) are also typically required.
Laboratory Clean Rooms
An increasing number of laboratories, such as those supporting the manufacture of printing microelectronics onto silicon wafers, require the use of cleanrooms to prevent microparticles from contaminating surfaces or to protect lab personnel from dangerous pathogens.
Electronics Labs
Microelectronics can be damaged by even small amounts of electricity, such as static shocks. Laboratories engaged in prototyping and testing electronic equipment need to be equipped with anti-electrostatic discharge (ESD) systems to prevent inadvertent damage to electronic equipment.
6. How Will Your Laboratory Needs Change Over the Next 10 Years?
Predicting the future is always difficult, but if we were to make one forecast, it would be that change is inevitable.
Laboratory equipment is changing year-by-year, experimental methods are evolving rapidly, and computer-based scientific discovery methods are becoming one of the dominant forces in laboratory science.
So, given that change is inevitable, what can you do today when designing your laboratory to prevent it from becoming obsolete in 10 years?
The answer is to design in flexibility so that you can make changes over time without having to endure the interruptions caused by extensive renovation projects.
It’s this need for flexibility that is driving many laboratory customers toward specifying modular furniture solutions for their new lab projects. Unlike traditional casework installations, modular laboratories are built out of standardized components (including wet sink installations, fume hoods, workbenches, storage units, etc.) that can be installed on-site using ordinary hand tools.
As your needs change in the future, the task of rearranging the modules to meet your current requirements is greatly simplified. If you need to expand, you simply contact the factory (e.g. Formaspace) to order additional matching components to complete your lab expansion project. And, if you need to move, you can also easily disassemble and move the entire laboratory furniture set up to a new location without losing your initial investment.

7. What’s the Best Approach for Choosing a Lab Location?
The high cost of laboratory real estate, particularly in the so-called science clusters (located in the Boston and New York regions on the East Coast and the San Francisco Bay Area and San Diego on the West Coast), can be a determining factor when deciding where to locate your new lab startup.
In a departure from past practices, many new lab operations are opening in facilities originally designed for other purposes, such as underutilized retail locations, which can be leased at a relative discount compared to facilities that were originally purpose-built for laboratory operations.
If you’re evaluating the potential of converting an existing space into a lab facility, we recommend looking at our patented FabWall system. The modular FabWall system bolts securely into the floor, allowing you to divide open spaces into functional areas quickly and efficiently. Simply attach modular elements (such as wet sinks, workbenches, fume hood, and the like) directly to the FabWall.
The use of mobile lab furniture is another trend that facilitates the quick conversion of open spaces not originally designed for laboratory use.
Entire spaces can be kitted out quickly with workstations mounted on heavy-duty industrial-strength casters. Each workstation can support its own storage systems, shelving, as well as built-in electrical and networking connections.

8. How Can You Assure Laboratory Safety, Security, and Sustainability?
Safety first is the right mantra for laboratory design.
Here, details matter.
Double-check all safety requirements and make sure you are in compliance.
Questions you should ask yourself include: Are the fume hoods sized appropriately to protect lab workers? Are there a sufficient number of eyewash stations and first aid kits available? Is access to PPE well-thought-out – to encourage proper use? Is there adequate storage for potentially dangerous chemicals or fragile scientific equipment? Have you provided easily accessible drying racks for highly breakable glassware?
In many cases, specifying mobile storage carts can help prevent accidents when transporting heavy equipment; these can also make it easier to safely transport equipment in need of maintenance or service away from heavily trafficked areas to a dedicated service bay.
Protecting personnel from the Covid-19 virus is also another important consideration. Are lab workbenches spaced far enough apart to encourage social distancing? Are lab employees protected from one another by the use of transparent shields when they need to work in close quarters? Is the HVAC system designed to provide enhanced ventilation, ideally pulling air up and out of the facility rather than pushing it down toward the floor? Can you offer outdoor work areas for employees to conduct some of their work activities outside as well as provide pleasant outdoor areas for taking breaks and eating meals?
Greater emphasis is also being placed on lab security, especially given recent reports of foreign espionage directed at pharmaceutical research labs developing Coronavirus vaccines. Are your computer system sufficiently isolated and protected? Also, given that more employees will be accessing the outdoors, does the facility’s security perimeter policy take this into account?
Sustainability is another major concern in laboratory design. As we mentioned earlier, modular furniture designs can be reconfigured without difficulty, even moved to new locations if needed. This not only protects your original investment, it can also help you accrue LEED credits when performing future renovations or moving to a new facility.
Laboratory energy use is another important sustainability issue, especially given that most laboratories use energy at a greater rate than comparable office buildings (due to higher airflow requirements from fume hoods or cleanroom installations). Reducing energy use in laboratories remains a challenge, but new designs are showing it is possible, by increasing natural ventilation or redesigning the airflow in cleanroom installations for greater efficiency.

9. Will You be Able to Attract and Retain Lab Expertise/Talent?
The ability to attract and retain talent is a major concern for all companies, and laboratory facilities are no exception.
There’s a simple test you can take: Would you want to work in the new laboratory you’re planning?
Does your design provide enough of the in-demand features that today’s employees are looking for, including open sightlines, plenty of natural light, good noise control to prevent distractions, even some connection to the outside world, such as green plants or other natural elements?
Are you providing enough amenities to retain today’s workers? Keep in mind that wellness on-the-job is important these days, and offering a comfortable, ergonomic workspace is as good for you as it is for your employees. Formaspace can help you specify lab seating that is both easy to clean and maintain in lab conditions but also provides workers with enhanced back support as well as the ability to change positions throughout the day. That’s also a feature that’s available in Formaspace desks, tables, and workstations. Our optional sit-to-stand furniture allows employees to change from working in a seated position to a standing position throughout the day for increased blood circulation and reduced fatigue.

10. Where Can You Find the Right Laboratory Partners?
This brings us to our final question to ask when you are making plans to launch a new laboratory facility.
Where can you find the right laboratory partners who can share their experience?
One approach is to join one or more lab trade associations that represent your industry sector and speak to other members about whom they can recommend as reliable partners to work with.
It’s these kinds of word-of-mouth recommendations that may lead you to Formaspace.
Formaspace stands ready to help make your new lab project venture a success. We build all our lab furniture here in Austin, Texas, at our factory headquarters, using locally produced steel and other American-made raw materials.

We have built furniture systems for hundreds of laboratories nation-wide; our client list includes Abbot Laboratories, Amgen, Baxter, Bayer, GlaxoSmithKline, Johnson&Johnson, Merck & Co., Novartis, Pfizer, Roche, and Quest Diagnostics Inc.
Formaspace is also a great resource to turn to when you have questions about laboratory design. Our Design Consultants are standing by to answer any questions you have. We can also provide full-service assistance in designing your next laboratory project – even it’s your first one.
Will your project be next? We hope so.
Take the next step.
Talk to your Formaspace Design Consultant today and see how we can partner with you to make your next lab project a success.

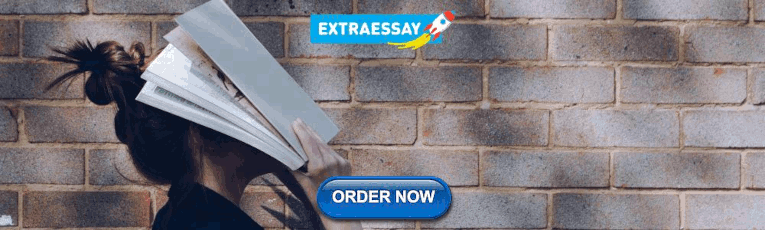
COMMENTS
Crafting Your Mobile Lab Business Plan 1. Market Analysis. Before hitting the road with your mobile lab, it’s crucial to understand your target market. Conduct thorough research to identify:
A good place to start is by researching the market demand and identifying the business case for your new venture. Here are a couple of business case examples – but yours will need to be more detailed, backed up by solid technical and market research. To take advantage of new research/testing opportunities, such as those created by the Covid ...