Resume Worded | Proven Resume Examples
- Resume Examples
- Administrative Resumes
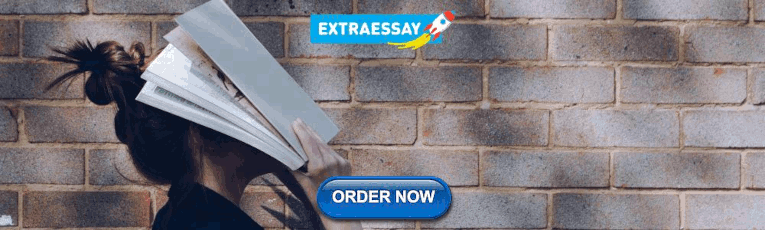
4 Warehouse Manager Resume Examples - Here's What Works In 2024
Warehouse managers are responsible for upkeeping, dispatching, and receiving packages. they also keep track of products on the warehouse tracking system and create statistic reports frequently. however, the most important role of a warehouse manager is to protect employees by maintaining security measures. if you have experience with warehousing and would like to apply for a manager role, read on. we’ll give you relevant industry tips and show you how you can write the best warehouse manager resume. we’ll also share three warehouse manager resume templates so that you can have some inspiration..
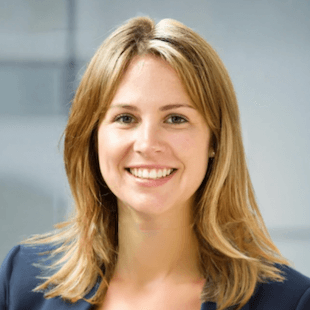
Warehouse managers have a crucial role in the supply chain industry. They’re in charge of supervising employees and ensuring they follow safety compliance. Warehouses often store fragile and sometimes dangerous products that need to be handled carefully. If they’re misused or placed wrongly, it can lead to financial losses and decreased productivity. That’s why warehouse managers play such a huge role in ensuring that employees are doing things right.
In addition to damaged products, employees can also get hurt when manipulating them. That’s why the warehouse manager must train and supervise them. On the other hand, warehouse managers are also in charge of updating the inventory tracking systems and providing productivity reports to their superiors.
Warehouse managers are the connection between clients, transportation companies, and suppliers. They make sure the supply chain process is seamless. The supply chain process has its own laws and legislations. Warehouse managers must comply with them and ensure the rest of the team members do as well.
If you’ve ever been to a warehouse before, you’ll notice there are thousands of packages on different racks. Most of us would get lost trying to find a particular product in that storage system. Yet, a warehouse manager wouldn’t.
Warehouse racks have designated labels that help employees easily find products and keep track of inventory. There are numerous ways to organize those labels, and warehouse managers are responsible for that task. Warehouse label organization also helps managers have easy access to information they use when creating productivity and inventory reports.
Another crucial role that warehouse managers perform is delegation. They assign tasks to each employee and create teams for different duties.
Warehouse Manager Resume Templates
Jump to a template:
- Warehouse Manager
- Warehouse Operations Manager
- Assistant Warehouse Manager
Jump to a resource:
- Keywords for Warehouse Manager Resumes
Warehouse Manager Resume Tips
- Action Verbs to Use
- Related Administrative Resumes
Get advice on each section of your resume:
Template 1 of 4: Warehouse Manager Resume Example
A warehouse manager is the head of storage operations. They assign tasks, designate rack labels, train, and oversee employees. They are also responsible for maintaining long-term relationships with suppliers and transportation companies and addressing problems clients have about their service. On the other hand, warehouse managers assist employees and foster a safe work environment. Without them, the storage operations would be disorganized and inefficient. There are numerous career paths to becoming a warehouse manager. Ideally, you should have a bachelor’s degree in Supply Chain Management, Administration, Logistics, or a related field. However, there are other paths such as apprenticeships, college courses, or working your way into this position.
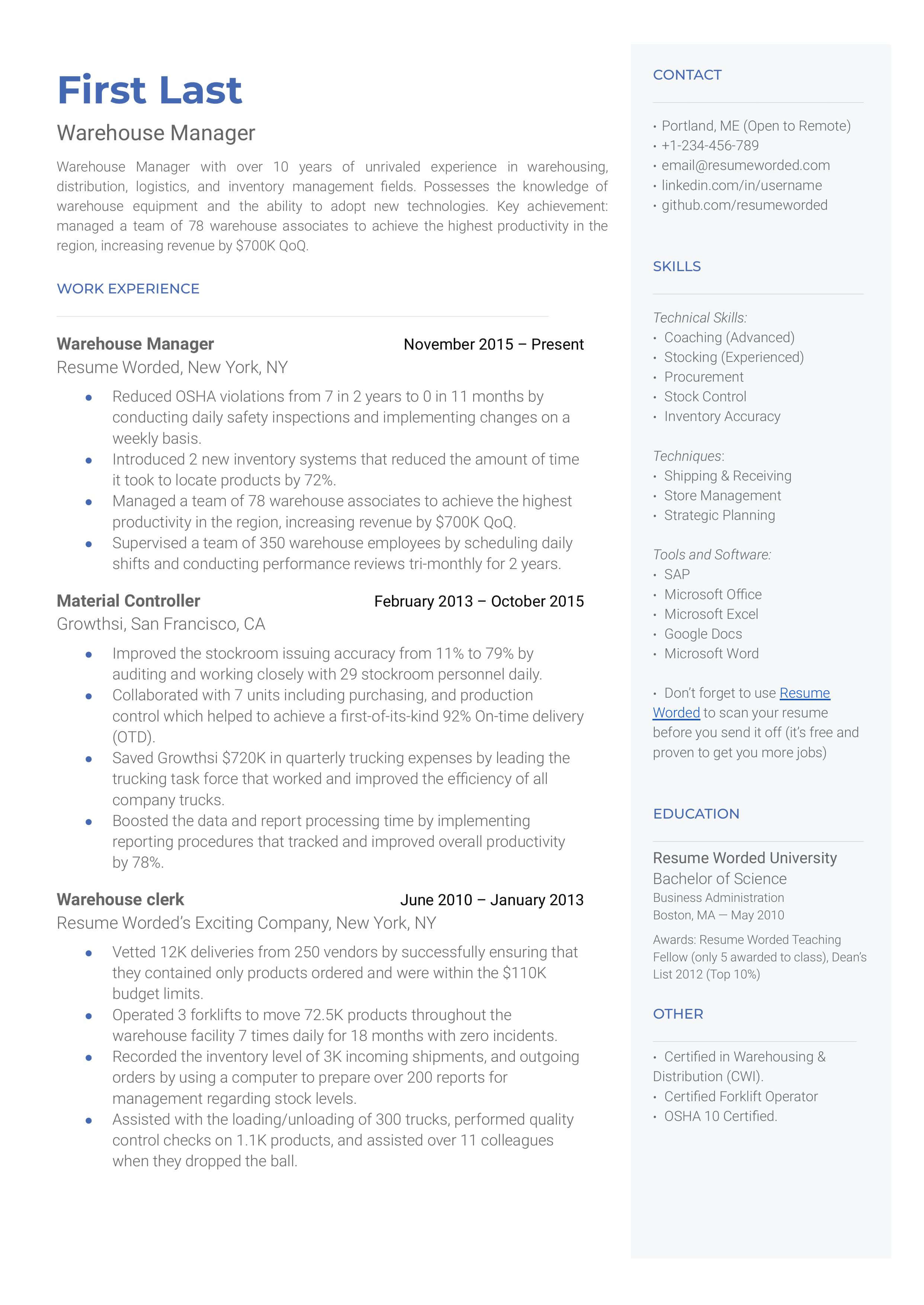
We're just getting the template ready for you, just a second left.
Tips to help you write your Warehouse Manager resume in 2024
quantify your achievements..
As a warehouse manager, your goal should be to increase productivity, reduce risks, and foster safety operations. All of these achievements can be quantified and this is the best way to explain them. Try to include metrics when mentioning your accomplishments and this will help recruiters have a clear view of your potential.
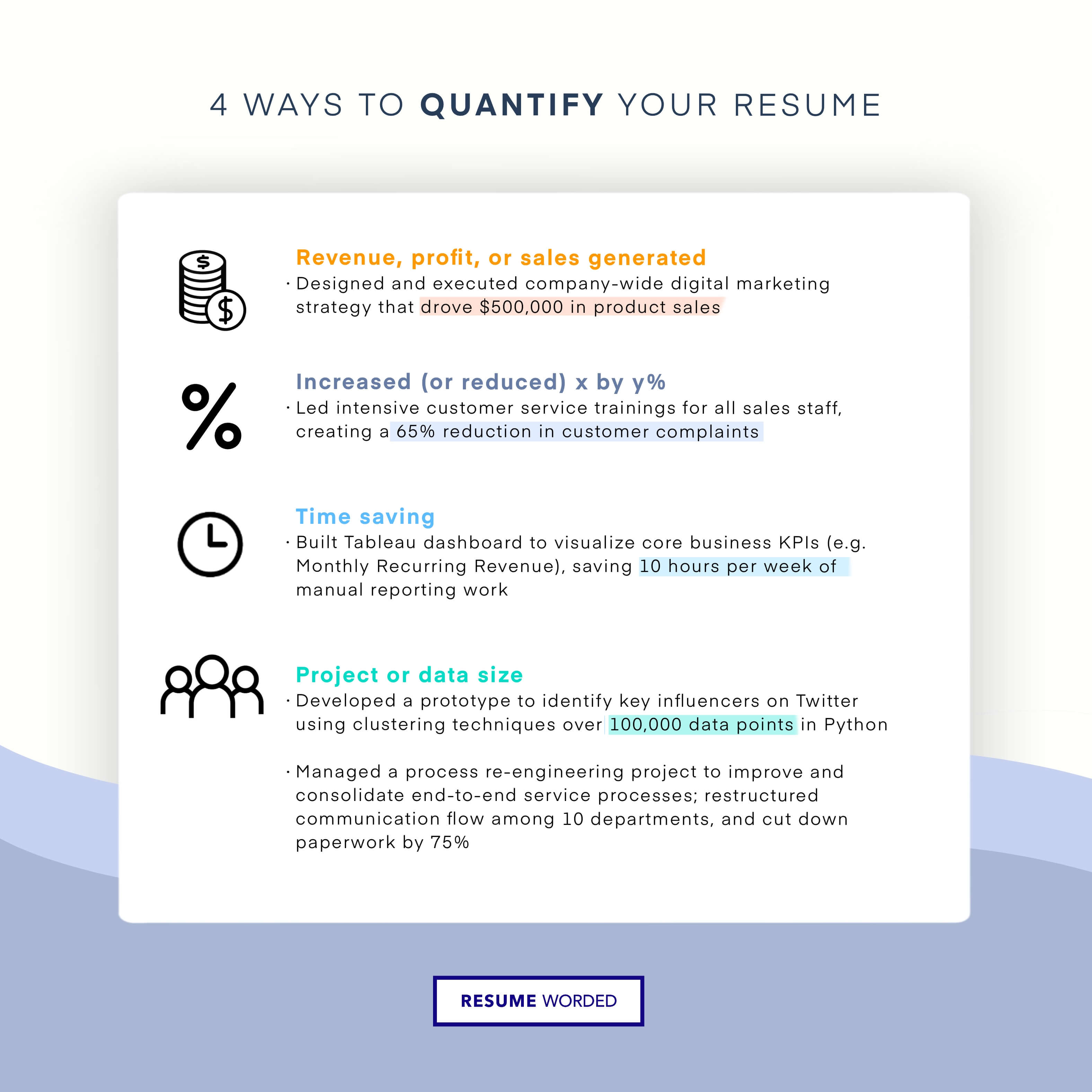
Mention your familiarity with inventory tracking systems.
Warehouse companies use inventory management systems to maintain a seamless supply chain experience. They help them keep track of packages, and identify issues in the operations, and improvement opportunities. As a warehouse manager, you should be familiar with them. That’s why you should mention them in your resume. Some of the most popular ones are NetSuite, SphereWMS, Infoplus, mobe3 WMS, and Odoo.
Skills you can include on your Warehouse Manager resume
Template 2 of 4: warehouse operations manager resume example.
As the name suggests, this operations manager is in charge of the daily operations of a warehouse. Your tasks may include, ensuring the distribution plan is effectively realized, tracking inventory, overseeing the dispatching of inventory, etc. You will need to understand the goods your company is selling, their sales cycle, available transport methods, and the workings of a warehouse. As a manager, you will also need to have experience effectively managing a team. Take a look at this strong warehouse operations manager resume.
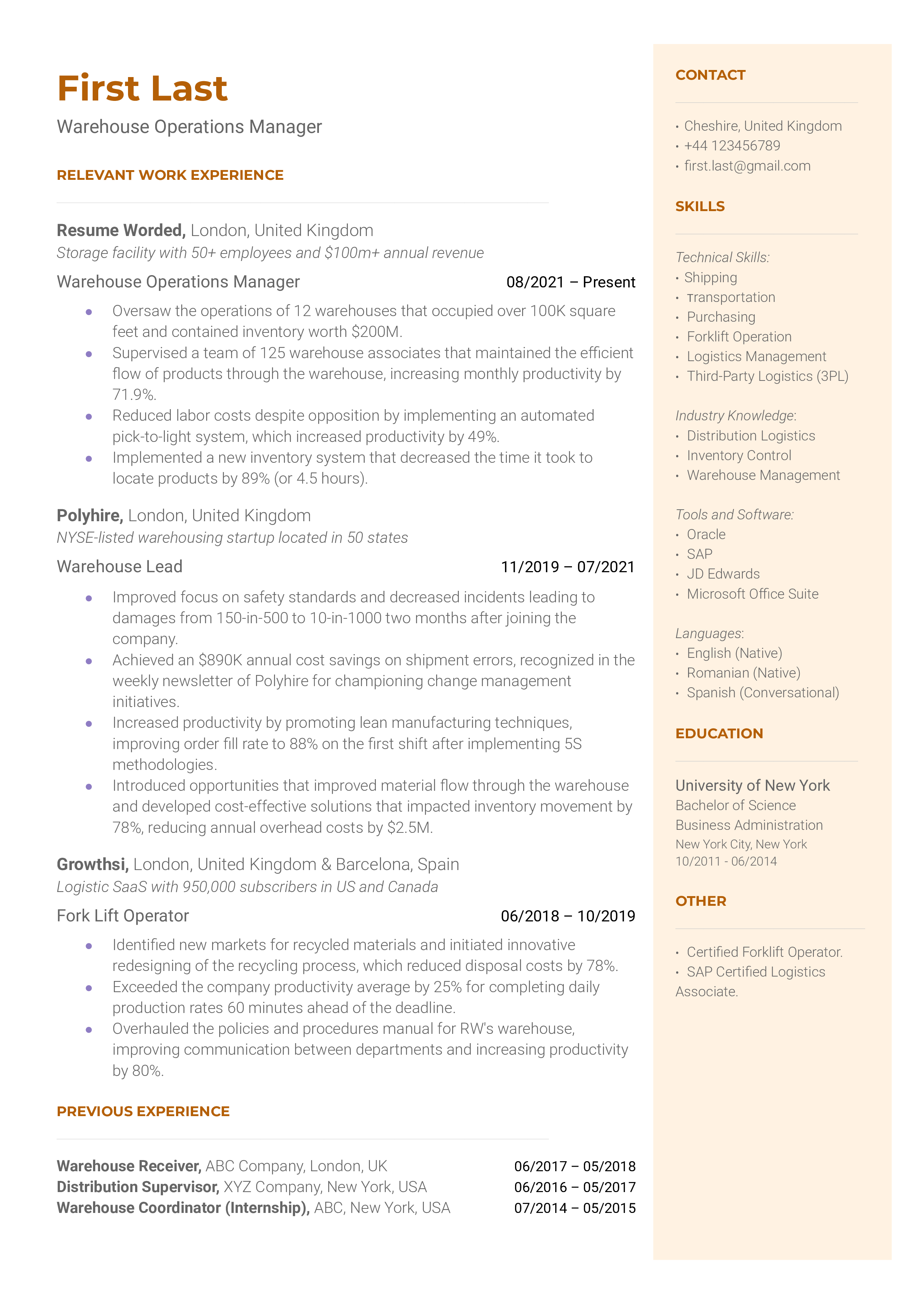
Tips to help you write your Warehouse Operations Manager resume in 2024
quantify the size of the teams you managed..
Warehouses usually need a sizeable workforce to operate efficiently so show recruiters that you are capable of managing large teams by listing the number of people you have managed in previous positions. This applicant impressively supervised 125 warehouse employees in their previous position.
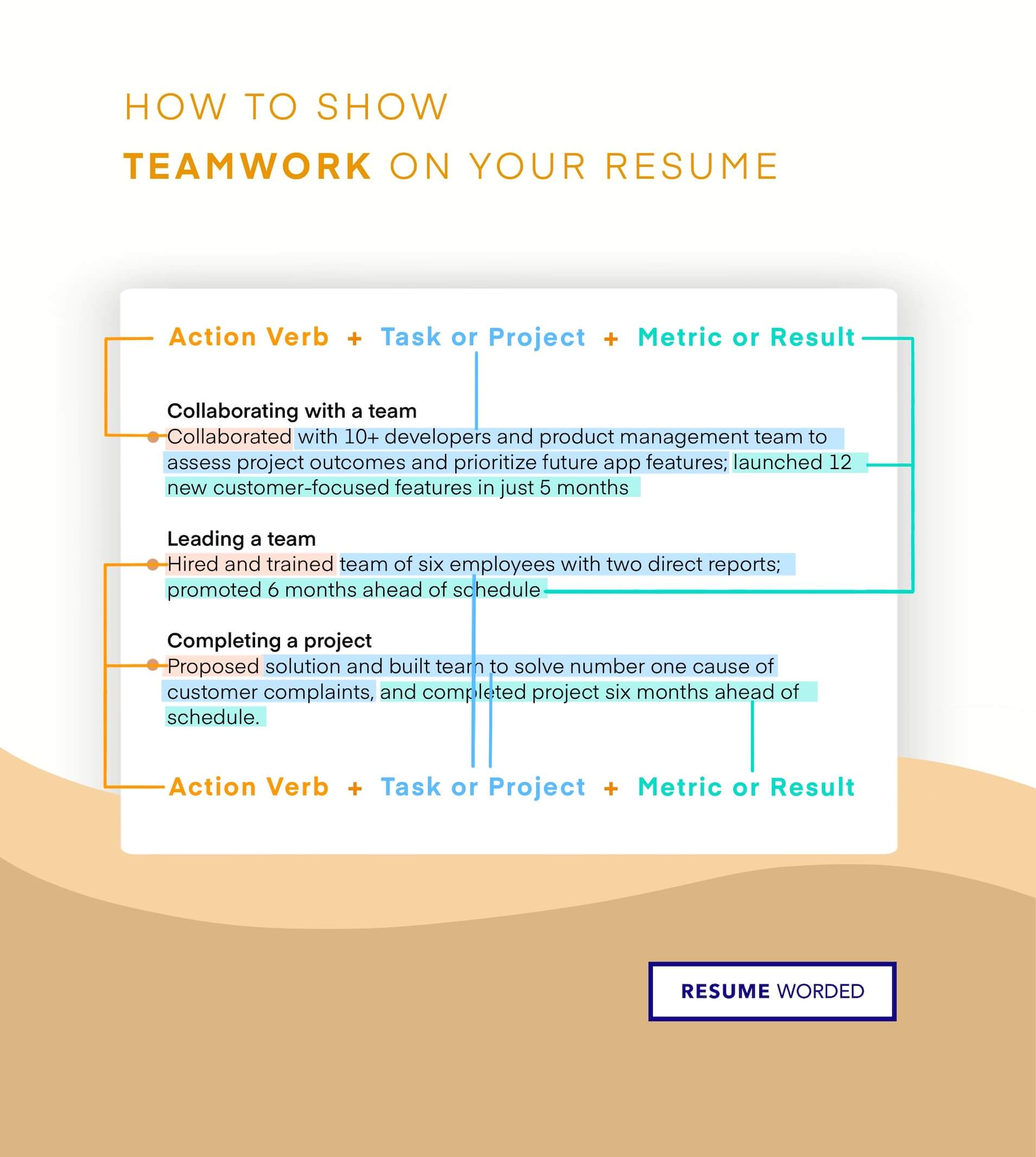
Your tools section should reflect industry standards.
Ensure that your tools section includes all the main tools used by professionals who operate warehouses and manage teams. If you applying to a specific company, do research to find out what tools they use and ensure you include those tools in your resume.
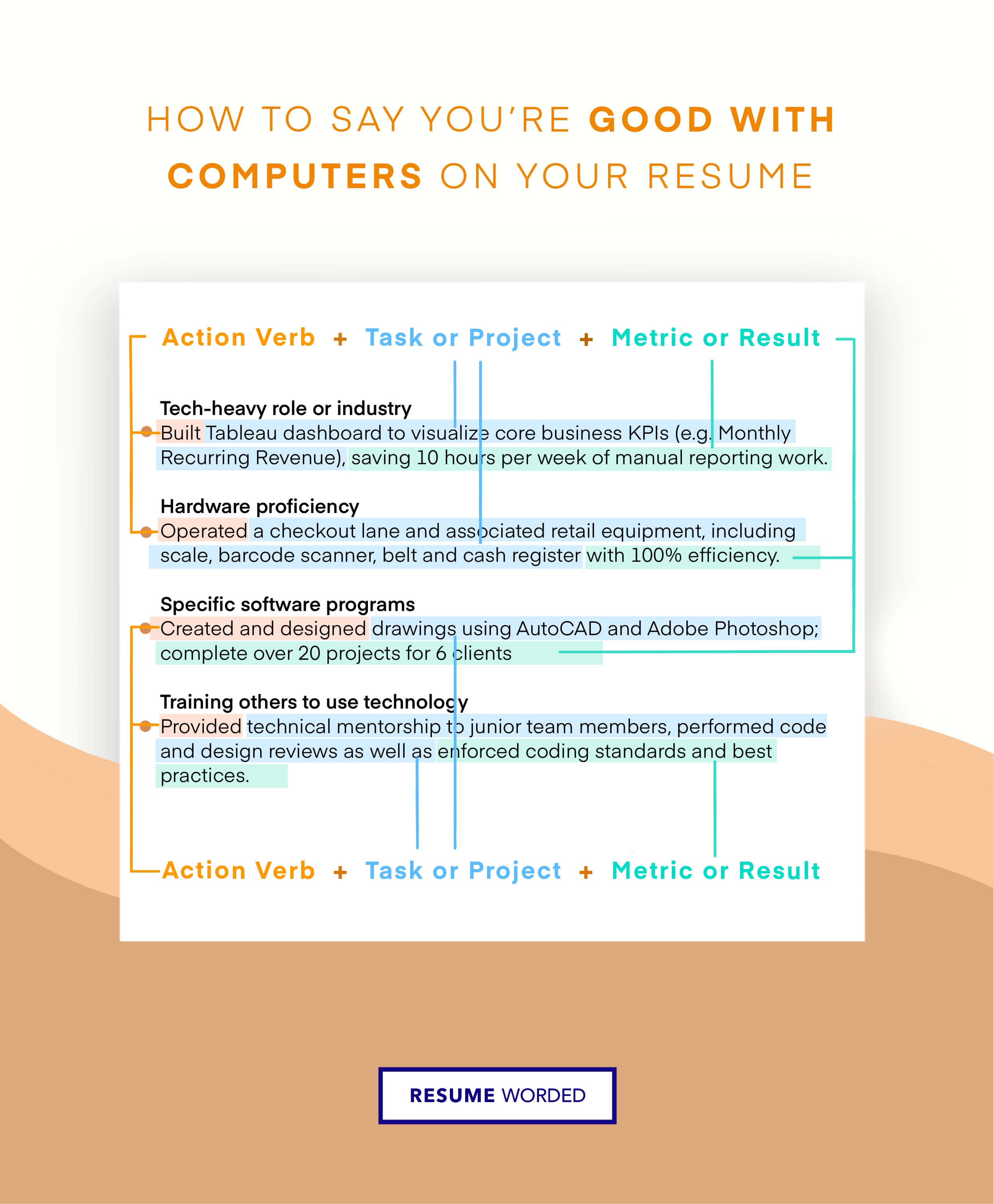
Skills you can include on your Warehouse Operations Manager resume
Template 3 of 4: warehouse operations manager resume example.
A warehouse operations manager oversees storage operations. They receive and dispatch packages and create strategies to improve the warehousing service. This is a systematic role in which they must supervise internal and external resources. This includes monitoring employees and meeting with external vendors. Although they must comply with stakeholders’ requirements and goals, warehouse operations managers are expected to make business decisions independently. They must also drive workplace safety and delegate tasks to subordinates.
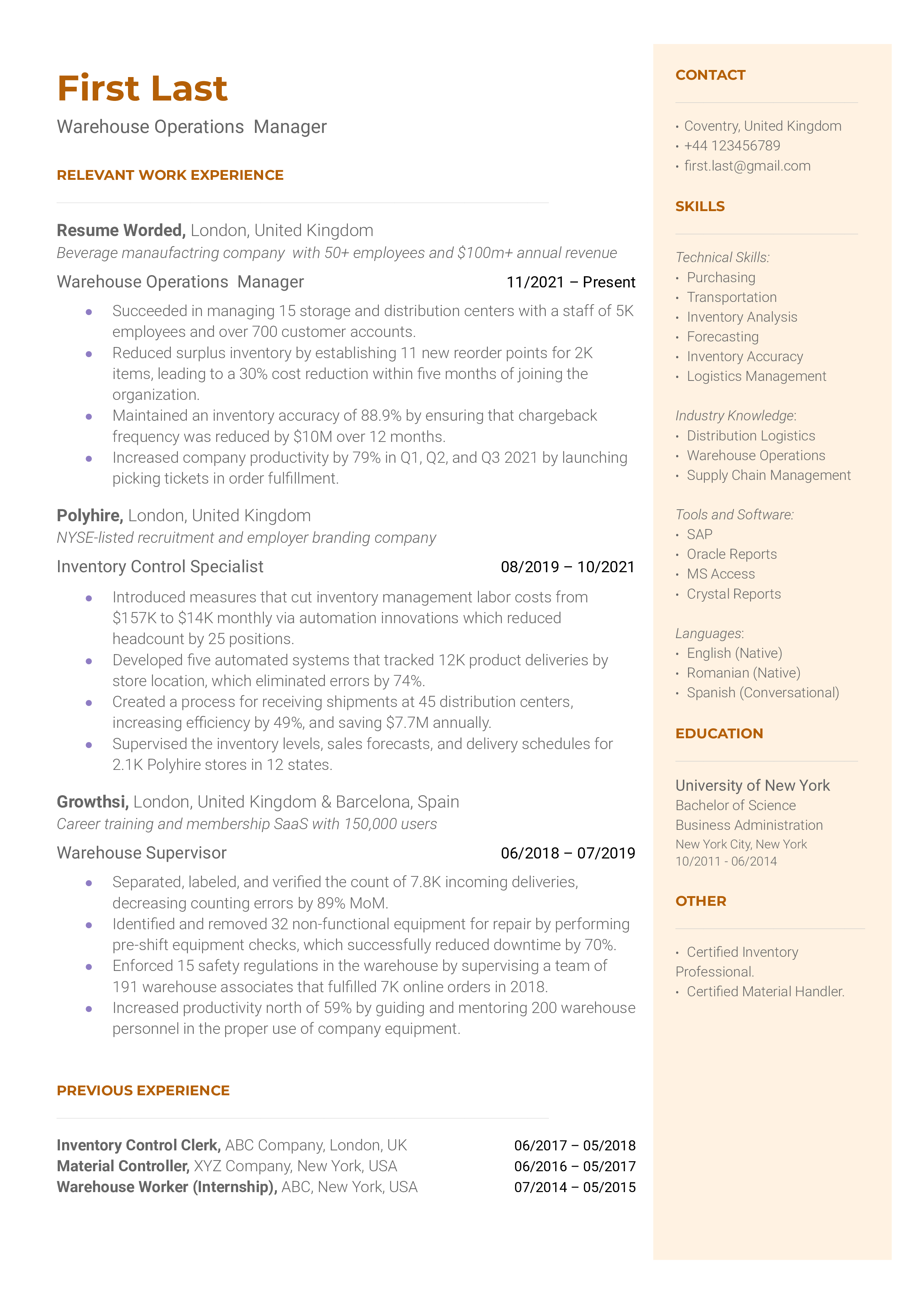
Indicate your knowledge of supply chain legislations and laws.
As a warehouse operations manager, you are expected to comply with supply chain local and federal legislations and ensure employees follow these laws as well. You should also be familiar with internal policies and stakeholders’ goals. Therefore, it is crucial to mention your familiarity with supply chain compliance in your resume.
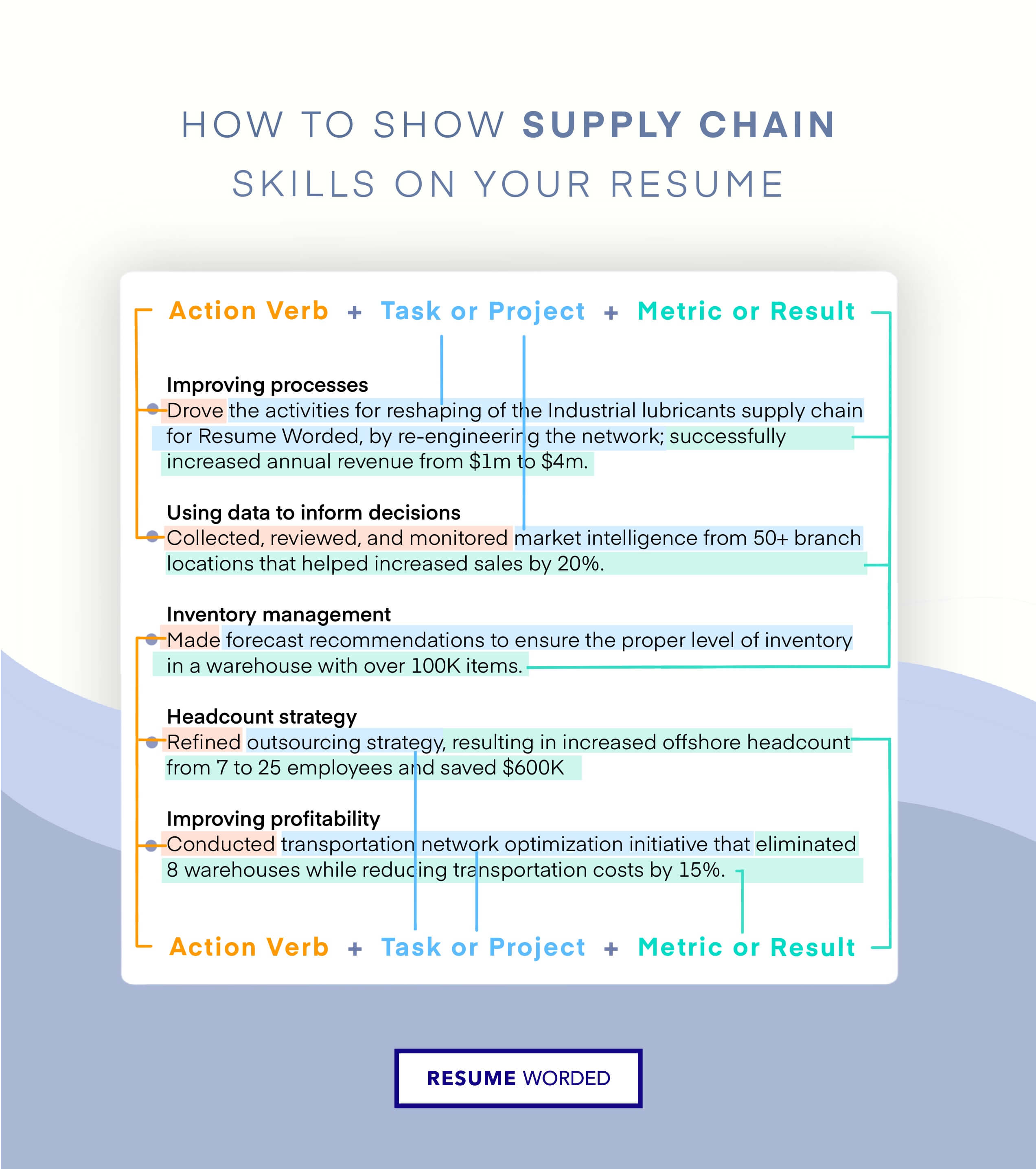
Demonstrate your administration skills.
As we mentioned earlier, you will have to make business decisions independently. This often involves setting business strategies, getting suppliers, and creating budget reports, so your administration skills must be on point. When writing your warehouse manager resume, try to indicate your administration skills.
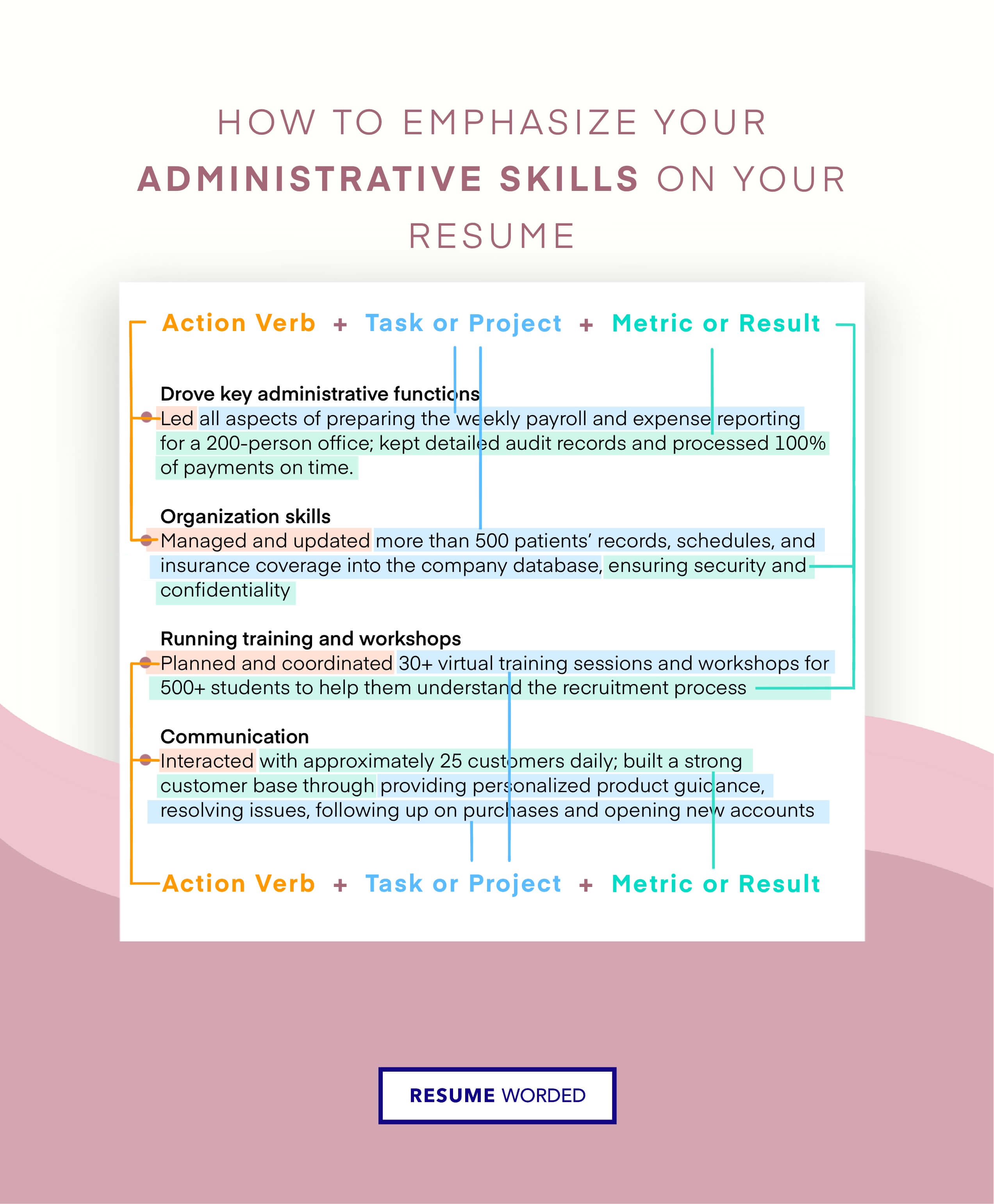
Template 4 of 4: Assistant Warehouse Manager Resume Example
The assistant warehouse manager is responsible for processing orders and keeping track of inventory. They are also in charge of obtaining quotes from vendors and negotiating with them based on budget constraints. An assistant warehouse manager will take control of the entire operations when the warehouse manager is absent. To become an assistant warehouse manager, you must have computer literacy, logical thinking, negotiation skills, and be familiar with safety and legal compliance. You should be familiar with inventory management systems and supply chain protocols.
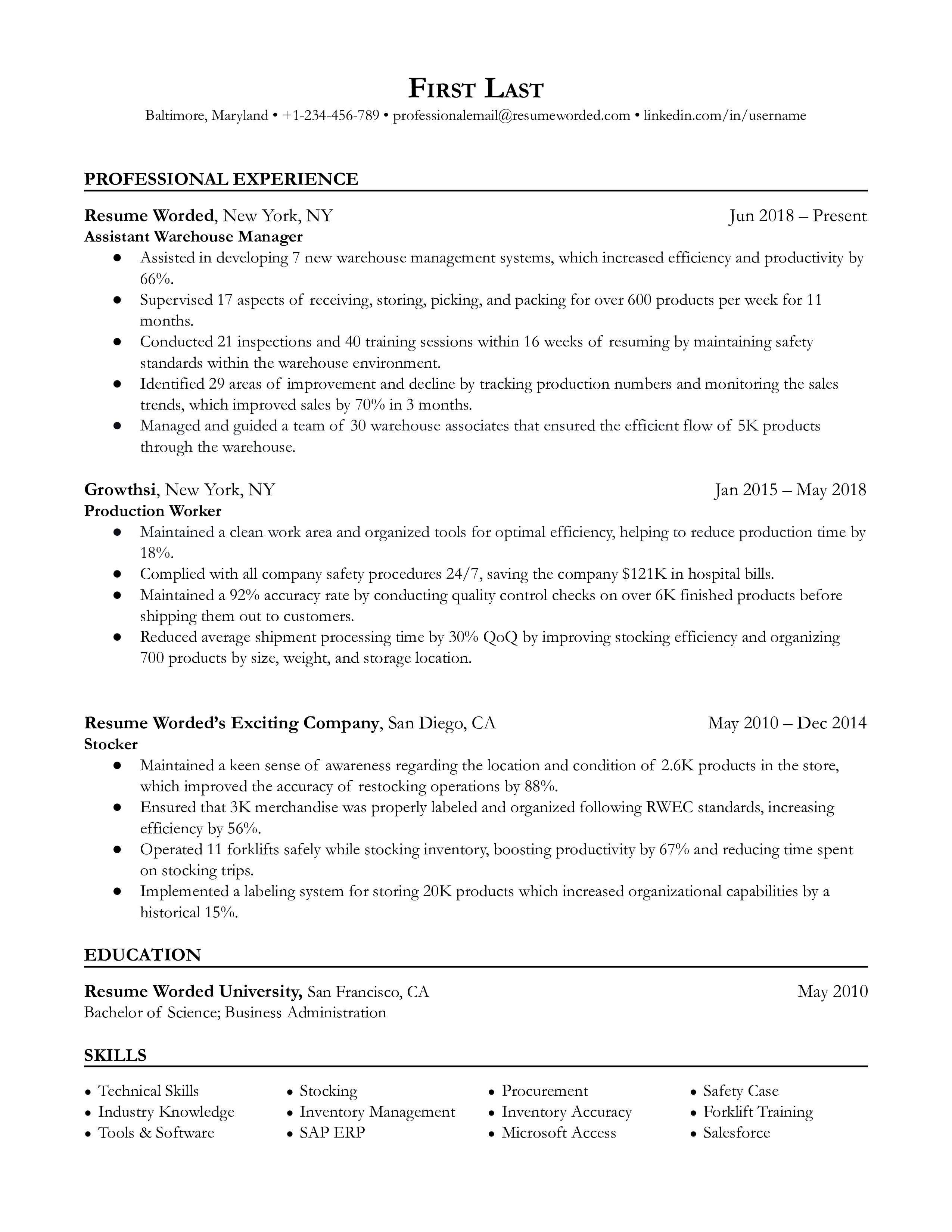
Tips to help you write your Assistant Warehouse Manager resume in 2024
emphasize your knowledge of the supply chain process..
Usually, assistant warehouse managers don’t have enough experience to get the highest managerial role. However, you can still get the role by demonstrating your knowledge of the supply chain process. Talk about what you’ve learned in previous roles and how you can implement that knowledge to improve productivity and safety.
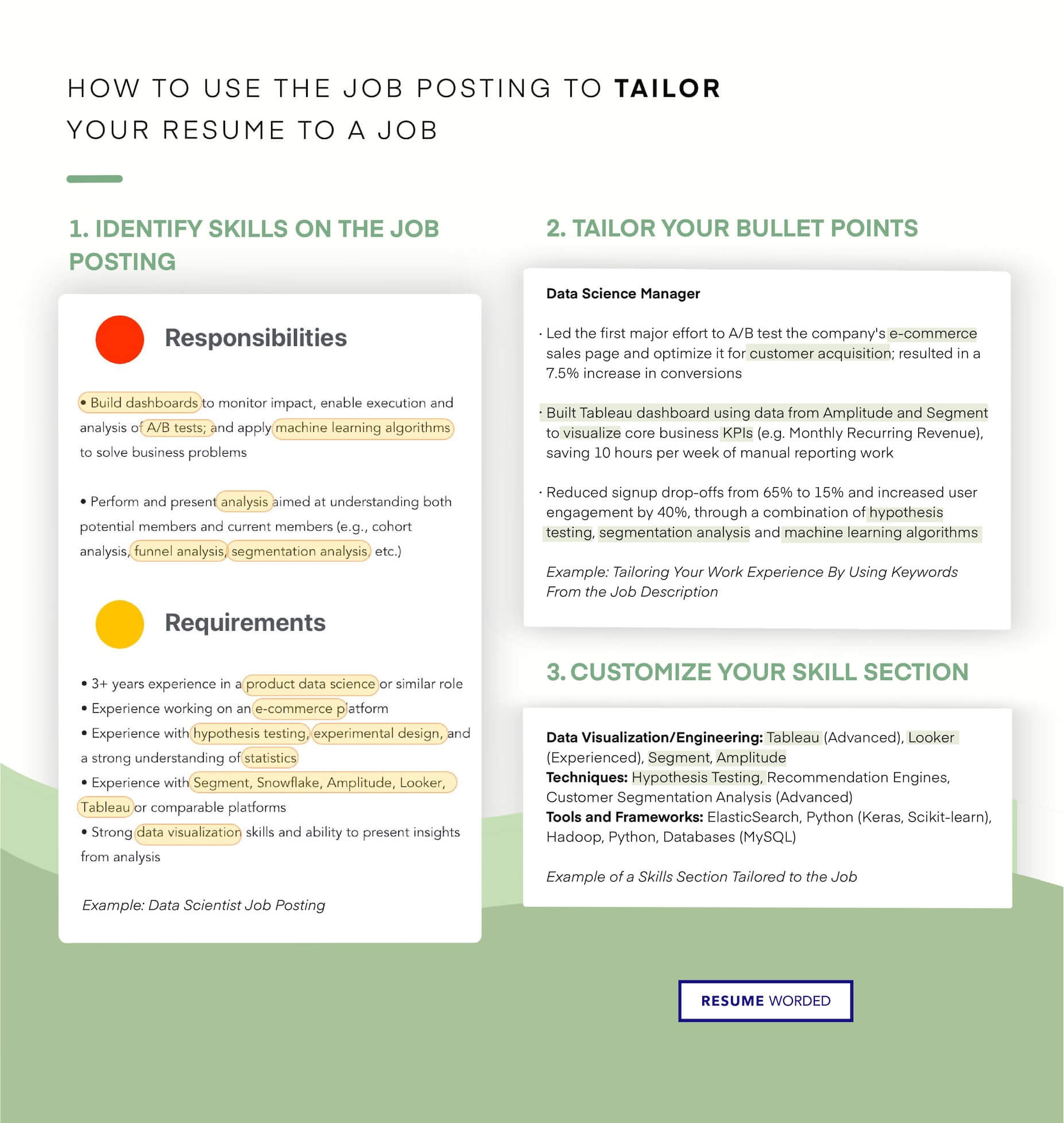
Highlight your ability to work in a high-paced environment.
Warehouse management is a high-paced work environment, so you should be able to work under pressure. This is something you should mention in your assistant warehouse manager resume. Recruiters might be looking for someone who can keep up with the high pace of receiving and dispatching numerous orders daily.
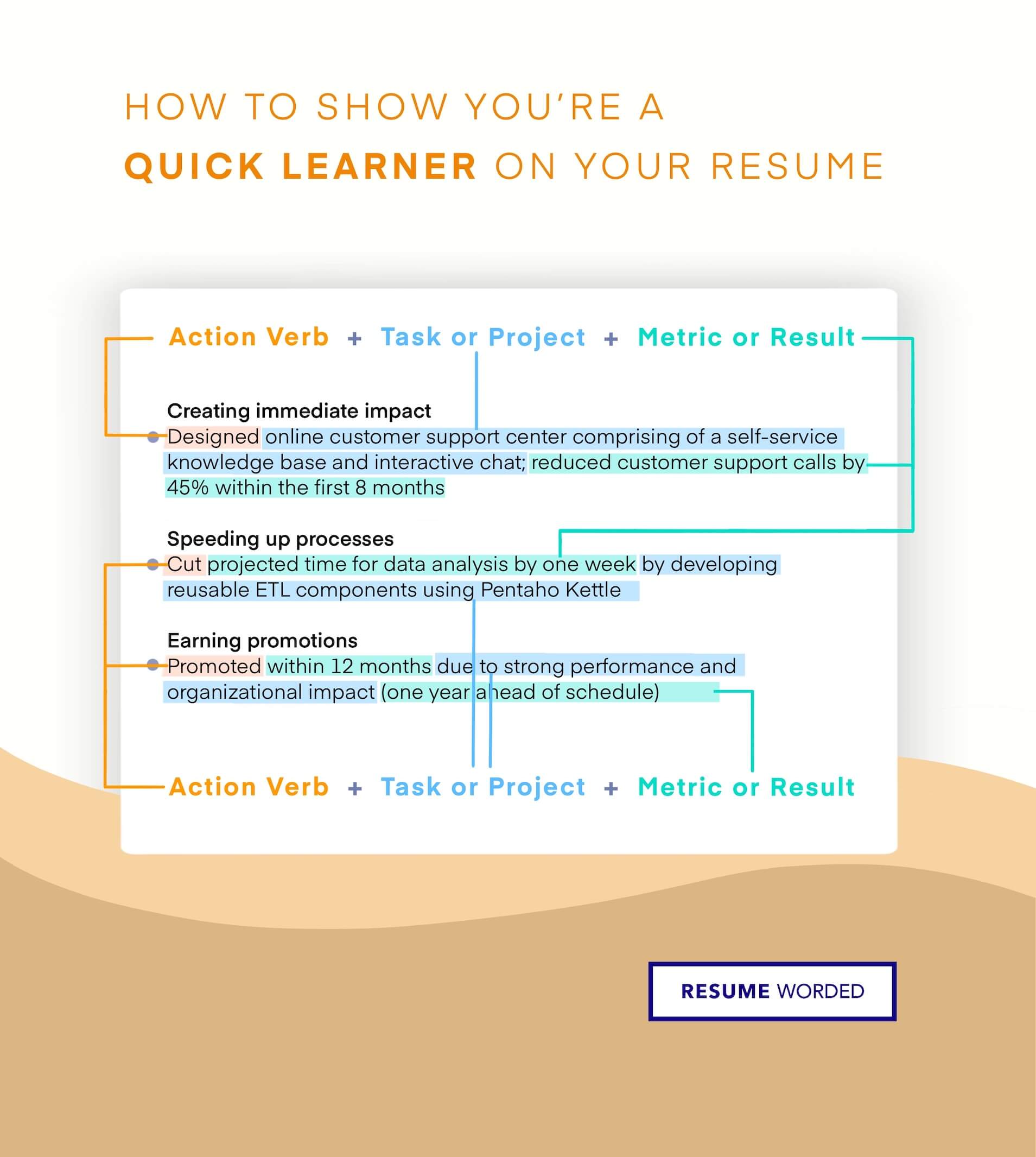
Skills you can include on your Assistant Warehouse Manager resume
We asked hiring managers at top companies like Amazon, FedEx, and UPS what they look for in warehouse manager resumes. Based on their insights and years of experience hiring for these roles, we've compiled expert tips to help your resume stand out. Whether you're an experienced warehouse manager or just starting out, these tips will show you how to highlight your skills and achievements effectively.
Show your impact with metrics
When describing your warehouse management experience, use specific numbers and metrics to show the impact you made:
- Implemented inventory management system that reduced stockouts by 25% and improved order fulfillment rate from 92% to 98%
- Managed a team of 50 warehouse associates and improved productivity by 15% through process optimization and training initiatives
Compare this to vague statements that don't convey your true value:
- Responsible for managing inventory and reducing stockouts
- Led a large team to improve warehouse productivity
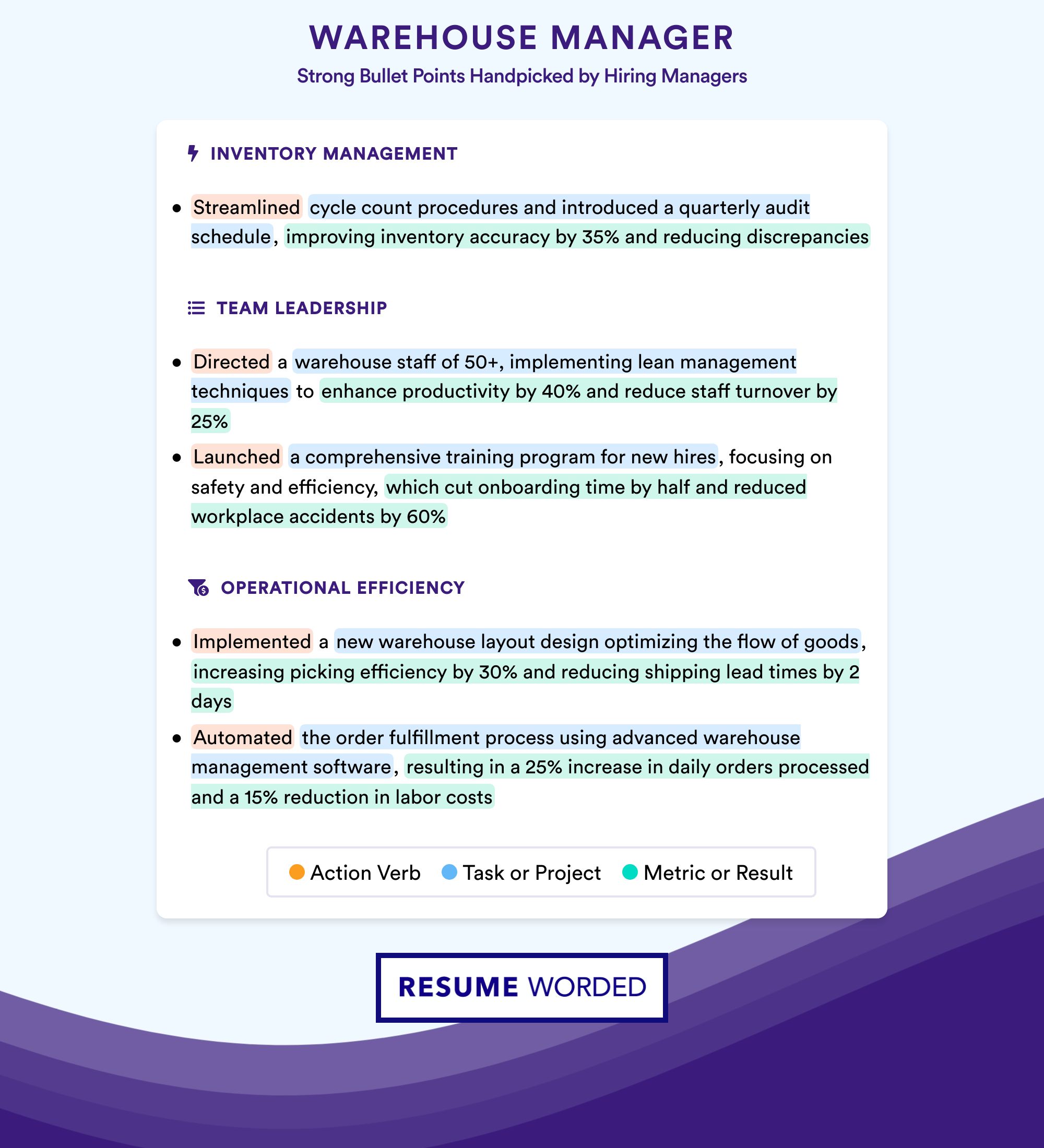
Highlight your leadership and people management skills
Warehouse managers are responsible for leading and motivating teams. Emphasize your people management abilities with examples like:
- Coached and mentored team leads, resulting in 3 promotions to supervisor roles within 12 months
- Resolved conflicts and maintained positive employee relations in a union environment
- Collaborated with HR to reduce turnover rate from 40% to 25% through improved hiring practices and employee engagement initiatives
Demonstrate your process improvement expertise
Employers value warehouse managers who can streamline processes and drive efficiency. Show how you've optimized warehouse operations with examples like:
- Implemented Lean Six Sigma methodologies to eliminate waste and reduce order processing time by 30%
- Redesigned warehouse layout and product slotting system, increasing storage capacity by 20% without additional square footage
- Automated manual processes using warehouse management software (WMS), resulting in a 15% reduction in labor costs
Tailor your resume to the job description
Customize your resume to align with the specific requirements of each warehouse manager job you apply for. For example:
- If the job focuses on technology implementation, emphasize your experience with WMS, ERP, or automation projects
- For roles that prioritize safety, highlight your success in maintaining OSHA compliance and reducing accidents
- If the company handles specialized products like hazardous materials or pharmaceuticals, showcase your relevant industry certifications and training
Showcase your cross-functional collaboration skills
Warehouse managers often work closely with other departments like transportation, purchasing, and customer service. Highlight your ability to collaborate across functions with examples such as:
- Partnered with transportation team to optimize routes and reduce freight costs by 10%
- Worked with purchasing to implement just-in-time inventory system, reducing carrying costs by $500K annually
- Collaborated with customer service to improve order accuracy and reduce returns by 15%
Include a compelling professional summary
Start your resume with a strong professional summary that captures your key strengths and experience. For example:
Results-driven warehouse manager with 8+ years of experience optimizing operations for Fortune 500 companies. Proven track record of reducing costs, improving efficiency, and leading high-performance teams. Six Sigma Black Belt with expertise in WMS implementation and Lean methodologies.
Avoid generic summaries that could apply to any candidate, like:
Experienced warehouse manager seeking a new opportunity. Skilled in managing teams and improving processes.
Writing Your Warehouse Manager Resume: Section By Section
header, 1. include your full name and key contact details.
Your header should feature your full name prominently at the top. Use a slightly larger font size than the rest of your resume to make it stand out.
Below your name, include your key contact details:
- Phone number
- Professional email address
- LinkedIn profile URL
- City and state location
Avoid listing your full mailing address, as it's no longer necessary and takes up valuable space. For example:
- John Smith, 123 Oak Avenue, Anytown, California 98765
Instead, use a concise format like:
- John Smith | 555-123-4567 | [email protected] | linkedin.com/in/john-smith | Anytown, CA
2. Showcase a relevant certification or job title
If you hold a certification that's highly relevant to warehouse management, such as a CPIM (Certified in Production and Inventory Management) or CSCP (Certified Supply Chain Professional), consider featuring it after your name in your header. This immediately establishes your credibility.
Alternatively, if you have an impressive job title like "Senior Warehouse Manager" or "Warehouse Operations Manager" in your most recent role, you may want to include that in your header as well. However, avoid listing a full professional summary or multiple job titles, as that belongs in other sections.
John Smith, CPIM 555-123-4567 | [email protected] | linkedin.com/in/john-smith | Anytown, CA
This header quickly conveys that John is certified in production and inventory management, giving him an edge over other candidates.
3. Ensure your email and LinkedIn URL are professional
Warehouse managers often interact with various stakeholders, from suppliers to senior executives. Therefore, it's essential to project a professional image through your contact details.
Double-check that your email address is appropriate and incorporates some version of your real name. Avoid outdated or cutesy handles like:
- [email protected]
Similarly, include a link to your LinkedIn profile, but make sure your URL is clean and customized with your name:
- linkedin.com/in/john-smith
An updated LinkedIn profile with a custom URL not only looks more professional but also makes it easier for recruiters to find you online and shows that you're social media savvy.
Summary
A resume summary for a Warehouse Manager position is optional, but can be a strategic way to provide additional context about your background and highlight key skills that are most relevant to the job. Avoid using an objective statement, which is an outdated approach that focuses on what you want rather than what you can offer an employer.
When writing your Warehouse Manager resume summary, focus on your most impressive achievements, management abilities, and industry expertise. Tailor your summary to the specific requirements of the job description. Keep it concise, no more than 3-4 sentences or bullet points.
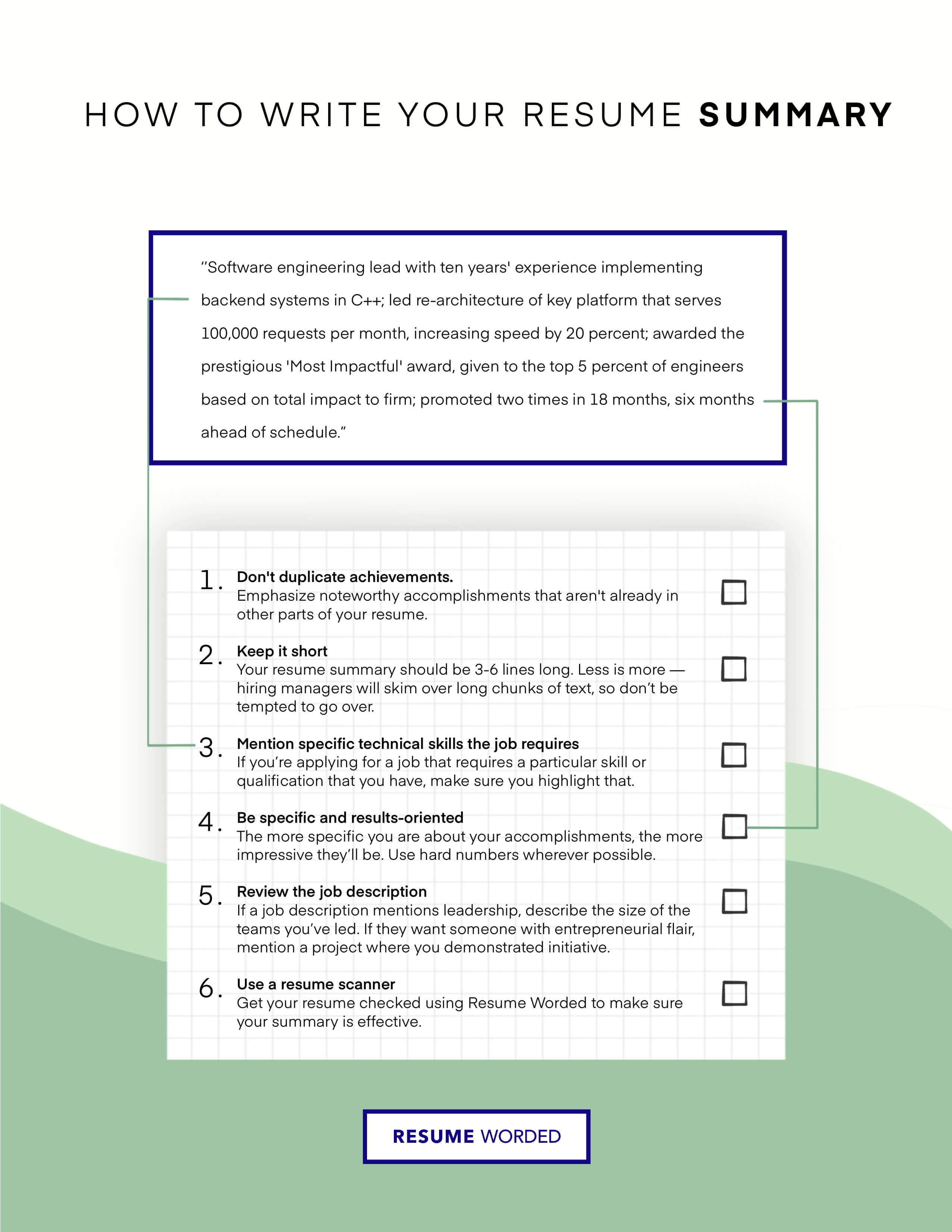
To learn how to write an effective resume summary for your Warehouse Manager resume, or figure out if you need one, please read Warehouse Manager Resume Summary Examples , or Warehouse Manager Resume Objective Examples .
1. Emphasize your leadership and management abilities
As a Warehouse Manager, your ability to lead teams, streamline processes, and drive results is crucial. Highlight your leadership skills and quantify your achievements in your summary.
Results-driven Warehouse Manager with 8+ years of experience overseeing inventory control, logistics, and team leadership. Proven track record of implementing Lean Six Sigma methodologies to reduce costs by 15% and improve order fulfillment accuracy to 99.7%. Skilled in training and managing teams of up to 50 employees to exceed productivity goals.
Avoid making vague, unsubstantiated claims:
- Experienced manager with strong leadership skills
- Hardworking Warehouse Manager who can handle pressure
2. Showcase your technical expertise and industry knowledge
Demonstrate your knowledge of warehouse management systems, inventory optimization techniques, safety regulations, and other industry-specific expertise. Use industry keywords to help your resume pass applicant tracking systems (ATS).
Effective summaries for Warehouse Managers might mention:
- Expertise in WMS software, including SAP and Oracle
- Knowledge of OSHA safety regulations and HAZMAT procedures
- Familiarity with inventory control methods like FIFO and JIT
- Lean Six Sigma Green Belt certification
However, avoid simply listing keywords without context:
- WMS, SAP, OSHA, FIFO, Lean Six Sigma, inventory control
Experience
Your work experience section is the heart of your resume. It's where you show a hiring manager how you've applied your skills to produce results. Let's look at how to write an effective work experience section step-by-step, with examples from successful warehouse manager resumes.
1. Highlight accomplishments with metrics
When describing your work experience, focus on your accomplishments and the results you delivered, not just your day-to-day responsibilities. And whenever possible, quantify those accomplishments with metrics.
Compare these two bullet points from a warehouse manager resume:
- Responsible for managing inventory levels
- Reduced inventory variances by 37% and increased inventory accuracy to 99.7% through implementation of cycle counting program and quarterly audits
The second example is much stronger because it uses hard numbers to show the specific results the candidate achieved.
2. Showcase leadership and communication skills
Warehouse managers need to be strong leaders who can motivate a team while also communicating and collaborating cross-functionally. Highlight examples of how you've demonstrated these critical soft skills.
Partnered with sales to implement new demand forecasting process, improving forecast accuracy by 16% and reducing back orders by 22%.
In this example, the candidate showcased their communication and collaboration skills by working with another department to improve a key process.
Reduced team turnover by 18% by leading development of new employee onboarding and training program.
This example demonstrates the candidate's leadership abilities in developing their team.
Plug your bullet points into our free tool, Score My Resume , to get instant feedback and suggestions tailored to warehouse manager resumes.
3. Mention promotions and career progression
Showing that you've been promoted or taken on increasing levels of responsibility helps demonstrate your value to an employer. Be sure to clearly call out any promotions in your work experience section.
Here's a good example:
Warehouse Associate, ABC Company, June 2016 - March 2019 Warehouse Manager, ABC Company, March 2019 - Present • Promoted to manage a team of 15 warehouse associates... • Increased picking and packing efficiency by 24% by reorganizing warehouse layout and streamlining processes... • Reduced safety incidents by 38% through implementation of new safety protocols and monthly training...
By separating out the two positions and specifying 'Promoted to...', this candidate makes their advancement within the company crystal clear to a hiring manager.
4. Tailor your examples to the job description
One of the most important ways to make your resume stand out is to customize it for each job you apply to. Carefully review the job description and make sure your work experience highlights the key skills and qualifications required.
For example, if a warehouse manager job description mentions 'WMS' multiple times, you'll want to showcase your experience with warehouse management systems:
- Implemented new WMS, reducing picking errors by 41% and increasing order accuracy to 99.8%
- Conducted monthly training on WMS processes for all new hires, ensuring proper system usage
On the other hand, if the job focuses more on logistics, you might include examples like:
- Negotiated new contracts with carriers, reducing average shipping costs by 18%
- Collaborated with logistics team to design new distribution network, cutting average delivery times by 2 days
Our Targeted Resume tool can help you quickly see if your resume has the right skills and keywords for a specific warehouse manager job. It's an easy way to check if you've tailored your resume well.
Education
The education section of your warehouse manager resume should be concise and highlight your relevant qualifications. It's important to list your degrees in reverse chronological order, with the most recent one first. If you have a college degree, you can leave out your high school information.
1. Include relevant coursework if you're a recent graduate
If you've graduated within the last few years and don't have much work experience, you can boost your resume by listing relevant coursework under your degree.
- Bachelor of Science in Supply Chain Management, XYZ University, Graduated 2022
- Relevant Coursework: Logistics Management, Inventory Control, Warehouse Operations, Supply Chain Analytics
This shows employers that you have a solid educational foundation in the skills needed for a warehouse manager role.
2. List certifications to showcase your expertise
Industry certifications demonstrate your commitment to professional development and can set you apart from other candidates. Include them in your education section or in a separate 'Certifications' section.
APICS Certified Supply Chain Professional (CSCP), 2020 Certified Warehouse Management Professional (CWMP), 2018
These certifications prove you have the knowledge and skills to effectively manage a warehouse.
3. Keep it brief if you're a senior professional
If you have over 10 years of experience, your work history should be the main focus of your resume. Keep your education section short and to the point.
- Bachelor of Business Administration, ABC University, Graduated 1995
- Courses: Intro to Management, Business 101, Marketing Basics, Organizational Behavior
- Dean's List 1993, 1994
Instead, simply list your degree, major, and university:
- BBA, Supply Chain Management, ABC University
Action Verbs For Warehouse Manager Resumes
As a warehouse manager, you must communicate efficiently with your team members, suppliers, and transportation employees. You must be direct and provide clear instructions. How would you reflect that in your resume? By using the right words and structure. Action verbs can help you persuade your potential employer by expressing your responsibilities clearly.
By using accurate dynamic verbs, you will clearly demonstrate your duties in previous work experiences and appear more accountable. However, we understand how easy it is to fall into the temptation of vague terms. That’s why we’ll show you some handy action verbs that you can use for your warehouse manager resume. Take a look below to get some inspiration.
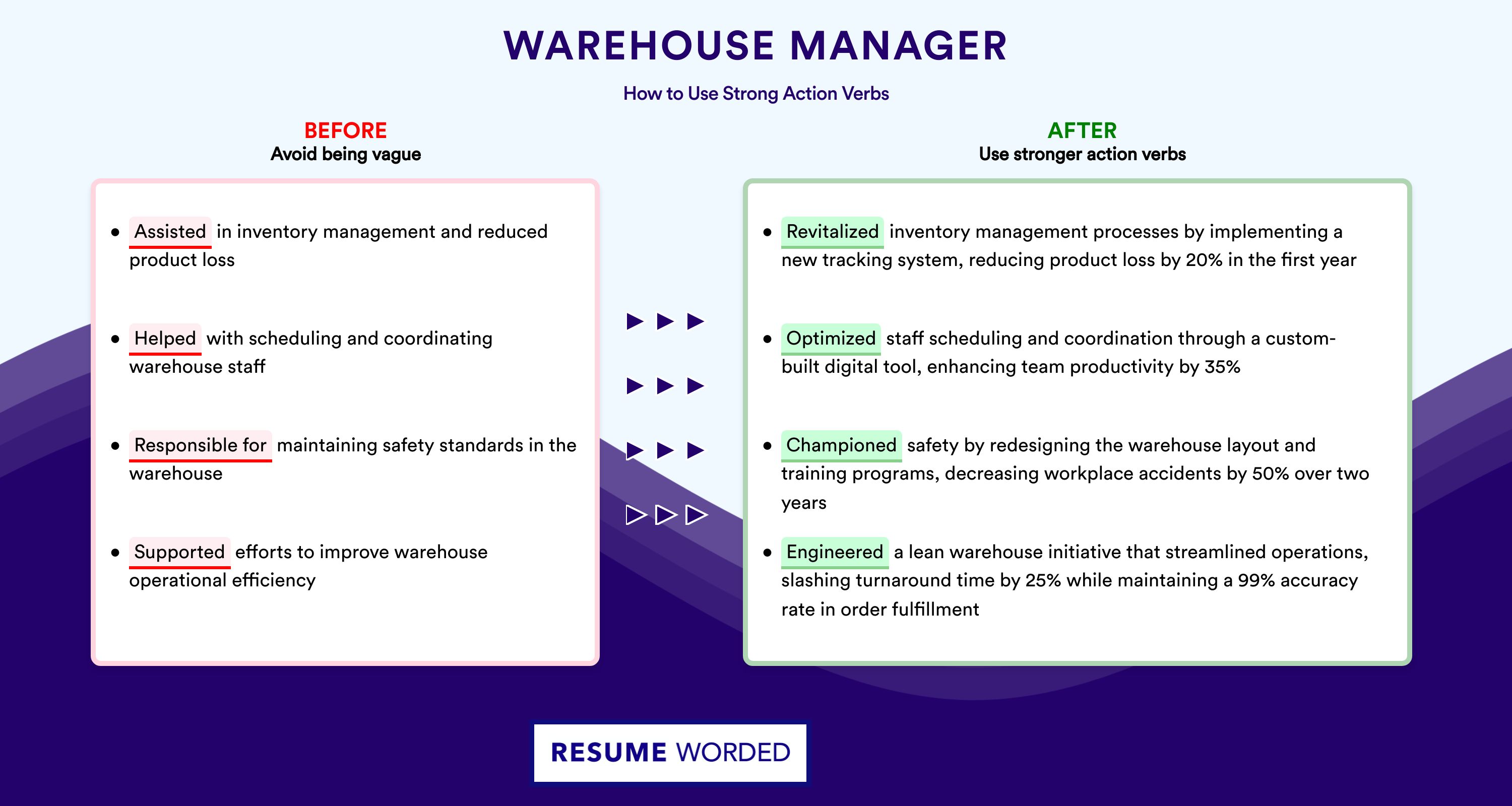
- Accelerated
- Co-ordinated
For a full list of effective resume action verbs, visit Resume Action Verbs .
Action Verbs for Warehouse Manager Resumes
Skills for warehouse manager resumes.
Warehouse managers must have excellent leadership and communication skills. They should have knowledge of administration, math, and business management and be familiar with the supply chain process. As a warehouse manager, you should also have great customer service skills.
If you want to stand out with your warehouse manager resume, try to emphasize your ability to work under pressure since this is a high-paced job. This role requires logical thinking and math literacy, so that’s also something you’d like to highlight. If you need some inspiration for the skills section, take a look below. We’ll show you some industry-relevant skills that you can include.
- Warehouse Operations
- Warehouse Management Systems
- Logistics Management
- Supply Chain Management
- Operations Management
- Transportation
- Inventory Control
- Microsoft Access
- Inventory Management
- Customer Service
- Safety Case
- Forklift Operation
- Continuous Improvement
- Lean Manufacturing
- Warehouse Control
- Third-Party Logistics (3PL)
- Materials Management
- Store Management
- Transportation Management
- SAP Warehouse Management
Skills Word Cloud For Warehouse Manager Resumes
This word cloud highlights the important keywords that appear on Warehouse Manager job descriptions and resumes. The bigger the word, the more frequently it appears on job postings, and the more 'important' it is.
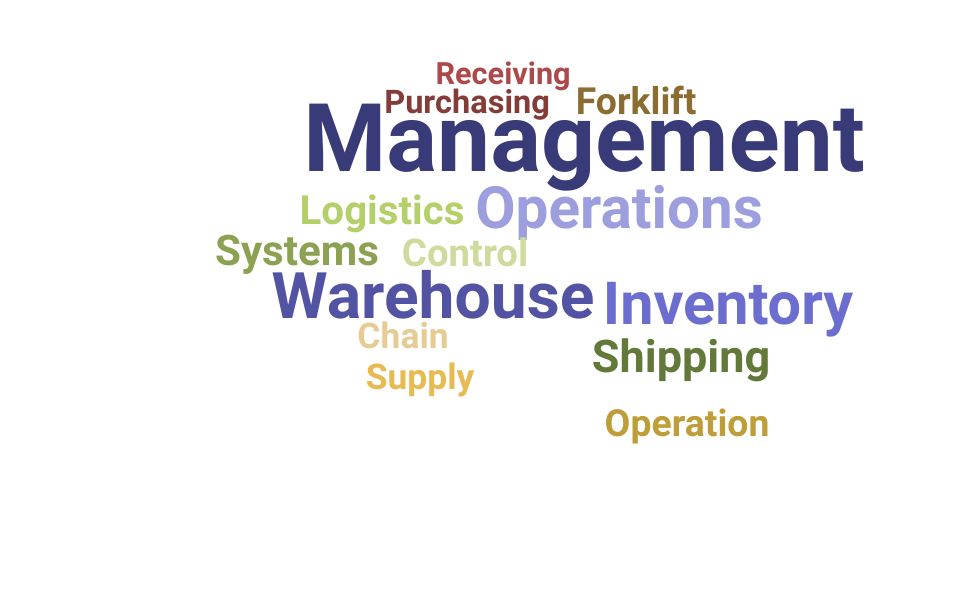
How to use these skills?
Other administrative resumes, business intelligence.
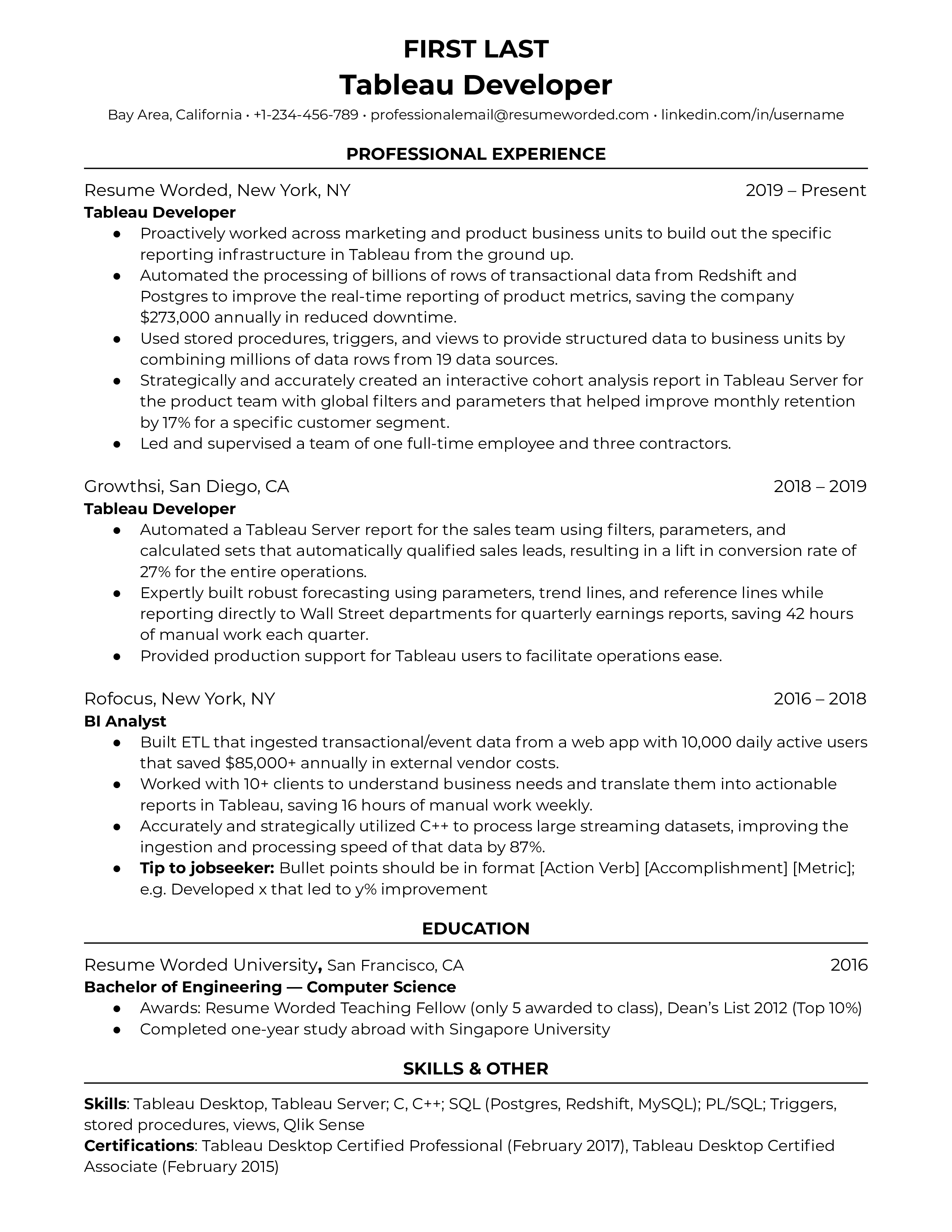
Data Engineer
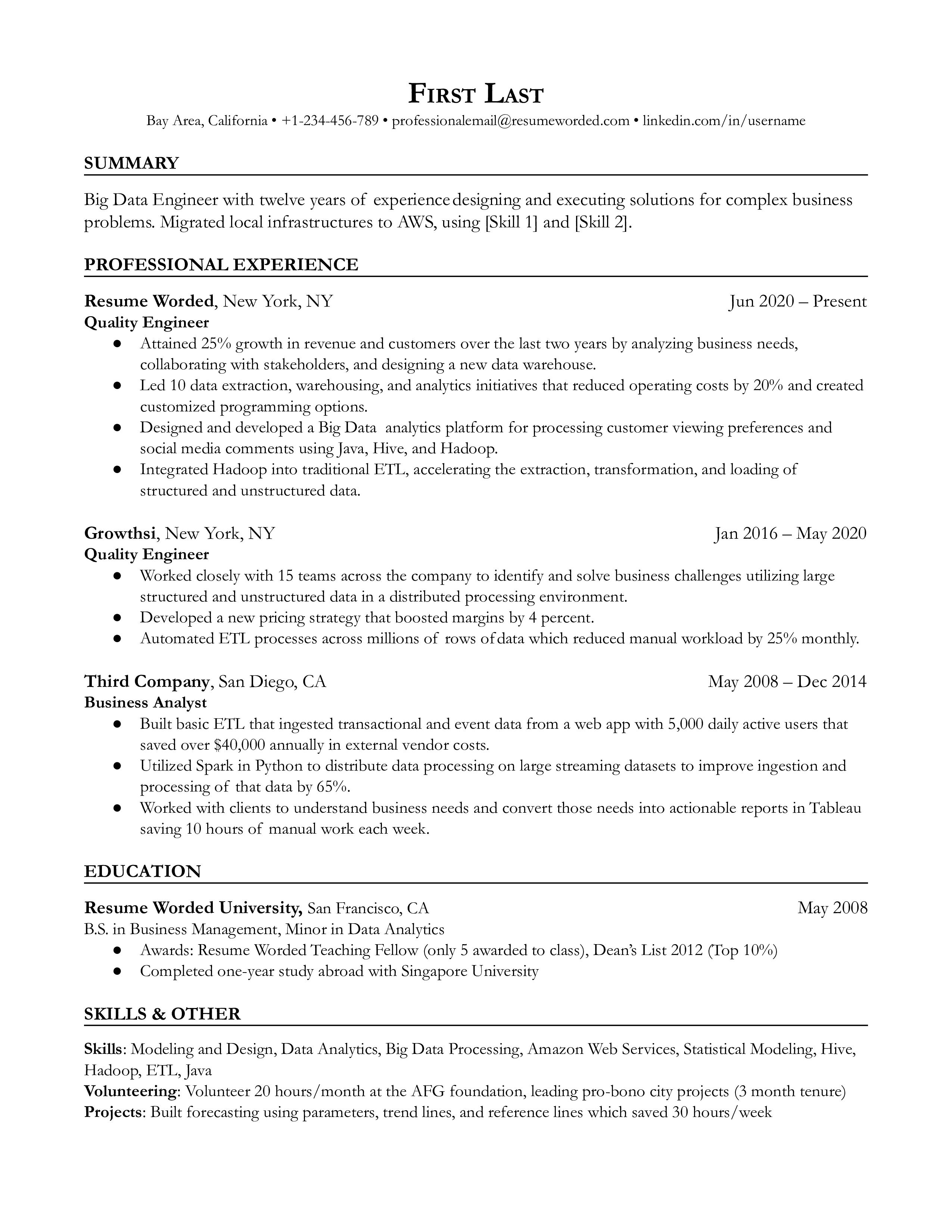
Operations Manager
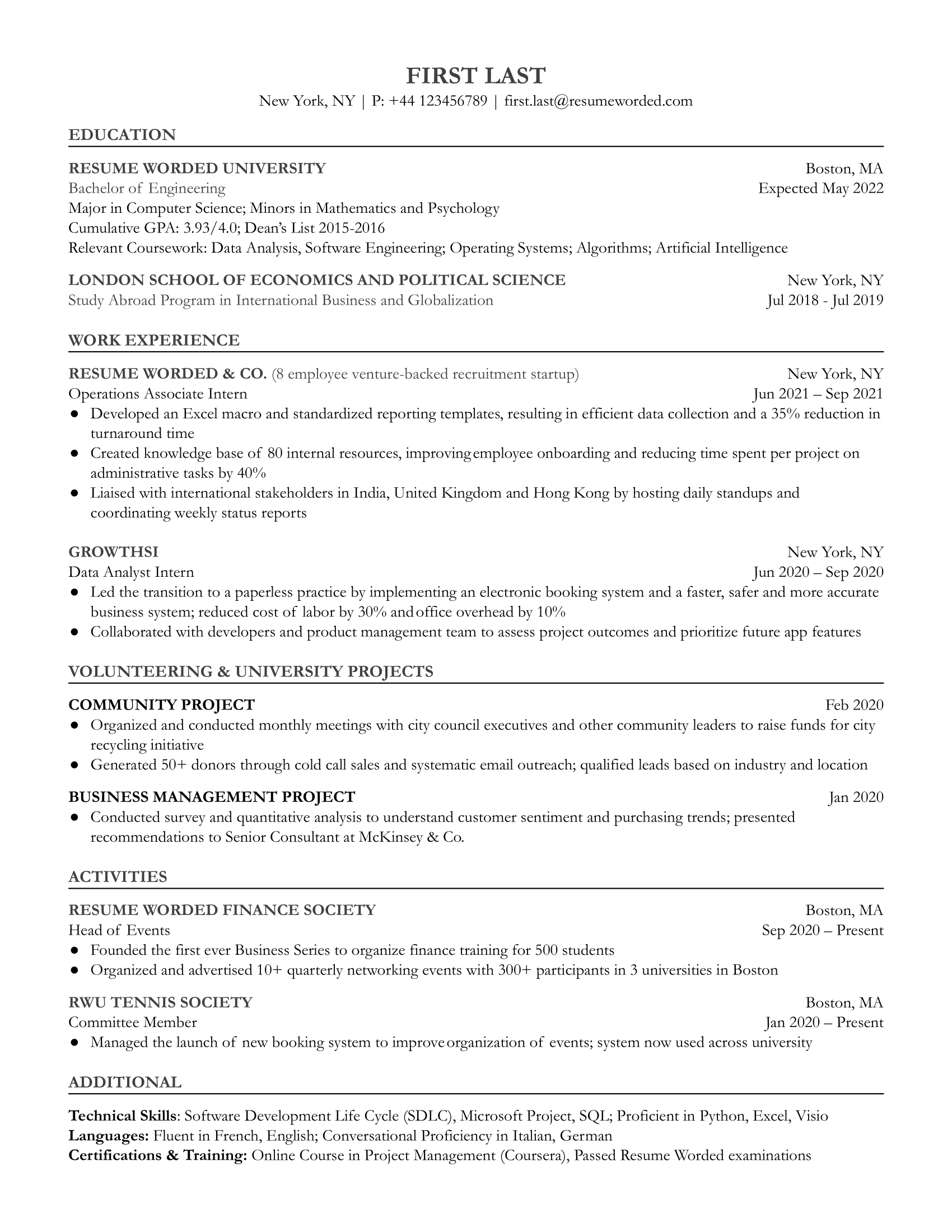
- Customer Service Resume Guide
- Virtual Assistant Resume Guide
- Administrative Assistant Resume Guide
- Executive Assistant Resume Guide
- Office Manager Resume Guide
- Research Assistant Resume Guide
- Customer Success Resume Guide
- Back Office Resume Guide
- Inventory Manager Resume Guide
- Desktop Support Resume Guide
- Loan Processor Resume Guide
Warehouse Manager Resume Guide
- Fundraising Resume Guide
- Service Desk Resume Guide
- Help Desk Resume Guide
- Administrative Coordinator Resume Guide
- Administration Resume Guide
- Scheduling Resume Guide
- Gig Economy Resume Guide
- Project Administrator Resume Guide
- Facilities Resume Guide
- Revenue Cycle Resume Guide
- Warehouse Manager Resume Example
- Warehouse Operations Manager Resume Example
- Assistant Warehouse Manager Resume Example
- Tips for Warehouse Manager Resumes
- Skills and Keywords to Add
- All Resume Examples
- Warehouse Manager CV Examples
- Warehouse Manager Cover Letter
- Warehouse Manager Interview Guide
- Explore Alternative and Similar Careers
Download this PDF template.
Creating an account is free and takes five seconds. you'll get access to the pdf version of this resume template., choose an option..
- Have an account? Sign in
E-mail Please enter a valid email address This email address hasn't been signed up yet, or it has already been signed up with Facebook or Google login.
Password Show Your password needs to be between 6 and 50 characters long, and must contain at least 1 letter and 1 number. It looks like your password is incorrect.
Remember me
Forgot your password?
Sign up to get access to Resume Worded's Career Coaching platform in less than 2 minutes
Name Please enter your name correctly
E-mail Remember to use a real email address that you have access to. You will need to confirm your email address before you get access to our features, so please enter it correctly. Please enter a valid email address, or another email address to sign up. We unfortunately can't accept that email domain right now. This email address has already been taken, or you've already signed up via Google or Facebook login. We currently are experiencing a very high server load so Email signup is currently disabled for the next 24 hours. Please sign up with Google or Facebook to continue! We apologize for the inconvenience!
Password Show Your password needs to be between 6 and 50 characters long, and must contain at least 1 letter and 1 number.
Receive resume templates, real resume samples, and updates monthly via email
By continuing, you agree to our Terms and Conditions and Privacy Policy .
Lost your password? Please enter the email address you used when you signed up. We'll send you a link to create a new password.
E-mail This email address either hasn't been signed up yet, or you signed up with Facebook or Google. This email address doesn't look valid.
Back to log-in
These professional templates are optimized to beat resume screeners (i.e. the Applicant Tracking System). You can download the templates in Word, Google Docs, or PDF. For free (limited time).
access samples from top resumes, get inspired by real bullet points that helped candidates get into top companies., get a resume score., find out how effective your resume really is. you'll get access to our confidential resume review tool which will tell you how recruiters see your resume..
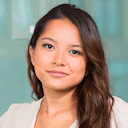
Writing an effective resume has never been easier .
Upgrade to resume worded pro to unlock your full resume review., get this resume template (+ 3 others), plus proven bullet points., for a small one-time fee, you'll get everything you need to write a winning resume in your industry., here's what you'll get:.
- 📄 Get the editable resume template in Google Docs + Word . Plus, you'll also get all 3 other templates .
- ✍️ Get sample bullet points that worked for others in your industry . Copy proven lines and tailor them to your resume.
- 🎯 Optimized to pass all resume screeners (i.e. ATS) . All templates have been professionally designed by recruiters and 100% readable by ATS.
Buy now. Instant delivery via email.
instant access. one-time only., what's your email address.

I had a clear uptick in responses after using your template. I got many compliments on it from senior hiring staff, and my resume scored way higher when I ran it through ATS resume scanners because it was more readable. Thank you!
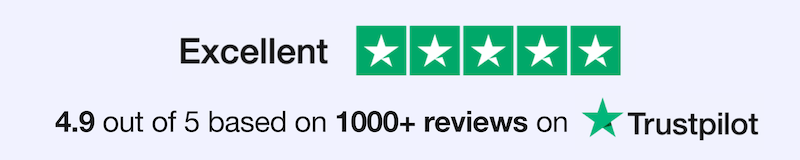
Thank you for the checklist! I realized I was making so many mistakes on my resume that I've now fixed. I'm much more confident in my resume now.
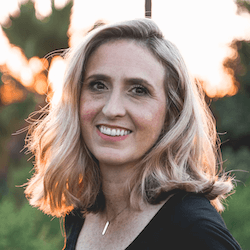
Resume Builder
- Resume Experts
- Search Jobs
- Search for Talent
- Employer Branding
- Outplacement
- Resume Samples
- Warehouse and Inventory
Warehouse Manager Resume Samples
The guide to resume tailoring.
Guide the recruiter to the conclusion that you are the best candidate for the warehouse manager job. It’s actually very simple. Tailor your resume by picking relevant responsibilities from the examples below and then add your accomplishments. This way, you can position yourself in the best way to get hired.
Craft your perfect resume by picking job responsibilities written by professional recruiters
Pick from the thousands of curated job responsibilities used by the leading companies, tailor your resume & cover letter with wording that best fits for each job you apply.
Create a Resume in Minutes with Professional Resume Templates
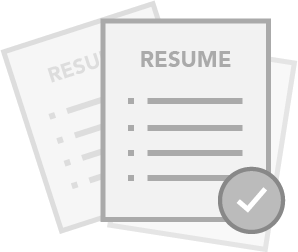
- Oversee the receiving and unloading process for inbound shipments. Direct supervisors to ensure procedures are followed such as product is correct by count and item code; ensure checks for damage, infestation, shelf life and temperature are completed upon receipt and review the labeling, putting away of product and documentation is completed accurately and in a timely manner
- Manage, monitor and maintain proper inventory records of the movement of goods in and out of the Warehouse
- This position will be responsible for assisting the component in minimizing product costs and maintaining tight inventory controls
- Ensures safe working conditions including properly training employees on proper safety methods
- Ensures visibility and accessibility to employees, by practicing Management by Walking Around
- Manage all aspects of the distribution center facility
- Identify process inefficiencies and make recommendations for process improvements
- Manages the engineered standards and pay for performance program for the night shift associates intended to maximize efficiency
- Leading a team of 2 Teamleaders and 40 Warehouse Assistants
- Interviews, hires, trains/retrains, tracks performance, rewards, disciplines, addresses department complaints and quickly resolves employee concerns
- Adhering to Company policies, procedures, and directives regarding standards of workplace behavior in completing job duties and assignments
- CECOME Management
- Managerial Courage
- Process Management
- Develop, execute, and maintain effective and efficient methods of theatrical asset management, storage, and handling
- Provide and execute solutions for ongoing warehouse facility maintenance, organization, and improvements
- Manage daily duties/assignments and ongoing development of warehouse staff
- Develop and manage use of new asset tracking database system, regularly ensuring accuracy of inventory database versus stored assets
- Provide scheduling support and resource allocation for warehouse staff
- Perform regular quality checks of stored assets for maintenance assurance purposes
- Directly ensure and maintain safe work environment throughout warehouse facility
- Ability to multi-task with strong organization skills and attention to detail
- Ability to be a strong leader and a team player with the ability to properly assign tasks to co-workers and motivate them
- Basic computer knowledge and proficiency with the Microsoft Office Suite
- Ability to hold supervisors accountable and delegate accountability to others
- Good knowledge of maintenance and labor saving practices
- Strong ability to engage and communicate with teams
- Demonstrate ability to solve problems, achieve results and foster strong customer service orientation
- Knowledge of Lean, Six Sigma and Kaizen methodologies would be highly advantageous
- Work with the Operations Manager on the operations budgets and be accountable for meeting the established budget for applicable areas
- Strong proficiency with MS Office
15 Warehouse Manager resume templates
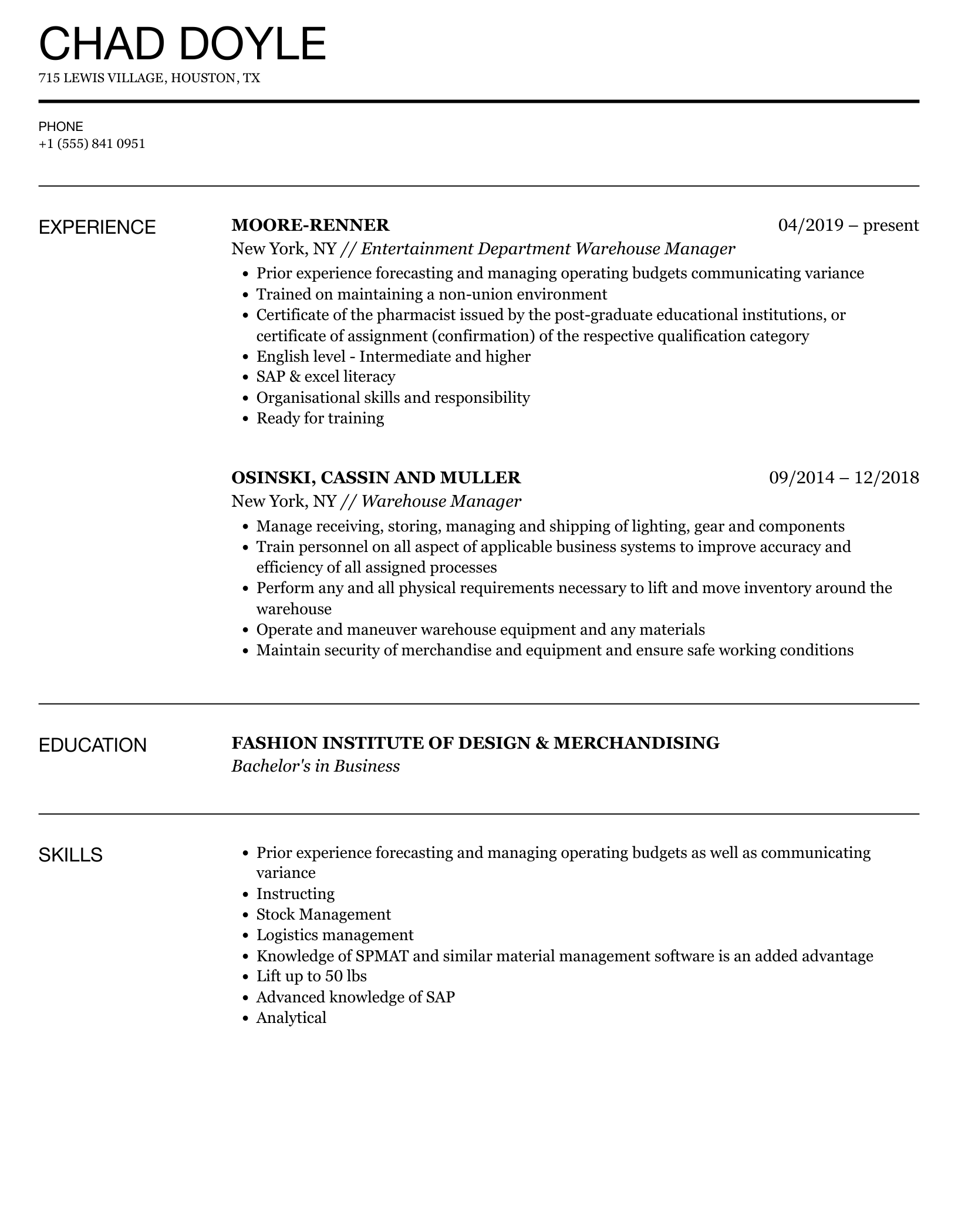
Read our complete resume writing guides
How to tailor your resume, how to make a resume, how to mention achievements, work experience in resume, 50+ skills to put on a resume, how and why put hobbies, top 22 fonts for your resume, 50 best resume tips, 200+ action words to use, internship resume, killer resume summary, write a resume objective, what to put on a resume, how long should a resume be, the best resume format, how to list education, cv vs. resume: the difference, include contact information, resume format pdf vs word, how to write a student resume, entertainment department warehouse manager resume examples & samples.
- With project team support, manage transportation and procurement of assets to/from theme park or project site based on individual production needs and timelines
- Provide information to project team per required needs – Asset inventories, transportation logistics/timelines, etc
- Manage and track annual operating facility budgets
- Ensure facility compliance with regulatory agencies and maintain proper documentation
- Coordinate schedule of use and/or access to facility as required by project team or departmental needs
- Organize, maintain, and track department wide archives (documentation, media, etc)
- Minimum 5 years’ experience of relevant warehouse management experience
- Minimum 3 years’ in a leadership role within entertainment and/or theatrical production
- Solid background in managing and tracking technical elements
- Strong, well-rounded technical theatrical skills and knowledge of warehousing logistics including but not limited to familiarity of theatrical equipment and techniques
- Must be willing to work weekends, holidays and nights as required
- Bachelor’s degree or in Theatre, Performing Arts, Production or related field
- Relevant experience in management of data entry/processing/analyzing
- Knowledge of warehousing and inventory tracking software and aptitude to learn new software applications
- Solid understanding of production of live entertainment in a theme park environment
- Demonstrated ability to work on multiple projects concurrently, with confidence to multi-task and delegate as required
- Background in development and/or management of asset tracking system(s)
- Solid financial and budgeting skills
- Ability to drive results of teams through strong leadership and development skills
- Ability to identify and communicate creative solutions to challenges, and to maintain a consistent focus on priorities with persistent follow-through
- Confidence to communicate across all lines of business, with all levels of management
- Ability to deal well with ambiguity and constant change, working in fast-paced environments with accelerated production schedules
- A strong passion to drive high quality results, both end product as well as process
Warehouse Manager Resume Examples & Samples
- Manages six supervisors whodirect a total of 90 employees
- Delegates and oversees daily work flow including: coordination of workflow, order pick commitment, stock replenishment, and warehouse inventory for 1st, 2nd and 3rd shifts
- Coordinates activities of distribution warehouse with other departments as needed
- Attends and participates in daily department meetings
- Adheres to all CBS Company policies and procedures
- Supports the commitment to safety and follows all safety protocol
- Utilizes WMS, Oracle, MS Office Suite programs daily as required by workload and company communication
- BS Degree (exp. in lieu of education)
- Able to manage staff and lead employees to successfully meet daily commitments
- Able to maintain positive leadership while completing daily work goals in a hectic environment
- Able to prioritize and re-prioritize workflow according to work needs
- Able to analyze reports and implement work flow to meet daily commitments to reach goals, notifies Director when in need of an alternate plan
- Able to complete projects on time and within budget
- Able to work as a team: contributing to brain storming sessions and accepting others input
- Able to delegate work to direct reports
- Able to take initiative
- Able to suggest and implement process improvements
- Able to deal with frequent change and/or unexpected events
- Able to follow instructions
- Able to commit to long hours of work when necessary
- Flexible concerning work hours including both duration and shift
- Able to work in a warehouse environment:walking and standing most of the day, lift up to 50lbs., and support physical work demands as needed
- Excellent Computer/Technical skills (WMS, MS Office Suite)
- Excellent problem solving and decision making skills: able to resolve problems in a timely manner, use team resources to reach best solution, treat employees with respect, inspire trust in them and use good judgment
- Excellent interpersonal skills at all levels
- Excellent verbal and written communication
- Knowledge of transport
- Man Management
- Inventory control systems
- Good Knowledge of continuous improvements
- Operations Management
- Material/ Logistics management
- Management role in automotive suppliers
- Proven track record of Man Management
- Usage of SAP
- Strong Leadership style
- Ability to operate under pressure
- Responsible for opening warehouse according to established procedures
- Manage the day to day operations of the warehouse and processing facility
- Minimum 3+ years warehouse experience (shipping/receiving)
- Able to operate a fork lift
- Ability to interact effectively with the hourly workforce and operations management
- Successful completion of OSHA/DOT physical examination
SAP Business Warehouse Manager Resume Examples & Samples
- Providing input and advice regarding SAP capabilities and functions to customer organizations
- Building positive client and peer relationships by developing an understanding of customer's business and project scope
- Developing exposure to multiple sub-areas within Ernst & Young Canada
- Assisting with the orientation of new team members
- A bachelor's degree in computer science, engineering, accounting, finance or a related field with relevant work experience
- Prior experience working with SAP with several full cycle implementations covering design, build and testing
- Functional hands on experience in SAP implementation and configuration in: General ledger, accounts payable, accounts receivable, and fixed assets in SAP systems features and functionality
- Understanding of integration points with CO, SD, MM, PM, and PS
- SAP Certification is an asset
- Ability and comfort level researching client inquiries and emerging issues, including accounting regulations, industry practices, and new technologies
- Ability to develop and present new ideas and conceptualize new approaches and solutions
- Strong written and verbal communication, presentation
- Excellent interpersonal relations and demonstrated ability to work with others effectively in teams
- Ensure 100% parts availability to internal production lines
- Customer liaison to ensure 100% on time delivery
- Develop and implement internal logistics processes to include FIFO, material flow, warehouse layouts and line side stock presentation
- To ensure successful transfer from projects to Operational Logistics at launch
- Manage material handling budget and maintenance contracts
- Deliver departmental objectives within budgetary parameters
- Implement and develop a warehouse management system
- Continually develop internal control systems to achieve Zero mis-labels at Customer
- Liaise with Materials Manager to achieve best possible inventory levels
- Manage and continually review packaging loops to ensure that adequate supply for Barton Manufacturing and that space utilisation is kept at optimum level
- Ensure all employees comply with corporate and divisional HSE and Ergonomic policies and procedures and safe systems of work
- Degree or equivalent qualified
- JIT/FMCG background
- Proven track record in management of a warehouse. Experience of inbound and outbound logistics is essential
- Automotive JIT sequencing experience
- Experienced people manager who can motivate and direct as appropriate
- Knowledge of SAP systems advantageous, background in warehouse management systems essential
- Exposure to high volume automotive manufacturing
- Project management experience an advantage
- Experience working with Jaguar and Toyota will be an advantage
- Highly motivated self starter who can develop and implement ideas
- Good organisational and communication skills at all levels within the business
- Ability to work effectively within a pressured environment while maintaining positive and respectful working relationships
- Desire and vision to create a world class manufacturing facility
- Responsible for the Retail Merchandise replenishment of a high volume retail store
- Responsible for maintaining Visual Standards within the Coca-Cola store as an output of replenishment
- Manage warehouse using Good Manufacturing Practice (GMP)
- Manage Fleet Operations of Company vehicles to include inspections, service schedule and maintenance, and insurance
- Must be able to communicate cross various functions of the business
- Develop and maintain an effective supply network capability that enhances speed, cost effectiveness and process performance in order to support customer-focused initiatives
- Develop standards/specifications for quality, delivery time, store replenishment and lead-time for orders in order to support customer-focused initiatives
- 4 years managing in a distribution center environment
- Fluency in English required; Spanish or other language(s) a plus
- Capacity Planning and Management: Knowledge of multiple levels of the supply chain used to analyze contingency points, labor staffing and feedback on supplier capacities. Ability to predict suppliers’ capabilities to deliver goods and service necessary based on company system and industry trends. Ability to translate all supplier capabilities associated with commodities, products and/or services. Ability to align supplier capabilities with Company strategy. Ability to comprehend supply/demand market conditions
- Negotiation: Exploring alternatives and positions to reach outcomes that gain all parties’ support and acceptance; striving for outcomes that are a win-win for all parties involved
- Customer and Guest Focus: Making customers (external and internal) and their needs a primary focus of one’s actions; developing and sustaining productive customer relationships; creating and executing plans and solutions in collaboration with the customer
- Labor Management: Proven Ability to manage labor budgets, labor management and scheduling systems, seasonal workforce and staff recruitment
- Facility Safety: Manager a safe environment and deploy proper procedures and processes to ensure safety is first. Vehicle and forklift safety to Company and OSHA standards
- Offload and accurately check all incoming stock for shortages and damage
- Ascertain urgency of orders to be picked up on a daily basis and pick accordingly
- Monitor all orders throughout the day to ensure all orders are collected as were originally requested
- Ensure all paperwork is filled out in and all required information is documented
- Full understanding of custom processes and regulations and work accordingly
- Liaise with different departments (Customer Service, Shipping, Exports) to ensure all deadlines are met
- Operational management of all Warehouse Managers in terms of cost control, Capex projects, standard work, operational effectiveness, cycle counting, stock-takes, hygiene and environmental standards, Health and Safety, CI initiatives, optimum & most efficient use of transport, logistics management and training requirements
- 4 - 6 year's warehouse leading and inventory management experience
- Diploma level qualification
- Experience of managing a new warehouse implementation process
- Detail orientation individual who has excelled in inventory control and management previously
- Experience of leading and motivating small teams
- Detailed Warehousing Systems experience
- A self-starter
- Able to manage staff and lead employees tosuccessfully meet daily commitments
- Able to maintain positive leadership whilecompleting daily work goals in a busy environment
- Able to prioritize and re-prioritize workflowaccording to work needs
- Able to analyze reports and implement workflow to meet daily commitments to reach goals, notifies Director when in needof an alternate plan
- Able to complete projects on time and withinbudget
- Able to work as a team: contributing to brainstorming sessions and accepting others input
- Able to suggest and implement processimprovements
- Able to deal with frequent change and/orunexpected events
- Able to commit to long hours of work whennecessary
- Flexible concerning work hours including bothduration and shift
- Able towork in a warehouse environment: walking and standing most of the day,lift up to 50 lbs., and support physical work demands as needed
- Excellent Computer/Technical skills(WMS, MS Office Suite)
- Excellent problem solving and decision makingskills: able to resolve problems in a timely manner, use team resources toreach best solution, treat employees with respect, inspire trust in them anduse good judgment
Inventory Warehouse Manager Resume Examples & Samples
- Plans, organizes and directs warehouse operations, which includes receiving, retrieving, transferring, and shipping goods in accordance with company systems and controls
- Develops strategies to process and control material flow within the warehouse facility
- Leads the implementation of Lean Manufacturing tools and principals to reduce warehouse lead times, increase labor efficiencies, and improve internal customer service
- Develops and maintains operational plans to include all business requirements which include labor hours, production costs, KPI reporting, and meeting financial objectives
- Develop an accountable supervisory staff with an emphasis on teambuilding, communication, performance accountability, and positive employee relation’s management
- Ensures inventory is being controlled and maintained through cycle count program; reconciling any discrepancies and implementing procedures and processes to ensure accuracies are being maintained
- Ensures that physical condition of the warehouse is being maintained through appropriate cleaning policies, and coordinating with facilities to consistently inspect the condition of equipment, racking, etc
- Safeguards warehouse operations and contents by establishing and monitoring security procedures and protocols; works closely with Security and Environmental, Health and Safety departments
- Develop, implement and direct a safety program designed to ensure the safety of all associates within the work place
- Stay current on new technology which will improve the efficiency of the DC operation
- Strong leadership skills and demonstrate the ability to develop a strong team
- Attention to detail and outstanding organizational skills
- Resolves issues effectively and efficiently
- Minimum of five years of warehouse supervisory experience
- Computer knowledge including, but not limited to, MS Office, WM and SAP preferred
- Directs in-bound and out-bound inventories of merchandise, equipment and supplies to ensure efficient storage and utilization of product
- Tracks, reconciles, and orders product inventories for the Market Center to effectively manage out-of-stocks, out-of-date product and weeks-on-hand to fulfill client needs
- Communicates with affected managers and front line personnel regarding any voids, delays or other product changes that may affect a client delivery as well as to discuss alternative product needs where required to meet client demand
- Communicates with vendors as needed to ensure timely delivery of ordered product and equipment
- Manages warehouse workforce that receives, stocks, rotates and pulls product and ensures that work is completed using safe practices
- Participates in hiring process for warehouse team
- Responsible for the training, coaching and performance management of each member of the team
- Monitors workflow and ensure proper inventories are pulled for daily routes
- Supervises the completion of all daily warehouse work. Models and leads Service STARS culture and safety leadership, and all key initiatives relating to these core values, to provide a positive Market Center environment
- Owns and fosters effective communication at all levels of the organization. Maintains all business records and documentation as required including personnel records, warehouse product and asset inventories, route inventory data and vendor sales, contact and pricing communication
- Requires a minimum of 1 year of relevant experience in warehouse or related operations with a Bachelor’s Degree or 2-4 years relevant experience with a High School Diploma/G.E.D
- DSD Warehouse experience a plus
- Excellent organizational, time management and multi-tasking skills
Assistant Warehouse Manager Resume Examples & Samples
- Daily and weekly meetings with staff
- Be able to perform all aspects of the DC operations including receiving, data entry, order processing, picking, auditing, shipping, delivery, replenishment and merchandise return
- Efficiently maintain product flow through the warehouse and processing accuracy
- Researching and resolving warehouse-to-store issues
- Effective performance evaluations for staff at annual intervals
- Overall organization and maintenance of the facility
- Accountability for all staff members (attendance, punctuality, productivity, accuracy, safety)
- Manage delivery fleet (maintenance and upkeep)
- Ensure safety and security of facility to include warehouse operations and delivery operations, eliminating the temptation of theft
- Maintain all SOX compliance regulations
- Payroll management in the facility
- Maintain good relationships with internal warehouse staff, store management and personnel, and corporate office personnel
- Innovative rewards and accountability tools must be developed, maintained, and updated to keep facility staff motivated and challenged
- Develop hourly and salary staff members under responsibility to take on more responsibility, encourage growth within the company, and increase employee retention
- Effectively maintain seasonal and temporary help, as needed
- High School diploma or equivalent, bachelor’s degree preferred
- Minimum 5 years’ experience in warehouse
- Minimum 3 years warehouse supervisory experience
- Must possess a valid US Driver’s License
- Spanish fluency, plus
- Experience with AS400 inventory management software, plus
- Knowledge of retail products associates with the ski industry, golf industry and cycling industry, plus
- Maintain appropriate inventory levels
- Maintain a clean and hazard free work environment
- High school education or equivalent necessary
- Need to Work Holiday's, Weekends and Moslty Evenings
- Use of Company vehicles (snowmobiles, suburbans, pick-up truck, etc.) , tommy lifts, all back of house equipment, materials and utensils. Palet Jacks, Elevetors, etc
- Manages and coordinates the receipt, stocking and distribution of items at the central warehouse
- Manages the purchasing of all custodial equipment & supplies
- Manages warehouse personnel and drivers for two warehouses. This manager will ensure that all warehouse items are delivered in a timely manner on assigned routes, and in compliance with all organizational rules and regulations
- Works closely with subordinate employees to ensure work is being completed and that work assignments are fully explained when necessary
- Trains team members on a periodic basis to ensure that performance standards are met on a regular basis
- Meets with client/customer to ensure that all deliveries are meeting the customer’s needs
- Responsible for working with customer/client in organizing periodic equipment auctions
- Manages and reconciles physical inventory cycle counts
- Responsible for managing and operating a budget each month
- Develops and maintains a good working relationship with client, customers and vendors
- Completes and submits the required paperwork (expense forms, personal log books, timesheets, work orders, material requisition slips, etc.)
- Communicates effectively with site administrator and building staff
- Bachelor’s degree in related field preferred
- 10 plus years of industry & management experience as well as the ability to manage in a diverse environment with focus on client and customer services. activities
- Must be proficient in Microsoft Office Outlook, Excel, Word
- Experience utilizing Government E-Management Solutions (GEMS) highly desired
- Inventory management and control experience required
- Management Skills
- Associates Degree (A.A.) or equivalent experience in technical industry, satellite, cable, or telecommunications management preferred
- Working knowledge of Microsoft office and inventory software systems and Siebel preferred
- Ability to lead and develop others in achieving company goals and objectives required
- Solid written and verbal communication skills with attention to detail and prioritization required
- Ability to work full time, up to and including 6 days a week, weekends and holidays as needed
- Support all aspects of the General Manager’s vision for Magna Exteriors Belvidere
- Employ strong communication techniques, motivational methods, goal setting and professionalism in the development of exceptional employee relations with all Magna Exteriors Belvidere employees
- Embrace all principles of the Magna Employee Charter and ensure that all Magna Exteriors Belvidere employees understand and follow the same principles
- Provide solid direction to the Materials Warehouse Managers on all shifts, including Brownstown location, toward the attainment of their respective goals and objectives
- Participate in monthly Employee meetings
- Continuously examine the supply chain network in order to identify opportunities to reduce on hand inventory, decrease logistics costs, increase inventory turns, and improve the overall supply chain efficiency
- Employ standardized work practices at all levels within the Materials Warehouse
- Participate in Benchmark activities inside and outside of Magna facilities
- Support Magna Exteriors Belvidere cost reduction initiatives to ensure Customer and Company financial objectives are accomplished
- Support the requirements of Magna’s Capital Appropriation procedure. Analyze all capital expenditures for appropriate value
- Participate in the hiring process for new Magna Exteriors Belvidere employees. Maintain consistent, fair and equitable practices in the hiring and promotion of employees
- Follow the guidelines of the Magna Exteriors Belvidere Employee Handbook and direct all Magna Exteriors Belvidere employees in the correct use of the handbook as required
- Minimum five years’ experience in materials warehouse management
- Receiving: Our Receiving department is the first line of our operation and the Receiving Manager and their associates own receiving, tagging, categorizing, and binning 100% of our new inventory. This department also works extensively with our merchandising department on issues from billing to inventory counts
- Returns: The Returns department runs point on the entirety of our returns operation; overseeing a team of associates who process current inventory returns back into active inventory and manage quality control to the highest standard so we can continue to delight our customers!
- Outbound: This is our largest team, responsible for every aspect of the shipping process including picking, hand folding, and shipping as well as quality control to ensure we are delighting our customers with every “Fix”
- At least 3-5 years of warehouse management experience
- Experience leading and directing a team is a plus
- Proficient in Microsoft Office Suite
- Exceptional verbal and written communication skills
- Ability to collaborate with all levels of management and staff
- Strong multitasker with the ability to meet tight deadlines
- All stocks are to be accurately recorded on Oracle
- Accurately record stocks on Oracle pre-movement
- Carry out daily physical stock counts to cross-check production details, highlight any inaccuracies to production management and ensure that these are corrected by the following working day at latest
- Present metrics including Operator records to Site team and ensure any issues are resolved
- Attend and participation in Site VM meeting
- Maximise the use of storage space. Ensure that products / pallets are safely stacked and racked
- Agree with DFI Master Planner quantity, type and timing of product moves to outside stores
- Liaise with QA, transport and supply chain admin and others as necessary to optimise loading
- Prepare for stock take, take part / facilitate stock take teams and complete stock-take reconciliation
- Ensure that only the correct product type / specification (as cleared in writing/via Oracle by QA) is shipped to customers
- Ensure that all product is shipped on time and in full to customers in good condition with no customer complaints
- Excellent code management to minimise code residues
- Use ERP Dashboards to monitor/analyse stock
- Issue IDB product as scheduled
- Liaise with outside warehouses. Issue product from outside warehouses. Maintain a record of the tonnage stored and loaded from outside warehouse(s). Agree storage and movement statement with outside warehouse prior to receipt of invoice. Pass invoices for payment
- Liaise with Supply Chain Management and Site Manager re changes affecting staff working arrangements so that issues are highlighted and addressed in a timely manner
- Supervise staff to ensure the effective operation of the Warehouse
- Run the Operator CI workgroup meetings and take part in the Powder Supply Chain CI meetings and optimise metrics for both
- Feedback progress to operators on corrective actions based on Operator Metrics/measures
- Select, run and record Problem Solving Events (PSE's)
- Working with the Site EHS Officer to manage Health and Safety within the Stores area including reporting accidents/incidents/near misses; ensuring adherence to safety procedures; completion of Site CRMS tasks
- Participation in Continuous Improvement Initiatives and other projects as required
- Oversee the recording of hours for warehouse personnel i.e. Ensure CORE T&A is updated to reflect hours worked and that coding is correct
- Ensure high standards are maintained in the warehouse and that all product is kept in excellent condition
- Deal with any customer complaints and ensure no over- due actions are present for the warehouse
- Update warehouse related SOPs as necessary
- We are seeking an Assistant Warehouse Manager who will support the Operations Manager and the General Manager in the guidance and control of all warehouse functions
- The Assistant Warehouse Manager will ensure proper products are on hand to support sales volume and product mix and is responsible for ensuring accurate physical inventories and supervising the warehouse staff
- Must have the ability to manage in a diverse environment with focus on client and customer service
- Provide leadership & direction for a team of receivers, shippers and cycle counters including supervision of Oracle receipts, creation of shipping documents and material transfers/deliveries
- Drive process improvements & standards in our shipping, receiving and material handling practices
- Ensure safe work environment in the warehouse for all employees
- Maintain and drive 5S in the warehouse to be best in class
- Responsible for scheduling, workload planning, and equipment required for the receipt, sorting, warehousing and inventory control of all warehoused items
- Manage the traffic responsibility aspects of the import/export activity including order entry review, invoicing, drafting and documentation for export
- Coordinate warehousing activities with production, EHS, marketing and technology including material receipt, storage and delivery
- Supervise day-to-day activity and performance of various 3PLs
- Maintain effective training program for 3PL providers and internal logistics personnel to ensure adherence to established processes and procedures
- Follow Quality Management System policies, procedures and work instructions
- Maintain daily, monthly and quarterly metrics as prescribed
- Other duties as necessary through the evolution of the role & process
- Bachelor’s degree from an accredited university or college
- Minimum of 5 years of experience managing a warehouse & the warehouse workforce
- Proven change management experience
- Experience setting goals and tracking performance to those goals
- 3PL logistics experience
- Strong problem solving, quantitative, and analytical skills
- Ability to lead and direct multi-functional teams
- Ability to maintain focus in an environment subject to constant change and pressure
- Cross referencing physical inventory with digital records
- Scheduling and assigning tasks; monitoring employee work performance
- Maintaining order and cleanliness of warehouse; grounds and offices
- Training and developing staff
- Designing product layout
- Ensuring all items are properly stored and catalogued
- Assisting the team with related tasks, as needed
- At least 4+ years of relevant leadership experience in retail, ecommerce, warehouse operations, or fulfillment
- High school diploma or equivalent; Bachelor’s degree preferred
- Well-versed in domestic and international shipping practices; UPS, FedEx, and USPS
- Trained to operate pallet jacks, forklifts, and other related warehouse equipment
- Outstanding management and interpersonal skills
- Capacity to uphold the company’s high standard of integrity and ethics
- Extremely adept at multitasking and prioritizing
- Bilingual fluency in Spanish a plus
- Oversight of Departmental resources to ensure accurate and efficient productivity, efficient utilization of storage space and equipment, proper protection of materials and company assets while maintain safety
- Must be able to interpret trend and volume-related data to effectively manage Departmental labor resources and forecasts
- Achieves financial objectives by adhering to an annual budget; scheduling expenditures; analyzing variances; initiating corrective actions
- Manager must model customer passion for all levels of teammates across the organization
- This role will directly manage hourly teammates through the use of Team Leaders and Supervisors. Workforce includes staffing provided by a third party service provider. Responsible for coaching, developing counseling, and disciplining employees; planning, monitoring, and appraising job results in a timely manner
- Provide oversight, guidance and training, tools, methodologies and reporting across NPOC Departments in collaborative manner in relation to, inventory control, materials management and related activities
- Responsible for ensuring the health and safety, quality, and productivity targets are met within the Department
- Complies with federal, state, and local legislation as well as Company policies and procedures
- Work with Warehouse Supervisor to create an environment of continuous improvement (Electrolux’s Manufacturing System), Lean principles in all aspects of the warehouse and activities and contribute to the implementation of best practices across the NPOC
- This position will also have direct accountability for the Employee Engagement initiatives and results within assigned Department
- This role has strategic and tactical accountability
- Must have demonstrated ability to execute large-scale improvement projects
- Must have demonstrated ability to eliminate waste through cost reduction projects year-over-year
- Must have demonstrated people management skills, including the ability to motivate, mentor and train others
- Must possess strong interpersonal skills and the ability to lead others
- Six Sigma certification or Lean Certification is preferred
- Must be team oriented and dedicated to continuous improvement
- Must be well organized and able to recognize priorities and plan accordingly
- Must be of high moral character and can perform in a manner consistent with Electrolux values and professional responsibility
- Must be able to lead by example and instill in others a sense of mission, urgency, enthusiasm and company pride
- Possess strong math skills
- Computer proficiency is a must
- Ability to function independently and multi-task
- Supervising office, warehouse, and delivery personnel; potentially across multiple locations
- Managing the daily operations of a warehouse and support fleet operations for a direct store delivery center assuring timely and cost effective service levels in partnership with the sales team
- Entering all computer data such as invoice processing, corrections, inventory, payroll, vehicle management, weekly time, stock outs, and message transmission
- Managing hourly employee recruitment, discipline and compliance of company policies and efficient daily warehouse operations
- Managing the efficient loading and unloading of trucks, work safety management and training, and federal/state/local regulatory compliance
- Conducting accurate record keeping, inventory, damaged/destroyed goods, and the consistent enforcement of company policies
- Managing activities and developing solutions among key groups to ensure order fill, case-fill and on-time delivery
- Completing shipping documentation / invoices and scheduling pick-up for all outgoing shipments
- High School Diploma or GED with significant experience related to warehouse
- Strong computer skills and solid management / conflict resolution abilities
- Experience with process change and Lean / Six Sigma
- Excellent communication as well as demonstrated experience in project management
- Lead a cross trained team to perform the pick, pack, and ship functions for parcel, LTL, and truckload shipments
- Arrange outbound freight carriers, in accordance with shipment planning
- Ensure timely and accurate goods receipts from all inbound channels
- Manage assembly schedule adherence, with a focus on quality
- Maintain an accurate inventory, through accuracy of transactions and a routine cycle count program
- Manage return goods process, assuring timely and accurate disposition
- Maintain monthly warehouse and assembly budgets, managing equipment, service, and supply expenses
- Create, Maintain and adhere to standard operating procedures that support reliable performance
- Drive continuous improvement through efficient warehouse practices
- Practice and enforce all required safety regulations. Correct any violation or poor safety conditions and/or report to management
- Cultivate a culture of quality and focus on the end customer
- Responsible for talent selection, new hire integration, and ongoing development of staff
- Responsible for all Plant Warehouse department performance (Safety, Quality, Service, Employee Morale, Cost)
- Inventory value of $8MM of raw ingredients and packaging materials
- 15MM pounds of bulk raw ingredients
- 3,000 pallets of raw ingredients and packaging materials
- Completion of monthly cycle count process
- Responsible for Distribution Center Department performance (Safety, Quality, Service, Employee Morale, Cost)
- Ensure ASRS performance in support of customer orders and plant production( 19,320 pallets)
- Inventory – 27,900 pallets
- Provide direct customer service to external customers
- Completion of monthly cycle counts and two semi- annual complete inventories
- Develop and maintain effective cost control programs which support Plant and corporate goals
- Supply Chain plant lead with HQ’s: Product Supply, Customer Service, Logistics, Sales, Procurement and DSD functional leads
- Actively lead the implementation of IL6S for the Chicago plant
- Verbal /Written communication skills
- Change Management
- Strategic planner
- Bachelor’s degree (4 yr)
- General Work Experience (Min 4 yr)
- Knowledge of SAP, WMS applications (Min 2 yr)
- Supply Chain – Distribution, Material Management (Min 2 yr)
- Leadership (Min 2 yr)
- Customer Service (Min 2 yr)
- Accomplishes warehouse human resource objectives by recruiting, selecting, orienting, training, assigning, scheduling, coaching, counseling, and disciplining employees; communicating job expectations; planning, monitoring, appraising, and reviewing job contributions; planning and reviewing compensation actions; enforcing policies and procedures
- Achieves operational objectives by contributing warehouse operations information and recommendations to strategic plans and reviews; preparing and completing action plans; implementing production, productivity, quality, and customer-service standards; resolving problems; completing audits; identifying trends
- Meets financial objectives by forecasting requirements; preparing an annual budget; scheduling expenditures; analyzing variances; initiating corrective actions
- Develops warehouse operations systems by determining product handling and storage requirements; developing, implementing, enforcing, and evaluating policies and procedures; developing processes for receiving product, equipment utilization, inventory management, and shipping
- Develops warehouse design by planning layout, product flow, and product handling systems; evaluating and recommending new equipment
- Develops and implements warehouse operations system improvements by Leads continuous improvement projects as assigned, analyzing process work flow, manning and space requirements, and equipment layout
- Maintains safe and healthy work environment by establishing, following, and enforcing standards and procedures; complying with legal regulations
- Secures property by developing protection and access policies and procedures; coordinating patrols with security department
- Updates job knowledge by participating in educational opportunities; reading professional publications; maintaining personal networks; participating in professional organizations
- Troubleshoots all receiving and shipping complaints to find the cause, help resolve the issue, and prevent reoccurrence
- Accomplishes the warehouse operations and company mission by completing related tasks to fulfill the needs of the company and the customer as deemed by the Plant Director or Unit Manager
- Manages warehouse resources, shipping supplies and other consumables, including minor facility maintenance
- A minimum of 5 years of Operations or Logistics experience
- Intermediate PC and database skills
- Strong knowledge of inventory management systems
- Forklift certification a plus
- Experience with Continuous Improvement (i.e. Lean Six Sigma Certification)
- Managing Processes, People Management, Supervision, Data Entry Skills, Data Entry Management, Data Processing, Dependability, Reporting Skills, Analyzing Information , Dealing with Complexity, Deadline-Oriented
- Manages the daily work and safety of associates engaged in order selection, product replenishment, and order loading, to include all warehouse functions, selectors, loaders and night forklift operators
- Manages labor hours and consumable supplies within budget. Prepares work schedules including extra work days and shifts as needed
- Reviews night warehouse functions and various warehouse productivity reporting. Suggests efficiency ideas, cost reduction measures and assists with the implementation of changes within night warehouse. Identifies problems, proposes solutions to other members of management and promotes cooperation with other departments
- Coordinates efforts with Safety department to aid in training, conducting associate observations, updating preferred work methods, conducting accident investigations to determine root causes, and routine safety inspections. Makes recommendations for disciplinary action and/or behavior modification where required
- High school diploma or general education degree (GED); three - five years related experience and/or training; or equivalent combination of education and related experience
- Plan warehouse resources and activities in keeping with ROV objectives and targets
- Establish, monitor, improve, and report key business metrics with a focus towards customer satisfaction
- Improve warehouse organization / layout to reduce cycle time to receive, pull and ship or issue material
- Ensure that workplace’s health and safety requirements are met and take responsibility for the proper storage and security of the warehouse building and material
- Review and improve department processes to increase productivity to eliminate “waste”
- Manage reconciliation of in transit accounts for outbound and inbound intra company shipments
- Train employees, direct work to the appropriate personnel, conduct performance reviews and address and resolve complaints in accordance with OII’s policies and applicable laws
- Create, implement, and track Warehouse group activity, measurements, and KPI’s
- High school diploma or General Education Degree (GED)
- Bachelor’s degree in Business, Operations or Supply Chain Management
- Three (3) to five (5) years related experience; or combination of education and experience
- Oil industry experience preferred
- Responsible for inventory control procedures
- Manages inventory levels to ensure crews have material to meet installation needs, maintaining cycle count accuracy (scrap/adjustments/variance/loss reduction)
- Manages auditable records including but not limited to packing slips, pick lists, Great Plains Journal Entries, job close-out paperwork, warehouse safety audits, etc., ensuring documents are easily retrievable on demand
- Meets or exceeds spend targets as it relates to variable and fixed costs for the warehouse facility via systems currently in place, and/or works with appropriate staff to establish new systems of measurement
- Responsible for hiring, training, and performance management of a team of up to 3-5 employees
- Act and represent the company as a member of a regional warehouses management team and in absence of the Regional Operations Manager this position will be the Sr. Manager overseeing that locations fleet, crews, and operational/office staff
- Mentors and develops warehouse team members for future roles within the company and for vacation and absence coverage
- Determines work schedules and assigns areas of responsibility to warehouse personnel as well as packing, loading, crating, recouping and dispatching
- Schedules maintenance for install and audit vehicles where appropriate
- Oversee receiving and verification freight against receiving documentation, noting discrepancies and/or damage and report findings
- Provides direction and guidance to staff on the vision, policies and procedures
- Reviews and approves all related appropriate departmental vendor invoices for accuracy and compliance
- Trains warehouse and support staff with a 90% retention rate
- A bachelor’s degree in Logistics, Supply Chain, Business, or related field
- Previous supervision or management experience
- Inventory planning systems experience required; Great Plains a plus
- Must be highly organized and process-oriented
- Possess strong problem-solving skills related to people and inventory
- Must be able to lift 50 lbs
- Must have a valid state driver’s license
- Directs and coordinates the overall supply operation at the warehouse level
- Achieves high levels of customer satisfaction through excellence in supply management
- Ensures effective accountability of all assigned property
- Manage supply staff and resources to meet fluctuating requirements
- Ensures stated goals and customer requirements are met
- Interfaces well with the customer and with other functional groups to answer questions and resolve problems
- Informs senior management of issues which could impact productivity
- Provides required reports are delivered in a timely manner
- Utilizes analytical techniques and causative research skills to identify areas for needed emphasis and to recommend improvements
- Monitors production for compliance with scheduling directives, cost factors, and other applicable standards
- Ensures compliance with standard operating procedures and performance standards
- Ensures facilities operate in a safe and efficient manner
- Maintains a professional, respectful and productive work environment
- At least ten years of supervisory experience
- A comprehensive knowledge of governing regulations, policies, procedures in instruction in supply management
- Through knowledge of applicable US Army analytical techniques
- Operational skills and knowledge of Army automated supply systems
- Excellent interpersonal skills to interact well with the customer and with employees at all levels
- The appropriate verbal and written communications skills to conduct meetings, execute plans, prepare reports, plans, and working instructions
- U.S. citizenship and TESA/ASSA certification required. May require a SECRET security clearance
- Ensure all warehouse related processes are operated at the optimum rate, efficiency & aligned with the manufacturing plan & the quality requirements of the work
- To problem-solve either by using departmental expertise or that of the specialists in engineering, quality or production to achieve rapid resolution or isolation of any issues
- Ensure systems are in place to effectively control stock accuracy and manage the annual stock-take processes
- Ensure effective planning of inbound freight schedules to meet inventory requirements and maintain effective communication to ensure the relevant people are kept appraised of when Goods are scheduled to arrive
- To manage onsite storage of finished goods in the canopy area
- Ensure systems are in place so that shipments are compliant with all Dangerous Goods Regulations and Directives
- Ensure systems are in place to create formal packing specs, from drafts received from packing dept
- Minimum 5 years post-graduate experience in warehouse management, with the last 2 years in a manufacturing leadership role, preferably in a business manufacturing mechanical engineered products and/or gas pressure systems/ components
- Proven experience managing a complex MRP system
- Proven experience of warehouse management and stock control
- At least 5 years relevant experience in a similar environment, ideally backed up with a IOSH qualification. Preferably educated to degree level, but not essential
- Must have an excellent understanding of best practice warehouse management, inventory control and accuracy and have the ability to manage and develop a team, whilst driving change
- The position requires an inspirational leader and outstanding team player, who is self-motivated and can translate plans into results. This individual will be strong in analytical, problem solving and decision making skills with a passion for safety, customer care and quality together with excellent communication skills
- Achieves operational objectives by contributing warehouse operations information and recommendations to strategic plans and reviews; preparing and completing action plans; implementing production, productivity, quality and customer service standards; resolving problems; completing audits; identifying trends
- Meets financial objectives by forecasting requirements, preparing an annual budget, scheduling expenditures; analyzing variances; initiating corrective actions
- Develops and implements warehouse operations system improvements by leading continuous improvement projects as assigned, analyzing process work flow, manning and space requirements, and equipment layout
- Maintains safe and healthy work environment by establishing, following and enforcing standards and procedures; complying with legal regulations
- Accomplishes the warehouse operations and company mission by completing related tasks to fulfill the needs of the company and the customer as deemed by the Unit Manager
- A minimum of 8 years of operations or logistics experience
- A minimum of 5 years of supervisory experience
- Strong PC and database skills
- Strong knowledge of inventory management system
- Experience with Continuous Improvement (i.e. Lean Six Sigma certification)
- Develops and conducts training programs related to export compliance
- Provides support and advice to division regarding licensing requirements and related international issues on proposals; bids; and ongoing contracts
- Supports International Travel Export Authorization requirements
- Maintains current knowledge of relevant regulations; procedures and practices
- Manage the accurate accountability; inventory; storage; shipment; and turn-in of any TESS training aid/device
- Provide electronic reporting for workload; usage rates; damage; accurate timely inventory; system availability; manpower and other factors affecting mission
- Conduct inspections and record equipment deficiencies on appropriate Government forms
- Record and report damage
- Conduct functional test(s) of TESS training aids/devices
- Implement electronic inventorying and accurate accountability measures
- 8-10 years of related experience in logistics management/supervision and logistical support ops with working knowledge of industry inventory systems; FAR export/property control and compliance; preferably in the professional services industry. Familiarity with MILES ; NTC and related equipment is required
- Receipt, storage, movement and issue of all Plant materials and recording
- Contacts with all levels of management within the plant
- Contacts with Abbott personnel in other affiliates especially in QA / Planning /Shipping / Distribution / Marketing
- Contact with suppliers for material receipts
- Contacts with Customs / Revenue in relation to Finished Goods shipments and documentation, Product Rebates, Authorised Economic Operator and Known Consignor status
- Manage the receipt, storage, movement, issue and recording of all movements
- Maintain required levels of cGMP across all storage areas including working with the external warehouse provider
- Manage the Finished Goods shipping process liaising with ALOG, the external warehouse, shipping lines and Revenue (on line shipping documentation)
- Maintain all inventory records and accuracy levels and maintain all required shipping documentation to meet Revenue and Abbott requirements
- Control equipment including maintenance and contracts on Forklifts, Automated Guided Vehicles (AGV’s), lifting, cleaning and storage equipment
- Monitor warehouse conditions including temperature, access (security), pest controls and general housekeeping in line with policies and procedures
- Minimize distressed inventory
- Liaise with IT on the various systems supporting a smooth warehouse operation including Shipping Documentation, AGV support and general Manufacturing Control System (MCS)
- Promote use of Inventory Control System MCS and Shipping System
- Manage Shipping to ensure product availability and ensure no backorders including use of Air Shipment if required
- Work with Customs to maintain status of Authorised Economic Operator (AEO) and Known Consignor (if required)
- Manage the security aspects of incoming material receipt and warehouse access (both internal and external warehouses) to meet the requirements for FDA approval and AEO / Known Consignor status
- Work with Planning to maintain settings/parameters and base data in the Inventory Control System and Shipping Documentation System
- Generate and review warehousing/inventory metrics
- Generate and issue Warehouse status reports for Abbott Cootehill
- Foster a culture of continuous improvement through active deployment and participation in the plant’s Business Excellence Programme
- Ensure adequate training and development of the warehouse and shipping staff to perform their role safely. Foster a culture of environmental and safety awareness as required by the site EHS program
- Meet target project dates and achieve budget targets for the warehouse and shipping areas including control of the external warehouse costs
- Keep up to date with new ideas and latest technology relating to the functional area including labeling, bar-coding, shipping software and Revenue changes
- Maintain close liaison and co-operation with all other departments, affiliates and personnel in order to optimize the plant’s operations
- Ensure execution of activities in compliance with Abbott Cootehill and Divisional Quality procedures and policies
- Ensure Environmental Health & Safety standards are met and all EHS regulations and procedures are adhered to
- Complete all activities in a safe manner ensuring that any potential safety issues and areas for improvement are addressed
- Ensure Environmental procedures e.g. recycling, waste minimization is adhered to and improvements made where possible
- Optimise the use of human resources by encouraging an atmosphere of involvement, open communication and effective teamwork
- On an annual basis, establish the functional goals for area of responsibility with Manager. Update and review progress against goals on a quarterly basis
- Complete Goal Setting, Performance reviews/appraisals and Development plans for direct reports
- 4/5 years’ experience in manufacturing environment as a people manager with a minimum of 1 year in a logistics or supply chain role
- Manage the overall warehouse activities to be in compliance with company’s policies and vision
- Oversee receiving, warehousing and distribution
- Set up layout and ensure efficient space utilization
- Adhere to all warehousing, handling and shipping requirements
- Comply with all applicable OSHA, EPA, HACCP and ADM health and safety work practices, production and material handling procedures
- Manage inventory level and status at assigned warehouse location
- Monitor warehouse and inventory conditions
- Recruit, select, orient, coach and motivate employees
- Administer supervisory responsibilities in accordance with the company’s policies and applicable laws, including interviewing, hiring and training employees; appraising performance; rewarding and disciplining employees; addressing complaints and resolving problems
- Develop strong partnership with plant management, planning, transportation, quality and inventory control
- Produce reports and statistics regularly (In/Out Status report, dead stock report, damaged inventory, etc.)
- Warehouse management experience
- Ability to implement process improvement initiatives
- Hands on experience with warehouse management and inventory system
- Bachelor’s degree preferred, or Associate’s degree with 3+ years of experience demonstrating progressive responsibility in warehousing preferably in the food industry or equivalent
- Implement the Manufacturing plans as established by the Production Scheduling Operation, specifically to materials availability and associated work orders, utilizing lean processes that will assure highest possible quality products at the lowest possible cost, delivered in accordance to schedule commitments
- Provide leadership in the attainment of goals with respect to safety, quality, cost, utilization, efficiency, on time delivery and compliance. Providing expertise in international shipments. Troubleshooting any issue that may arise in international freight transportation and handle technical details relating to custom regulations and necessary documentation for international shipments
- Develop necessary business plans to enhance all material requirements; including throughput, labor hours, digitization improvement and accuracy utilizing lean / six sigma tools. Own collection and monitoring of operational data to ensure potential problems are averted and maximizing efficiency
- Implement process / product improvement programs and provide process method excellence throughout the warehouse organization
- Interface with other internal organizations, customers and vendors to assure requirements of quality, cost and timing are assured including expediting if necessary
- Select, hire, train, develop, and provide ongoing leadership and direction of assigned personnel
- Provide ongoing supervision, accountability and counseling for employees, guiding them in current positions and assisting with career development and training
- Ensure communication of key business / customer issues to employees
- Ensure assigned employees are aware / comply with all GE, government, and customer policies, procedures, rules and regulations where applicable
- Bachelor’s Degree from an accredited college or university
- Minimum of 5 years of experience in a warehouse leadership position
- Strong ability in computer systems including CAS Production System, Oracle and SAP
- Ability to develop and motivate a high involvement team through commitment to meeting customer and organizational goals
- Knowledge of warehouse policies and regulations established by businesses, as well as, government and other customers
- Strong problem solving and analytical skills with the ability to identify critical issues
- Knowledge of the disciplines of warehouse management such as production and inventory control, lean / six sigma and standard cost systems
- Strong propensity for excelling in a demanding environment
- Manage all primary warehouse and store facilities as well as secondary off site facilities
- Manage the warehouse staff, warehouse storage space and warehouse inventory
- Plan, organize, implement and review warehouse activities to maximize efficiency and effectiveness
- Management of stores distribution and movement to and from the Warehouse and Stores
- Ensure implementations of Standard Operating Procedures within the warehouse environment to ensure that the department is in compliance with all company policies and procedures
- Ensure that stock levels are securely maintained to meet customer needs and inventory budgets
- Ensure that all inventory reports are prepared timely and accurately
- Monitor and control rotating stock to ensure quality accuracy, delivery and distribution of stock
- Ensure Occupational Safety & Health practices and policies are implemented and adhered to
- Liaise and communicate with external suppliers and internal clients
- Check and monitor all operational procedures and raise corrective actions or recommend change to procedures as required
- Ensure the safety and security of warehouse and storerooms are maintained and monitored
- Conduct cyclical physical stock check for all inventories and investigate significant discrepancies
- Provide guidance to warehouse staffs in accordance with company's code of conduct and warehouse management ethics
- Experienced in the assembly, testing, or repair of electronic devices
- Valid driver’s license for the state in which you are based
- Basic mechanical assembly skills
- Basic knowledge of electricity, electronics, and mechanics of gaming type devices
- Ability to read and understand schematics and service manuals
- Strong customer service
- Desire to lead and help others
- Pleasant personality, especially towards customers
- Open warehouse according to established procedures
- Manage supply inventory including ordering supplies to ensure adequate supplies are in inventory to meet the requirements of all jobs
- Coordinate shipping and receiving operations for warehouse operations
- Manage the loading and off-loading of trucks with supplies
- Organize supplies in the warehouse
- Direct warehouse team as necessary
- Maintain the up keep of the warehouse yard
- Assists Operations (chemists, field services and wastewater) with truck loading process
- Check the supplies for all work teams trucks to ensure they match needs of jobs (e.g. assess all loads to ensure proper container type and supplies, PPE, etc.) – sign off approval process
- Conduct spot truck checks (license, registration/insurance/DriverLog/VIR)
- Ensure truck permits, registrations, stickers are up to date and works with Manager to ensure paperwork in binders are up-to-date regularly
- Interact with chemist teams to ensure they are familiar with safety-related equipment, etc
- Maintain inventory and calibration/maintenance of critical operations equipment (SCBAs, digital scales, printers, etc.) – utilizes equipment/inventory tag system
- Maintains Meters/Monitors program - inventory, maintenance (charge), calibration
- Inventory and maintenance of ER Supply Cage
- Conduct STOP audits in Warehouse (at minimum) quarterly
- Spread salt on entry/exit ways to ensure safety in warehouse during the winter
- Minimum 1 year shipping & receiving experience - required
- Minimum 1 year supervisory experience - required
- Computer experience including MS Office - required
- Must be able to ride ski lifts
- Must be able to work in extreme outdoor weather conditions, at night -required
- Repetitive lifting, 50 - required
- Valid driver's license including motor vehicle record & criminal background check - required
- Previous experience with snowmobile, snowcat and forklift operation - preferred
- Spanish speaking - preferred
- English speaking/reading/comprehension - required
- Advanced knowledge of warehouse distribution principles and techniques
- Proficiency with Microsoft Office products; intermediate to advanced knowledge of Excel
- Working knowledge of DynMRO preferred or experience in the handling and management of government property strongly desired
- Good interpersonal and supervisory skills with an ability to lead, coach, and manage others
- Eight (8) years of progressively responsible experience in a warehouse environment
- One (1) year of previous supervisory experience
- Hazardous materials certification required
Regional Warehouse Manager Resume Examples & Samples
- Interface directly with customers (internal and external), suppliers, National Distribution Center and DSO Sales Leader(s) to assure goal alignment and performance metrics
- Provide interface with National Distribution Center regarding orders, warehouses, and delivery
- Initiate, plan, and support orientation and training programs
- Coordinate the move and/or opening of new facilities
- Identify, develop, and implement operational best practices and processes improvements for local field warehouses to improve productivity, cost effectiveness, and customer satisfaction
- Responsible for inventory accuracy
- Stock and arrange product to ensure warehouse inventory turns
- Coordinate annual warehouse inventory
- Oversee inbound and outbound shipments; resolve delivery issues
- Schedule incoming freight from factories around daily activities
- Coordinate with local and regional freight companies (setup times, hot shots, etc.)
- Ensure dealer receives undamaged product
- Oversee cleanliness of warehouse
- Load and unload freight with forklift
- Other support services as needed
Logistics / Warehouse Manager Resume Examples & Samples
- Management of the timely data collection to update operations metrics on an hourly basis, in an inventory control and systems environment, to achieve productivity targets, reduce cost per unit, eliminate errors and thus deliver excellent customer service
- Implement change and contribute in cross-functional Six Sigma initiatives within your site and the broader Amazon EU Operations network
- Drive continuous process improvement and make our customer experience better than ever
- Be degree qualified
- Have experience in leading large and diverse teams
- Possess the ability to manage detail, establish root cause and be able to extract and analyse data. Must be able to demonstrate effective problem-solving and analytical capability
- Thrive on change, inclined to operate with flexibility and commit the time required to get the job done. Work shifts, including weekends, in an operational 7/365 environment. Willing to relocate if necessary
- Manage and drive staffing plans, schedules, quality initiatives, performance levels, process change initiatives, and other Process Improvement/ Six Sigma initiatives to enable Operations and ultimately the FC to attain Amazon&rsquos Business Plan
- Manage a team of approximately 200+ (400 in peak season) employees within a very fast-paced/ time-critical and demanding environment. This will include the setup and implementation of career development plans for all your Direct Reports, i.e. the Area Manager
- Manage a shift directly and a major process directly or indirectly & becoming a subject matter expert in your area
- Set / clarify requirements and expectations for Area Managers and Team Leaders
- Work closely with other support teams (HR, Financial Manager, Facilities Manager, Safety & Security Manager, IT Manager) to build and secure support and resources for projects and initiatives
- Carry out supervisory responsibilities in accordance with the organisations policies and procedures
- Implement change and/or develop new processes as required to provide ability to better direct ship multiple products to multiple locations and geographies
- Participate from time to time in cross-functional Process and Business Improvement projects within the FC and the broader Amazon EU Operations network
- Significant Operations team leadership experience in a similar fast-paced process driven manufacturing, production or distribution/logistics environment
- Excellent communication skills with the ability to communicate to all level
- Demonstrated ability to manage, motivate, and influence work behavioursPracticed working knowledge of Lean techniques such as Kaizen or Six Sigma
- Demonstrated problem solving and analytical capability
- Demonstrate the ability to manage detail, establish root cause and be able to extract and manipulate data
- Able and willing to work to flexible schedules/ shifts and commit the time required to get the job done
- Bias for action - this role is fundamentally about managing and driving production within specified area/s and process improvement through efficiency and change
Warehouse Manager Designate Program Resume Examples & Samples
- Provide timely service to customers while minimizing warehouse and production costs
- Schedule the receiving and delivery of raw material and finished products in a timely manner
- Supervise the efficient loading of orders to minimize customer out of stocks
- A minimum of 3 to 5 years of Operations or Logistics experience
- A minimum of 2 years of supervisory experience
- Manage and prioritise workloads to deliver the required output in order to service external and internal customers
- Lead and motivate the team to sustain a world class approach to 5S and warehouse organisation, identifying and implementing improvements
- Measure, maintain and report department KPI’s including cycle counting, goods receipt on time, overtime, and customer complaints
- Lead the warehouse training and development strategy ensuring each operator understands their part in the business and has the opportunity to develop
- Lead the implementation and evolution of our zero harm culture within the warehouse
- Ensure work is carried out in a safe manner and all near misses, incidents and accidents are reported and investigated
- Work experience within a warehouse environment, ideally within the chemical sector
- Computer Literacy with a high proficiency in major IT tools including SAP and Microsoft Office
- Strong leadership and people management skills and experience. You will positively influence and act as a role model for the team
- Excellent organisational skills, with the ability to multitask and adapt to changing priorities
- Good communications skills across all levels of the organisation
- Knowledge and experience of lean manufacturing tools and techniques
- Fork lift truck license or the capacity to learn
- Bachelor’s Degree from an accredited university or college
- Minimum of 3 years of experience in logistics, warehouse and/or manufacturing operations
- Bachelor's Degree in Business Administration, Logistics or Materials Management
- Bilingual (Spanish and English)
- Strong interpersonal and demonstrated proactive leadership skills
- Lead initiatives of moderate scope and impact
- Effective problem identification and solution skills
- Strong planning skills
- Strong computer skills in MS Office and similar platforms
- Inventory systems oriented. Knowledge in SAP-ERP system
- EHS, OSHA, DOT regulations oriented
- Supply chain courses and/or certifications
- Lead and supervise a team of Shift Managers (2-5 front-line supervisors depending on location) and associates in outbound or inbound operations
- Responsible for the overall safety, quality, performance and customer experience of the shift
- Carry out supervisory responsibilities in accordance with the organization’s policies and procedures
- Accountability for meeting and exceeding operational goals
- Strategic planning and forecasting; appraise performance; resolve problems; and address staffing needs
- Mentor, train and develop teammates for career progression and learning
- Ability to develop and share best practices across the shifts and network
- Direct management experience for a salaried employee population and its performance
- Experience with performance metrics and process improvement and Lean techniques (how, when, who)
- Candidates must be flexible to work weekends and/or overnight shifts regularly
- Degree in Engineering, Operations or related field and MBA preferred
- Experience with a contingent workforce during peak seasons
- Ability to handle changing priorities and use good judgment
- 5+ years management experience in a manufacturing, production, delivery or distribution environment
- Interest in long-term career development
- Proficient in Microsoft Office, especially Word and Excel
- Proficient with Maximo Asset and Inventory Management modules
- Familiar with CostPoint database in receiving assets
- Four (4) years of progressive experience, including management of a small staff in a high volume receiving/inventory or supply management environment
- Strong organizational skills, be analytical, and have a high capacity for attention to detail
- Experience in inventory control and materials planning, including experience in tracking and replenishing bulk inventories
- Knowledge of computerized inventory and purchasing systems is required
- Knowledge of hazardous waste management procedures
- Ability to manage workloads effectively, including adapting to changes, planning, organizing, and prioritizing work
- Able to work effectively under stress and pressure
- Able to research, analyze, and evaluate information and make good decisions based on inventory data
- Knowledge of computer software, including spreadsheets and word processing is required
- Familiar with FAR 52 and 45 Government Property clauses
- Able to work effectively in a diverse workforce
- Education: Associate’s Degree required - Logistics diploma/certificate/training is highly preferred
- Security Vetting: Must successfully obtain an MRPT - must maintain eligibility at the required security level for the duration of the contract
- Language Skills: Must be able to communicate effectively in English, both orally and in writing, with all levels of employees and vendors
- Citizenship: U.S. Citizenship is NOT required for this position
- Medical: Favorable passage of a drug screen and physical examination
- Driver’s License: Valid Driver’s License from Home of Record (HOR)
- Manages the engineered standards and pay for performance program for the warehouse associates intended to maximize efficiency against the engineered standards
- Reviews, tracks and analyzes Critical Success Measures and compares the results with the targets on a regular basis; develops and implements plans for improvement in areas such as order filling errors, late deliveries, and overall service levels
- Good negotiating skills
- Supervise the distribution departments engaged in processing product
- Help drive the Operations team to create and follow standard work that enables 100% takt attainment, while maintaining a safe environment and a zero defect product
- Create an environment that promotes career development, motivates team members to share their career goals and where you assist them with forming a plan to meet those goals
- Promote lean cultural transformation, 5S program, usage of value stream tools and visual factory
- Advocate for transformational change by identifying techniques to break down barriers, while encouraging employees to participate in Rapid Improvement Events (RIE’s) and change their way of thinking
- Encourage employees to perform safely and to their highest ability by acknowledging their efforts and rewarding them accordingly
- Build a sense of community within the team by promoting a team environment, actively listening to employees need sand providing coaching where necessary
- Conduct performance reviews to provide production team members and team leaders with constructive feedback in order to improve their skills and performance
- Responsible for fostering an environment where all employees are treated with respect and dignity, there is an emphasis on open communication throughout the team and business goals are actively clarified
- Integrate processes, teams, people, and resources to achieve daily and long term operating objectives for shop operations in safety, quality, customer delivery, costs and people development
- Consistently apply Trane policies and procedures
- Develop and meet budgets, operating plans and control costs for shop operations
- Plan requirements and organize equipment, material, and manpower to meet required production, quality, and cost goals
- Managing Supervisors and Team Leads assisting them in meeting production requirements, approving work schedules, and in hiring, transfers, discipline, dismissals, and planning budgets
- Meet production schedules and maintain quality levels while maintaining low cost
- Prepare and gain approval for the annual operating budget and maintain control of operation within the budget including monitoring controllable expenses and labor variances and implementing cost reduction programs
- Seek out and implement new processes in conjunction with Engineering
- Work closely with Supervisors to resolve operational problems
- Develop and maintain excellent working relations and communications with Customer Service, Buyers, and Planners to assure a functional operation
- Develop and maintain charting for cell productivity, on time order delivery, quality of shipment, etc
Divisional Warehouse Manager Resume Examples & Samples
- Providing primary leadership for warehouse location in Flagstaff, AZ
- Addressing insource vs. outsource in addition to optimum use and practices within existing warehouse network
- Hiring and developing warehouse team members
- Understanding key business processes for warehouse areas and propose right-sized IT/System solutions to support them
- Providing shipping/receiving function with leadership and development of functional excellence
- Maintaining accuracy of information in system databases used for capacity and planning purposes
- Collaborating with Buyer/Planners to establish appropriate inventory levels of warehouse items
- Managing critical parts inventory and distribution
- Driving continuous improvement projects for areas of responsibility
- Successful experience implementing warehouse strategy and associated change management activities
- Strong written & oral communication skills and ability to prepare/deliver presentations and lead meetings
- Lead a warehouse team of fifteen staff members and four apprentices in a functional and disciplinary capacity
- Plan, organize, and supervise day-to-day business, while ensuring customer quality standards are met
- Handle department-specific customer complaints and initiate suitable countermeasures to prevent problems arising in the future
- Hold appraisal meetings, ensure cross-functional skills, and oversee development of team
- Maintain, optimize, and monitor departmental processes (analyses, ABB regulations, IRIS, and ISO9001)
- Oversee warehouse management, monitor operations center, perform annual and quarterly stocktakes, and conduct reporting
- Provide reports for head of department and senior management with regard to warehouse capacity, planned process changes, etc
- The successful applicant will be responsible for Managing, leading and developing Vestas warehouse and logistical operations in the region of NSEA. Primary focus upon Japan and South Korea. Including managing and guiding 3rd party warehousing and logistical operations providers in accordance with Vestas leadership model
- Ensuring alignment across functions in the NSEA region (Order handling, Sourcing & procurement, Forecast & Planning and Transport & Logistics)
- Follow up on KPI’s and maintain daily management board in all warehouse locations
- Primary responsibility and focus on Safety
- Responsibilities also include staffing, warehouse operations and P&L reporting
- Provide leadership and direction for all operations functions, coordinate monitor and measure the operations activities, implement effective methods and procedures throughout, manage operational equipment and resources
- Lead and manage QSE compliance in relation to role
- Develop and foster “Safety First” culture. Implement Vestas safety policy and ensure compliance
- Ensure all operations are aligned with Vestas sustainability
- Ensure the strategy deployment & improvement plans at operational level
- Direct and coordinate operations within Supply Chain Management guidelines
- Work with department heads to insure coordination of purchasing, storage, and shipping in timely and most cost efficient manner. Execute ramp-up, ramp-down
- Ensure operations are operating effectively, efficiently and lean
- Develop and manage quality improvement initiatives. Follow up with stakeholders as applicable
- Manage inventory reporting and physical count process for the operations (stock count etc)
- Maintain a focus on stable operations and operational consistency
- Manage, direct and provide leadership to all operational aspects of warehouse (e.g. 5 S, 5 WHYs, capital expense, quality, logistics, cost and time management etc.)
- Interact closely with all stakeholders when developing and executing inventory strategies. Especially Service and Construction Departments
- Ensure best practice sharing
- Report on all aspects of performance
- Develop annual warehousing budgets to meet Vestas forecasted growth. Budget control/cost down for warehouse operations and logistics
- Bachelors degree in Business, Engineering, Logistics, Supply Chain Management, Operations Management or similar discipline. Preferred but not essential
- Trade qualification or Diploma in Engineering Mech/Elec
- 7 or more years warehousing or distribution management experience
- 10 or more years supervisory / management experience
- 10 or more years in a manufacturing, distribution, engineering or service organization
- Six Sigma green belt certification (or higher) would be highly regarded but is not essential
- Plans and leads preparation for new merchandise on the sales floor, truck unload, freight flow, display assembly, ticketing, and stocking tasks for the freight team
- Provides clear work direction, training, and coaching to freight team members regarding freight flow process and furniture assembly
- Serves in the Manager on Duty role as needed including opening and closing the store. When serving in this role, provides leadership and direction to floor associates and ensures that store, merchandising, and customer service standards are continuously met, including merchandise presentation, signage, recovery, and cleanliness. Drives the customer experience and ensures resolution of customer issues
- Availability to work a variable schedule of at least 30 hours per week, including nights, weekends, and holidays required
- Ensure an attitude of safety consciousness throughout the warehouse
- Enforce all Safety rules through safety observations
- Provides direct daily supervision to ensure a safe clean and efficient operation of the warehouse
- Assists in training and motivating of personnel for increased effectiveness
- Coordinates loading and unloading operations of both inbound and outbound shipments
- Ensures product is stored and stacked in the most efficient manner
- Makes recommendations to the Director on initiatives to improve warehouse operations
- Provides leadership in regards to problem solving
- Directs work force to achieve maximum efficiency
- Applies sound communication and motivational techniques in supervising, counseling and disciplining subordinates
- Leads by setting the good example
- Ensures the efficient and safe operation of all materials handling equipment
- Reports for monthly meetings will require, Power Point, Excel, and Microsoft word
- Ensures damage to product, equipment and the facility are prevented
- Ensures compliance to OSHA standards GMP regulations, Food Safety, C-TPAT and standard operating procedures
- Ensures accuracy on all inbound / outbound shipments
- Assists Director in evaluating space utilization and suggest methods of improvement
- Coordinates the relocation and consolidation of product as required
- Ensures all personnel are trained properly in their respective area, and cross-trained in other related positions within department
Distribution & Warehouse Manager Resume Examples & Samples
- Responsible for development and management of the Logistics
- Local Contract manager for all 3rd party logistics services
- Bachelors Degree in Logistics (preferred) or Management
- 3 - 5 years experience in manufacturing or warehouse
- SAP knowledge and experience
- Team/Plant Management experience
- Maintains receiving, warehousing, and distribution operations by initiating, coordinating, and enforcing program, operational, and personnel policies and procedures
- Complies with local warehousing, material handling, and shipping requirements by studying existing and new legislation; enforcing adherence to requirements; advising management on needed actions
- Monitors volume of business and determines appropriate work schedule
- Sets productivity and establishes necessary controls to ensure objectives are met
- Monitors condition and maintenance of operating / material handling equipment
- Constantly monitors the efficient handling of shipments and receipts to create an error free culture
- Reviews the loading and unloading schedules to maximize efficiencies and reduce expenses
- Coordinate floor cycle counts, physical inventory and reconciling records
Specialized Distribution Warehouse Manager Resume Examples & Samples
- Responsible for implementing the highest standard of Quality & Compliance across all operational processes, and enforcing Regulatory and Good Manufacturing Practices (GMP) as required by Health Canada and as required by acting on behalf of the manufacturers
- Responsible for the enforcement of Security, laws, regulations, policies and programs. Ensures that the facility and transportation security standards are followed
- The ultimate goal in applying these high degrees of standards, policies and programs is to take a market leadership position in safeguarding the health of the patients as well as ensuring the proper storage and distribution of medicine, medical devices and active pharmaceutical products in a safe and secure environment for our employees
- Accountable for achieving the highest standard in Health Canada Regulatory and GMP audits, Manufacturers audits, and Security audits and ensuring proper review, update, and action on policies and programs to ensure compliance. Take appropriate and timely actions to close any gaps
- Ensures that all vehicles, equipment, buildings and property are maintained in accordance with Company standards
- Responsible for ensuring proper use and follow ups on the facility IT systems (operational and quality systems) and maintaining accurate data entry and product traceability (inventory, etc.) at all times
- Responsible for preparing budget for the facility
- Accountable for achieving results related to quality, productivity, and financial
- Develop a health, safety and environment program. Ensure that health and safety practices are followed within the workplace through on-going monitoring of health and safety programs and audits; provision of all equipment, material and protective devices
- Responsible for preparing and submitting the expense and capital expenditure budgets for the facility. Operates within approved budget parameters
- Actively analyze on-going expenses within the facility to ensure that budgets are met and take corrective action where variances occur
- Analyzes operating and delivery procedures, systems and schedules and all other facility activities to identify potential efficiency improvements and cost-savings. Recommends changes to the General Manager. Implements approved changes
- Supports and coordinates implementation of corporate programs in sales, marketing, finance, human resources and information services
- Ensures that responsibilities are defined and assigned to supervisors and employees so as to maximize efficiency and productivity
- Ensures policies and practices are respected related to employee relations and promotes efforts to build strong employee engagement
- Maintains appropriate communications with all levels of the organization and ensures that facility employees are aware of company's progress and direction
- Monitors, maintains and identifies opportunities to improve customer service levels for all manufacturers/customers
- Conducts information session for employees to communicate the Company’s progress and direction to facility employees
- Plans the activities of his/her staff; assesses results and takes appropriate measures to improve performance
- Maintain communication between all departments; Regulatory & Compliance, Specialty Pharmacy, Finance, IT, Transportation, Customer Service, etc
- Supports and executes performance reviews for facility Leadership team, initiating development plans and actively coaching areas of opportunity
- Participate in Customer meetings, from time-to-time, as the Operational expert
- Participate in Business Development strategies and opportunities by proposing recommendations on value-added services to manufacturers/customers
- Perform miscellaneous duties as assigned by the General Manager, Specialized Distributions
- Always keep work area safe, organized and clean
- Follow company Health and Safety policies
- Experience in the pharmaceutical industry is required
- Possess at least 7 to 10 years of leadership experience within a distribution facility environment (experience in a 3PL model would be an asset)
- An undergraduate degree in business or supply chain management is preferred; an equivalent combination of post-secondary education and directly related experience may be considered
- Proven history of leading diverse teams towards achieving objectives through collaborative and participatory management practices. Strong ability to manage through delegation, engagement, and proper follow-up
- Ability to analyze business metrics and deliver strategies to effectively set targets and standards of performance which meet or exceed quality and profitability objectives
- Effectively develop distribution facility supervisory teams through coaching and mentoring
- Experience in managing the business within budget parameters
- Experience in a Continuous Improvement environment would be considered an asset (i.e.: Six Sigma, Lean, etc.)
- Strong communication and analytical skills (Proficient working knowledge of Microsoft Office Suite)
- Strong organizational and tactical planning skills
- Ability to take initiative, strong work ethic, behaves with a sense of urgency
- Strong problem solving & decision making capabilities
- Ability to adapt quickly to new situations, as well as new and changing processes, programs and services
- Effectively communicate both verbally and in writing
- High degree of driving Customer satisfaction & engagement, and be recognized as Customer solutions oriented
- Competency to analyze qualitative and quantitative data in order to make sound management decisions
- Ability and willingness to solve complex problems and conflict situations in a timely, respectful, and fair manner
- Highly developed time management skills with the ability to prioritize and delegate duties as needed
- Driven to results and motivating others towards achieving them
- Committed to motivating others to achieve team success
- Strong advocate and role model for local engagement initiatives
- Openness to new concepts, ideas and creative solutions
- Assess existing staff needs and work with managers to identify opportunities
- Meet regularly with team members collectively, as well as on an individual basis to monitor progress toward meeting objectives, track performance, coach and counsel if necessary; as well as recognizing team and individual successes
- Delegate tasks with discretion while maintaining personal responsibility and accountability for follow through on such tasks
- Management skills – coaching and development of supervisors
- Demonstrated employee engagement skills
- Strong communication skills – open, honest verbal and written communications
- Must be open to flexible night hours, Sunday through Thursday with a typical start time of 6PM
- WMS experience
- Responsible for maintaining a safe workplace and ensuring that safety is the highest priority in the workplace
- Comply with all Environmental Health & Safety and Quality Assurance requirements and goals. Provide information and materials to these divisions as necessary to ensure adequate and legal documentation
- The Warehouse Manager provides daily work assignments and supervises Logistics Warehouse persons
- Shipping and receiving functions
- Picking and replenishment of line-side containers by material handlers
- Development and performance of warehouse personnel and activities as they relate to the movement of all material throughout the compound
- Inventory and cycle counts
- Coordination and processing of all Return to Vendor damaged merchandise
- The tracking and movement of material shortages/overages to their designated areas
- Receiving and inventoried area is maintained in a safe, clean and orderly fashion
- Performs scheduled and unscheduled inspections
- Maintains an on-site inventory of supplies and materials to ensure timely response and completion of routine or emergency site repairs
- Makes recommendations for additional inventory to meet the requirements of the Statement of Work (SOW)
- Ensures all supplies and services are procured on behalf of the U.S. government (USG) and ensures they are used for no other purposes
- Ensures that common supplies, materials, equipment and services are procured from local and regional supply markets to the maximum extent practicable
- Ensures proper material controls are in place and operations are in compliance with established standard operating procedures (SOP), SOW and Occupational, Health and Safety Administration (OSHA) standards
- Assists in developing the SOW when required
- Reports any malfunctions, or lack of compliance with the SOW to the Program Logistics Manager
- Maintains effective, timely and respectful communication and interaction with other employees, managers and supports other organizations
- Implements section priorities with logistics, procurement, and warehouse team
- Collects, analyzes and summarizes data for report preparation and submits written reports
- Performs other administrative tasks including material ordering, inventory and work scheduling
- Responsible for facility custodianship of work areas and management of vehicles, material handling equipment, tools and spare parts
- Must be able to take initiative to analyze a situation and make frequent technical decisions based on SOPs and safety codes
- Must be able to evaluate operational effectiveness and develop/maintain effective operation control mechanisms
- Must be able to work effectively with minimal supervision with a strong focus on procedural compliance and customer service
- Performs other duties and special projects as assigned
- Three to five years of progressive experience, including small staff management, in a high volume, multi-unit receiving/inventory or supply management environment
- Relevant overseas logistics experience
- Knowledge of FAR
- Knowledge of Cost Point and Maximo are a plus
- Experience with space management and maintaining accountability of government assets
- A strong commitment to maintaining a high performing team which delivers high customer satisfaction
- Ability to add, subtract, multiply, and divide in all units of measure, using whole numbers, common fractions and decimals
- Understanding how inventory affects company contractual obligations
- Knowledge of ALL principles and processes involved in operating and supporting supply chain functions at a large-scale overseas facility
- Knowledge of principles and processes for providing excellent customer services
- Expert computer skills, specifically in Microsoft Word, PowerPoint and Excel
- Ability to become an active and functioning member of a team
- Obtain Certification for International Air Transport Association (IATA) and U.S. Department of Transportation (DOT) regulations every 24 months
- Manage three direct reports and off-site warehouse inventory and activities
- Select couriers and freight forwarders to ensure Supplies, components and chemical shipments arrive in a manner to meet manufacturing start-up lines
- Fully knowledgeable in and able to create and maintain SOP's for all phases of department operation to ensure full compliance with Transportation, ICAO/IATA Technical Instructions, FDA, Import and Export Regulations
- Proficient in Microsoft Dynamics AX , Excel, Word, PowerPoint and Outlook
- Control product inventory and distribution supporting over millions of dollars.This position has full responsibility and authority to make necessary decision and/or take action
- Possess extensive knowledge of 49 CFR and ICAO/IATA regulations as they pertain to the transportation of hazardous materials
- Knowledge of the FDA, cGMP's, Import and Export requirements to meet governmental regulations for international shipping of chemicals, biological products, and investigational clinical supplies
- Six plus years of experience in managing warehouse operations and staff, along with four years of packaging and shipping of hazardous chemicals and/or biotech products, preferably in a pharmaceutical environment
- Have the ability to read and define Material Safety Data Sheets to identify chemical hazards
- Bachelors Degree in basic sciences or business administration preferred
- Knowledge of Microsoft Dynamics AX for Inventory and Warehouse Management modules as well as Microsoft Excel, Word and PowerPoint
- Ability to train staff to a high degree for compliance to all government regulations of hazardous material transportation
- Demonstrate strong auditing skills for inventory accuracy
- Detail oriented for maintaining data to support internal and external audits
- Possess ability to identify and communicate with AvidBioservices employees and 3rd party carriers to ensure shipment integrity is maintained
- Ensure materials are received from proper vendors, delivered to inventory and finished goods, and packaged according to specification
- Maintain material availability to meet production schedules and/or ensure products are shipped per customer requirements
- Generate warehouse productivity reports
- Oversee maintenance of warehouse equipment, providing both preventive maintenance programs and all necessary repairs
- Recommend equipment requirements and replacements to upgrade and maintain warehouse productivity and efficiency
- Oversee and lead the implementation of the RMP (Risk Management Process) system and operational standards as outlined in the factory accountability list in order to achieve targeted RCR
- The incumbent is responsible for managing and evaluating the performance of personnel in the Warehouse Department
- Plan, organize, and manage department functions effectively
- Manage inventory (timely, compliance with Company policies, timely reporting, Fifo rotation)
- Assure accurate and timely computer system data entry (SAP)
- Assure accurate shipping, receiving, and production records
- Assist with hold and recall procedures to assure customer safety in conjunction with Quality
- Direct activities to assure that storage requirements for ingredients and finished goods are met
- Assure department personnel safety, training, motivation and effectiveness
- Develop, implement and monitor department goals
- Develop and manage department budget
- Assume all safety, system, and lift truck certification and training
- Maintain proper housekeeping and sanitation
- Coordinates and expedites flow of materials for planned production
- Plan, organize and implement effective communications for/with
- Manages capital and process improvement projects for department
- Department employees
- Other department/employees in facility
- Outside carriers and storage locations
- Factory and corporate management
- External vendors
- Provide leadership for facility by active involvement on Factory Staff and other teams/committees as required. Provide input into the long-range planning of the facility
- Make effective decisions impacting department, factory budgets, and personnel. Incumbent also may be required to make decisions impacting Company business and outside agencies or companies, such as USDA, purchasing contracts, product hold/recall, etc
- Administer department and Company policies and procedures as part of the factory management staff
- Financial Controls and Budgeting: Responsible for providing leadership and guidance during budget building with constant emphasis on practical business and financial responsibility
- Interprets company policies to workers and enforces policies and safety regulations
- Human resource responsibilities will include departmental interviewing/evaluating/hiring prospective employees, goal setting, performance evaluation, employee relations, consistent administration of policies and procedures, training, recognition, EEO/AAP, Labor Relations commitment/opportunities and compliance with internal and external requirements
- Training and Safety – Provide a safe and healthful work environment for all personnel through consistent support of the company’s Kraft Heinz Safety Process. Oversee safety processes including, but not limited to, goal setting, hazard recognition, and elimination, administration of safety procedures and corresponding corrective action, area inspection, job skills, and compliance training, accident investigation and safety meetings
Global Transportation & Warehouse Manager Resume Examples & Samples
- Deliver on stated objectives including transportation cost control, modal selection and strategy development, audit finding remediation, address security and compliance matters, manage carrier relationships with Procurement, lead transportation performance improvement projects, transportation systems integration and support, maintenance of guidelines and directives related to transportation, performance benchmarking and reporting, and continuous optimization of transportation and warehouse operations
- Coordinate the efficient movement of temperature controlled freight to meet internal / external requirements through carrier management, transport route, and Standard Operating Procedure development. Responsible for managing Transport Standard Operating Procedure's in accordance with EU & US GDP and internal Global Standard Operating Procedure's
- Influence and manage clear Primary and Secondary transportation goals for the Pharma group. This will require knowledge of Bayer logistics procedures, transportation requirements, and global commerce regulations
- Recommend corrective actions for problems encountered in shipping, billing and inventory management
- Develop and acts as a Center of Expertise for all transportation related topics including modal selection, route optimization, carrier load capacity utilization, temperature control and cold chain, shipping technology (i.e., track and trace, temperature monitoring), software tools (i.e. route optimization, freight payment, delivery confirmation, load tendering) and establishes BHC best practices and operating standards
- Autonomously manage inbound and outbound freight and monitor/improve carriers
- Design and optimize Warehouse and Transport network
- This position will manage inbound and outbound freight and carrier performance as well as be responsible for global air and ocean bids for all products under Pharma Division
- Align as well as steer global/divisional/local projects and initiatives with corporate platform and sites
- B.A. or B.S. in Logistics and/or Supply Chain
- 10 + years of leadership experience demonstrating broad and global exposure to GDP, cool chain, dangerous goods & trade compliance. or an equivalent combination of education and experience; 5-7 years Transportation & trade compliance
- Experience with global warehouse and transport of time and temperature sensitive movements and optimization
- Understanding of US Department of Commerce/Bureau of Industry export regulations, OFAC/Treasury embargoes/license requirements
- Export Control Classification Number/HCCN commodity classifications, dangerous goods, export compliance
- Broad experience in working with freight forwarders, air/inland carriers, warehouse personnel and internal departments including QA, Regulatory, Technical Operations, etc
- Knowledge of international shipping required and experience with cold chain procedures (time/temp controlled shipments) a must
- High level of creativity in proposing solutions for dealing with unique circumstances
- Must be flexible and be able to deal with changing priorities without losing sight of the overall business
- Strong interpersonal and communication skills working within an environment of constant change
- Experience with TMS/S&D modules SAP
- Multi lingual (German/English)
- Promote company culture and ensure discipline to all company policies and procedures
- Supervises employees in the performance of their job, coordinates training to ensure employees know all aspects of their jobs, supports and provides direction through effective goals/objectives setting
- Facilitates a robust department structure by assisting in effective staffing levels and creating succession plans and related employee development plans to support current and future needs
- Aids in developing and executing an annual strategic plan for the department supporting company performance objectives and industry/ field related benchmarking and trends
- Collects, collects and monitors data related to the overall effectiveness of the department
- Reinforces new processes and procedures as required to support changing business demands
- Facilitates effective communication through department meetings and an open door philosophy
- Facilitates and promotes a work environment based on fairness and consistency , in accordance with the principles of the Magna Employee Charter
- Aids in department budget preparation, approval and attainment
- Facilitates all warehouse operations to effectively maintain inventory accuracy at all times ensuring minimal product on the production floor at all times
- Ensures all warehouse operation/transactions are reflected in CMS
- Ensures robust scheduling system is in place and utilized
- Ensures material planning personnel utilizes MRP system product release and delivery
- Ensures confidentiality of all proprietary and human resources related information
- Overtime and travel may be required
- Involvement in the incident/accident investigation program, determine root causes, corrective actions and following up to ensure completion
- Identifies unsafe conditions and actions , ensuring all health and safety policies are followed
- Establish and enforce Customer Service policies to ensure 100% Customer Delivery is met
- Ensure that 5S standards are enforced
- High School Diploma/GED c
- Completion of community college diploma and/or certificate
- 3 to 5 years of work related experience
- Minimum 3 years supervisory Experience required
- Delivery/performance to plan on all assigned tasks
- Employee Development
- EOS Metrics
- Flawless Program Launches
- Health and Safety Measurable
- Manpower Allocation
- Meet all Department goals and objectives
- Obsolescence
- QOS Measurable
- Quality and accuracy of administrative support
- Records/File Maintenance 100%
- Coaches / Mentor
- Effective Delegation Skills
- Focuses on Continuous Improvement
- Results Orientated
- Must have a strong knowledge of receiving, warehouse, issuing and material handling operations, methods, and practices
- Strong knowledge in MRP/ERP system
- Proficiency in Microsoft Word, Power point, outlook and Excel is required
- Cultural awareness
- Ability to communicate with people from all functions within internal and external supplier
- Ability to motivating and coaching team to work effectively and efficiently
- Ability to adapt to changing environment
- Minimum High School,or related field
- Minimum 5 years experience in Warehousing, Receiving, Inventory Control, or Materials Management in a manufacturing environment with 3 years Supervisory experience
- Ability to communicate clearly in English , any further language is an advantage
- Effective written communication skills
- Ability to handle pressure and assess and allocate priorities
- “Can do”, hands-on approach to work
Warehouse Manager, Midshift Resume Examples & Samples
- Ensure the safety and security of all human capital and material goods
- Evaluate current procedures and practices for accomplishing department objectives
- Focus on process improvements for all warehouse functions
- Ensure high quality employee attraction, engagement and development at all levels
- Organize interdepartmental activities ensuring completion of the project on schedule and within budget constraints
- Must be open to flexible midshift shift hours, Monday through Friday, with typical start time of 2PM; must be open to overtime and covering other shifts as needed
- Experience managing budgets and expenses
- Project Management
- Open to relocation for promotional opportunities within 2-3 years
- Ensure compliance with health, safety, and environmental regulations
- Ensure compliance with inventory cycle count and control processes
- Achieves financial objectives by preparing an annual budget, scheduling expenditures, analyzing variances, and initiating corrective actions
- Maintains warehouse staff job results by coaching, counseling, and disciplining employees
- Conduct root cause analysis and implement corrective actions
- Ensure good condition of facility/equipment through regular audit and implementation of preventative maintenance protocols
- Manage third party contracts for services to warehouse
- Respond timely and professionally to customer complaints and inquiries
- Conduct analysis of warehouse activity to identify optimizations to pick, pack, shipment, and putaway processes
- Conduct capacity planning and ensure labor and equipment resources balanced with demand
- Ensures warehouse staffing needs through recruiting, selecting, orienting, and training employees
- Monitor warehouse workflow indicators and respond to exceptions
- Collaborate across departments to ensure efficient workflow and positive working relationships among teams
- Bachelor’s Degree in Business, Industrial Engineering, or related discipline
- 5-10 years of leadership experience in a high volume pick/pack operation
- Less than 5% travel
- Superior decision making and problem solving skills
- Ability to work well under pressure and meet deadlines
- Experience with warehouse management systems
- Experience in building a team in a high turnover environment
- Proficiency in MS Office applications including Word, Power Point, and Excel
- Ability to work a flexible schedule supporting both first and second shift operations
- Experience with selecting, procuring, operating, and maintaining a variety of warehouse material handling equipment
- Experience with SAP WM module
- Experience with leading a warehouse infrastructure and IT systems transformation
- Experience with Microsoft Access and Power BI applications
- Experience with warehouse scanning equipment and applications
Perishable Warehouse Manager Resume Examples & Samples
- Supervises and directs warehouse activities for up to 200+ employees to ensure that both incoming and outgoing product are handled properly using proper training, accuracy systems and programs. Controls production standards as well as, other measurable such as meeting projections for labor expenses. Assists in the preparation and administration of department budget
- Leads, mentors, coaches and directs warehouse supervisors, union and non-union employees. Train and develop supervisors, identifying and mentoring high potential candidates
- Implements and monitors Company “best practices” in managing inventory using warehouse management systems ensuring accuracy
- Establishes and monitors warehouse to ensure compliance with safety and sanitation standards regarding government regulations and Company policies. Enforces safety standards to reduce accidents and related expenses resulting from unsafe work practices. Attends monthly safety committee meeting
- Develops and maintains good working relationship with retail division and store personnel. Works with customers, in person when necessary, to resolve complaints
- Administer the collective bargaining agreement and effective resolve union grievances and issues
- Develop successful partnerships with other distribution departments
- Ensure that warehouse staffing levels are appropriate for maximum productivity
- 5S Compliance, Sarbanes-Oxley compliance
- Participate in special events as requested, i.e. hiring, employee morale functions
- Seven year previous experience and/or formal training and/or 4 year college degree in logistics with extensive experience in warehouse operations, preferably with the Company or in the grocery industry
- Possess thorough knowledge of material handling equipment, traffic management to include truck and rail deliveries and transportation
- Working knowledge of OSHA, USDA, HAACP, FDA, DEA, safety, sanitation and food safety regulations for warehouse operations
- Ability to analyze, forecast and measure day-to-day operations
- Basic computer skills required and personal computer experience with working knowledge of MS Word, Excel
- Working knowledge of engineered labor standards and Warehouse Management Systems
- BS degree in logistics, supply chain management or business administration Proven work experience as a warehouse manager
- Proven ability to implement process improvement initiatives
- Leadership skills and ability manage staff
- Managing and coordinating the WHS receiving, storage, distribution & administration processes of all goods within the facility
- Ensuring quality, delivery budget and environmental objectives
- Coordinating and monitoring the performance and progress of staff
- Planning current and future capacity requirements
- Initiate (process) improvements and drive implementation at our processes
- Create reports and statistics for internal- and external customers
- Overseeing maintenance of the facility
- Overseeing Safety & Security developments
- Ensures the efficient management of labor hours and consumable supplies within budget and work schedules including extra work days and shifts as needed
- Ensures the use and updating of receiving, selection and loading software systems
- Demonstrate knowledge of Spreadsheet software and Word Processing software, and ability to learn Sysco technology software and programs. Must have excellent computer skills
- Ability to manage the pressures and stress associated with a deadline-oriented atmosphere and customer service issues. Demonstrates skill in making independent decision in support of company policies and procedures in a timely manner
- While performing the duties of this job, the associate is regularly required to talk or hear. The associate is frequently required to stand; walk; sit; use hands to finger, handle, or feel; reach with hands and arms and climb or balance. The associate is occasionally required to stoop, kneel, crouch, or crawl. The associate must occasionally lift and/or move up to 100 pounds. Specific vision abilities required by this job include close vision, distance vision, color vision, peripheral vision, depth perception and ability to adjust focus
- While performing the duties of this job, the associate is regularly exposed to wet, hot, extreme cold and/or humid conditions; and moving mechanical parts. The associate works non-traditional business hours including evenings, nights, weekends, holidays and on call. The associate may occasionally be required to travel to other Operating Companies or the corporate office as business needs dictate (i.e. training, business continuation, etc.). The associate is occasionally exposed to high, precarious places. The associate is occasionally exposed to fumes or airborne particles. The noise level in the work environment is usually moderate
Warehouse Manager / Materials Manager Resume Examples & Samples
- Manage warehousing operations and coordinate plant demand, production and materials flow
- Manage Inventory/ Cost Control for raw materials, packaging and finished goods
- Accountable for leading a small team to increase their skills, performance, and results in order to meet the needs of downstream customers
- Provide leadership and strategic focus for the accomplishment of business goals, including guidelines for inventory coverage ranges, frequency of product runs, production run quantities, timing of promotional support, etc
- Manages key plant interfaces with corporate (R&D, Customer Service, Transportation, and Marketing)
- Monitors purchasing function for raw materials, packaging, work in process and co-packer production to support the most current production plans while adhering to lead times and inventory investment guidelines and minimizing any obsolescence exposure
- Reviews and coordinates plant capacity, master production schedules, weekly schedules, and stock status reports for raw materials, packaging materials and finished goods
- Bachelor’s Degree (strongly preferred)
- Experience with purchasing / vendor management
- Familiar with SAP
- Working knowledge of Microsoft Office (Word, Excel, Outlook, PowerPoint)
- Experience with MRP use and applications/understanding of complex planning concepts, forecasting and scheduling
- Practical knowledge of inventory/warehouse management systems
- Manage supervisors of warehouse employees. This includes hiring and training employees; planning, assigning, and directing work, appraising performance, rewarding and disciplining employees, addressing complaints and resolving problems
- Focus on the productivity, process and quality of warehouse operations
- Reduce controllable expenses
- Improve cost productivity, outbound shipment quality, and process improvement
- Assist and maintain appropriate inventory levels and product loss control
- Conduct physical counts of inventory and reconcile floor counts and inventory shipments
- Lead and assist in daily operations, which could include but are not limited to developing training plans, performance feedback, project implementation, continuous process improvement, customer and supplier quality, and communication with internal business leadership and employees
- 5 years experience in warehouse/distribution center operations
- Continuously improve productivity and waste to meet financial objectives
- Meets financial objectives by forecasting expenses each period, preparing annual budget, analyzing variances, and taking corrective actions to stay on plan
- Schedules the receiving and delivery of raw materials/finished products in a timely manner
- Utilize docks, warehouse layout and bulk truck loading patterns to minimize loading time
- Supervise approx. 60 warehouse non-union & union employees
- Track and report accurate inventory to aid in production scheduling
- Manage warehouse resources, shipping supplies and other consumables
- A minimum of 4 years of Warehouse and/or Logistics experience
- Demonstrated people management and leadership skills
- DSD delivery experience preferred
- Ability to manage a department budget
- Familiar with NIS or similar inventory Management system
- Familiar with Voice Pick and Warehouse Vision
- Familiar with Krono's, SAP, or employees timekeeping systems
- Familiar with product sequencing software for DSD
- Participate in hiring, supervising, training, and development of the warehouse staff
- Coordinate the scheduling of warehouse personnel to ensure proper coverage in order to receive and distribute products/materials in a productive and cost-efficient manner
- Coordinates all inbound and outbound orders
- Responsible for the general condition of the warehouse(s), shipping/receiving areas, and yard areas in regard to container storage and overall cleanliness. Inspects for any improper warehousing of inventory & insures the warehouse is neat and clean at all times
- Manage warehouse supplies at proper inventory levels and insure all warehouse costs are meeting plan. Work within working capital guidelines to meet goals and objectives
- Provide effective communication between service center office staff and the warehouse personnel
- Provides the highest level of customer service
- Develops/maintains various warehouse productivity reports
- Develop a production plan by line by plant to meet forecasted and actual customer demand requirements
- Interact with customer service and plant schedulers to resolve issues and build consensus on customer/market supply strategy
- Balance capacity with demand on a short term and long term basis
- Manage inventory investment throughout the chain to minimize working capital investment
- Analyze data to create information on safety stock levels, ERQ’s and forecasting requirements
- Single point of contact for CAM, SEM, and PS inventory and schedule related inquires by Customer Service, Sales, Product Management, etc
- Work with transportation and business teams to identify and implement optimization opportunities within the supply chain focused on reducing costs and increasing service levels
- Monitor phone calls, voice mail, e-mails and other communication, providing professional communication in a timely manner
- Monitor all warehouse activity for proper output, productivity, and safety processes
- Manage all ISO procedures, documentation, and control of records, correct forms and training
- Provides employees with guidance, training, and communication regarding job requirements, all OSHA safety guidelines, ISO procedures, & PolyOne rules/expectations
- Performs performance appraisals and provides timely feedback regarding performance reviews to the employee
- Bachelor’s Degree in Business, Operations Planning, Logistics or related degree preferred
- Technical knowledge of Supply Chain, Purchasing, Materials, Manufacturing, and/or related functions
- Strong computer and analytical skills combined with the ability to manage large amounts of quantitative data
- Proficient in the use Microsoft Office software and have working knowledge of ERP/SAP applications, specifically the Materials Management and MRP modules
- Ability to actively listen to customer and plant issues, efficiently troubleshoot problems and implement solutions in a timely and customer focused manner
- Demonstrated analytical, verbal, and written communication skills
- Current knowledge of warehousing, material handling, and inventory control practices
- Must have manual dexterity sufficient to operate a wide variety of small hand tools, scales, hand trucks, fork lift, and mixer/blender machinery and computer equipment
- 5-7 years of warehouse experience
- 3 years of prior supervisory/lead experience of warehouse operations
- Related purchasing, planning, scheduling and/or negotiation experience preferred but not required
- Must maintain Company approved Fork Lift Operator's Licenses. This may include one or more different types of forklifts
- APICS certification preferred
- Produce a situational analysis report with recommendations and implementation plan
- Review SOPs, operations, and the level of implementation and adherence to policies and procedures. Offer recommendations
- Conduct a review of all installed components of SAGE and produce recommendations
- Improve performance within the warehouse
- Ensure that warehousing SOPs are being adhered to at all times
- To Manage the day-to-day operations of the warehouse
- Conduct baseline stock inventory of warehouse
- Ensuring the proper receipt and storage of all received commodities
- Ensuring the prompt entry of all orders
- Ensuring the correct picking, packing and distribution of orders
- Identifying and segregating expired product for? disposal
- Identifying current and potential product shortages
- Identifying and implementing process changes as required to ensure more efficient operations of the warehouse
- Making changes to the layout and organization of? the warehouse to facilitate efficient operations, as required with the assistance of a short term assistance of a logistician and local staff assigned to this function
- Promptly informing the management of any issues which have? an adverse impact on warehouse operations
- Regularly review progress made in the process for product recognition within the supply chain system, with emphasis on identification of a specific item and its owner in the warehouse.? This includes the product ID and other partner coding systems and the need to frequently change product pack and carton sizes
- Train Warehouse Management according to established schedule. Review and evaluate uptake of training provide
- To develop a training curriculum, training materials and conduct training for the following staff on the required SOPs
- Senior technical team
- Warehouse team leaders
- Warehouse staff
- Logisticians
- Review and evaluate uptake of training provided
- Provide refresher training to warehouse staff and provide basic training to other technical staff at central and regional levels
- Review access rights for all staff and recommend / update according to new management hierarchy and stock security procedures in place
- Review all available reports and update per stakeholders requirements, mainly stock movement, stock locations, stock value, etc
- Reconciling stock data in SAGE with the current physical contents of the warehouse
- To develop a training curriculum, training materials and conduct training for the following staff on the required SAGE functions
- Identify and train at least two super users on the use of SAGE day-to-day functions (including report development)
- Review “receiving” SOP to include systematic weight and volume data on all products to assist in linking order deliveries and distribution
- To create and implement the following teams to improve the warehouse operations
- Good receipt teams
- Stock control and picking teams
- Dispatch checkers
- Goods receiving
- Put-away goods
- Internal movements
- Cold chain management
- Order entry – standard process and manual process
- Print all missing rack labels to reflect current layout
- Evaluate and implement pick face requirements for all products
- Routine empty slot verification
- Move slow moving items to far end of racking
- Move fast moving items closer to packing and checking areas
- Any other improvement that is identified
- In collaboration with management stakeholders and partners identify reporting requirements and develop additional automated reports as required
- Ensure proper implementation of all relevant SAGE functions
- Develop procedures for proper maintenance and backup of the SAGE system and database
- Train potential IT staff to conduct routine maintenance and backup procedures
- Any other tasks identified in the course of the TA visit
- Diploma in warehouse management // Bachelor’s degree in business with concentration in warehouse management preferred
- At least five years of experience in warehouse management, of which at least three years must have been spent in a senior management position preferably in a pharmaceutical or public health supplies management environment. Experience working in warehouse management of perishable products a plus
- Education - 15pts
- Experience - 40pts
- Knowledge of software & computer skills -30pts
- Laguanges (French and/or English ) (Portuguese a plus) - 15pts
- Bachelor's degree preferred
- Must have a valid driver's license and be able to obtain DOT certification to operate DOT regulated vehicles
- Industry background to include vending, food service, route distribution (e.g. uniform distribution or customer products), retail
- Must be able to work various shifts - 24/7/365 operations
- Support the General Manager in the guidance and control of all warehouse, purchasing and inventory functions
- Use Aramark technology and tools to minimize product costs and maintaining tight inventory controls
- Ensure proper products are on hand to support sales volume and product mix
- Ensure accurate physical inventories
- Hire, train, coach, develop, schedule and discipline members of the Warehouse and Concessions teams
- Participate in hands-on execution of events from a Warehouse and Concessions perspective
- Must be willing to travel during the off season to support other Aramark accounts
- Insure import and export compliance on corporate initiatives and ensure customs inventory accuracy
- Analyses and implements changes and/or programs to ensure the accuracy of raw material/finished goods inventory and manage safety and lean initiatives in the warehouse
- Lead the warehouse team in attaining key metrics: On Time Delivery, cycle count accuracy, physical/customs inventory accuracy, sales target, operation excellence and Days on Hand
- Plan, coordinate, and implement programs to achieve strategic and profit plan objectives with Material and logistics department, which are consistent with plant objectives
- Provide leadership support to high performance work teams while maintaining a positive employee relations climate
- Fosters an environment that promotes Eaton’s goals, philosophies, and encourages continuous improvement
- Provide coaching, mentoring, and training for subordinate employees to achieve performance goals, increase employee engagement, and provide career development opportunities
- Bachelor’s degree with a minimum of 10-15 years of supply chain/warehouse experience
- Ability to establish systems & drive sense of urgency among team members
- Developing and empowering teams
- Bilingual: English/ Tagalog
- Knowledge of Lean principles a plus
- Experience in setting up warehouse will be an added advantage
- Ensure customer delivery: feed and monitor the sequencer, supervise preparation and loading of finished products into trucks, track shipments, communicate all shipment failures, implement customer Misdeliveries per Million (MPM) follow up and contribute to its reduction
- Ensure adequate production lines supplies: assure the cleanness and tidiness of stocking areas, ensure feeding of production lines (small train), supervise the unloading of pieces and measure suppliers MPM and manage a warning system in picking zone
- Conduct the implementation of logistics basics: booking operations, traceability, labelling, container management, etc
- Monitor visual management system: deploy visual First In First Out (FIFO) and install physical alert systems
- Organise equiptment and human resources
- Look for productivity gains
- Manage, train and coach logistics operators team
- Bachelor's degree in engineering
- Experience in production in an industrial environment
- Minimum bi-lingual (English required)
- Assures the accomplishment of warehouse functions by performing accurate shipping & receiving activities
- Implement initiatives to improve the chain and logistic materials movement
- Identifies opportunities and proposes & implements these through DBS & DMS
- Is an expert in Lean Conversion, Kanban, Kaizens, +QDIP boards, Standard work and other DBS & DMS tools
- Assures the availability of materials to support productions schedules and performance
- Assures the product and material movements in the safety matter through the buildings and suppliers
- Maintains an efficient inventory system to guarantee the material disposition
- Maintains staff by recruiting, selecting, orienting, and training employees; maintaining a safe and secure work environment; developing personal growth opportunities
- Accomplishes staff results by communicating job expectations; planning, monitoring, and appraising job results; coaching, counseling, and disciplining employees; initiating, coordinating, and enforcing systems, policies and procedures
- Completes operations by developing schedules; assigning and monitoring work; gathering resources; implementing productivity standards; resolving operations problems; maintaining reference manuals; implementing new procedures
- Responsible for the improvement and profitability of the company’s goals by; participating and ensuring end of month, end of quarter and end of year activities are completed, accurately and on a timely manner; supervising employees; evaluating actions and performance
- Controls expenses by gathering and submitting budget information; scheduling expenditures; monitoring variances; implementing corrective actions
- Maintains professional and technical knowledge, by and as applicable, attending educational workshops and training; reviewing publications; benchmarking state-of-the-art practices; participating in professional societies
- Ensures optimal housekeeping by following procedure and completing corresponding checklist
- Contributes to team effort by accomplishing related results; keeping business information confidential; administering the system security; ensuring data accuracy and integrity; maintaining updated professional and technical knowledge; assuring systems compliance with laws, regulations, and corporate standards; ensuring a safe and healthy environment
- Complies with QRS, ISO and all applicable regulations and company procedures
- Ensures that all personnel in his/her area is aware of the importance of Environmental Policy and EMS (Environmental Management System) requirements, their roles and responsibilities and the potential impacts of their work
- Identify opportunities and propose ideas for minimize or eliminate environmental aspects or impacts
- 5+ years of related work experience in the Manufacturing and Material Management functions at the Medical Devices or Pharmaceutical industries
- 2+years of Supervisory experience
- 2+years’ experience of Quality System, ISO regulations, CAPA system, GMP’s practices
- 2+years’ experience in general warehousing, shipping, traffic and inventory functions
- 2+ years’ experience in Negotiation, arbitration and conflict resolution skills
- 2+ years’ experience of import/export regulations and requirements
- To manage the day-to-day operations in the warehouse and waste handling areas on site
- To ensure adequate manning of the warehouse team including provision of ‘cover’ as required
- To ensure that all activities in the manufacturing warehouse and waste handling areas are carried out accordance with Standard Operating Procedures
- To ensure that all activities in the manufacturing warehouse and waste handling areas are carried in compliance with Environmental, Health and Safety policies and procedures
- To ensure that all activities in the manufacturing warehouse and waste handling areas are carried in compliance with Quality Assurance policies and procedures. Specifically
- To raise and close out CAPA actions and deviations in a timely manner
- To raise deviations and undertake investigations as necessary
- To undertake a monthly departmental meeting where open actions are reviewed and prioritised
- To manage the ERP system for thesite to ensure accuracy in shipments and inventory transactions and conduct stock checks on a frequent basis
- To work collaboratively with all site departments to ensure appropriate and effective support of the warehouse and hold regular discussions with the Edinburgh departments to forward plan material movements
- To ensure warehouse team members are adequately trained and that the training records are kept up to date in MasterControl. To develop a training plan and review this on a quarterly basis. Ensure all members of the team have objectives and are managed through the company performance management scheme
- To maintain logistics documentation and provide reports and statistics, e.g. on stock accuracy and number of orders on a frequent basis
- To promote good working relations within the logistics teams
- To carry out such as other tasks as may be reasonably required from time to time
- To lead the roll out of the SAP system within the logistics team and co-ordinate the interactions with the affiliated departments
- Identify areas of improvement and establish innovative or adjust existing work practices
- Act as a point of contact for the site in Customer and Regulatory Audits
- To develop a housekeeping plan for area of responsibility and ensure through regular reviews that the standards are maintained
- Good team working, communication and inter-personal skills
- Ability to lead and manage teams
- Good technical ability to analyse business and customer needs
- Ability to work to tight and moving deadlines
- A flexible and versatile approach to people and situations
- IT capabilities
- Reliable and trustworthy
- Experienced in the implementation of software systems
- Experience of Warehouse Management, including material management (raw materials), inventory control and despatch
- Experience of managing warehouse teams – including support of personal development plans and training requirements
- Detailed document management and development of record management systems
- Responsible for the management of logistics functions, including: (1)warehouse management (receiving, put-away, order picking, etc.), (2) inventory management, (3) transportation and material moving, (4) negotiation/ contracting with logistics service providers, (5) management of logistics service providers, (6) freight bill audits and payments, (7) claim administration, (8) space/ facilities management, etc
- Performs/ provides centralized logistics/ warehouse management functions/ services to an integrated multi-plant facility with four (4) production departments: (1) Precision Parts Manufacturing, (2) Card Reader Assembly, (3) ATM Assembly, and (4) Die Manufacturing
- Leads/ manages more than 140 logistics personnel consisting of 7 supervisors, 12 leadmen, 90 warehousemen, 20 material movers, 4 truck drivers, 5 inventory analysts, 2 facilities planning/ time study personnel
- Must have a Bachelor's Degree in any four year courses
- Should have at least 3 - 5 years of experience as Warehouse Manager or Assistant Manager in a manufacturing company
- Must possess the following skills
- Active listening
- Reading Comprehension
- Speaking in public
- Service Orientation
- Excellent negotiation skills
- With good judgment and decision making
- Time management
- Superb Writing skills
- Management and Personnel Resources
- Can work under pressure with minimum supervision
- Must be computer literate
- Keen eye for details
- Maintain a professional attitude and help solve problems when communicating with customers
- Manage day-to-day warehouse operations solving problems through the normal course of operations
- Monitor product from offsite storage
- Monitor safety and sanitation standards, working with supervisors to ensure sanitation and safety audits are completed daily
- Maintain good employee relations through one on one contact during the course of normal operations
- Work on 2nd and 3rd shifts to be exposed to operational needs and assist in training of supervisors
- Maintains a safe and healthy work environment by establishing, following, and enforcing standards and procedures and complying with legal regulations
- Maintain quality standards of finished product
- Ensures smooth delivery of product for the sales organization
- Achieves operational objectives by contributing warehouse operations information and recommendations to strategic plans
- Reviews and prepares any action plans while ensuring productivity, quality and customer service stands
- Meets financial objectives by forecasting requirements; preparing an annual budget; scheduling expenditures; analyzing variances and initiating corrective actions
- Develops team to solve day-to-day operational issues and reach short- and long-term performance goals
- Delivers effective change leadership while driving business changes and minimizing people impact
- Communicates cross-functionally to assist team to solve operational issues
- Motivates the team members to achieve plan goals
- Develops processes for receiving product, equipment utilization, inventory management, gate processes (check in/out) and shipping
- Bachelor's degree preferred or equivalent experience in consumer packaged goods or a related industry
- A minimum of 5 years of operations/logistics or supply chain experience
- Lean Six Sigma Experience preferred
- Experience with continuous improvement (i.e. Lean Six Sigma certification, TPM, lean manufacturing, etc)
- Proficient in Microsoft Suite applications
- Ability to give and receive constructive feedback
- Ability to lead a team-based approach to decision making
- Strong leadership with the ability to get results through mentoring others
- Willingness to work off shifts and weekends as needed
- Attract, retain, and develop effective Front Line Managers and Warehouse personnel to ensure an efficient, motivated, and skilled workforce
- Assign duties and tasks to employees as appropriate and establish performance criteria
- Review job performance and coach as necessary
- Train Warehouse personnel in proper safety procedures, forklift, driver's licensing and accident reviews
- Screen, interview, and hire new Warehouse employees
- Efficiently and accurately deliver bulk orders to fulfill commitment to our customers and support CCBCC sales objectives
- Ensure route trucks, bulk rigs, and transport assets are efficiently and accurately loaded/unloaded to support the efficient movement of goods and materials to their ultimate destinations
- Manage and control Warehouse Inventory to keep shrink and customer service levels within standards and support Sarbanes/Oxley control requirements
- Monitor product inventory levels and available sales/production/transportation data to ensure product is available when/where needed to support sales activity
- Ensure the maintenance and security of Warehouse and grounds to meet CCBCC and government sanitation guidelines and preserve and protect company materials and assets
- Bachelor’s Degree in business, engineering or technical discipline field highly preferred
- 3-5 years of management, production, manufacturing or other relevant experience is required
- Ability to work in a constant state of alertness and safe manner
- Responsible for organizing the warehouses and the work flow
- Coordinate transportation carriers and performance through the utilization of TMS and ensuring all scheduled shipping and receiving appointments are timely and in support of production and customer requirements
- Responsible for maintaining inventory based on FIFO and assist in preventing customer service issues
- Responsible for delivery of KPI’s for warehouse and cost control
- Bachelor's Degree required within fields of Accounting, Applied Economics, Finance, Business, Operations Management, or Supply Chain
- A minimum of 3-5 years’ experience in a manufacturing warehouse and distribution leadership role
- Candidates should have previous work experience within a food manufacturing and distribution environment
- Bilingual, a plus
- Train warehouse employees and ensure they are provided ongoing skills development and coaching, to improve job performance
- Schedule warehouse employees, and initiate short and long-term goals with supervisors
- Manage the forklift safety and training process for the site
- Maintain and improve the warehouse safety and accident prevention program with the site safety coordinator
- Oversee cycle counts of product inventories and ensure that all inventory is accurately accounted for, in accordance with company policies and procedures
- Identify gaps in effectiveness of work processes and worker performance, contributing to errors in inventory management and product losses (i.e. shrink), taking corrective action as needed
- Create purchase orders, and follow up with vendors and end-users throughout the procurement process
- Maintain strong relationships with growers and shippers to order the highest quality produce, at minimal costs
- Adhere to purchasing policies of Del Monte and price parameters given by the General Manager in purchases
- Work with Office Manager and accounting team to ensure accuracy and timeliness of the invoice corrections and credits from vendors
- Work closely with Quality Assurance department to ensure proper documentation is maintained on all on received produce
- Work closely with Sales departments to ensure customer and shipping related issues are communicated
- Work with Del Monte Commodity Managers, Transportation department and outside vendors to ensure product delivery in an effective timely matter
- Assist in all areas within the facility as needed
- 4 year College Degree in related field, from an accredited institution, and/or equivalent work experience in a similar position
- 6 years of warehouse experience, loading and unloading 48 and 53 ft. trailers, with knowledge of axel weight limits and load damage prevention
- Proficiency with supply chain strategies and distribution systems
- Knowledge of Microsoft Office Programs (i.e. Excel, Word and Outlook, etc.)
- Manage team of 50+ warehouse workers and their activities, including setting priorities and metrics, recruiting, hiring, terminating, reviewing performance and coaching employees
- Implement business strategies set forth by senior management and participate in improving the business by administering and evaluating short and long term objectives for warehouse as well as offering potential alternatives to existing methods
- Work with Inventory Management team to manage inventory and optimize order fill rate
- Implement and ensure compliance with Rexel's continuous improvement program to create a more efficient warehouse flow and ensure accurate receiving and order filling processes
- Supervise and coordinate the annual physical inventory counting and recording
- Ensure compliance with DOT and safety legislation and related company policy by ensuring proper training, maintaining warehouse vehicles and equipment, verifying employee driver's licenses and permits are current and maintained
- Develop Distribution Center budget and routinely analyze and control expenditures to meet budget requirements
- Serve as Primary contact between Distribution Center operation and business unit managers. Communicate with customers and company personnel to resolve customer problems and expedite customer deliveries when necessary
- Implement health and safety initiatives of the business
- Bachelor's degree, or an additional 8 years of equivalent work experience will be considered in lieu of degree
- Minimum of 5 years leadership experience with logistics knowledge
- Prior experience leading non-exempt workforce
- Ability to set metrics and drive goals down to the individual level to achieve results
- Prior experience managing Profit & Loss center
- A thorough knowledge of warehousing principles, practices and procedures is required
- Prior work experience in logistics field
- Working knowledge of warehouse safety & compliance
- Excellent written, verbal, interpersonal, and presentation skills are required
- Organization and time management skills, detail oriented, able to prioritize in a multi-tasking environment and ability to work under pressure and adhere to deadlines
- Strong analytical, troubleshooting, and problem solving abilities
- Develop and enforce warehouse safety procedures, programs, and activities; promote high level safety awareness among the team
- Experience with startup facilities with a focus on Greenfield experience
- Experience in working with chemical type products stored in drums
- Assist in the development of individual and team performance improvement goals aimed at supporting achievement of company objectives
- Direct staff: select, hire, train, coach, develop and assure performance
- Promote, develop, and maintain a work environment that promotes employee inclusion, recognition and effective communication
- Maintain effective, positive employee relations in the facility, to attract, retain, and motivate highly qualified employees
- Develop new operating policies and procedures in the distribution process to foster and ensure continued process improvement
- Identify the root cause and impact of delays or other issues in the distribution center; implement corrective actions in a timely manner
- Limit inventory risks throughout operation by insuring: regular cycle counts and audits occur
- Establish goals, operational procedures, objectives and position responsibilities for direct reports
- Experience with Lean Principles or Six Sigma processes
- Analyze operations and develop/recommend/implement continuous operational improvements
- Manage work schedules according to fluctuating customer demand
- Perform other job-related duties as assigned
- Interface directly with the customer to ensure issues are resolved in a timely manner while maintaining a high level of customer satisfaction
- Strategic operational planning and execution for the operation
- Directs the day-to-day activities of a central warehouse facility that is responsible for the distribution of product
- Plans, supervises and records, either by manual or automated inventory control system, the receipt, storage and distribution of equipment, supplies and specialty items in centralized warehouse operation
- Compiles and submits regular reports of damaged or outdated stock or supplies, over/under shipments, return of goods to manufacturer, etc
- Contacts manufacturers and customers/dealers to reconcile invoice discrepancies, shortages or over shipments or to arrange for emergency shipments or requisitions
- Oversees inventory control, including maintaining accurate daily inventory, monitoring inventory variances and supervising periodic full physical inventories, supervises maintenance of facilities, product handling equipment and inventory warehousing control systems, manual or automated
- Provides daily oversight and supervision for assigned staff
- Champions safe working conditions
- Coordinates all warehousing activities with management and administration
- Develops and implements storage systems and procedures to obtain maximum use of space and storage areas
- Ability to work with employees at all levels at the center and across the Company, as well as successfully interact with outside vendors and Company customers/dealers
- Experience: Previous management or supervisory experience; experience in the receipt, storage or distribution of supplies or equipment preferred
- Manages materials, equipment and supplies by directing receiving, warehousing and distribution services. Supervises warehouse staff and truck drivers
- Managing the layout and set up of the warehouse for the appropriate storage of goods and supplies
- Implementing cost cutting rules in all aspects of storehouse transactions and related activities
- Maintaining and overseeing the shift allocations and workings of all warehouse staff
- Setting and allocating targets to warehouse staff and organizing staff training activities
- Coordinating and negotiating with transporters for dispatch of goods
- Ensure that the operation complies with all federal and state laws that regulate the transportation industry
- Strong leadership and motivational skills with effective team building capabilities
- Knowledge of the safety and legal procedures for handling and receiving goods
- Ability to effectively manage time and resolve crises
- Experience of 4 to 5 years in the field of warehousing or supply chain
- Manage annual warehouse budget (to include all labor, shipping, and external services/goods costs)
- Schedule the receiving and delivery of raw material and finished products in a timely manner (production facility only)
- Ensure optimal inventory levels of full goods are maintained in order to fulfill daily sales needs
- Supervise the efficient building and loading of orders to minimize customer out of stocks
- Develop capability of warehouse loading team and Product Availability Supervisors
- Manage OSHA mandated audits and controls
- Oversee pallet certification process and monitor Customer Connect (Service) Performance Scorecard
- Manage Emergency Response process for the entire facility
- Manage Environmental (EPA) audit and control processes (structural, electrical, etc.)
- Manage PBG internal Control and Compliance controls (including "check in/check out" process, inventory, administrative paperwork for Fleet, Warehouse, and vendor reports and billing)
- Act as liaison for all municipal power and water suppliers
- Act as a liaison between Sales and Production to ensure proper execution and adequate product levels to support special sales and promotions
- Bachelors degree; preferably in Supply Chain Management, Operations Management, or Electrical, Chemical, Industrial, or Mechanical Engineering
- Oversees inventory management and loading operations within a large plan
- Effectively growing Manufacturing and Warehouse capability through coaching and support, standardization of measures, and strategic development of quarterly and annually objectives
- Leads Manufacturing and Warehouse processes through consistent product availability, warehouse productivity, national inventory program, asset preservation and reliability, and cost reduction while consistently meeting and exceeding quality assurance standards
- Build people capability through effective employee relations, hiring, training, and communication for both management and front-line hourly personnel
- Profit and Loss (P and L) responsibility for transport, fleet, and warehouse loading operations
- Ensures compliance with all Health and Safety regulations
- 5 plus years of work experience in warehousing required
- 2 plus years work experience in a management position
- Experience in consumer package products or similar industry preferred
- Ability to develop Standard Operating Procedures
- Strong employee relations, interpersonal and verbal/written communication skills
- Strong computer skills required
- Solid problem solving, planning, process
- Follow company policies and procedures and define responsibilities of subordinates. Evaluate and conduct employee performance appraisals and relay information about the operation of our company to insure the company goals and objectives are obtained
- Must be a self starter and be able to lead others and give direction
- High School Graduate or equivalent preferred
- Read, Speak and Write the English language
- 21 years or older
- Overall responsibility of store administration
- Maintain stock information, monitor daily material movement and actual production schedules versus inventory levels
- Inventory control, stock turnover analysis and materials scheduling
- Make shift planning for store personnel
- Lead a diverse team of 16 warehouse specialists, including training and development in regards of performance, safety, compliance, SAP, processes
- Plan, direct and monitor all activities in the warehouse and proactively initiate improvement activities to implement best in class processes
- Develop and manage warehouse operations to control effectively the receipt, storage, picking and dispatch of products and systems to customers worldwide
- Ensures high delivery performance in both export and domestic business
- Manage the material flow to and from our Production Unit in Bulgaria
- Manage a team to meet departmental goals via appropriate allocation of workload and effective resource management
- Formulate performance improvement plans and make termination decisions as necessary
- Interview, select, train, and develop new employees
- Evaluate employee work and productivity and monitor for process adherence and compliance
- Responsible for inventory control procedures by managing inventory levels to ensure crews have material to meet installation needs, maintaining cycle count accuracy (scrap/adjustments/variance/loss reduction), and meeting or exceeding turn goals by balancing inventory levels to ensure targeted demand is fulfilled
- Manage auditable records including but not limited to packing slips, pick lists, Great Plains Journal Entries, job close-out paperwork, warehouse safety audits, etc., ensuring documents are easily retrievable on demand
- Meet or exceed spend targets as it relates to variable and fixed costs for the warehouse facility via systems currently in place, and/or works with appropriate staff to establish new systems of measurement
- Oversee materials transfer to other sites to include vendor issue resolution
- Responsible for metric achievement, including processes & procedures implementation and actions to achieve all metrics
- Establish and control handling and storage plans and procedures and schedule maintenance for install and audit vehicles where appropriate
- Insure the security and proper management of the warehouse equipment and materials received and stored
- Manage departmental vendor invoices, oversee freight documentation and maintain complete and accurate safety & hazmat records and complies with all appropriate standards
- Train warehouse and support staff
- 1-2 years of relevant warehouse experience
- Experience with material planning a plus
- Must have a clean driving record (example, no DUI in the last 5 years)
- Detail-oriented, resourceful and able to manage shifting priorities
- Ability to positively and effectively interact with internal and external customers
- Regular, reliable and predictable performance required
- Must be able to successfully pass a pre-employment criminal screen. Additional pre-employment driving and drug screens may be required based on job responsibilities
- Key member of the manufacturing operations management team, reporting directly to the director of manufacturing
- Manage the warehouse and inventory control functions for the entire manufacturing site
- Ensure monthly revenue targets are attained
- Exceed goals on key performance metrics related to inventory control, safety, quality, delivery, and cost
- Ensure budget objectives are met by assisting in the preparation of an annual budget; scheduling expenditures; analyzing variances; and initiating corrective actions
- Assist in process audits; inventory audits;ISO audits
- Lead continuous improvement efforts beyond the warehouse and manufacturing floor to achieve global supply chain optimization goals
- Mentor, train, and develop world-class employees for career progression
- Great communication skills in order to effectively partner with vendors and drive the business forward
- Actively use Aramark technology and tools to minimize product costs and maintain tight inventory controls
- Establish proper products alongside a hand in supporting sales volume and product mix
- Hire, train, coach, and develop, schedule and discipline members of the Warehouse team
- Engage staff and actively participate with hands-on execution of events from a Warehouse and Concessions perspective
- Bachelor's degree is an asset, equivalencies will be considered plus 1-3 years’ experience in a warehouse setting
- Responsible for supervising the accurate and efficient process of receiving stocking shipping replenishment and picking all classes of merchandise
- Ensures compliance with all government regulations
- May assist the Operations Manager in the preparation of the department budget and ensures warehouse operations with approved budget; manages associates and warehouse supplies to operate within the departmental budget
- Effective presentation skills
- Ability to meet deadlines and work in a production-driven environment
- Responsible for developing the overall equipment preservation, rigging and lifting plans for the project
- Responsible for project equipment and material management from arrival on plant to the delivery on construction site
- Overall equipment and materials receipt, logging, inspection, storage, preservation and site delivery management
- Working with multiple contractors to ensure timely delivery of equipment and material to each work package contractor
- Managing warehouse staff productivity and running an efficient process from receipt on site to construction
- Perform procurement and logistics functions to where applicable
- Attract, retain, and develop effective Warehouse personnel to ensure an efficient, motivated, and skilled workforce
- Monitor product inventory levels and available saled/production/transportation data to ensure product is available when/where needed to support sales activity
- Lead and Manage Production Warehouse
- Work Cross-functional with all departments to endure quality and maximize productivity
- Manage a smooth, efficient, cost effective operation to include labor management, supervision of all aspects of services and inventory control and manage P&L statements
- Oversee all Retail merchandise and non-merchandise inventory, receiving, processing of receiving on appropriate forms, stocking, cleanliness and organization of stockroom and delegation to warehouse attendants
- Analyze and recommend logistics solutions that provide an optimal inflow of property shipments
- Provide effective and timely tracking, processing, coordination, and clearance of import shipments
- Promote and develop team-oriented philosophy stressing the importance for providing unparalleled commitment to excellence in service
- Manage any discrepancies with orders, inventory or processing
- Provide guidance and leadership to the Warehouse Supervisor
- Conduct shift briefings with Warehouse Supervisor to review daily operations
- Lead and control work output of staff to include but not limited to work assignments, time and attendance record keeping, and quality assurance
- Assess shift schedules to maintain control of staffing needs
- Review training documentation for all new hires on shift
- Review and approve requests for days off, vacations and leaves of absence (LOAs)
- Enforce Company and department policies and procedures
- Ensure all equipment is in proper working order and accounted for prior to leaving for the day
- Ensure a safe, clean & compliant environment
- Motivate and promote teamwork
- Identify and train personnel to ensure continued professional development within the department
- Communicate and respond, both internally and externally to any operational/ scheduling issues
- Ensure that vendor shipping documents are received in a timely manner
- Perform post entry auditing on import documents
- Provide backup to the domestic traffic department as needed and manage and report all damage claim activity
- Warehouse Supervisor
- Bachelor’s Degree in Business Management, or equivalent work experience
- At least five (5) years of experience in dock/warehouse/transportation management
- At least three (3) years of experience in working in a warehouse
- Ability to communicate, both verbally and written, clearly and concisely and interact effectively at all levels and across the organization
- Working knowledge of Microsoft Office
- Ability to work independently as well as collaboratively with all levels of the organization
- Ability to lead and mentor a team
- Lead transportation planning of all material inbound & outbound through internal and external logistics
- Monitoring customer delivery performance, cost reduction programs, lead-time improvements, and quality improvement projects to metrics targets
- Establishing cost and quality goals and ensuring efficient integration of factory, supply chain, logistics, maintenance and quality to achieve targets
- Optimizing material flow throughout the plant site, ensuring availability of needed resources, to include operating personnel and material handling equipment, always working to eliminate traffic bottleneck
- Providing management for the development and implementation of cost effective material handling plans and equipment, including purchased logistics services,
- Establishing general policy including schedules to be followed on all three shifts, servicing production area needs in off shift hours
- Maintains and reviews a range of Logistics performance measures to drive continuous improvement
- Lead, guide & coach to develop & maintain the high level of logistics performance
- Report on achievement of targets and identify any correction, preventive actions to have sustainable good result and people management
- Male or Female not over 45 years old
- Bachelor degree or higher in Supply Chain Management, Transport Management, Logistics Management, or any related fields
- Minimum of 10 years direct of experience in logistics management, transport management and supply chain
- Expert knowledge and understanding well Lean Supply Chains, External & Internal Logistics, handling systems and Parts Physical Inventory management, lean concept, continuous improvement, cost deployment, projects management in Material Handling /Logistics areas
- CPS Functional Job Role Qualified;· APICS CPIM or CSPC National Certification will be advantage
- Understanding of the various materials systems and how they interrelate
- Capable of working and communicating with a variety of company (all levels) and supplier personnel
- Strong problem-solving skill,
- Good interpersonal teamwork and leadership skills
- Excellent communication in English and collaboration skills
- Ensures products, parts, or supplies are shipped, distributed, or received in an efficient manner
- Confers with department heads to ensure coordination of warehouse activities such as production, sales, records control, and purchasing departments
- Screens and hires warehouse personnel and issues work assignments
- Controls costs through productivity of personnel, efficient utilization of storage space, and proper protection of stored materials
- Responsible for enforcing company policies of conduct and safety and initiates disciplinary action
- May require availability outside of normal business hours
- Bachelor’s degree in supply chain, business logistics, engineering, or related discipline
- Strong background based on warehouse management or related disciplines
- Well versed in Logistics tools and techniques
- Experience on people management
- Must demonstrate strong problem solving skills, organizational skills, and the ability to work
- Demonstrated influence management skills and organizational know how
- The role is subject to gaining HMP Security Clearance
- Instructing and Training a group of prisoners in an enclosed environment
- Working in close proximity (face to face contact with prisoners)
- Liaise with Supervisors and other Management to ensure targets are identified and act as a point of reference for operational problems
- Ensure that you and your team operate in accordance with company policy, procedures and legislative requirements
- Develop a highly motivated team of Supervisors by encouragement and promotion of open communication, leading task setting activity, holding regular briefing sessions and chairing minuted managers meetings as required by the Site Operations Manager
- Ensure all Health and Safety Legal requirements are met and adhered to
- Ensure all Supervisors conduct disciplinary meetings where necessary to prevent failure of an employee to reach required standards or KPI targets
- Actively support and communicate issues relating to operational performance , Health and Safety, Colleague Liaison Boards and deputise for the Site Operations Manager on occasions with regard to chairing , leading and documenting meetings on the above
- Assist in the recruitment and training of new staff. Ensure induction training for all new starters and agency workers is carried out within your area of responsibility
- Oversee daily activities of the warehouse to maximize production goals and requirements
- Utilize 5S methodology to keep the warehouse well organized, neat, and clean
- Answer the dock door to receive in all shipments, utilizing forklift and pallet jack when necessary
- Ensure safety of everyone in the warehouse through proper training and OSHA adherence
- Execute all projects in the most efficient manner, managing productivity and reporting results
- Responsible for temp labor management, material purchasing, project setup, and execution
- Establish and implement job assignments for temp staff to effectively ensure efficient operations
- Must be able to supply sound communication and motivation techniques to supervise, develop, coach, and lead the team
- Exceed operational goals as related to sales, profitability, expenses and operations through implementing and coordinating systems and processes
- Responsible for all items that arrive or leave the warehouse must be logged into the system promptly and delivered as required
- A working knowledge of all items on the warehouse floor at all times is required
- Arrange shipping to customers –will involve label making, domestic and international freight scheduling, and cost analysis to determine best shipping methods
- Provide tracking to external customers and internal team
- Coordinate daily receipt of inbound freight, interfacing with brokers and vendors
- Process all supporting documentation including BOL, packing slips, and invoices
- Prepare shipping documentation for outbound shipments
- Report metrics of position on a weekly basis to Internal Process Manager
- Update all daily and monthly operating reports as directed
- Review ongoing departmental performance results and take corrective measures as needed
- Maintain a clean, orderly, and organized warehouse
- Ensures safe working conditions including properly training employees on proper safety methods, assists Human Resources with the management of workers compensation claim
- Audits various paperwork and postings for accuracy and compliance with appropriate local, state and federal laws, statutes and company policies
- A real passion for service and customers
- Strong desire and belief to be the best in all aspects of your role
- Smart personal appearance
- Clear and confident verbal communicator
- First he ensures the optimisation of the daily tasks in order to facilitate flow (unpacking, returns, preparation, shipment)
- His role is also to ensure the updating of inventory and transfers to other depots
- He optimises the operational costs and ensures the purchase of warehouse consumables
- As a manager he allocates the workload within the warehouse's operational staff and organises inventories with the logistics manager
- Finally he ensures the overall stewardship of the building and participates in the improvement of safety conditions
- Plan work schedules and assign duties to maintain adequate staffing levels, to ensure that activities are performed effectively, and to respond to fluctuating workloads
- Enforce company policies and procedures, abide by same
- Inform designated employees or departments of items loaded, and problems encountered
- Managing office, warehouse, and delivery personnel; potentially across multiple locations
- High School Diploma or GED with significant experience related to warehouse operations
- Warehouse experience in a lead capacity
- Supervise staff to include hiring, training, evaluating performance, providing compensation recommendations, and determining disciplinary actions when necessary
- Manage the warehousing and related supply chain operations of the location with a moderate or complex customer requirements and product base, which includes the implementation and administration of warehousing and distribution programs, safety initiatives, applicable quality and efficiency improvement measures, and related areas; may involve a complex material or product mix with high volume
- Manage activities among various departments at the location, such as inventory management, traffic, distribution, production, and quality control to implement, monitor, and update operations, processes, equipment, and related areas
- Assist with developing and implementing an overall warehousing and supply chain strategy at the location, such as supply chain metrics, resource allocation, efficiency and safety programs, budget development, and process improvement projects; ensures applicable measurements are met
- Develop, analyze and review a variety of warehouse reports to improve customer relationships, costs, quality, efficiency, cycle times, volumes, and implement management changes as required across the functions
- Develop appropriate policies and procedures to ensure compliance with warehousing or supply chain principles and practices and applicable laws, rules, and regulations; monitors compliance with these areas
- Perform a variety of projects that require project management principles, various warehousing and supply chain practices, and collaboration with other departments within the division
- Assist with developing and monitoring the location budget
- Six years of warehousing experience, including two years of supervisory experience
- Bachelor’s degree in Business Administration or Operations Management or equivalent education and experience
- Manage various warehousing and related supply chain departments
- Apply broad warehousing and supply chain management principles and practices
- Develop and implement policies and procedures
- Apply project management principles and practices
- Develop and analyze warehouse and supply chain reports
- Interpret and apply department policies and procedures and applicable laws, rules, and regulations
- Lead various warehousing and supply chain operations for the location
- Interact with senior management
- Microsoft Office applications (Word, Excel, PowerPoint, Outlook); and other applicable applications
- Communicate effectively with co-workers to provide and receive direction
- Lead and supervise team of Area Managers (2-5 front-line supervisor depending on location), and 100-300 hourly associates in outbound or inbound operations
- Manage the receipt and storage of inventories, the maintenance of accurate inventory quantities within the system, and the shipment of requested inventories in accordance with customer instructions on a timely basis
- Prepare budgets, reforecasts, roll forwards and supporting schedules; monitor performance against same; and explain variances as required. Responsible for meeting and exceeding operational goals
- Strategic planning and forecasting; Hire, develop, discipline and terminate employees in a fair manner consistent with Corporate policies and procedures. Includes preparation and communicating annual performance reviews in a timely fashion
- Communicate with Sales, Marketing, Customer Service, Production Planning, Manufacturing, Industrial Engineering, I.T., and Human Resources on issues related to order requirements, future inventory availability, personnel issues, shipping requirements, operating costs and other business issues as required
- Develop, implement and monitor procedures necessary to ensure compliance with customer labeling and shipping requirements
- Review, question when appropriate, and approve invoices for warehouse expenses in accordance with Company Approval Authority
- Monitor developments and new technologies in Supply Chain Logistics. Communicate any opportunities to management with recommendations to improve processes or customer service that will result in a lower total cost to service our customer
- Promote safety and provide a safe working environment for all employees. Monitor compliance with local, state and federal safety and environmental laws and regulations
- Maintain the physical facilities and equipment utilized for warehousing and shipping finished goods in a safe and operable condition
- Communicate problems, issues and other significant events to the Vice President Logistics on a timely basis
- Promote a positive Company image through participation in approved community activities. Mentor, train and develop teammates for career progression and learning. Develop and share best practices
- This position requires proven ability to drive process improvements and the ability to keep pace with our explosive growth while motivating others to meet the challenges of an extremely deadline-driven environment
- Other responsibilities as may be assigned by the VP Logistics
- Bachelor’s degree in Engineering, Operations or related field. MBA preferred
- 5+ years management experience in manufacturing, production or distribution environment
- 2+ years Amazon experience
- Direct Management experience with a salaried employee population
- Proficient with shipping requirements of major retailers, replenishment order picking and shipping strategies, broken box picking, material handling equipment and a general knowledge of business and transportation law
- Experience with performance metrics, process improvement and Lean techniques
- Experience with a contingent workforce during peak season
- Ability to work weekends and/or overnight shifts regularly
- Ability to handle changing priorities and use good judgement in stressful situations
- Therefore, you’ll aim to achieve productivity targets, reduce cost per unit, eliminate errors and ensure an excellent customer experience,
- Implement process change and contribute in cross-functional Six Sigma initiatives within your site and the broader Amazon EU Operations network
- Possess a degree level qualification
- You’re competent in two or more production or supply chain areas, with an impressive track record in a similar, fast-paced logistics, distribution or manufacturing environment,
- You possess the ability to manage details, establish and carry out root cause analysis, and then extract and analyse the data you generate,
- You thrive on change, and are willing to relocate if necessary,
- You have excellent written and spoken English
- Receive all incoming shipments and transfers, ship outgoing transfers, debits, and fast finds, maintain shipping logs, and file all paperwork according to audit requirements
- Complete transfers, consolidations, and debits while maintaining inventory integrity and stockroom organization
- Support general store maintenance and presentation including inventory replenishment, maintenance of store fixtures and floor layouts, seasonal changeovers, restocking and pricing/signing changes
- Maintain an organized and clean shipping/receiving area, and ensure health/safety standards are upheld
- Proactive participation in Weekly Managers’ Meetings with other store leaders to align work efforts and achieve success as a team
- Highly organized and detail oriented
- Proven ability to set goals and create roadmap to accomplishing goals
- Leadership experience and ability to drive team success
- Effective communication with team and managers
- Ability to work independently and in team environment
- Computer literacy is an asset
- High school education
- Physical qualifications include the ability to work long hours standing/walking, lifting up to 50 lbs, reaching above shoulder height and stooping/bending/crouching
- A flexible schedule with availability to work evenings, weekends, and off store hours
- You will play a critical role in the management, control and direction of either Outbound, Inbound or Reverse Logistics area of Operations within our Fulfilment Centre. The extent of your duties will include
- Lead, motivate and support a large team within a time-sensitive and demanding environment. This will include the setup and implementation of career development plans for all direct reports
- Be a Subject-Matter Expert on larger processes and activities within the fulfilment centres, i.e. 5s audits, alignment with Standard Work procedures across the network
- Work closely with other support teams (HR, Financial Manager, Facilities Manager, Safety & Security Manager, IT Manager) on staffing plans, schedules and performance levels to enable the Fulfilment Centre and the broader Operations network to attain Amazon’s Business Plan
- Have excellent communication skills, both verbal and written
- Be competent in two or more production or supply chain areas, with an impressive track-record in a similar fast- paced logistics, distribution, manufacturing or engineering environment
- Have a sincere bias for action and be passionate about achieving results and driving production through efficiency and process improvement
- Implement process change and contribute in cross-functional Six Sigma initiatives within your site and the broader Amazon EU Operations network,
- You’re fluent in English,
- Master’s degree, or equivalent Level 7 qualification,
- You possess a grasp of Kaizen and Lean methodologies and related techniques
- Strong planning, change management and organizational skills
- High degree of initiative, team building and dedication to effective positive change
- Leadership of the Warehouse Team, ensuring their ongoing development and engagement in achieving Warehouse KPI,s and contribution to the overall site performance and success
- Ensuring full compliance with Company and Regulatory Authorities Safety Health and Environment systems, policies and procedures
- Involvement in Total Performance Management activities within and beyond the Warehouse function
- Inventory accuracy of all materials
- Analysis of stock levels to optimise material flow and future Warehouse requirements to meet Production Planning and Procurement requirements
- Management of projects ranging from implementation of new procedures to equipment and technology upgrades
- Ensuring timely and accurate dispatch of finished goods to local and export markets
- Demonstrated capability to lead teams and manage for results
- Leadership experience within a Warehouse environment and relevant industry experience
- Strong communication skills as you will be working closely with our Production and Procurement teams
- Previous experience working with an inventory management system (preferably SAP)
- TPM experience highly regarded
- Bachelor Degree minimum
- Min. 5 years of operational experience in industrial distribution or warehouse environment with at least 3 years in a leading role
- Strong leadership and interpersonal skills
- Professionalism and dedication to develop and train employees
- Ability to work independently, under pressure, tight deadlines and pro-active in solving problems
- Proficiency in Thai and English is a must, German is an advantage
- Ensure Operational SLA's are met and maintained
- Plan, direct and implement warehouse operations and administrative support to meet prescribed productivity and services goal
- Ensure the development of systems and procedures for operating and managing physical facilities, human resources, equipment and product in a profitable manner
- Operate in compliance with local statues with special focus on hazardous goods, customs and food storage regulation
- Initiate structured programs to monitor and improve quality / Productivity constantly managers continues improvement for site together with local KNPS manager
- Acts as escalation point of customers vendors and service providers
- Ensure health and safety standards applicable for the site
- Master Degree in Logistics
- Proven knowledge and understanding of warehouse operations and related processes
- High level knowledge of warehouse management system + MS Office
- Proven understanding of practical inventory management in warehouse environment
- Extensive experience in people leadership, able to lead teams through coaching and development
- Previous strong Logistics/ FMCG experience from a people focused business
- Strong commercial acumen to drive performance and analyse financial data
- A strong track record of delivering excellent results through a team
- Background in Lean and Continuous Improvement
- Monitor and correct unsafe acts and conditions, supervise, discipline and direct work of Warehouse Operators
- Timely, damage free delivery of product per releases against Scheduling Agreements using most cost effective and customer friendly delivery options
- Analyze need and arrange appropriate most cost effective transportation logistics, challenge Customer Service guidelines for shipping when appropriate, evaluate carrier performance and select alternatives
- Supervise and audit data entry, implement proactive corrective action to insure error free posting and billing
- Monitor and correcting record keeping activities to insure accurate inventories and shipping records
- Keep operating supplies at minimum while meeting OE delivery expectations
- 3+ years warehousing, inventory control, distribution and transportation responsibilities
- Manage the WH inventory to ensure all material and stocks are kept in good and safety condition
- Arrange regular cycle counting and physical counting to make sure inventory accuracy and fulfill company’s KPI target
- Establish and maintain warehouse management system including working procedure, reporting & filing, security and safety standards, SAP WM system improvement
- Develop and train warehouse team to maintain team’s competency
- Initiate and lead WH related improvement project
- Responsible for internal and external audit for warehouse management
- Green line implementation in warehouse area
- Plan, coordinate and monitor the receipt, order, assembly and dispatch of goods
- Use space and mechanical handling equipment efficiently, making sure quality and environmental objectives are met
- Manage the facility’s fixed and variable costs
- Keep Inventory control systems up to date and make sure inventories are accurate
- Plan future capacity requirements
- Analyze staffing needs and participate in recruitment process
- Ensure proper training of staff and analyze future needs
- Monitor staff performance and progress using progressive disciplinary measures as required
- Motivate, organize and encourage teamwork within the workforce to ensure productivity targets are met or exceeded
- Ensure all Health and Safety rules are met and suggest preventive measures to improve the overall H&S standards of the facility
- Produce regular reports and statistics on a daily, weekly and monthly basis
- Visit customers to monitor the quality of service they are receiving
- Participate in customer reviews and projects
- Provide frequent communication and feedback to the team
- Drive Continuous improvement methodology throughout the facility
- A minimum of 5 years of experience in a supervisory capacity in Supply Chain/distribution network is required
- Experience managing business processes and leading large groups of individuals (preferably in a distribution environment.)
- Confirmed leadership, motivational and influencing skills
- A strong Workplace Health and Safety background
- Established communication skills (verbal, written and presentation skills) with the ability to communicate strategic concepts effectively to all levels of the organization
- Ability to work in a high pressure environment, while being adaptable and flexible (includes working various different shifts as required)
- Ability to use information technology to access, analyse and qualify operational data
- Advanced computer skills (Microsoft Office tools)
- Energetic, hard driving and able to respond quickly in a fast-paced, change oriented environment
- Experience with P&L’s is considered an Asset
- A college degree in a related discipline such as Supply Chain Management, Business Administration, etc. would be considered an asset
- Safety - Oversee ongoing safety training, forklift certification, and daily/weekly/monthly safety awareness programs
- Cleanliness - Complete warehouse organization - maintain a clean, safe and organized warehouse (be proud of it!)
- Shipping for all retailers, consumers, events, tradeshows, Costco roadshows, and international customers (targeting 100% on time shipping and 100% accuracy)
- Manage all shipments out of Domestic (Utah), Cross-dock (China), and DSV (Europe) warehouses
- Outbound freight cost and reliability – Negotiate lowest possible freight and small parcel rates with best-in-class carriers
- Receiving from all vendors and customer returns (including proper process controls)
- Returns processing - Properly disposition returned product (recycle, open box/refurb, repack)
- Inventory Management – Optimize available warehouse space, manage relationships with off-site overflow warehousing partners, zero/minimal shrink at cycle counts, full inventory counts
- Management of automated warehouse picking, packing, order management and inventory system
- In-house production (including ongoing kitting and repack projects). Ensure that production is 4 weeks ahead of sales forecast
- Planning and budgeting for full-time, temporary and contractor warehouse personnel resources
- Implement, maintain a cross-training program with all warehouse personnel
- Planning and budgeting for warehouse equipment and infrastructure improvements and maintenance
- Product inventory maintenance assuring that product is maintained and stored properly. Manage the battery maintenance tracking program
- Ability to clearly communicate with co-workers and vendors
- Demonstrated commitment to continuous improvement in all phases of warehouse operations
- Demonstrate knowledge of and implement the use of best practices
- Demonstrated performance in inventory management and controls
- Demonstrated team leader—build and motivate efficient and effective teams; team player, willing to jump in and lend a hand where needed
- Ability to use MS office suite for accounting, budgeting, communication; as well as ERP system (currently Sage/MAS) for transactional management; shipping software
- Working knowledge of retailer shipping requirements
- Experience with international shipping, including export documentation and labelling
- Knowledge of Hazmat/DOT and air and ocean shipping requirements for Dangerous Goods; current Hazmat shipping certification preferred
- Problem solver, self-directed and highly motivated; well-organized and punctual
- Focused and consistent attention to detail
- Experience using various shipping methods/vendors: UPS, FedEx, DHL, LTL, etc
- 7+ years’ experience in comprehensive warehouse operations, including budgeting, hiring, supervision, growth/transition
- Ability to operate and receive forklift certification, required
- Experience effectively managing a large team (30-40 people)
- Manage, lead, and coordinate team to procure, issue and receive MRO spare parts for the Decatur Central Distribution that supports multiple sites inventory management
- Proactively evaluate current processes and systems to identify areas of improvement that extend the value stream, along with develop and implement best practices throughout multiple disciplines
- Maintain optimum inventory stocking levels to ensure on time deliveries to meet customer requirements while maximizing turns, minimizing carrying costs, and transportation charges
- Plan, organize, and prioritize time to meet tasks and deadlines
- Manage conflict resolution including ability to address difference of opinions or facts and use the most appropriate method to reach a solution
- Analyze data to anticipate current and future needs
- Work with Global Procurement on contract compliance, item number utilization, and identifying potential contracted items
- Evaluate suppliers to achieve cost-effective inventory management and relationships
- Manage KPI’s and goals to maintain a high level of inventory accuracy and customer support that align with higher level goals and objectives
- Implement consignment and VMI process through multiple commodities
- Manage projects to improve performance & meet customer needs, generating and implementing innovations for improved performance and a logistical competitive advantage
- Monitor fixed assets & coordinates implementation of approved CARs and support budgeting for site logistics with focus on continuously improving year over year performance against metrics
- 5+ years of experience in logistics, transportation and/or warehousing environments
- 2+ years of supervisory experience, preferably in a high-SKU (500 – 1000 SKU) logistics network
- 1+ years Ecolab Supply Chain supervisory experience
- HAZMAT experience
- Directs warehouse and shipping operations of finished goods inventory to maintain minimal stock and variances
- Responsible for departmental employee relations including staffing, training, supervision, and performance appraisals
- Analyzes department procedures regarding quality, cost effectiveness, accuracy, efficiency and productivity. Implements corrective action as needed
- Communicates effectively with other departments to plan and direct work activities and resources to ensure production within quality, quantity and cost specifications
- Establishes production goals for the department(s). Monitors and documents performance against production standards. Implements correction actions where necessary
- Maintains plant and quipment to provide a clean and safe working environmen. Implements training and process improvement actions
- May establish policies and procedures related to the function
- May be responsible for Departmental Budget
- May mentor or coach staff or Supervisors
- Performs other duties as assigned
- Establishes operational procedures for activities such as verification of incoming and outgoing shipments, packaging, handling and disposition of materials, and keeping warehouse inventory current
- Manages warehouse staff by recruiting, selecting, orienting, and training employees
- Manages warehouse staff job results by coaching, counseling, and disciplining employees; planning, monitoring, and appraising job results
- Prepare and implement action plans to ensure the warehouse achieves planned productivity targets
- Coordinate with all department heads to effectively and efficiently communicate the needs of the company and its customers
- Design and implement operational and maintenance plan to ensure minimum costs and prevent operational delays
- Develop and maintain current postings of Key Performance Indicators that pertain to the state of the warehouse
- Use Lean Methodology, KPI’s and data analysis in the constant pursuit of cost reduction and efficiency in all areas of operations
- Effectively perform and mentor direct reports on how to identify issues using the Root Cause Analysis method to identify the root cause of problems or events
- Assist the VP, Operations in the strategic planning and major projects related to new or expanded locations
- 5-10 years: Management experience
- Reviews open sales orders, open purchase orders, open vendor claims, and open transfers
- Reviews warehouse procedures and ensures proper warehouse safety procedures are followed
- Consults with regional buyers and/or vendors to obtain product or service information such as price, availability, and delivery schedule
- Manages inventory, controls stock outs and reduces excessive inventory
- Performs cycle counts to prevent inventory shrink
- Manages freight expense and approves invoices/freight bills for payment
- Manages Accounts Payable discrepancies in a timely manner
- Supervises the proper routing, loading and preparing of orders for shipment and delivery in accordance with customer instructions
- Trains new employees on warehouse and distribution procedures
- Discusses defective or unacceptable goods or services with inspection or quality control personnel, users, vendors, and others to determine source of trouble and take corrective action
- Supports sales staff in meeting sales objectives
- Other non-essential job duties may be assigned
- Actively supports the Company’s commitment to safety and its “Core Values.”
- Represents the Company at all times with high moral standards while adhering to the Company’s “Code of Business Conduct and Ethics.”
- Formulate a daily, weekly and monthly plan for warehouse operations
- Inspect warehouse and grounds for hazards and initiate corrections process
- Conduct or participate in daily Job Hazard Analysis and conduct or participate in daily tool box safety meetings
- Ensure that all warehouse service staff has proper training with regard to equipment being operated and Safety Department requirements, including daily tool box talks, safety meetings, SAM alerts, SAP, safety certifications and other programs as they develop
- Work closely with Project Management/Estimating to determine resource needs for projects
- Attend large project kick-off meetings when requested or required
- Manage and monitor daily warehouse activities and ensure compliance with company operation procedures, hours of operation, attendance and use of safe work practices
- Coordinate training and employee enrichment programs with Warehouse Director
- Assist Supply Chain Management to develop, expand, monitor and maintain a qualified supplier base to allow for growth and stability and reduced costs thru supplier master service alliances
- Monitor, report, and forecast equipment capital purchases for the regional warehouse
- Identify cost effective opportunities to increase utilization of warehouse dispatched vehicles, tractors/trailers
- Monthly reporting of cost, revenue, and utilization trends of all company owned equipment
- Interface with cost control for reporting tool loss
- Monitor compliance with Fleet Manager’s maintenance program for all fleet owned/rented equipment assigned to the warehouse
- Ensure the warehouse is in compliance with DOT requirements through the Fleet Manager including supervising warehouse driver’s logs
- Oversee the dispatch of company owned equipment to jobsites, which includes maintaining the maintenance records and inspection records of all owned or rented equipment
- Coordinate dispatch and return of tools and equipment with all of the regional warehouses
- Secure any necessary trucking permits or escorts for transportation of tools and equipment dispatched to and returned from jobsites
- Manage warehouse operations including supervising safety, training requirements and implementation, staff instructions, discipline and encouragement as needed
- Participate in the process of interview and selection of warehouse employees
- 7+ years’ experience in warehousing, equipment maintenance, in the construction industry
- Previous related supervisory experience
- 2+ years’ experience in supply chain management and fleet operations
- Working knowledge of DOT rules and regulations
- Strong time management skills; ability to prioritize multiple time-sensitive requests
- Proficiency in PC applications, including Microsoft Word and Excel
- Strong communication skills, time management and organization skills, and interpersonal skills
- Ability to be on call 24/7
- The Warehouse Manager will be responsible for our Stock Control and the Returns and Credits department
- Ensuring that targets are met
- Drive continuous improvement
- Liaise with other Warehouse Managers
- Budget & KPI responsibility for thE above areas
- You will be reporting into the Operations Director of PANDORA EMEA Distribution Centre
- A Logistics Distribution backround
- Proven track record of continuous improvements, ideally in a company with fast moving consumer goods (FMCG)
- Minimum of 3 years experience in managing stock Control and Returns & Credits
- Experience of working in an international business
- Proven Ability to Effectively manage, mentor and train Teamleaders
- A good communicator at all levels
- Experience across various WMS systems would be advantageous
- A dedicated individual and results driven - Proven ability to initiate, drive and implement plans to deliver results
- Experienced in driving forward continous improvement
- Exceptional interpersonal skills and team-buidling skills
- Fluent in english, german is a plus
- 2+ years of warehouse management experience
- Go getter mentality
- Leadership of 5+ employees
- Willingness to get "hands dirty"
- Ensure activies are within business compliance, company guidelines and regulations and laws
- Manage the EHS, including monthly reporting
- Management duties including appraisals, development plans and targets, and employee surveys
- Handle the cost budget and forecasting
- Ownership of the SMT business system in the DC
- Share responsibility for freight solutions and agreements for domestics transports and exports ouf of DC
- Monthly reporting to SMT logistics with corrective actions
- Drive and develop relationships with key stakeholders (e.g. sales and IT) in Singapore and related markets
- Assemble, wrap, strap and stage orders for shipment. Process orders as packers arrive
- Receive inbound shipments; including separating reserved items from inventory items; entering into system and labeling; and placing accordingly
- Run reports to keep current on newly placed orders, as well as retrieving associated purchase orders. This keeps CNVRE current and knowledgeable in determining space considerations, as well as shipper choices
- Field all inquiries via e-mail and phone with regard to inbound/outbound. CNVRE often acts as intermediary between TSM's, delivery services and vendors
- Miscellaneous: Maintain an orderly work environment and forklift. Order office and shipping supplies. Create month-end report
- Participates in special projects and performs other duties as required
- Scientific university degree or engineer
- At least 8-10 year experience in pharmaceutical production or equivalent
- GMP for pharmaceuticals
- Advance knowledge in supply chain
- Manage, coordinate and plan warehouse storage , distribution, inventory and shipping of products and materials to meet productivity, efficiency and budget goals
- Supervise , motivate and encourage teams of blue and white collars to achieve maximum productivity
- Coordinate specific projects of improvements to ensure quality , efficiency, productivity, security
- Plan and develop systems and procedures to improve the operating quality and efficiency of the operations. Develop solutions to enhance efficiency. Coordinate and implement solutions from process solutions, analysis and general value stream projects
- Direct staff in the development , analysis and preparation of reports and the use of KPIs
- Respond accordingly to inquiries and/or complaints from employees, customers, and vendors to promote positive relationships
- Monitors workflow within established administrative procedures
- Maintain documentation in accordance with company policies and procedures (i.e., attendance and performance records)
- Utilize Lean methodologies for process improvements, cost savings, quality control, and safety assurance
- Maintain current knowledge of warehousing best practices and serve as a champion of continuous improvement activities in all aspects of warehouse operations
- Responsible for a range of general duties including follow-up on assignments, maintenance and cleanliness of warehouse facilities, informing Manager of any budget divergences and plan changes, and miscellaneous tasks/projects delegated by the Warehouse Manager
- Maintain a personal awareness and ensure others are cognizant of occupational health and safety requirements and goals
- Provides back-up to Warehouse Manager
- Demonstrated skill in lending organizational skills to warehousing operations to achieve neat and clean operational areas
- Demonstrated ability to multi-task assignments
- Demonstrated skill in the following qualities: patience, cooperation, flexibility, proactive approaches and service-oriented approach
- Demonstrated effective written and oral communication skills
- Demonstrated competence with personal computing and the Microsoft Office Suite
- Knowledge of ERP systems and reporting software, ability to generate ad-hoc reports
- Demonstrated experience working with formal quality systems and Lean operational principles
- 2-5 years of Supervisory experience
- 5-7 years of related work experience in a manufacturing or distribution environment
- Associates Degree, Bachelors degree preferred in related field
- Must speak, read and write fluent English
- Ability to interpret a variety of instructions furnished in written or oral form
- Skills in providing verbal and written feedback, including performance evaluations
- Ability to maintain positive relationships throughout the organization
- At least a Bachelor’s Degree, Diploma, Professional Degree in Logistic/Warehouse Management or equivalent
- At least 5 years of working experience in a warehouse
- Good command in the English language plus Strong team management skills
- Proficiency in Microsoft Excel, plus strong planning and analytical skills
- Control logistics processes: (yard/exteriors management, receiving, delivery to lines, bookings, TPA preparation, alert management, cycle counting in all warehouse locations under plant supervision) with strong relationship with material planners and master schedulers
- Ensure full inventory accuracy through proper analysis in case of deviance
- Ensure internal customer satisfaction: supervise day to day warehousing activities, anticipate resources in line with customer requirements (PIC/PDP), manage impact of launch of new programs within the warehouse
- Improve logistics performance: surface optimization, labour efficiency, handling utilisation, HSE, alert management with strong support from PC&L improvement function as well as other plant functions (Quality,
- Bachelor degree in engineering or economics
- 2 years experience in logistics in an industrial environment
- Operational knowledge of Production & Logistics methods
- User knowledge of SAP and Microsoft Office
- People management skills
- Minimum bi-lingual (English and Romanian required)
- Tracks and resolves problems involving damaged goods, incorrect orders, and missing goods
- Assists in developing policies and procedures for Warehouse operations
- Continually enforces productivity standards. Discusses areas needing improvement
- Plans time on warehouse floor with employees to achieve a positive presence in the facility
- Approves E-Time/Payroll records. Tracks attendance on all hourly employees
- Works with local IT group to maintain acceptable technological standards
- Knowledge of budgeting, supply contracts, and shipping requirements
- Must be proficient in Microsoft Office Applications, Word, Excel, PowerPoint
- Minimum 10 years within a large store/warehouse in a manufacturing environment
- Knowledge of Warehouse Management Principles
- Knowledge of Quality Management Systems, Environmental Health and Safety, GMP and Operational Excellence standards
- Knowledge of Microsoft packages
- Knowledge of related legislation iro storage conditions, OHS Act
- Managerial and Supervisory experience essential
- Proficient in Supply Chain business systems
- Proven track of delivering change management
- Step change results
- Strong leadership characteristic
- Must have ER/IR background to deal with unionized environment (BPCS, MGX, JDE)
- Ensures that the Goods Receiving Department performs to the required standard
- 1 Ensures that all goods received are checked and booked in correctly and timeously on a daily basis as per SOP S/101
- 2 Ensures that all representative samples / materials are locked away immediately on receipt
- 3 Ensures that all goods received have the correct status labelling e.g. “HOLD LABELS” on receipt
- 4 Ensure that the delivery schedule is adhered too
- 5 Liase with suppliers for delivery time slots
- 6 Ensure that the Bulk Raw materials is correctly received and picked for NAR scanning in the Dispatch Warehouse
- 7 Ensure daily sampling is adhered too
- 8 Contacts the Purchasing, Supply Plan Department and the Laboratory Manager with regards to damaged goods and incorrect or no documentation received
- 9 Ensure that supplier alerts is raised for damaged and incorrect goods received
- 3 Log picklist on a daily log
- 4 Issues Pick Lists to Turret Stock Pickers and co-ordinates Picking activities
- 5 Ensures that all Pick Lists and Requisitions are completed properly and issued to the Data Capture Clerks for stock level adjustment on the BPCS system
- 6 Ensures that all Shop Orders are completed properly and booked to the next operation on the BPCS system when collected by production
- 7 Co-ordinates the delivery of components for production from various off-site storage locations as required
- 8 Identify and analyze resources which are bottlenecks and make recommendations on how these bottlenecks can be overcome
- 9 Ensures that the approved report for Raw Materials and Components is completed on a daily basis for the items in the Bulk Store and Dispatch Warehouse
- 3 Completes the Level 1 Audits in the Warehouses and assist in Internal Level 2 audits as an auditor as required
- 4 Maintains Good Housekeeping in the Warehouses through regular cleaning and 6S
- 5 Ensures environmental monitoring & recording is completed in the Warehouses as required
- 6 Ensures all lot controlled stock bear the correct status labelling and are segregated as per the applicable SOPs and Regulatory requirements
- 7 Complete Warehouse business risk assessments; manage and mitigate risks in line with GSK Risk Assessment & Management Standards on a regular basis
- 8 Participates in audits e.g. Level 2, MCC, ISO, MHRA, etc. and mitigate any findings that arise expeditiously Updated GQP,GDP and QMS standards
- 4 As changes to the working environment occur ensure that the relevant systems are updated to reflect needs and ensure that training is executed and records updated
- 5 Coaching staff when new procedures and policies or individual/group performance is substandard
- 6 Identify potential skills shortages and recommend a plan of action to remedy this threat. Competent and skilled Productive workforce
- Ensure Bulk Store and Finished Goods Warehouse compliance with EHS standards
- 1 Ensures that the relevant policies and procedures are being adhered too at all times
- 2 Identifies work place hazards in the Warehouses and related areas. Develop and implement mitigation plans to eliminate / reduce the hazard
- 3 Provides appropriate personal protective clothing and equipment based on risk assessments
- 4 Ensures that appropriate personal protective clothing and equipment is worn, maintained and stored correctly
- 5 Include EHS related training requirements in training matrix and ensure that all staff are competent by completing training
- 6 Ensures that material requiring special storage conditions e.g. flammable, refrigerated, explosive, etc. is handled in line with local legislation and GSK standards
- 7 Investigates, document and report all Near Misses and Adverse Events
- 8 Ensure corrective action decided upon as a result of an incident or accident is implemented
- 9 Ensures compliance to applicable EHS standards in addition to those listed above & create EHS awareness & culture among subordinates
- 10 Participates in audits e.g. Corporate EHS, etc. and mitigate any findings that arise expeditiously
- 11 Ensure that the Level 1 EHS audits is carried out timeously to eliminate the problem/issue and its possible reoccurrence
- 12 Ensures that all employees are inducted and aware of the risks involved in working in their areas of work. Safe working environment in which the risk of incidents and accidents is greatly reduced
- Maintain equipment to required standard in the Bulk Store and Finished Goods Warehouse
- 1 Liaises with Engineering Department and Suppliers to repair damages to facilities & equipment
- 2 Ensures that planned maintenance is performed on applicable equipment e.g. dock loaders as per the prescribed schedule
- 3 Ensures that all equipment meets validation requirements and understands change control procedure
- 4 Takes corrective action when critical pieces of equipment e.g. scales do not meet the specification
- 5 Ensures that all forklifts and pallet trucks are in proper running order before commencement of the day’s work
- 6 Ensures that the batteries of Turret Truck Machines, Forklifts, Pallet Trucks and Walkie Stacker used are filled with water at the end of the shift and the machines placed on charge
- 7 Liaises with contract company to service and repair forklifts as required
- 8 Challenges and optimizes processes by completing OE projects and regular JDIs within the parameters of the QMS on a continuous basis
- 9 Ensure sufficient equipment available to meet operational demand. Well maintained equipment
- Continuously improve Bulk Store and Finished Goods processes
- 1 Regularly assess the internal and external supply chain to formulate and propose changes
- 2 Regularly assess the physical layout and flow through the Warehouses to identify any possible shortcomings and make necessary proposals
- 3 Have discussion with staff regarding ways of improving productivity in their work areas. Come up with a plan of action to implement agreed improvement suggestions
- 4 Continues monitor system performances and make recommendations for improvements
- 5 Stay well informed with all new developments in this area for acquisition of future enhancements.Streamline supply chain to provide excellent customer services
- Ensures clear communication/Problem solving and troubleshooting between Bulk Store/Value Streams and customer service Logistics
- 1 Liaises directly with Value Streams, Dispensary, QC Labs to establish daily, weekly and monthly production requirements
- 2 Liases directly with the customer logistics team in Bryanston for all local requirements and Logistics controller for all export related matters
- 3 Attends Value Stream Board Meetings to understand daily requirements & re-priorities daily schedules if required
- 4 Liaise with the different departments and suppliers to resolve problems immediately, which affect the efficient and productive running of the various sections
- 5 Attends SLT meetings in the absence of Site Logistics Lead
- 6 Attends weekly Warehouse Management meetings
- 7 Conducts Bulk Store and Finished Goods Staff meeting each morning to plan & prioritise daily work
- 8 Facilitate meetings between individuals/groups where consensus can’t be reached on matters of mutual interest, which will affect the efficient and productive running of the various sections. Good Communication/ Effective management of problems and change
- Personnel Performance Management
- 1 Manages Warehouse personnel in line with GSK Managerial Standards including taking disciplinary action when required
- 2 Authorises all leave absence of subordinates in accordance with the Company Policies and Procedures Manual
- 3 Ensure robust PDP’s are in place for all subordinates
- 4 Ensure Robust development plans are in place for all subordinates
- 5 Recruits, inducts, trains and coaches Warehouse personnel to required standard
- 6 Conducts required performance appraisals in line with Company policy and procedure
- 3 Completes reasonable duties and related ad-hoc projects when required
- Initiative, drive for results and continuous improvement
- Understanding of e2e Supply Chain planning processes and interaction with other areas of the business
- High levels of energy and initiative to manage competing priorities and meet critical deadlines
- Bachelor’s degree required, preferably in Operations/Materials/or Supply Chain
- Experience within a production/inventory control environment
- Working knowledge of an ERP systems is essential, preferably SAP
- At least 2 years of production or warehouse supervisory experience
- Rockwell Automation will only employ those who are legally authorized to work in the United States for this opening. Any offer of employment is conditional upon the successful completion of a background investigation and drug screen
- Experience leading in Shipping/Receiving environment
- 5 years of people manager experience
- Monitors accuracy of bin maintenance, stocking and order pulling to insurecustomer satisfaction
- Monitors expense budgets for repair and maintenance of equipment and overallbuilding expenses
- Communicates directly with purchasing department on shipment errors andinventory needs, and schedules all inbound overseas containers to bereceived
- Oversees recycling center to assure correct scheduling of product
- Responsible for training and development of all warehouse personnel, toinclude hiring and evaluating employees
- Worksdirectly with satellite managers on maintaining accurate delivery of stockorders and sold product transfers delivered on a daily basis
- Comply with all safety standards and requirements to assure a safe andhazard-free workplace
- Initiate and support the continual improvement of LKQ Corporation qualityimprovement system
- Supervises, trains and motivates warehouse employees
- Assists in accurately pulling, filling, packing and setting up orders for delivery or pickup
- Manages Safety and HAZMAT compliance for the facility
- Establishes operational procedures for verification of incoming and outgoing shipments, handling and disposition of merchandise, and keeping of warehouse inventory
- Maintains effective security and inventory control procedures
- Manages driver-related issues including drug screens & licensing and handles fleet issues including DOT compliance
- Ensures all equipment is stored at end of day and all doors and gates are secured
- Other job duties may be assigned
- Supervise multi-skilled warehouse personnel as assigned, to ensure that performance meets established safety, quality/Good Manufacturing Practices (cGMP), quantity, warehousing and cost standards
- Import, export, and hazardous materials compliance; freight management; transportation and traffic
- Manage, coordinate and directly supervise employees including coaching, counseling, performance reviews and feedback/initiating corrective action as needed, in a timely fashion
- Collaborate with other area supervision and Human Resources in ensuring consistency in situations requiring corrective action with employees
- Provide leadership and support to warehouse supervisors and non-exempt warehouse personnel in solving technical problems or contacting other resources as appropriate to solve problems
- Ensure compliance of local, state and federal regulations and guidelines (e.g., Good Manufacturing Practices (CGMP), Occupational Safety and Health Administration (OSHA), Environmental Protection Agency (EPA), etc.)
- Ensure SOPs for areas of responsibility are updated, accurate, and complete
- Ensure formal and informal training occurs in employee technical skill development as well as other training initiatives including safety, CGMP, teamwork, etc
- Support the Cleveland Site Management Team in the timely completion of assigned projects, including participating in Operational Excellence initiatives and procedures of the Warehouse
- Participate in cost reduction programs with respect to waste and other inefficiencies
- Perform other supervision duties and responsibilities as assigned
- B.S. or B.A. degree in a science or management discipline and at least four (4) years of warehouse and supervisory experience in a government regulated industry using standard procedures (FDA, pharmaceutical industry preferred), or Master's degree plus two (2) years of warehouse and supervisory experience in a government regulated industry or PhD plus one (1) year of experience
- Strong personal computer skills including experience with windows environment and Microsoft WORD
- Demonstrates ability to communicate positively with personnel at all levels
- Demonstrates ability to collaborate with others in cross functional settings
- Proven organizational, analytical and problem solving skills are required to appropriately balance short-term business demands
- Demonstrates ability to provide developmental opportunities to subordinates and provide constructive feedback in a timely fashion
- Knowledge of Excel and Enterprise operating systems (i.e. SAP, MES)
- Establishes operational procedures for activities such as verification of incoming and outgoing materialss, handling and disposition of materials, and keeping warehouse inventory current
- Ensures products or supplies are shipped, distributed, or received in an efficient manner
- Reviews MRP, Inventory, Schedule changes, Usage vs future needs
- Manage inventory to provide more efficient warehouse flow and ensure accurate receiving and order filling processes. Supervise and coordinate the annual physical inventory counting and recording
- Manage warehouse personnel and their activity, including recruiting, hiring, terminating, reviewing performance and coaching employees
- Assist Operations Manager with development of warehouse budget and routinely analyze and control expenditures to meet budget requirements
- Serve as Primary contact between warehouse operation and other managers. Communicate with customers and company personnel to resolve customer problems and expedite customer deliveries when necessary
- Evaluate shipping and delivery via common carriers; perform cost analyses and negotiate pricing for shipping services and common carriers. Evaluate and negotiate pricing for warehouse equipment, maintenance contracts, packing supplies and other warehousing expenses
- Participate in seminars and training classes to enhance and maintain necessary business knowledge
- Supervises a staff of 7 to 30 people and carries out supervisory responsibilities in accordance with the organization's policies and applicable laws. Responsibilities include interviewing, hiring, and training employees; planning, assigning, and directing work; appraising performance; rewarding and disciplining employees; addressing complaints and resolving problems
- Proficient in MS Office applications, especially MS Excel
- 3-5 years leadership experience
- Greenbelt Certification
- Bachelor's Degree in Supply Chain or Business is preferred
- Establish operational procedures for activities such as verification of incoming and outgoing shipments, handling and disposition of materials, and keeping warehouse inventory current, keeping all floor, shelving and racks clean and organized. Keep all overstock put away weekly
- Inspect physical condition of warehouse and equipment. Prepare work order for repairs and requisitions for replacement of equipment
- Confer with department heads to ensure coordination of warehouse activities with activities of other functions such as production, sales, records control, and purchasing
- Direct salvage of damaged or used material
- Participate in planning personnel safety and plant protection activities
- Count, weigh or measure items in incoming and outgoing shipments to verify information against bills of lading, invoices, orders and other records
- Assist in monthly cycle counts
- Assist in annual inventory
- Six months' experience in warehouse and inventory operations
- Valid driver's license and insurability
- Able to work in a fast and dynamic environment with a high emphasis on achieving results
- Excellent communication, technical, organizational, leadership, and mentoring skills
- Team player prepared to lead, work in, and embrace a team-based culture
- Demonstrated understanding of business drivers, customer needs and multi-site dynamics to create viable strategic plans
- Must possess strong ability to negotiate and influence others internally and externally
- Capital budgeting experience is required
- Lead, coach, mentor, motivate and inspire direct reports to achieve an optimum level of performance by consistently demonstrating role model behavior in all that is said and done
- Plans and directs Warehouse activities and establish priorities in keeping with safe, effective and efficient operations and cost factors, while ensuring inventory accuracy and timeliness
- Work with industrial engineering and management personnel to establish productivity and quality standards
- Set goals for employees and motivate Warehouse personnel to achieve their goals
- Work with the supervisors to develop a safety culture with zero incidents/accidents
- Conduct 5S audits. Ensure 5S audit actions are addressed in a timely manner and are effective
- Ensure employees know and understand customer and quality requirements and standards
- Set the quality direction to meet/exceed customer requirements in a cost effective manner
- Maintain employee awareness and adherence to ISO standards and procedures. Ensure the Quality Policy and objectives are understood and enacted
- Ensure process corrective actions are addressed in a timely manner and are effective, including conducting audits of effectiveness
- Provide leadership in identifying, developing, and implementing process improvements in the Warehouse
- Ensure that equipment is maintained and operated in a safe manner
- Evaluate and provide training as needed, setting in place a long-term training strategy
- Track employee progress and evaluate as needed
- Conduct annual performance reviews for direct reports in a timely manner. Recommend increases in compensation in accordance with pre-determined guidelines
- Participate in the annual Management Resource Planning (MRP) process. Prepare, communicate and maintain career development plans for all direct reports
- Compile, distribute, evaluate, and action Warehouse metrics
- With inventory control personnel, conducts cycle counts and physical inventory activities as required
- Works with inter and intra department personnel to ensure inventory accuracy, and to ensure effective corrective actions put in place to correct inventory accuracy deficiencies
- Participate in and satisfactorily complete all training seminars and related programs required of the assigned position
- Trains associates in warehouse procedures including WMS/ IT systems, safety procedures, and material handling equipment
- Develops and ensures that KPIs meet both DC objectives and customer requirements by measuring compliance to KPIs and implementing corrective actions to achieve required results
- Publish and communicate KPI results to both associates and facility leadership
- Identifies and improves warehouse distribution processes to support annual plan initiatives and customer requirements
- Develops talent to maximize individual, team and organizational effectiveness and measures against performance management objectives
- To supervise warehouse operatives
- To ensure that all despatches to customers (both export and UK) are undertaken on time
- To ensure that the correct quantities are despatched and that product is correctly packed and labelled
- To control all incoming components into the site, ensuring Goods Received Notes are raised within 30 minutes - all stock correctly located within the Warehouse
- To ensure the MRP system is accurately maintained in terms of stock quantity and location (cycle counting, etc.)
- To ensure that the housekeeping is of the highest standard and all aisles are free of materials / finished goods
- To ensure all items returned from Assembly are “booked” correctly against each WP or PC and returned to stock
- To produce weekly data relating to Warehouse performance
- Analyse and report on weekly Work In Progress variances
- To arrange appropriate transport
- To ensure all activities are conducted in a safe manner and that all equipment and racking is regularly checked and complies with Safety Legislation
- To be responsible for ensuring that the company procedures for Stock Taking re applied and that cyclical stock checks are conducted 40 times per year
- To advise Customer Services Manager of any risk which may result in a customer delivery not meeting the original schedules promise date
- A minimum of 10 years’ experience within a warehouse/logistics/supply chain environment
- Proven leadership and people management experience
- Basic Health & Safety awareness, understanding of COSHH / Risk Assessments
- MRP II experience
- Strong Excel and data analysis skills
- Management of projects such as
- Warehouse Design
- Distribution Network Redesign
- High Performance Logistics
- Customer Logistics
- Adapted LEAN concepts as part of your way of work
- Familiar with the Continuous Improvement and Problem Solving methodologies
- Delivers the financial and service (incl. quality) and HSE targets regarding warehousing activities
- Develops and implements projects innovating the site logistics processes (increase service, decrease costs, with a focus on warehousing)
- Designs and develops management information reports for cost information, savings, productivity and customer claims. Analyzes reports and takes action as required
- Establishes budgets for departments supervised and implements controls necessary to keep expenditures within budgetary limitations
- Accounts for proper allocation of man hours
- Ensures all site safety rules are strictly followed to that no injuries occur
- Is familiar and complies with all the applicable corporate as well as site and laboratory policies/procedures with regard to personal conduct, HSE and Product Safety & Regulatory Affairs (PSRA) standards
- Inspires commitment to AkzoNobel’s purpose, vision, strategy, core principles, values and leadership behaviors
- Acts as an ambassador and creates an open environment in which the team as a whole and its members individually can perform at their best
- Stimulates, manages and follows through on employee engagement and builds on the workforce to reflect the societies and markets in which we do business (D&I)
- Ensures that job profiles are in place, sets objectives for team members, reviews development and provides clear, open and constructive feedback on performance combined with the appropriate actions
- Strengthens the talent pipeline by developing talent and regularly assesses and discusses talent and internal movement. Continuously monitors and evaluates retention risk
- Ensures reporting line is fully informed and acts in line with HSE and Compliance regulations
- Manages and plans relevant budgets and proactively manages costs
- Reports on progress on a continuous base
- EH&S: Develop and drive a culture of continuous improvement in the area of EH&S relating to Warehouse/Shipping staff
- People: Providing management & leadership to staff in the areas of pperformance management and training and development plans
- Quality: Manage, develop & ensure compliance to all regulatory and quality procedures & systems including ensuring all SOPs and Work Instructions accurately reflects the process and are up to date
- Service: Maintain high quality service levels to internal & external customers ensuring achievement of OTIF targets
- TEOA: Provide leadership in the roll-out for Warehouse and Shipping functions
- Resources: Optimise the use of personnel and resources in meeting demanding service levels to support changing business needs
- Inventory control: Implement robust inventory management control processes and procedures targeting best in class inventory accuracy
- Cost Management: Ensure effective management of all associated costs including labour, freight, inventory write-offs, external warehousing providers
- Systems: Support the rollout of SAP ERP across the site
- Trade Compliance: Ensure compliance to all customs and related trade regulatory requirements
- Supervises a team of individual contributors with functional responsibility for performing ongoing receiving, put-away, picking, kitting, replenishment route running, inventory control and/or packing duties
- Schedules discrete work activities and assignments, efficiently allocates available resources for shift coverage and coordinates operating coverage plans with other departments
- Anticipates opportunities for development of self and staff. Develops talent development plans in conjunction with Human Resources and other functional groups as needed
- Develops and maintains all policies and procedures that are specific to plant warehousing. Ensures such policies and procedures as designated for warehousing are followed safely, accurately and efficiently
- Works and communicates directly with Finance and functional management to develop and meet operational budgets for headcount, depreciation and cost center spending
- Manage and effectively executes exception activities as required by warehouse function (e.g. processing of urgent material receipts, inventory purges, rapid replenishment of short materials to manufacturing work center(s) etc.)
- Actively benchmarks and leverages lean oriented tools such 5S and Six Sigma to eliminate waste and help error proof transitional work
- Owns management of workforce capacity and material space requirements planning processes. Responsible for developing 1-3 year operating models for the warehouse and inventory control functions
- Management of operations and resourcing necessary to support satellite warehouse locations
- 10 + years of experience working in a warehouse environment associated with a production facility
- Experience in leveraging lean process tools such as Six Sigma and 5S
- APICS CPIM and/or CSCP certification
- Skilled in MS Office suite, WMS, Access and/or SQL database experience
- 2-4 years of experience in shipping-receiving, stockroom, and use of computer inventory control systems
- Managerial experience
- 1-2 years of general maintenance experience or applicable work experience
- Strong prioritization skills
- Ability to complete multiple duties with accuracy shifting from one to another with frequent interruptions and competing deadlines
- Ability to work independently and prioritize duties with minimal supervision, in order to meet deadlines
- Apply high energy, self motivation and initiative to learn and be trained on various types of equipment and maintenance techniques, to include resin and spray equipment, HVAC, plumbing, PLCs, VFDs, etc
- Daily job duties will be varied and dynamic, requiring high levels of customer service and attention to detail
- Workload will be tracked via daily schedules and assignments requiring responsibility and accountability for quality and timeliness of completion
- Compliance to safety policies and procedures is required, as well as identifying risks and hazards prior to job completion
- Requires high foot travel and working throughout the facility. Lifting overhead within prescribed safety limitations. Working at heights: ladders, rooftops, booms and lifts, work platforms, etc. Working outside in all possible weather conditions. Overall good physical condition and agility
- Work hours: typically 4 days per week at 10 hours per day, 3:00 PM to 1:30 AM daily, but times will be adjusted as demands require. Weekend work is scheduled according to workload and as repair needs dictate
- Two year technical degree or equivalent
- A minimum of 3-5 years facility maintenance experience preferred
- Documented work experience in: CNC programming and diagnostics; HVAC; electrical and maintenance experience
- Strong mechanical and electrical background and experience, with experience in electrical motor controls and ladder logic programming
- Experience reading blueprints and schematics and building to specifications
- Ability to fabricate and order materials for open work orders and jobs
- Requires one to three years of substantive experience in one or more of the skilled trades areas (mechanical, electrical, fabrication) and high school diploma/GED
- Will be required to be certified in fork lift and high lift (genie boom) operations and operate other equipment such as yard tractor, EPJ, articulating lift, pick-up
- Requires ability to use a wide variety of hand tools, powered and manual
- Ability to read measurement devices, including OHM/voltage meters, measuring tapes, calipers, various equipment gauges as required
- Good safety awareness, attitude, and attendance. Self-starter and a team player
- Knowledge of 5S, Kaizen and LSS a plus
- Physical requirements include: working at heights on booms, lifts and platforms, lifting parts and pieces up to 50 lbs, traveling up and down stairs on a constant basis, sitting, squatting and bending in various awkward positions for certain lengths of time - including working overhead, traveling in and out of work areas, walking and being on your feet for a majority of the work day, etc
- Working closely with transport to plan delivery and dispatch
- Managing warehouse layouts and restructuring when needed
- Updating and amending K8 WMS locations and virtual warehouse structure
- Being involved in the rotas, recruitment, employee training and appraisals for warehouse colleagues
- Ensuring stock is stored correctly and safely
- Measuring and monitoring pick accuracy, damage and write offs
- Responsible for the daily management of Health and Safety, employee welfare and ensuring safety in all operational areas
- Organizes, directs and supervises the work of warehouse employees and purchasing employees
- Ensures the warehouse storage areas are organized according to Lean 5S and Safety principals
- Ensures receipts are properly entered into warehouse supply system
- Maintains and executes materials management programs
- Operates fork-lifts to stack and retrieve supplies and materials
- Documents and maintains inventory and ensures production area organization and cleanliness. Ensure that the team tracks and organizes equipment and material
- Has knowledge of commonly-used concepts, practices, and procedures within a particular field. Relies on instructions and pre-established guidelines to perform the functions of the job
- Effectively assist in and lead in the creation, implementation, maintenance and improvement of materials management systems
- Work closely with production manager and supervisors to eliminate wasteful spend, moves to just in time purchasing, and analyses trends to spot opportunities for improvement and implement solutions
- Interacts with vendors and suppliers to negotiate improvements in cost and vendor performance, manages purchasing responsibilities, assists with forecasting and cycle counts as needed
- Secures warehouse appropriately
- Protect the Company’s investment in tools and equipment
- Develop and promote a safe, positive, and efficient work environment
- Lead the LEAN initiatives to support creating efficiencies in the work environment
- Develop and maintain relationships with other managers and departments to support a cohesive team environment to serve the customer
- Computer skills including Microsoft Office, especially with proficiency with EXCEL spreadsheets
- Prior experience implementing LEAN projects and other efficiency related methodologies
- Track record of improving safety and safety procedures
- Excellent abilities to prioritize and adjust schedules and instill a sense of urgency in team members while managing multiple projects
- Aggressive, high-energy, can-do, get-results person with high integrity
- Computer literate with computer skills in MS Office
- Prior experience in related work required
- Prior experience of at least 5 years in the warehouse/construction industry with an understanding of warehouse practices and procedures
- Demonstrated ability to coach and counsel other workers in a positive manner
- Bilingual (English and Spanish) speaking and writing preferred
- Experience as Manager or manager in related field or general business
- Maintain all aspects of equipment according to company standards
- Report to the Service Manager and will be assigned duties on a daily basis
- Maintain availability for after-hours service calls and be available for an open work schedule
- Maintain and inventory the supplied tools for the work required in maintaining diesel engine trucks and associated equipment
- Utilize various diagnostic equipment to determine malfunction and utilize available technical information to determine and perform correct repair procedure
- Diagnosis, removal and replacement of injectors, pistons, liners, cam shafts, cylinder heads, rod and main bearings, oil pans, clutches, fan hubs, differentials, fifth wheels, brakes, changes or recharges batteries, and replaces transmissions and other parts
- Perform all necessary diagnostic and documentation functions on the company computer system
- Perform preventative maintenance work as requested
- Document and submit necessary paperwork or enter into mobile service program as work performed in an accurate and timely manner
- Respond to customer inquiries regarding the work. Foster positive customer relations
- Advise customer and/or service writer of any repairs or services which should be performed within the next 3 months
- Have a current and valid CDL and Medical card as required by the FMVS
- Mechanical aptitude and technical ability is a must
- Ensure forklifts, plumbing scales, security system and fire alarms remain operational
- Complete inventory of all material and storage units on a monthly basis
- Ensure warehouse meets RSMO and MTO guidelines
- Charge and keep track of weight tickets for office and public use
- Assist in loading and unloading shipments when necessary
- Achieve or exceed projected labor and productivity goals and objectives in accordance with established policies and operational procedures. Offer recommendations for improved control or changes
- Responsible for all departmental warehouse operations; productivity, daily tasks, employee performance, safety, sanitation and facility conditions etc.as assigned by the Warehouse Manager
- Directly supervise all shift management and supervisory staff. Identify and provide development opportunities for personnel interested in future supervisory and management opportunities
- Oversee the set-up and execution of labor needed to accomplish shift operations Direct supervisors to ensure the assignment of job responsibilities are performed based on employee’s seniority and job qualifications while providing employees the ability to meet company productivity standards. Oversee the reassignment of job responsibilities, scheduling of overtime hours, and address productivity issues as they arise
- Monitor the stacking of product and the order selecting process daily, identify and address issues affecting pallet height, product combinations, order breaks and ability to meet company productivity standards. Review staged outbound shipments for stability, labeling, etc
- Oversee the loading of product. Direct supervisors to ensure loads consistently meet established guidelines such as delivery sequence, weight distribution on axle groups and product integrity
- Apply sound communication and motivational techniques in leading, coaching and developing employees. Requires consistency and follow-through of performance and employee related issues. Document substandard performance and take corrective action including formal discipline and termination when necessary
- Ensure the training and certification for employees given specialized job assignments such as receiving, loading, or operation of power equipment. Ensure the proper documentation and maintenance of qualifications list of job responsibilities as well as training and certification records in employee files
- Set an example of personal integrity, appearance and ethical business practices which provides a standard of conduct for all warehouse personnel
- Communicate directly with the Buying Department; ensure timely handling of recalls, inventory shortages/overages, processing of purchase orders and other issues as they arise
- Conduct daily facility tours to make observations and reinforce desired behaviors and processes
- Ensure compliance with applicable local, state, or federal requirements governing cleanliness, food storage safety and pest control standards, i.e.: a state or federal product recall
- Interpret and apply the terms of collective bargaining agreements, company working conditions and wage agreements and company personnel policies as the established guidelines to be adhered to and followed by all employees and appropriately apply to the daily operation of the warehouse
- Ensure records and reports regarding warehouse activities are prepared on a timely basis and effectively maintained. Calculate and input operational data such as labor hours and job codes to summarize productivity and payroll. Utilize reports to assist with meeting operating goals
- Ensure compliance of safety standards are maintained and adhered to consistently. Address potential safety hazards quickly. Possess an understanding of ammonia and fire systems; coordinate emergency evacuations; communicate with outside emergency response teams
- Keep warehouse neat and well organized; through facility tours, and application of company policies such as “clean as you go”
- Conduct employee observations to ensure safety guidelines are being met consistently, address unsafe behaviors immediately. Investigate all reported employee injuries and reported collisions or incidents; identify causes and determine preventative measures that could be taken, address accordingly
- Perform other duties as needed or assigned
- At least 4 (four) years of progressive supervisory experience in a Distribution Center environment
- Demonstrating skills in leadership, organization and communication
- Demonstrating strong analytical and problem-solving skills with strong attention to detail in order to effectively monitor progress and complete assignments
- Demonstrating knowledge of host, PC and internet-based software applications including Microsoft Office software; (Word, Excel, Outlook, etc.)
- Utilizing strong proficiency with numerical data and calculations
- Demonstrating working knowledge of Microsoft Office software (Word, Excel, Outlook, etc.)
- Apply working knowledge of material handling principals, practices and standards of warehousing
- Apply working knowledge of employment law and employee relations to workplace situations including discipline and attendance
- Understand with mental alertness overall company warehousing practices, in-depth understanding of policies/procedures and the ability to judge/react to shift operation needs
- Utilize excellent verbal, written and inter-personal communication skills
- Demonstrate initiative, self direction, and possess excellent time management skills
- Work in a team-oriented, collaborative environment and develop a strong rapport with others
- Utilize strong proficiency with numerical data and calculations
- Confidently and effectively handle confrontations with difficult individuals
- Maintain a high degree of confidentiality with sensitive information
- Understand and accurately apply collective bargaining agreements, company working condition and wage agreements and union contracts with employees and daily operation appropriately
- Possess knowledge of host, PC and internet-based software applications including Microsoft Office software; (Word, Excel, Outlook, etc.)
- Stand and walk for long periods of time
- College degree or substantial responsible experience and 4 (four) or more years in a Warehouse Distribution preferred
- Oversee all aspects of warehouse operations including budget management, staffing, inventory control, distribution of product, and safety compliance
- Manager interacts directly with customers in a sales capacity, and must ensure excellent customer satisfaction
- Review warehouse performance metrics on an ongoing basis and proactively develop and implement improvement measures, using Lean and Six Sigma principles
- At least 2 years of experience with Customer Sales or related field
- At least 2 years of experience in warehouse management and employee supervision are required
- 2 or 4 year degree in business, distribution or related field
- Experience in lean or six sigma principles is highly desirable
- Ability to work under pressure and with minimum supervision
- Ability to lead a team to produce positive results. Must have the ability to lead and motivate a small warehouse/driver team
- Strong oral and written communications skills
- A U.S. driver's license with an excellent DMV record is required. Qualifications desired
- Responsible for achieving financial objectives by managing the fixed and variable Warehouse and Shipping budgets. Annual department budget dollars of approximately $10M
- Position is responsible for developing and maintaining all processes and procedures that will maintain product integrity and facilitate an efficient operation for an average of 2.7M - 3 M cases per month valued between $149,000,000 - $170,000,000
- This position will manage all Warehousing, Distribution and Shipping functions; it will directly manage four Band 5 employees and oversee 50+ Band 7 unionized employees
- Development and execution of Warehouse strategy, both short and long term
- Work is close and in partnership with other Area Manager(s) to drive consistent best practice in regards to people and processes
- Implement any necessary systems, processes or procedures to increase efficiency while maintaining minimal inventory loss
- Lead the ‘Move’ portion of the Manufacturing Management System (MMS)
- Safety = Zero Harm. Own & maintain safety improvement plans. Leverage the SIRC process maximizing safety mitigation and ensuring ZERO harm
- Schedule adherence > 95%. Ensure highest standard of reliable delivery building Diageo’s reputation as a great partner and enabling optimal in market inventory
- Super engaged > 75%. Believe wholeheartedly that super employee engagement enables all the above. Always seek out creative ways to engage with your most valuable asset
- Good Manufacturing Procedures (GMP). Perform tasks per the Master Sanitation Schedule (MSS) and follow general housekeeping guidelines and rules for Food Safety Regulations. Keep area updated with 5S
- Be innovative. Generate ideas to improve area of responsibility, communicating these ideas to appropriate personnel
- Responsible for inventory control, monthly destruction reporting and monthly shipping affidavits
- Third Party Logistics: Ensure daily service levels are met & responsible for maintaining relationships with local trucking & warehousing providers
- Responsible for inbound material pallets & dunnage inventory
- BA/BS in Business Management, five plus years of leadership experience in fast paced and high volume warehouse environment; or equivalent combination of education and experience
- Proven track record of leading a team
- Strong analytical and budgeting skills
- Computer literate – Intermediate Excel and Word /SAP experience
- Excellent organization skills. Ability to handle multiple priorities, prioritize effectively, and manage time
- BS Degree in Logistics/Business Administration or related plus 2 years Logistics supervisory experience. “or”
- High School graduate or equivalent with 4 years progressive warehouse management responsibility including 1 year supervisory experience. “or”
- One year minimum as TWW Working Supervisor or TWW Inside Sales Representative (I or II) with one year previous supervisory experience
- Interpersonal communication
- Knowledge of company software
- Conflict management skills
- Knowledge of government regulations as it applies to moving
- Required: High School diploma or GED
- Required: 5-7 years of related experience
- Supervise day-to-day activities of the associates in Material Stores, Shipping and Receiving
- Responsible for establishing work plans and schedules for assigned areas that will achieve goals for internal schedules, program deliveries and product quality
- Possess a working knowledge of freight shipping options, bill of lading (BOL) etc..,
- Understand and uphold security requirements pertinent to assigned areas of responsibility
- Develop and foster a mindset that focuses on continuous improvement activities, root cause investigation and countermeasure development
- Ensure all tools and equipment used in Receiving / Shipping / Material Stores areas meet safety standards and are maintained accordingly
- Maintain area productivity goals and oversee the processes to keep them on track to meet or exceed the goals
- Support an open environment for cost reduction opportunities within area
- Support the Operations group and its objectives including the development and implementation of development and cross training plans
- Monitor resources regularly in order to prevent budget over runs and schedule delays
- Provide regular feedback to operations manager regarding problems and progress
- Participate in shipping meetings and provide status of shipments, ensuring movement of items through the shipping process
- Able to lift 25+ lbs if needed
- Solid understanding of warehousing and logistics operations
- Ability to work independently in a fast pace environment
- Strong management and leadership skills
- Intermediate to Advanced knowledge of MS Excel
- Bachelor’s Degree in Logistics Manager or Chain Supply Management
- Clean and maintain the warehouse
- Manage warehouse staff
- Manage all deliveries, warehouse inventory, and tooling
- Create job kits for large projects as well as a process for managing them
- Upon job completion, pull all tooling off the job and inventory
- Create tech kits for service techs and create process for managing
- Create and manage an install team that would prefab fiber and copper for bigger Data Center installs
- Go through all storage cages and create a data base of info and process for removal of unused inventory
- Other responsibilities as assigned
- Must possess a minimum of three (3) years supervisory or managerial experience
- Must have general accounting knowledge
- Must be able to work at heights, off of a ladder and in confined spaces, lift up to 50 pounds and move up to 75 pounds
- Must have general computer skills and be proficient with Microsoft Office (Word, Excel )
- Must meet Company minimum driving standards
- Employee will comply with all Johnson Matthey Hazardous Waste procedures and local, state and federal regulatory requirements
- Will ensure the warehouse complies with all Johnson Matthey Hazardous Waste procedures and local, state and federal regulatory requirements
- Supervises daily operations of the warehouse, including all aspects of shipping, receiving, material storage & accountability
- Ensure finished goods scheduled shipment to customer meet identified customer-specific requirements. Use all JM and customer-required automated systems as needed
- Coordinate with internal departments as required to fulfill customer orders. Ensure defect free product is supplied to all Customers
- Responsible for receipt and shipment of all non-precious metal raw materials stored at the Warehouse. Ensure Quality-approved materials are delivered as requested to support Production operations
- Has direct responsibility for the work efforts and procedural adherence for all JM staff and contracted labor at the Warehouse. Train and supervise performance of all staff members, and ensure all JM personnel policies are complied with
- Ensure the warehouse team is proficient in using all automated systems, including scanning equipment and material handling equipment
- Supervise operation and maintenance of a forklift fleet; ensure daily inspections are conducted; coordinate required maintenance with outside contractor
- Ensure that ECT practices and policies (quality, safety, environment, etc) are followed as an extension of JM Wayne
- Perform or assist with physical inventories on a monthly, semi-annual and/or annual basis. Will ensure all inventory control systems are reconciled to reflect the accurate status of all finished goods lots
- Comply with all federal, state, and local environmental, health, and safety regulations and requirements
- Comply with company policies
- College degree in relevant field required
- Experience in shipping, receiving, inventory control and domestic / international traffic procedures required
- Industrial experience and awareness of general safety and OSHA requirements highly desired
- Experience with automated inventory control, shipping, and scanning systems required
- Supervisory and cost center management experience highly desired
- Training in personnel supervision and team management desired
- Develop the needed competencies within warehouse and operations support to secure
- Proven leadership and success in building teams and motivating people
- 5+ years experience leading people
- Proven knowledge and working experience in managerial function (preferably in warehouse operations and logistics)
- Being an ambassador for IKEA culture and values both internally and externally
- Has proven and demonstrated competence/understanding of IKEA Warehousing concepts and processes to increase efficiency
- Microsoft tools (Word, Excel, Power Point, etc…)
- University degree in Logistics/Engineering and/or 4 to 6 years working experience in a management position (preferable in distribution , operations/systems and DC unit level manager experience)
- Fluent in English, both written and spoken
- Analyze and report operational performance matrix and KPI’s
- Completes operational requirements by scheduling and assigning employees effectively with appropriate follow up
- Maintains compliance with safety guidelines, reports discrepancies and recommends corrective action
- Promotes staff development through performance appraisals and succession planning in coordination with Human Resources
- Implements continuous improvement processes and receptive to a changing environment
- Ensures that the operational staff is adequately trained and proper documentation is available and consistent with quality systems requirements
- Controls operational performance by reviewing data recorded in Oracle’s system and other tools, retrieving the data, designing reports and directing corrective action
- BS degree in logistics, supply chain management or 10 years equivalent experience
- Proven work experience as a warehouse manager with previous team of 60 plus employees
- Solid problem solving skills with the ability to organize and multi-task
- Excellent PC skills (Microsoft Office and Oracle)
- Leadership skills and ability to manage staff
- Evaluation of fork lift operator performance
- Strong knowledge of warehousing Key Performance Indicators (KPI’s)
- Independently manage large projects
- Follow and maintain all safety requirements
- Establish and deliver Warehouse performance targets for receiving, order fulfillment, customer service, shipping, and inventory control that represent the highest levels of safety, task efficiency, and service reliability
- Ensure the Warehouse team is involved in collecting, analyzing, and reporting data in each of these areas on a regular basis
- Develop, present, and execute the annual Warehouse Operating Plan that supports the macro targets for the Region
- Lead and motivate a three shift distribution center operation with up to 50 Warehouse Team Members
- Develop and work within the DC Budget of MM controllable expenses (i.e. labor, supplies, freight, and material damages) to achieve operational goals
- Lead in a manner that encourages engagement and develops the Nestle Continuous Excellence System (NCE)
- Provide training, motivation, and performance feedback to Warehouse team members
- Desire to improve distribution process and manage multiple tasks/projects
- Support company DSD routes by developing relationship sales partners
- Identify, justify, and execute the capital investment plan to support the DC operation
- Ensure inventory integrity and work with Corporate Logistics and Sales to minimize inventory variances, improve product freshness, and minimize inventory salvage
- Manage direct reports as a team establishing common objectives with joint accountability among team members including management and administrative staff
- Develop, present, and execute an annual Warehouse Plan that supports the macro targets for the Region. Also, responsible for monthly financial forecasting
- Minimum of 1 year warehouse experience
- Experienced with UPS shipping
- Performing cycle counts
- Responsible for all warehouse workers’ (material handlers and drivers)
- Ensures adherence to all company safety policies and procedures
- Responsible for new employee interviewing, selection and training of employees
- Responsible for training employees on the effective and safe use of equipment and machinery while adhering to Company’s safety policy and procedures
- Conducts employee reviews and makes pay rate or promotion requests to Branch Operations Manager
- Provide employee coaching/counseling while handling employee complaints and disciplining subordinates
- Responsible for overall maintenance of the Warehouse Operations Dashboard system to measure, monitor, evaluate and report on warehouse performance to goal while being responsible for delivery performance to meet Company productivity goals
- Overall responsibility for transportation logistics including scheduling of deliveries, establishing delivery routes, and selecting the most appropriate method for delivery to meet customer service objectives while utilizing company owned vehicles and drivers, parcel carriers (UPS and Fedex) and LTL carriers as required to meet customer service objectives and minimize total delivery costs
- Tracks customer complaints, questions and inventory problems presented by branch personnel
- Inspects physical condition of warehouse and equipment, prepares work order for repairs and requisitions for replacement of equipment
- Confers with department heads to ensure coordination of warehouse activities with activities of other functions such as production, sales, and purchasing
- Organizes annual inventory counts for assigned area/division
- Knowledge of shipping/receiving practices, policies and techniques
- Knowledge of merchandise handling and production methods
- Knowledge of supervisory practices and principles
- Skill in establishing and maintaining effective working relationships
- O 2 – 5 years Supervisory experience
- Oversees the shipping and receiving activities to ensure accuracy, completeness and quality of the incoming and outgoing shipments
- Ensure the correct procedures are in place and being followed and that employees are maintaining a high level of quality of the shipments and shipping on time
- Provide Leadership, training and coaching for employees when procedures or standard work is not being followed. Hold individuals accountable
- Pursue continuous process improvement practices (LEAN). Review work procedures and operational problems in order to determine ways to improve service, performance and/or safety
- Schedule, assign duties and track employee attendance
- Work closely with other departments to maximize warehouse labor costs
- Work with contracted freight companies to maximize profitability in shipping costs
- Maintain a safe work area and enforce all safety policies, including GMP/SOP’s
- Direct Delivery Driver in driving route and delivery route
- Investigate and resolve shipping errors when they occur
- Communicate bottle necks and potential shipping issues with Manager
- Responsible for effectively utilizing staff and supplies to maintain budget
- Responsible for maintaining Inventory accuracy, establish a cycle count program
- Run all daily and weekly reports, investigate and resolve any issues
- Responsible for year-end physical inventory
- Establish a KPI program in order to measure warehouse efficiency
- Manage inventory levels in order to reduce shrink (expired product)
- Meets deadlines, follows through on commitments and delivers on promises
- Able to take broad thinking around business issues and apply to departments strategies
- Strives for continuous growth and improvement
- Self starter that is resourceful and can work autonomously
- Ability to grasp medium complex concepts easily
- Able to motivate co-workers, colleagues and others
- Any other assigned duties by manager
- 5+ years experience managing in a warehouse/distribution environment
- Manufacturing background a plus
- Analytical skills to problem solve, investigate and improve procedures
- 2+ years working in the logistics field
- Microsoft office (excel-word)
- JDE experience a plus
- Responsible for daily operation tin the warehouse o strive for excellence
- Responsible to increase efficiency of warehouse operations to reduce cost, improve productivity and work spirit with total supply chain
- Ensures adherence of all safety requirements and proper training across their function
- You hold a degree in logistics, business administration, or in a related field,
- You have very good verbal and writing skills in Czech and English,
- You’re willing and able to work to flexible schedules and shifts: you always commit the time required to get the job done
- Bachelor’s degree in Industrial Engineering
- Advanced level of English
- Advanced organizational skills
- Open communicator
- Knowledge about Health & Safety
- Good knowledge & usage of Microsoft Office programs
- SAP knowledge would be preferable
- No restriction for travelling
- Oversee all Shipping, Receiving, Inventory Management and Control for facility
- Ensuring inventory transactions (shipping, receiving, moves or transfers) are accurately logged in Oracle
- Oversees cycle counts and reconciliation
- Responsible for the efficient layout and use of warehouse space, including designating row-rack-bin strategies
- Manages staff Forklift drivers on a daily basis. Communicates work schedules and verifies that employees have appropriate work instructions to successfully execute daily tasks
- Ensure employees are trained and certified on proper safe operation of equipment
- Ensure accuracy of shipment and supporting documentation
- Oversee receiving incoming materials to ensure accuracy of documentation
- Works with management to ensure effective organizational design and that roles are correctly organized, defined, documented and communicated to all employees
- Ensures effective safety procedures, tools and record keeping are managed through site leadership
- Adheres to company GMP’s (good manufacturing practices), safety procedures and all other quality processes
- Wear PPE (Personal Protective Equipment) when required
- All Warehouse staff
- Five to ten years of related experience and/or training; or equivalent combination of education and experience. Manufacturing environment experience required
- Candidate must possess a strong working knowledge of shipping, receiving and inventory management
- Knowledge of Lean Manufacturing practices is beneficial
- Outstanding verbal, written, multi-tasking and presentation skills
- Ability to create momentum and foster organizational change
- Bilingual in Spanish is beneficial
- Must have a working knowledge of MS Word and MS PowerPoint software, and be proficient with MS Excel software. Experience with Oracle is beneficial
- Directs supervisors in managing the warehouse and assure the most efficient receiving and loading schedule that satisfies customer delivery needs while ensuring the lowest total distribution cost per case
- Develop and implement policies and procedures that increase efficiencies of the department that meet or exceed customer expectations, resulting in high customer service ratings
- Interview, select, and train warehouse supervisors
- Provide effective leadership and demonstrate managerial courage while maintaining good rapport with colleagues. Ability to maintain and rally a team
- Collaborate with peers to drive improvements in department/center performance against key metrics
- Support and encourage an open-door policy to ensure open lines of communication with colleagues and respond to colleague issues or questions in a timely manner
- Uncover, prioritize and eliminate issues at an operational and tactical level
- Keep up with the latest in warehouse techniques and operating methods
- Ensure colleagues follow all Blue Line policies and procedures in order to meet safety goals and guarantee that delivery schedules are consistently met
- Coach and develop warehouse supervisors, including conducting performance management reviews and progressive disciplinary steps as necessary
- Assists Director in obtaining an “excellent” rating from the LCE Quality Assurance Department as well as achieving outstanding ratings from internal and external inspections or audit agencies
- Ensures warehouse equipment and security systems are properly maintained and functioning according to OSHA standards
- Bachelor’s degree in Business Administration or related degree with minimum of five (5) years supervisory experience within the warehouse distribution industry, or equivalent of 8 years supervisory experience in the warehouse distribution industry
- Possesses a strong understanding of FDA and OSHA compliance requirements, company policies and all national and state regulations and the ability to enforce them
- Proficient in software applications such as Microsoft Word, Excel, PowerPoint, and Lotus Notes
- Proven ability to build and maintain effective relationships and communicate with executive leadership, staff, customers and vendors
- Prior experience forecasting and managing operating budgets as well as communicating variance
- Evidence of strong analytical skills with demonstrated ability to make sound business-based decisions
- Previous experience with developing and adhering to department metrics
- Evidence of ability to effectively work in a fast-paced environment, handling multiple concurrent priorities
- Trained on maintaining a non-union environment
- Managing the warehouse
- Managing the warehouse employees
- Organizing acceptance, rational placing, storage and delivery of material at the warehouse
- Preparing documentation
- Optimizing materials storage system
- Ensuring health and safety rules are fulfilled
- Carrying out all types of inventories
- Organizing warehouse personnel work
- Higher technical education
- 4+ years of similar work experience
- Experience in automotive industry
- Experience of managing 40+ employees, 2+ shifts
- Highly developed organizational skills
- Communicative skills
- People Management skills
- Result oriented personality
- Primarily responsible for managing the daily tasks of a 20+ staff, 2-shift warehouse operations and supervising of warehouse personnel and drivers
- Responsible for Shift Managers and Supervisors, reporting into the Logistics Manager
- Handles all aspects of inventory management, shipping, receiving and cycle counting
- Manages the loading and unloading of exterior products and establish delivery of these products to our customers
- Coordinating inventory and shipments to ensure deliveries correctly on time within and outside the Facility
- Improve goods receipt, goods issue processes physically and ERP-based
- Managing handover-takeover between Warehouse and Operation
- Material flow management in kanban, supermarket, kiting process
- Manage warehouse associate work schedules to minimize overtime
- Establishing product location and leading daily cycle counts for inventory accuracy
- Annual inventory count planning and execute
- Develop, train, coach and motivate the Shift Managers, Team Leaders and Operatives, in conjunction with the HR department and carry out annual performance reviews
- Waste management
- Bachelor’s degree in Logistics or equivalent
- Strong leadership and training skills as evidenced by previous activities or work experience
- Strong MS-Office (Excel) knowledge
- Ability to manage successfully under the pressure of deadlines and to accept new ways of doing business
- 3 – 5 years of previous warehouse experience
- Manage daily warehouse operations and service levels to assure accurate and timely end processing of customer orders
- Build, guide and develop an engaged, high performance warehouse team
- Organize products within the warehouse for optimal efficiency in assembling and loading customer orders with safety, precision and speed
- Inspect, protect and maintain company facilities, equipment, vehicles and all other assets
- Previous Warehouse experience
- Effective communicator
- Detail-oriented, strong multi-tasking, and organization skills
- Computer literate to track, analyze and manage business results
- Desire to go above and beyond the job description
- Manage a team of 2+ employees to meet departmental goals via appropriate allocation of workload and effective resource management
- Interview, select, train, mentor and develop new employees
- Oversee material transfer to other sites to include vendor issue resolution
- Establish and control handling and storage plans and procedures
- Streamline warehouse operating procedures by identifying and eliminating redundant processes
- 3+ years of relevant warehouse experience
- Develop and maintain operational plans to include all business requirements which include labor hours, production costs, KPI reporting, and meeting financial objectives
- Direct and oversee the work of the QRC team to meet all production goals of the product lines in the timeliest manner within two days or less
- Develop improvements in inventory handling processes in order to drive improvements in efficiency and accuracy in all aspects of physical goods flow and reducing lead times from dock arrival to stocking where needed
- Establish production and quality control standards, develop budget and cost controls and obtain data regarding business metrics
- Maintain customer service standards at agreed upon levels. Should aim for two hours order acknowledgement turnaround and 8 to 48 hours from order entry to delivery
- Provide guidance and development of SOP’s including personnel requirements, material needs and facility and equipment needs
- Ensures all established costs, quality and delivery commitments are met
- Coordinates activities with all other functions of the organization and suppliers to obtain optimum production and utilization of human resources, IT and equipment
- Reviews production and operating reports and directs the resolution of operational and customer service problems to ensure minimum costs and prevent operational delays
- Maintain inventory levels to achieve high customer satisfaction in balance with high inventory turns to optimize working capital
- Manage inventory through creating and maintaining an adequate cycle count program
- Responsible for financial analysis of the operational expenses
- Monitors the interviewing and hiring process and manages performance of employees
- Ensures all assigned employees are trained and aware of and comply with company, government and customer policies, procedures and regulations
- Determines responsibilities of assigned organization and staff positions to accomplish business objectives
- Assure safety levels are maintained at the highest levels. Investigate EHS compliance issues and work to resolve issues/mitigate risks
- Recommends improvements to reduce cost and drive productivity within the department while achieving site specific goals
- Ensure timely unloading, receiving, storage and delivery of material to the production areas
- Ensure shipping functions are performed safely and in accordance with established EHS procedures
- Oversee and review the accuracy of shipping documentation in accordance with all trade compliance regulations
- Implement and enforce standard work across the functions
- Drive continuous improvement activities in all functional areas
- Provide leadership in selecting, developing and evaluating personnel to ensure the efficient operation of the function
- Manage suppliers and service providers that support receiving, warehousing and shipping functions
- Organize activities & assigning jobs accordingly to the staff requirements
- Engages in the typical responsibilities of a manager requiring planning, evaluating, organizing, integrating and delegating
- Identify and implement cost reduction measures to drive operational efficiency
- Strong leadership skills, with excellent supervisory skills
- Minimum of 5 years experience as an operations or warehouse leader
- Experience in moving inbound and outbound freight and leveraging freight consolidation techniques
- Familiarity with Microsoft Office products and other shipping software
- Knowledge of inventory control processes
- Basic financial and accounting knowledge
- Ability to work under pressure with fluid deadlines and changing circumstances
- Must be able and willing to work in a manufacturing plant environment, including extended periods of time in noisy, dusty, non-air conditioned or unheated areas
- Ability to interface with, influence, and gain credibility across all levels
- Experience with the following software: Mopar, OneLisa, OPPS, BNSF/UP rail website and RailConnect
- Gypsum products manufacturing experience
- Ability to read and interpret documents such as safety rules, operating and maintenance instructions and procedure manuals. Ability to write routine reports and correspondence. Ability to speak effectively before groups of customers or associates of organization
- Ability to calculate figures and amounts such as discounts, interest, proportions, percentages, time calculations and area
- Ability to solve practical problems and deal with a variety of concrete variables in situations where only limited standardization exists. Ability to interpret a variety of instructions furnished in written oral, diagram or schedule form
- Ability to use a computer, copy machine, fax machine, telephone and calculator
- Ability to speak other languages is not required but is helpful
- Ability to work under deadline pressure and to prioritize work duties
- Ability to prepare clear written memos and reports to BOM and Human Resources
- Adhere to required MRC Safety Training policies and guidelines; providing safety training to warehouse personnel; ensuring safety measures are followed by all Warehouse personnel
- Assure proper maintenance and appearance of fleet and compliance with fleet safety and DOT regulations
- Inspect physical conditions of warehouse/pipe yard and equipment, and ordering testing, maintenance, repair, or replacement as necessary
- Maintain warehouse cleanliness in compliance with OSHA and safety policies
- Manage all warehouse duties including: shipping, receiving of materials, stocking, and pulling products for shipment; and all functions required for the pipe yard (if appropriate for the location)
- Coordinate communication between the warehouse and the sales office to assure efficient and timely deliveries
- Verify all incoming and outgoing shipments; ensuring that daily cycle counting and other inventory management functions are performed timely and thoroughly
- Oversee preparation and follow-up for Warehouse Assessment process
- Perform warehousing duties and emergency delivery runs to customers as required by the branch's needs
- Assure security of warehouse and grounds
- Motivate and challenge Warehouse employees; delegating tasks to staff; monitor progress, measure results, and coach staff on performance
- Maintain appropriate employee documentation files
- Train or obtain training for employees to handle assigned tasks as needed
- Develop and promote internal employees and recruit new employees as needed
- Communicate and administer company policies to all employees throughout the branch
- Establish and maintain good rapport with internal and external customers through effective communication and providing prompt 24-hour support
- Maintain confidential information pertaining to supervisory duties, operations and contract information
- Assures compliance with company business processes
- Bullet point
- High School Diploma or GED (General Education Degree) and additional related training, and direct experience in a material a PVF or related material distribution operation
- Four (4) years experience working in a warehouse or closely related environment
- Two (2) years supervisory experience or demonstrated capability to supervise (warehouse-related supervision preferred)
- Ability to operate and become certified on forklifts, order pickers, cranes, and other typical warehouse material handling equipment
- Demonstrated in-depth knowledge of basic warehouse functions and procedures
- Valid Driver’s license with the ability to meet the MRC vehicle policy and the ability to travel as needed to MRC branches and customer locations upon request
- Demonstrated competence in the use of computers and software applications
- Ability to read and speak the English language proficiently in order to communicate with others; to understand and interpret safety instructions; and to respond to inquiries
- Minimum 6 years of experience
- Career in Industrial Engineering
- Experience with MRPs
- Experience with Warehouse Management System
- 80 % English
- Experience as lider or supervisor
- Work under pressure
- Experience in electronic manufacturing
- Excellent company culture
- Great pay & benefits
- Growth & development
- Smaller scale warehouses with close-knit team
- Maintains overall responsibility for the warehouse location
- Hires, develops, trains, and engages a professional team of associates
- Develops reporting on key performance goals including cost tracking
- 2+ years leadership experience in a wholesale distribution/manufacturing environment
- Must have worked with large national and regional vendors
- Multi-site experience is strongly preferred
- Proven strong written, verbal, interpersonal and analytical skills
- Proficient in Microsoft Work, Excel and Power Point
- Abilty to work in a constant state of alertness and safe manner
- Manage the shipping/receiving operations in a non-union manufacturing environment
- Provide coaching, timely feedback and direction to ensure team development
- Ensure all employees are working in a safe manner by developing a culture where employees participate, address unsafe conditions and behaviors, and make suggestions for improvement
- Develop departmental Key Performance Indicators (KPIs) that drive value and support for the Gypsum vision
- Provide expertise on the shipping/receiving processes, inventory control, motor transportation (via trucks), and warehouse distribution
- Coordinate with production and scheduling teams, motor carriers to ensure timely shipment and delivery of all products
- Work with the GP Transportation Group to ensure the most efficient common carrier is used
- Communicate gaps and opportunities with carriers, sales, the logistics group, and in-house contractors
- Communicate financial shipping issues to the plant controller
- Manage warehouse inventory and placement of in-house goods; including daily and monthly reconciliation of warehouse inventory
- Complete all correspondence and analysis in a timely and effective manner
- Exhibit strong problem solving, decision making, and multi-tasking skills in a fast pace environment
- Associate’s Degree or higher
- Two (2) or more years of leadership or supervisory experience
- One (1) or more years of manufacturing experience in Logistics, Shipping or Warehouse Management
- This is a Monday thru Friday, day shift position, however must be able to work weekends and holidays when needed
- Must have experience with Microsoft Word and Excel, and the ability to learn various computer-based logistics and production reporting applications
- Bachelor’s degree in Business Administration, Accounting, Finance, Supply Chain, Logistics, Engineering, Physics, Math, or Inventory/warehouse management
- Four (4) or more years of manufacturing supervisory experience in Logistics, Shipping or Warehouse Management
- Knowledge or experience with managing a continuous improvement process
- Logistical experience with truck shipments, customer service, and/or accounting
- Experience with Mopar and OneLisa software
- Excellent MS Excel skills
- Minimum of 3-5 years of fulfillment management experience in a warehouse, inventory control, or production environment
- Excellent supervisory skills
- Strong process improvement / continuous improvement skills
- Strong inventory control experience
- Computer applications using MS office
- Excellent knowledge of ERP and WMS systems, Oracle preferred
- Detailed knowledge of materials flow, shipping and receiving functions (both inbound and out bound) in a fast moving environment
- Working knowledge of OSHA, HAZMAT regulations and the willingness to become certified in one or more of these areas as necessary
- Excellent analytical and mathematical skills
- Manages Warehouse operations which may include preparation and control of budget, scheduling, purchasing, or statistical reports
- Interprets and/or implements company and internal administrative policies and procedures as they apply to functional area or assignments
- Ensures that activities are conducted in compliance with established procedures and keeps warehouse personnel informed of requirements and commitments in regards to all warehousing operations
- Lead and direct the general services group along with overseeing the preventative maintenance effort for the warehouse items and main mechanical equipment in storage
- 4+ years applicable work experience and combination of additional specialized experience/technical education can be considered in lieu of educational requirements
- Associates degree plus a minimum of four to seven years warehouse experience, including 3+ years as a supervisor. Experience with a large freight forwarder is required. An equivalent combination of education and experience may be considered
- Understanding of TSA, U.S. Customs regulations and Forklift Certification is required
- Inspires the trust of others; Works with integrity and ethically; Upholds organizational values
- 3+ year of management/supervisory experience
- Experience managing across various employee levels, days, and shifts (preferably multi-shift)
- Process improvement and workflow analysis experience
- Exemplary attendance and punctuality record
- Flexible to work any/all shifts, schedules, hours and areas including weekends, nights and holidays as needed
- Commercial print environment experience preferred
- 5+ yrs exp. in a Warehouse Management position
- Experience with Material Handling Equipment and processes
- Familiarity with Warehouse Management procedures and Inventory Control
- Previous experience in a management or supervisory role; preferably in a Warehouse or Distribution setting
- Demonstrated knowledge of material handling and traffic management
- Working knowledge of government regulations pertaining to warehouse operations
- Strong leadership skills and the ability to support divisional business objectives
- The ability to recognize and solve practical problems or issues
- The ability to effectively interpret and present information both one-on-one and in front of an audience
- Fork lift certification preferred
- Demonstrated strengths in interpersonal skills, including the ability to adapt to the audience and professionally communicate with a variety of people
- Self-starter with excellent organizational skills and an ability to handle multiple tasks concurrently and independently
- Demonstrated proficiency with Microsoft Office Products, especially: Excel, Word and Outlook
- The ability to communicate and interact with coworkers in a positive manner and be an integral part of a team environment
- Associates degree in a Business Management or related
- Five years previous experience in a management or supervisory role in a Warehouse or Distribution setting
- Three years of experience with IFS and/or ERP system
- The ability to solve complex problems with high attention to detail and work in a fast-paced environment subject to specific deadlines
- Must be a person of passion and integrity who has the drive to excel and deliver exceptional results
- Proven track record in people management role (leadership, engagement and people skills) in a physical handling environment
- Able to set clear and achievable goals for team
- Coordinates all physical handling activities in the station
- Provides guidelines to team leads to ensure Handling Operations are consistent with group business strategy
- Monitors Quality and adherence to standards and is responsible for constant improvement and optimization of product
- Responsible for cost monitoring and improvement
- Develops a high performance service culture in the warehouse
- Ensures compliance with corporate, local, provincial and federal regulations and guidelines
- Monitors subcontractor performance and develops improvement plans
- Owns staffing responsibility and training of contractors
- Maintains proactive communications and relationships with product, sales, and operations teams
- Supports the station with building maintenance and handling subcontractor management
- Responsible for accurate receiving and shipping of product
- Manage pulling process for accuracy and timeliness
- Ensures warehouse is up to company standards on appearance and functionality
- Responsible for 5S in the warehouse
- Partners with Operations Manager to ensure appropriate levels of inventory are on hand to maximize sales
- Reviews discrepancies from inventory and make appropriate corrections
- Ensures all merchandise is properly racked and tagged
- Assists Operations Manager with inventory and safety audits
- Assists in managing warehouse processes, directing work load, and dispatching drivers
- Monitors safety of warehouse operations and assists with training for new employees and periodic re- training for all those in the warehouse
- Manages Function of the operating warehouse
- Manage warehouse processes including receiving, put away, pulling, and loading trucks
- Responsible for initial new hire training, ongoing training and maintaining a safe work environment
- Follows and executes any additional direction sent out by the Operations Manager
- 3+ years Warehouse Management experience
- College preferred
- Ability to read and interpret financial reports, documents such as safety rules, maintenance instructions, and procedure manuals
- 2+ years Wholesale Experience
- 2+ years Previous warehouse/manufacturing experience
- Wholesale or Home delivery service
- Microsoft Office products
- Implements project specific warehouse procedures
- Responsible for safety of personnel and material in the warehouse and laydown yards
- Maintains inventory control
- Receives, stores, controls and issues materials and major/minor equipment
- Implements and maintains warehouse activity files; chronologically documenting performed activities such as preparing material receiving reports; over, short or damage reports; shipping reports, etc
- Assists in identifying shortages for resolution by Material Control
- Establishes and maintains a current receiving purchase order file (requisition and purchase orders are to be included)
- Issues the daily dock report of received materials
- Maintains inventory of all returnable containers that require a deposit, e.g., pallets, drums, reels, etc
- Verifies all demurrage invoices
- Responsible for warehouse runner
- Ensures that material systems and daily input of receipts and issues are current
- Inventory management to include daily/weekly inventory of entire warehouse to maintain appropriate inventory levels and product loss control
- Manage the operational controls and corporate compliance part of the operation on a daily basis
- High school diploma or general equivalency diploma (GED) with 5 years experience in warehouse/distribution center operations OR Bachelor's degree from an accredited university
- Is responsible for the warehouse facility at night; maintains that it is properly secured and that procedures limiting access to the warehouse facilities are followed in order to minimize the opportunity for pilferage and loss of inventory
- Determines work procedures, prepares routing and expedites workflow in order to load delivery trucks for distribution the following day
- Notifies the Senior Management in the event of an emergency, or serious threat of damage/injury to the facilities, personnel, or inventory
- Utilizes good judgment in the event of such a threat, minimizing damage and loss
- Manages 3-5 subordinate supervisors who supervise a total of 25+ employees in the Night Warehouse. Is responsible for the overall direction, coordination, and evaluation of these units. Also directly supervises one non-supervisory employee. Carries out supervisory responsibilities in accordance with the organization's policies and applicable laws. Responsibilities include interviewing, hiring, and training employees; planning, assigning, and directing work; appraising performance; rewarding and disciplining employees; addressing complaints and resolving problems
- Establishes an organizational structure by assigning responsibilities, delegating authority and selecting, orienting and training direct reports
- Leads warehouse staff by coaching, counseling, motivating and disciplining as needed; plans, monitors and appraises job results; directs and maintains activities designed to achieve and maintain high employee morale; fosters intra- and inter-department cooperation
- Achieves financial objectives by preparing warehouse budget, scheduling expenditures, analyzing variances, compiling and studying costs to initiate corrective actions; requests assistance from internal financial support as needed; studies new regulations affecting the transportation field and advising management of needed actions
- Maintains a safe, clean and secure working environment by establishing and enforcing procedures, rules and regulations; initiates fixed capital requests; monitors all safety and security systems and procedures on a regular basis; supports plant safety meetings that evaluate plant machinery, equipment and working conditions
- Ensures compliance with Corporate QS/RC and GMP procedures by initiating and monitoring related training programs; monitors transportation of product and schedules activities on a daily basis; maintains frequent contact with Production, Quality and Maintenance staff
- Strives for continuous improvement by analyzing new or alternative ways to improve operations; incorporates new staff suggestions into analysis; investigates deviations and Customer complaints making recommendations and/or implementing corrective action; responds to audit activities in a constructive manner and uses findings to improve operations where possible
- Assists in the administration of current and new business activities by developing plans and strategies to meet Customer requirements and maximize profit
- Monitors the implementation of plans and strategies by collecting, analyzing and preparing reports for review by appropriate company management
- Ensures that all federal, state and local regulations pertaining to, but not limited to, radioactive materials, licensing compliance, safety, EPA, OSHA, FDA rules and regulations are adhered to. Maintains a working knowledge of regulations and establishes a monitoring program that responds to audit activity in a constructive manner
- Promotes and protects the company reputation by participating and representing the company in local community activities
- Maintains professional skills, knowledge and abilities by attending educational workshops, reviewing professional publications and participating in professional societies
- Drives safe working behavior by demonstrating and promoting safe work performance, ensuring effective communications and recognitions, as well as identifying and anticipating safety training needs, and counseling and training employees
- Communicates in an effective manner by utilizing accepted business practices in a courteous and professional manner to provide timely and accurate responses and service oriented offers of assistance
- Provides protection to employees by promoting personal protection and issuing monitoring devices in hazard areas as required by safety rules
- Supports the STERIS AST business imperatives of Growth, Operational Excellence, Leadership Excellence and Customer Focus, by acting with integrity, treating everyone with mutual respect, exhibiting a genuine commitment to the success of all employees, and delivering satisfaction to our Customers through teamwork, innovation and continuous improvement; this will be accomplished while acting safely and is defined as "The STERIS Way."
- Ability to effectively read, write and verbally communicate in English
- Ability to work independently under general guidelines and supervision
- Requires computer literacy to include word processing, spreadsheet and software capabilities
- Effective interpersonal skills as demonstrated through prior management experience
- Above average organizing, analyzing and a minimum of Level 3 math skills (ratios, proportions basic algebra) to determine organizational Customer and regulatory problems to formulate corrective action plans
- Ability to adapt to changing duties and responsibilities
- Ability to influence people in their opinions, attitude or judgements; to generalize, evaluate and make decisions in stressful situations
- Manage and optimize the Customer Distribution Center within given frames based on an environmentally and socially sustainable Supply Chain
- Lead , coach and develop a high performing CDC organization (communication, flexibility, performance culture, competence development, succession planning )
- Secure efficiency and initiate improvements to reach excellence in operations defined in the CDC business plan and to fulfill performance goals defined in the GSP with customer in focus and total supply chain in mind
- Responsible for budget and result for the Customer Distribution Center and secure that benchmarking and improvement process is in place
- Secure that warehousing process and new technology is implemented in the CDC
- Secure that IKEA rules and country specific laws and regulations are followed ( safety & security, labor laws etc)
- Facilitate communication and cooperation with stake holders involved in Customer Delivery process in the CDC area
- Contribute to the creation of the CDC area business plan and implement local action plans secure necessary information flow and effective communication throughout the organization
- Lead and participate in networks and projects
- University degree (Logistics, Economics or related) or equivalent in working experience
- Min 3 years working experience in a management position (preferable in Logistics, Retail or related)
- Proven leadership skills enable to communicate, inspire and motivate co-workers
- Fluency in English ( written & spoken) and willingness to learn local language
- Good understanding of Supply Chain and aspects related to logistics
- Good Understanding of social and environmental aspects related to logistics
- Strong communication and relation skills, ability to build trustful relations and commitments
- The ability to get things done and to realize goals, with the desire to question current ways of working and to strive for quick, lean and simple solutions
- The ability to develop and to lead an organization in a changing environment
- Ability to implement structural way of working
- Customer oriented, always striving to reach customer success
- Warehouse supervision
- Ensures materials are stored properly to conserve space and comply with safety procedures. Oversees the rotation of inventories within the warehouse
- Inventory control - manage inventories to expected levels at competitive costs while covering customer demands
- Truck Scheduling - contact, schedule and organize trucks to meet our customer and plant requirements
- Cost control - find ways to reduce cost while meeting operational and customer needs
- Support all Corporate and Plant level Continuous Improvement (CI) Initiatives. Ensure the department maintains acceptable standard with respect to lean manufacturing, sanitation, and various initiatives as assigned
- Maintain high standards with respect to raw materials and finished product. Maintain good manufacturing practices with respect to handling, storage, shipment of goods and materials
- Foster and enforce a positive safety environment. Support all Corporate and Plant safety initiatives
- Effectively manage Warehouse workers and other assigned employees. This includes, but is not limited to identifying employee's skills and developing them by coaching and counseling on a regular basis. Providing feedback on both positive and negative performance
- Forecasting - monthly expenses in warehousing costs, warehousing labor and inventories
- Budgeting - prepare annual budget for warehousing costs, forklift maintenance and all associated labor
- Strong knowledge of warehouse, inventory, and supply chain concepts
- Strong knowledge of company policies and procedures
- Working knowledge of ERP systems, Eclipse preferred, and Microsoft office products
- General business acumen
- Working knowledge of OSHA, DOT, and FMCSA regulations
- Effective management, leadership, delegation, communication, interpersonal, detail orientation, accuracy, judgement, decision making, negotiation, creativity, organization, and stress management skills
- Ability to drive accountability
- Ability to effectively manage multiple tasks, priorities, and deadlines, and easily adapt to changing situations in a fast paced environment
- Adding, subtracting, multiplication, and division skills with or without using a calculator
- Ability to calculate figures and amounts such as margin, discounts, interest, proportions, percentages, area, circumference and volume
- Ability to read maps and use GPS
- Ability to maintain a high level of confidentiality
- Maintain a professional image as a representative of the Company
- Ability to read and interpret documents, such as safety rules, operating and maintenance instructions, and procedures
- Ability to operate standard office equipment
- Manages the shipping, issuing, receiving, storage, and inventory of spare parts in a 35K sq.ft. warehouse and 50K sq.ft. of outside storage space. Conducts the cycle count process. Completes on or before set scheduled date
- Conducts physical counts and frequent cycle counting and reports with the electronic records of the inventory management system (DataStream)
- Classify inventory types and drive optimization of inventory levels
- Maintains proper housekeeping conditions of the warehouse facilities, ensure security of the building and inventory, as well as the safety of employees working or visiting the areas
- Implements best practices for proper storage of inventory parts with frequent periodic inspections to ensure proper condition, prevent deterioration from weather conditions (for parts stored outside) or aging
- Cooperates with the Procurement and Method departments to ensure all necessary parts are available to maintain the reliability of the equipment of the plant
- Determines proper layout for safe and efficient storage of parts and equipment
- Manages warehouse optimization project focused on: warehouse structure, personnel, and catalogue improvement
- Replenishes inventory per the set MIN/MAX levels
- Produces regular reports and statistics on a daily, weekly and monthly basis to inform plant management on major KPI’s related to the warehouse operation as well as to identify opportunities for optimizing the inventory levels according to the current and future plant needs
- Drives implementation of consignment at the warehouse to decrease the working capital in inventories
- Supervises daily activities of the warehouse team (receiving, tagging, shelving and issuing of inventories)
- Monitors fuel, oil, lube and grinding aid inventories, and arrange for prompt replenishments
- Manages the flow of parts through the facility, to ensure that all items are received immediately and inventories remain centralized
- Drives automation and systems optimization at the facility. Work closely with IT to ensure that supporting systems are useful and effective to maintain a lean organization
- Bachelor’s degree in related industrial fields (industrial engineering, supply chain management, civil engineering, systems engineering), preferred
- Proficient computer skills on warehouse management software (databases, DTSM, SAP)
- Must have excellent interpersonal, oral, and written communication skills
- The ideal candidate must demonstrate the following
- Manages and assists with shipping and receiving, unloading trucks, checking in material and matching Purchase Orders (PO) to sales orders
- Read customer orders, work orders, shipping orders, or requisitions to determine items to be moved, gathered, or distributed and/or shipped
- Direct and support the movement of materials and items from receiving or storage areas to shipping or to other designated areas
- Direct the sorting and placement of materials or items on racks, shelves, or in bins according to predetermined sequence, such as size, type, style, color, or product code
- Coordinate the fulfillment of requisitions, work orders, or requests for materials, tools, or other stock items and distribute items to shipping or to designated route driver storage area in accordance with company standards and processes
- Assemble customer orders from stock and place orders on pallets or shelves, or relocate orders to a holding area or shipping department
- Ensure warehouse is accessible and safe. Organize warehouse and work area for orderliness at all times
- Wear the proper safety equipment and ensure Personal Protective Equipment (PPE) is used at all times by staff and others within the facility
- Ensure that all materials are marked with identifying information using appropriate method
- Direct the opening of bales, crates and other containers
- Assist in cycle counting and physical inventory
- Assist when necessary with the use powered industrial trucks to move materials
- Perform safety checks of all equipment and complete a daily log
- Perform any additional duties and responsibilities as assigned by management
- Work closely with all functional areas to ensure no impacts to production schedules will occur due to material or equipment deliveries
- Coordinate use of CPS Warehousing & Distribution services with other CPS sites, municipal agencies and private industries
- Manage warehousing and distribution equipment, supplies, and materials to ensure that customer requests are shipped and delivered in the most efficient and cost effective manner
- Creatively manage, develop and enhance all furniture, equipment and supply donation programs
- Travel, vet and secure donations, on behalf of Chicago Public Schools, of supplies, materials, furniture, and equipment
- Act as liaison to leasing vendor; review and process payment for vehicles assigned to the warehouse. Recommends the leasing, purchasing and modification of new and existing vehicles and projects annual costs
- Hire, train and discipline warehousing & distribution staff in compliance with departmental best practices and Board of Education policies and procedures
- Identify, implement and monitor key business metrics to obtain optimal results while sustaining low operating costs
- Adhere to local, State, and Federal regulations inclusive but not limited to OSHA, DOT, Collective Bargaining Agreement, and EEOC
- High School Diploma. Bachelor’s degree preferred; equivalent job experience accepted, or a combination of training and experience related to this position
- Five (5) or more years of distribution, warehousing or logistics experience working in transportation or related field
- Recent logistic experience which includes five (5) or more years of extensive knowledge of warehouse inspection methods, techniques, and processes
- Proficient in the use of Google applications, Oracle and CPS Knowledge Center is preferred
- Strong verbal and written communication skills with ability to read, analyze, interpret and write general business correspondence, reports and procedure manuals
- Impeccable organization and time management skills with proven track record of working under pressure, prioritizing demands of multiple due dates and superiors
- Must own a vehicle and hold a current valid driver’s license and vehicle insurance with good driving record
- Experience in successfully creating and/or modifying operations, development of new programs and business processes
- Have the ability to interact, present information and maintain relationships with corporate donors, building management companies, union representatives and various levels Chicago Public school staff with an elite level of professionalism
- Manage the day to day warehouse team as well as assist during the inbound and outbound shipping process; the opening and closing of the facility; ensuring activities are performed in compliance with company policies and procedures: and finally, managing the integrity of the Sort Processing area and Operations Vault and all Vault Procedures at all times
- Appropriate work assignments among sort employees and align daily assignments with customer needs
- Provide other management support as may be directed from time and to be available to work flexible hours
- Maintain a good working relationship with all branch employees and keep in constant communication with the General Manager of East Brunswick, the Director of Operations and the VP of Operations on matters pertaining to the warehouse and all staff
- Engage and actively meet/ communicate with the clients to clearly understand their demands and define BGS capabilities and operations/ manpower limitations
- Minimum of three (3) years supervising or Managing a group of logistics professionals engaged in secured logistics activities including but not limited to the Import/Export/Domestic shipping of sensitive and highly valuable items
- Minimum of three (3) years of experience in logistics in a high touch customer facing role and/or a role processing shipments through a logistics life cycle or transferrable Brinks or Brinks Global Service experience in a role that would serve as the foundation for this position
- Demonstrated PC proficiency with Microsoft Office, especially Excel
- Minimum of 21 years of age
- Experience in the freight/ shipping and security transportation business
- Bachelor’s Degree in Business Administration, Engineering or Process management
- Experience providing efficient and accurate customer services for import/export customers
- Manages department responsible for receiving, sampling, warehousing, JIT, logistics and related activities for the Devens Site and insures continued conformance with all relevant regulations (GMP, DOT, IATA, IMDG)
- Develops strategies for materials management functions and collaborates with Supply Chain leadership team to develop and implement the Supply Chain vision and strategy
- Collaborates regularly with the site planning, procurement, quality and manufacturing groups to ensure materials are available and delivered to support production activities
- Approve/author, SOPs, Investigations, CAPA, and change control related to materials management activities
- Partner with Technical Services to accomplish validation activities in materials management areas
- Identify capital needs, assist in CAR process, and follow through to closure
- Set, monitor, and spend according to applicable cost center budgets
- Promote Safety, Leadership, Team Building, Performance Standards, and BioPharma Behaviors
- Identifies and implement process improvements
- Provide project management support for new product implementations, productivity improvement, harmonization activities, and general site initiatives. Champion Operations Excellence initiatives related to warehousing and materials management
- Implement and oversee programs to maintain materials management areas and processes as inspection ready at all times
- Act as Warehouse Management SME during regulatory audits, as necessary
- Bachelor’s degree in business, logistics, supply chain management, industrial engineering or related discipline
- Knowledge of plant operations and a minimum of 8 years experience in a Supply Chain function with experience in GMP warehousing and logistics, or it's equivalent
- Experience in team management and project work is required
- Excellent understanding of DOT, IATA, and IMDG regulations for the transportation of hazardous materials
- Good working knowledge of trade and commerce regulations and practices as well as documentation requirements for both domestic and international transportation
- Good working knowledge of SAP WM module. Experience with TrackWise and/or Syncade MES a plus
- Excellent communications and computer skills with a demonstrated proficiency with MS Access, Word, Excel, PowerPoint, Project and SAP
- Ability to work independently and participate in project teams
- Able to communicate with all levels of Management, develop successful working relationships, and possess an ability to influence site team members
- A good work ethic and common sense is important
- Good previous experience of working in a fast moving warehouse
- A positive attitude and flexible approach to working
- Ensure all staff is in place and properly trained
- Drive a culture of "What you say matters, what you do matters"
- Manage receiving/shipping activity to execute on time delivery
- Support processes to drive accurate inventory
- Work with other FSBP plants/DCs, participate in best practice recommendations and significant accomplishment sharing
- Analyze and report on KPI's and activities driving improvement
- Communicate targets, objectives, and goals throughout the warehouse team
- Support and maintain an environment of continuous improvement that parallels company objectives, establish standard
- Assure all functions operate in accordance with company safety policy, also in compliance with DOT, HAZ-MAT, and all other Federal, State, and Local regulations
- Drive root cause analysis for service concerns
- Set goals and objectives towards teammate success and advancement
- Lead project analysis as requested
- Manage customer relationships
- Responsible for warehouse expense management
- Bachelors degree – preferably in logistics or business administration
- 10 years of progressive responsibility in a logistics environment including 4 years of supervisory experience and 4 years of warehousing experience
- Supervises warehousing activities to ensure that both incoming and outgoing product are handled properly using proper training, accuracy systems and programs
- Plans and assigns work for most efficient use of personnel and equipment, ensuring that production standards are being maintained
- Develops weekly, quarterly and annual goals and MBO’s
- Interfaces with warehouse management, transportation, human resources, and buyers to maintain efficiencies and service levels. Recommends and implements improvements in warehouse practices to promote efficiency, faster service and lower costs. Works with Facility Maintenance Manager to ensure that equipment is properly maintained and that any repairs are handled quickly and economically
- Prepares and effectively administers department budget. Authorizes overtime and work to control costs. Evaluates capital expenditures and prepare requisitions and recommendations. Develops sizing information to ensure proper utilization of warehouse space
- Prepares agendas and direct Safety Committee meetings, in accordance with the Safety Matrix; recommend additions or changes in safety procedures and policies
- Manages, coaches, mentors, motivates and trains warehouse employees
- Monitors SAP Warehouse Activity to ensure teams meet internal and external customer requirements
- Monitors overall warehouse performance
- Identifies, coordinates, assigns and implements warehouse projects as necessary to meet corporate goals and objectives
- Manages projects for warehouse that may involve software upgrades, equipment installations, facility relocations or expansions
- Maintains a personnel structure and staffing level to support customer requirements
- Performs reviews and handles disciplinary actions
- Facilitates communication and cooperation across the organization to ensure departments and processes collaborate to meet corporate objectives
- Analyzes all aspects of branch logistics to determine the most cost-effective and efficient means of inventory warehousing and the transporting of products and supplies
- Directs inbound and outbound logistics operations, such as transportation, warehouse activities, safety performance and logistics quality management
- Plans and implements material flow management systems to meet production requirements
- Maintains and monitors appropriate infusion ancillary supply inventory and is responsible for the procurement of supplies from approved vendors. May also be responsible for maintaining, monitoring and ordering drug through approved vendors
- Ensures compliance to Company product formularies
- Assists the Pharmacy Manager and/or General Manager in preparing for and conducting monthly and year-end physical inventories
- Oversees the management, distribution and return of all durable medical equipment, ensuring the proper tracking of all DME assets through established company policies and asset tracking systems
- Collaborates with other departments to integrate logistics with business systems and processes, such as customer sales, order management, accounting and shipping
- Directs distribution center operation to ensure achievement of cost, productivity, accuracy and timeliness objectives. Analyzes the financial and service impact of logistics decisions and act in real time
- Participates in courier management processes, such as selection, qualification and performance evaluation. Ensures courier compliance with Company policies and procedures for product transit and delivery. Negotiates rates for courier services
- Resolves problems concerning transportation, logistics systems or customer issues. Implements specific customer requirements, such as internal reporting and customized transportation metrics
- Maintains metrics, reports, process documentation, customer service logs, and training safety records
- Hires, trains and supervises the work of all warehouse and equipment staff. Serves as resource and support all warehouse employees
- Each employee is responsible for adhering to those performance programs, policies, procedures, guidelines and internal control standards established to guide the operation of the Company. Each employee must be made aware of and understand proper internal control procedures associated with their specific job function as communicated by his/her manager
- Each employee is responsible for reporting concerns that he or she may have with respect to deficiencies in internal control
- Managers and supervisors are responsible for ensuring that internal controls are established and functioning to achieve the mission and objectives of their unit. Each employee within an area under the manager or supervisor’s direction must be made aware of and understand proper internal control procedures associated with their specific job function
- Managers and supervisors must acknowledge that utilization of internal controls is an inherent part of a manager’s responsibility, not a new or additional function, and assure that internal controls are supportive of and consistent with the operating mandate and philosophy of the Company
- Management responsibility for all warehouse staff; may direct subordinate supervisors
- The employee is frequently required to stand, walk, sit, reach outward, and handle/finger
- Specific vision abilities required by this job include close vision, distance vision, peripheral vision, and the ability to adjust focus
- Work is normally performed in a typical warehouse work environment
- May occasionally be exposed to moving mechanical parts
- Knowledge of durable medical equipment and drug/supply procurement and logistics
- Excellent problem-solving, decision making and prioritization skills
- Excellent planning and project management skills. Ability to handle multiple projects concurrently
- Knowledge of issues and trends driving the healthcare industry
- Demonstrated knowledge and proficiency in the principles, procedures and best practices related to this position
- Ability to train employees
- Supports and promotes departmental goals and initiatives
- Strong interpersonal and communication skills. Ability to work cooperatively and effectively with branch departments and department team members
- Plans and organizes work effectively
- Prioritizes responsibilities and workloads
- Displays a neat, clean and professional appearance and demeanor at all times
- Ensure contractual requirements are met and assist with managing milestones
- Properly convey scheduling, potential conflict, needs and job progress to their manager and the customer
- Work with their manager to manage prime-contractor requirements, schedule and to deconflict any potential issues
- Attend daily/weekly production/progress meetings as required and contribute to project success. Responsible for Warehouse Access data base and to monitor, prepare and submit contract required monthly performance reports to management
- Ensure customer, project team, and contract requirements/regulations are met by team
- Interact on a regular basis with the customer, and speak knowledgably and reliably in order to field customer questions and concerns, in order to achieve 100% customer satisfaction
- Provide daily work assignment to the Warehouse personnel supporting all current contracts. Monitor work performance and accomplishment and interface with their manager for direction
- Coordinate and direct personnel loading and unloading shipments at multiple staging and receiving areas, transporting material and items between to various CONUS/OCONUS points using both commercial and government delivery systems
- Manage sorting and placing of material in defined storage locations using identifying information counts, and sorting incoming material to verify receipt of items on requisition or invoice. Examining received stock to verify conformance to specifications, filling requisitions or requests for materials and other stock items for issue to requester
- Manage a plan the storage of articles in bins, on floor or on shelves/racks, according to identifying information, such as style, size or type of material. Maintain traceability of material from procurement until issuance
- Read shipping orders or requisitions to determine items to be moved, gathered or distributed. Prepare material for delivery
- Coordinate conducting periodic inventories to a high level of accuracy and will be Inventory Team Lead for certain categories of material. Assist with periodic, special, cyclic, or perpetual inventory of stock Inputs data on adjustments of inventory counts to computerized stock records. Note damage to stock, location changes, and refusal of shipments. Inform supervisor or other appropriate personnel of low stock. Responsible for inventory discrepancy causative research and resolution
- Maintain familiarity with US Government, US Navy and customer requirements for handling, packing and shipping of various materials to include time sensitive shelf life and hazardous materials
- Ensure that 13 Mandatory rules are being adhered to
- Ensure that 13 HRLG are implemented and adhered to
- Manage teams in line with OHP guidelines
- Ensure that 7 inventory basics are implemented and adhered to
- Ensure that 7 delivery basics are implemented and adhered to
- Manage material flow from reception through to shipping / invoicing including JIT Centres
- Manage inbound and outbound transport flows
- Ensure that customer supply is stable and no MPM
- Ensure 5s in all Logistical areas
- Ensure the effective running of Pull flow
- Implement and maintain FES standards on the shop floor
- Find and implement productivity gains/cost savings
- Manage material handling equipment and company vehicles
- Respect for fundamental rights
- Employee Empowerment
- Development of economic and social dialogue
- Development of skills
- Ethics and business conduct
- Relevant M+3 qualification
- 3+years experience as a supervisor
- Knowledge of Pull flow and related logistics systems
- Ability to manage and motivate team
- Develop and recommend warehouse and distribution policies, procedures, and
- Bachelor’s degree in Business Administration and five to seven years of related distribution management experience; or any equivalent combination of experience and training
- Excellent organizational and interpersonal skills
- Exceptional oral and written communication skills. Good judgment and strong problem resolution skills
- Strong Word, Excel and Outlook skills
- Ability to successfully manage multiple priorities in a fast paced environment.EEO/AA/M/F/Veteran/Disabled
- 2-3 years supervisory experience in high volume manufacturing operations environment
- Experience of leading and achieving results in an extremely target driven high volume manufacturing environment
- Experience of Lean manufacturing and process control (six-sigma) techniques
- Proven skills and capabilities in leadership, communication, people management, and problem solving
- Use of Project Management tools and techniques
- PC Literate - particularly strong Excel and SAP skills
- English & Maths qualifications
- Degree in Engineering, Manufacturing or business related subject desirable. TEC level three/HND/BTEC (equivalent)
- IOSH Qualification
- FLT licence desirable
- Six-Sigma Green/Black Belt certification desirable
- Promote and contribute to an incident and injury free work environment
- Develop, implement, and measure goals to optimize and continuously improve Safety, Quality, and Productivity performance
- Continuous improvement of Warehouse and CSC processes, systems, and tools
- Develop and implement budget and processes necessary to maximize the effects of new technologies, to speed the production of new products, and to continue the success of current strategies, while taking into consideration the direction of marketing and R&D, and the inputs from engineering and the operational teams
- Launch and continue to Coach and Develop Autonomous Production Teams in a continuous improvement environment across multiple shifts
- Select, Train, Develop and Coach team members across multiple shifts
- Performance Management – Evaluation and Development of team members
- Consistent and fair application of company and department policies
- Ensure compliance with federal, state and local regulations
- Balance the prioritization of the needs of the Warehouse/CSC, Business, and Production Operations in order to meet department and site goals
- Develop and deploy effective communication methods for teams, shifts, departments, businesses, vendors, customers, etc. to share necessary information and accomplish both department and site goals
- Participate in and contribute to project teams and task forces that are beyond the scope of immediate warehouse/central shipping responsibilities
- Monitor, report and take action on Key Performance Indicators (KPI’s)
- Implement Lean tools (CL’s, CIL’s 5S, Lean Loss Analysis, Standard Work etc.) to identify and eliminate losses
- Utilize Visual Factory to Improve Work Flow
- Active member of Operations Leadership Team
- Lead Loss teams and Kaizens in Warehouse/CSC areas
- Minimum of a Bachelor's degree in appropriate field
- Minimum of 3 years of experience in Operations/Warehouse/Logistics Management with a minimum of two years of experience leading mid-to large size department/teams across multiple shifts
- Demonstrated Commitment and Actions to achieve high degree of Safety Awareness & Focus
- Demonstrated ability of strong verbal and written communication to reach multiple audiences
- Evidence of Change Leadership strongly preferred
- Demonstrated ability to develop and implement business strategy to achieve target objectives and results
- Demonstrated ability to plan organize projects and activities
- Strong initiative for self and as a leader, with proven success in dealing with ambiguity and working independently
- Strong computer skills in Microsoft Office Suite, SAP, etc
- Value Stream Mapping experience preferred
- Ability to work on backshift as needed (7p-7a)
- Experience in leading the implementation and utilization of Lean practices and tools (Kaizen, PDCA, CL, 5S, APT’s, etc.)
- Up to 2 - 5 years in a warehouse or shipping environment
- Ability to adapt to changing situations and to perform multiple tasks simultaneously
- Ability to safely load and ship product to various customer vehicles which may include commercial and non commercial vehicles of varying size
- Ability to pull and stage product for customers with the ability to do so quickly during rush periods
- Ability to keep the warehouse organized, well stocked and free from any safety or security hazards. Ability to multi-task and handle multiple order requests simultaneously
- Manage all aspects of Regional Distribution hub for South Texas including supervises and assigns tasks to Warehouse Associates based on business needs and customer priority
- Oversee the performance of all tasks involved in the shipment, receipt, and storage of supplies and equipment
- Supervise the product flow, facility layout, security, and maintenance activities of the Regional Distribution hub
- Develop and implement work flow processes to increase productivity and drives work force safety
- Oversees the partnership with LTL (less than a load) providers including cost control, damage claim rate, and customer satisfaction
- Responsible for staffing needs including hiring, performance management, coaching, development of Warehouse Associates
- Provide leadership for both the San Antonio Market and South Texas Region
- High School diploma/equivalent required, Associates degree preferred
- Distribution, warehouse operations leadership experience required
- Excellent communication and interpersonal skills required
- Minimum of 2 plus years of supervisory experience required
- Strong attention to detail, highly organized, self-starter
- Superior MS office application skills required including excel, outlook, ppt
- HVAC experience preferred
- At least 5 years of experience in dock/warehouse/logistics management
- At least 3 years of experience in working in a dock/warehouse or logistic operation
- Working knowledge of importing, exporting and logistics operations, with an emphasis on interaction
- Able to lead and mentor a team
- Assigns workers to accurately pull all customers orders and ship in specified time frame
- Generate and interpret Crystal reports to monitor employee productivity, customer exceptions and inventory audits
- Supervisory Responsibilities
- Manages personnel and all supervisors associated with shifts. Is responsible for the overall direction, coordination, and evaluation of these personnel. Carries out supervisory responsibilities in accordance with the organization’s policies and applicable laws
- Responsibilities include interviewing, hiring, and training employees; planning, assigning, and directing work; appraising performance; rewarding and disciplining employees; addressing complaints and resolving problems. Also responsible for asset control and the physical security of the facility
- Knowledge of basic office (spreadsheet, word processing, e-mail) as well as inventory and warehouse management software. Knowledge of AS400 and PKMS is essential
- Coach individual warehouse associates, plan, coordinate, and assign daily activities
- Maximize the cube fill rate on the delivery vehicles and minimize delivery costs and increase driver productivity
- Responsible for the proper collection, dispersal and retention of drivers logs, fuel tax reports, accident files and registers
- Manage the AS400 system for the purpose of measuring the pick accuracy and performance of employees (cycle count, bin walk, etc)
- Responsibility over the equipment, fixtures and vehicles assigned to the warehouse
- Provides leadership to the warehouse section and manages all processes related to storage, organization and cleanliness including the adjacent grounds
- Oversees the stocking of material, supplies and equipment received
- Monitors the issuing of material, supplies and equipment and ensures all documentation is properly prepared, signed and distributed to valid end-users as necessary
- Supervises and trains subordinates in the proper operation of warehouse equipment, ensuring all safety steps and precautions are adhered to
- Coordinates and oversees the delivery of material, supplies and equipment to various destinations
- Maintain and monitors the HAZMAT yard, ensuring all precautions are taken with regard to the storage and handling of hazardous materials
- Operates in compliance of OSHA and SHEMS
- Provide operator maintenance and inspection of warehouse equipment and vehicles as well as maintain the warehouse area in a clean and orderly state
- Lead, train and mentor warehousemen and truck drivers assigned to the logistics warehouse
- Must possess a current TS/SCI clearance
- A high school diploma or equivalent is required
- Five years progressive experience in a high volume, multi-unit receiving/inventory or logistics supply management environment
- Working knowledge of warehouse operations, including storage equipment and space management systems for the orderly stocking of material, supplies and equipment
- Position requires interpersonal skills relating to employees, customers and vendors
- Computer skills including an above beginner's level using Word and Excel - The ability to add, subtract, multiply and divide in all units of measure, using whole numbers, common fractions and decimals
- The employee must be able to lift and/or move up to 50 pounds
- Knowledge of ALL principles and processes involved in required materials
- Expert computer skills, specifically in Microsoft Word and Excel
- Must have the ability to be innovative and be an agent for change
- Represent IKEA values with regard to recruitment, training, development and leadership
- 5-7 years IKEA working experience in managerial function (preferably in warehouse operations) or 7-10 years of external high volume or multi-unit experience
- Understanding of budgetary process and similar business applications
- Strong logistics background (experience working in high volume distribution facility)
- University degree desired
- Clear and professional spoken and written communication skills are required. Must be able to speak and/or write clearly and to effectively communicate information and ideas so others will understand. Strong English language competency is a must. Bilingual is a plus
- Ability to effectively write reports and business correspondence based on audience need, and to effectively present information and respond to questions from groups, managers, customers, contractors and regulatory or government representatives as well as with other employees in the organization
- Ability to read, analyze, and interpret business periodicals, professional journals, technical procedures, or government regulations, and to interpret a variety of written, oral, diagram, or schedule instructions
- Highly motivated, results focused and able to concurrently handle multiple priorities. Ability to balance skills needed to plan strategically while being able to drive into a tactical approach as necessary
- Skilled in calculating figures and amounts and proficient in applying concepts such as fractions, percentages, ratios and proportions to practical and abstract situations, and working with mathematical concepts such as basic algebra, plane and solid geometry
- Proficient in high volume shipping and experienced with schedule planning in a shipping/warehouse environment. Understands methods for moving goods including relative costs, advantages and limitations
- Familiar with warehouse/inventory management systems, bar coding and computers (MS Office) for data and information entry and retrieval and for report, document and/or spreadsheet preparation
- Ability to solve practical problems and deal with a variety of abstract and concrete variables in situations where only limited standardization exists. Experienced using basic analysis methods to solve practical problems, collect data, establish facts, and draw valid conclusions
- Experienced in developing Return on Investment (ROI) and project management of modifications to equipment and factory procedures. Ability to make sound business decisions
- Possesses spatial capability to estimate and visualize available and needed capacity for raw materials through Work in Progress (WIP) and inventory needs. Understands how product components move, the fit and flow of processes, timelines, dependencies and benchmarks, and how to schedule and manage resources
- Ability to work nights, night time hours required
- 2 - 5 years previous supervisory experience required
- Prior Logistics Experience preferred
- Alignment and commitment to NWNA’s Leadership Framework (core values)
- Demonstrates confidence and influence in leading team to achieve productivity goals
- Skilled communicator (in groups and 1-on-1), who can set clear expectations with direct reports
- Ability to hold direct reports accountable through both quantitative and qualitative goal attainment
- Ability to provide training and development for direct reports
- Provides excellent role model, peer leadership and positive influence to fellow team members
- Positive team-player attitude
- Strong organizational skills / Attention to detail
- Possesses exceptional work ethic, energy, and drive
- Ability to handle physical requirements, including, but not limited to, repeated bending, stretching, twisting, and lifting up to 60 pounds
- Able to conduct regular inventory audits
- Able to safely use various warehouse equipment, including a forklift
- College degree preferred / High school diploma or equivalent required
- PC experience preferred (RMS, Excel, etc.)
- Systems proficiency with SAP (Globe), RMS, etc
- Travel required for role
- Manage all aspects of the day and/or night warehouse operations including receiving, restock, recoup, and order picking
- Maintain and manage department budget including labor and expenses including approval of all warehouse monthly purchases and invoices
- Manage capital expenditures tracking, reporting and purchases
- Design enhancements, review and react to critical reports and issues regarding labor, productivity and quality
- Manage all personnel issues including hiring, training, evaluating, disciplining and following up on warehouse staff concerns
- Oversee all aspects of safety with regard to state law and company policy
- Maintain appropriate levels of warehouse staff to meet budget as well as productivity requirements
- Develop and maintain positive, cooperative and team-oriented relationships with co-workers, supervisors, managers, and others you come into contact with through your job
- Minimum 7+ years warehouse management experience
- Strong Microsoft Office, communication, organizational, time management, analytical, relationship building, problem solving and attention to detail skills
- Ability to effectively layout warehouse and slot product
- Control logistics processes : (yard / exteriors management, receiving, delivery to lines, bookings, TPA preparation, alert management, cycle counting in all warehouse locations under plant supervision) with strong relationship with material planners and master scheduler
- Ensure full inventory accuracy through proper analysis in case deviance
- Ensure internal customer satisfaction : supervise day to day warehousing activities with strong relationship with shop floor supervisors, anticipate ressources with customers requirements (PIC/PDP), manage impact of launch of new programs within the warehouse
- Improve logistics performance : surface optimization, labor efficiency, handling utilization, HSE, alert management with strong support from PC&L improvement coordinator as well as other plant functions (Quality, FES, ME, Finance)
- Lead the Warehouse logistics team and set objectives
- Ensure adequate staffing, training and development of team members
- Establishes and effectively manages departmental budgets and objectives
- Responsible for inbound materials pallets and dunnage inventory
- Implement any necessary systems, processes or procedures to increase efficiency and maintain good customer service while maintaining minimal inventory loss
- Carries out all management responsibilities in accordance with Diageo NA and Relay policies and applicable laws, including interviewing, hiring, training employees, planning, assigning, and directing work; appraising performance, rewarding and disciplining employees
- Addressing complaints, and resolving problems
- Responsible for departmental programs such as Food Safety, Employee Safety, TTB Compliance, and Environmental Compliance
- Ensures all department employees are working safely, are aware of all safety rules, and are wearing required PPE
- Plans and coordinates work, trains, monitors and evaluates performance of all warehouse employees. Counsels and disciplines department employees as necessary
- Oversees all loading and unloading of materials, ensures materials are staged for counting and inspection, and that the shipping and receiving reports accurately report material shipped and received
- Resolves discrepancies with accounting regarding invoices, product received in and shipped from the warehouse, and receiving/shipping documents/reports
- Overseesthe rotation of inventories within the warehouse
- Works safely to prevent on-the-job injuries by following Buckhorn policies and OSHA standards
- 3+ years experience in warehousing, receiving, shipping, inventory control and forklift operation - required
- 3+ years supervisory experience - required
- Ensure adequate manpower to execute scope of work
- Ensure all materials databases and project reporting tools are updated with latest information
- Manage the flow of materials from requisition to installation to ensure safe and timely delivery
- Management and distribution of materials management workload
- Engage with and coordination of third party inspection requirements (e.g. rental plant and equipment)
- Ensure all materials management activities are completed in time for shipment of materials to relevant site(s)
- Manage the material control and warehousing functions to ensure timely delivery, receipt, checking, storing and issuing of goods
- Ensure all materials are clearly labelled with PO number, Client Ref and quantity
- Management of supply vessel movements and stock levels
- Ensure effective and timely reconciliation and disposal of surplus project materials ensuring costs are minimised
- Promote Health, Safety, Security and Environment within project team
- Possess at least 10 years of relevant experience
- Manages the overall operation, resources and organization of the warehouse making important business decisions supporting the organization’s overall business strategy
- Manages and oversees inventory control processes to ensure integrity (this includes the cycle count process)
- Manages the team and ensures that warehouse transactions (e.g. receiving, issuing, transfers and requisitions) are completed timely and accurately
- Manages the Warehouse Supervisor, internal warehousemen and external 3rd party vendors
- Proactively identifies and implements continuous improvement opportunities
- Collaborates with stakeholders, corporate and field locations as required to ensure total customer satisfaction within the warehouse functions
- Manages inventory and expenses
- Manages, leads, coaches and develops direct reports – driving performance and delivering results, product quality/knowledge, and timely, safe delivery
- Develops and emphasizes a culture of warehouse safety
- Maintains required records and documents accurately
- Conducts random physical inventory checks and report any findings
- Continuous quest to improve the warehouse operations
- Initiates, coordinates and enforces warehouse operational policies and procedures
- Possesses a solid understanding of supply chain activities and good warehousing practices
- Bachelor’s degree (or equivalent work experience) in Administration, Supply Chain, Logistics, Material Management or related fields
- Strong analytical, decision making and problem solving skills
- Must be able to establish and maintain good working relationship with team and all levels of management and employees
- Makes decisions that properly reflect company policy
- Strong, oral, written and organizational skills are required
- Extensive knowledge of oilfield and drilling materials
- Detail oriented with strong emphasis on quality
- 10+ years’ relevant warehouse, inventory, distribution and logistics management experience
- 5+ years’ of previous leadership and supervisory experience
- Outstanding leadership and communication skills; willing to make difficult decisions, communicate effectively with senior management of all business units
- Proficient in computer skills, specifically Excel, Power Point, Outlook and warehouse management software
- Positive team player with the ability to build relationships across all levels and departments
- Time management, prioritization and organization skills and the ability to delegate workload appropriately
- Able to handle and resolve conflict and performance issues
- Exercises sound independent judgment; self-directed and requires minimal supervision
- Ability to optimize time and resources to achieve expected results; effectively prioritize and organize work to fully contribute to team efforts
- Able to drive implementation of policies, procedures and best practices
- Exercises accountability, excellence, innovation, safety, teamwork and collaboration in daily activities
- Ability to manage and motivate teams
- Works under pressure with tight deadlines
- Works with stakeholders to provide service levels as requested
- Workload distribution
- Ensure quality through use and adherence to policies and procedures
- Good interpersonal skills, good computer skills
- Ensure inbound freight is all offloaded in a timely, efficient and orderly manner
- Ensure all freight is on handed and put away per required facility means utilizing all system technology
- Holding regular warehouse updates and safety meetings
- Providing an extremely clean and safe warehouse on a daily basis
- Oversee warehouse supply needs
- Any job as assigned by management
Related Job Titles
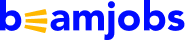
Build my resume

- Resume builder
- Build a better resume in minutes
- Resume examples
- 2,000+ examples that work in 2024
- Resume templates
- 184 free templates for all levels
- Cover letters
- Cover letter generator
- It's like magic, we promise
- Cover letter examples
- Free downloads in Word & Docs
3 Warehouse Manager Resume Examples That Work in 2024
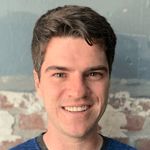
Warehouse Manager Resume
Clean warehouse manager resume, modern warehouse manager resume.
- Warehouse Manager Resume Writing 101
Every warehouse operation needs a strong leader to ensure the company’s policies and vision are achieved. You ensure operations succeed by overseeing and optimizing receiving, storage, and distribution processes with expert care.
Does your resume template help display your warehouse management skills effectively to help you land interviews?
With many policies and process improvement tasks in play, companies will want to know they are bringing in a well-versed pro for the job. You can optimize for success with our cover letter maker and warehouse manager resume examples that have helped many applicants land leadership roles in 2024.
Microsoft Word
Google Docs
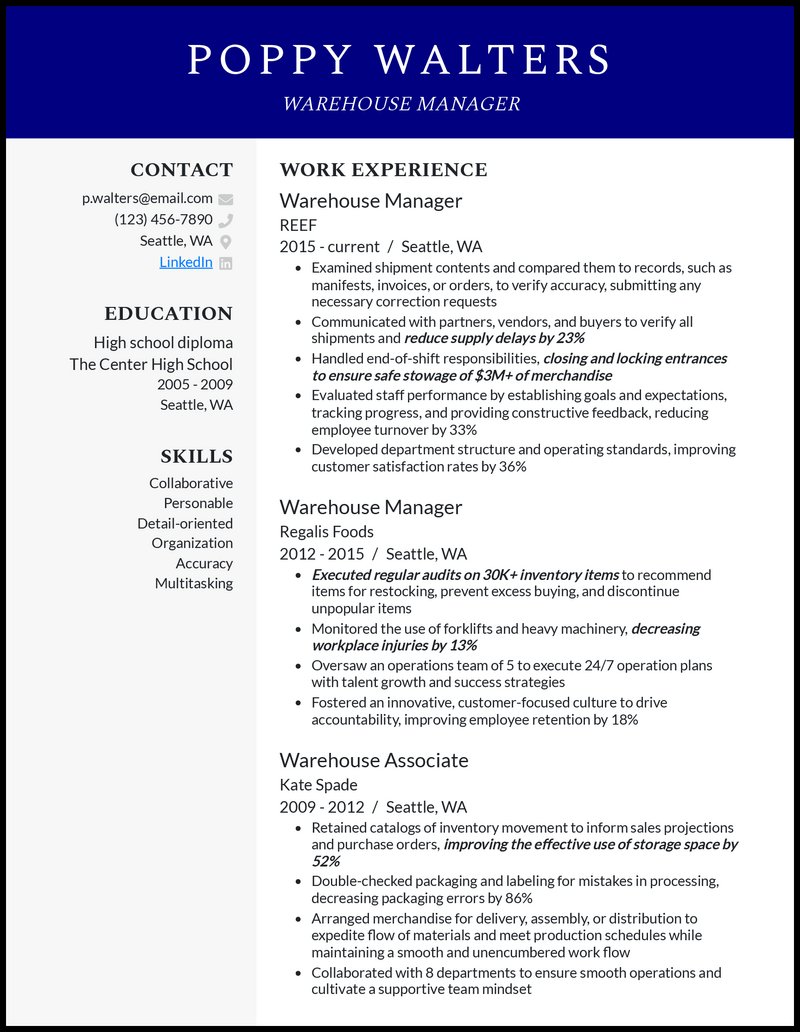
Related resume examples
- Warehouse associate
- Landscape worker
- Maintenance worker
- Warehouse worker
What Matters Most: Your Warehouse Manager Skills & Work Experience
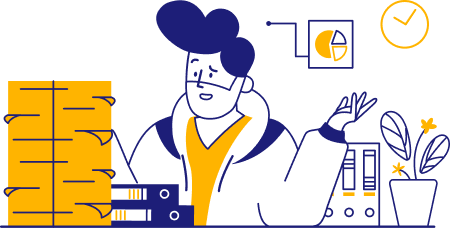
You handle many tasks, from cost management to enforcing OSHA safety regulations. That leaves many warehouse management applicants wondering what are the most essential job skills to include on resumes.
The first place you should look is the job description . Companies will tell you what they’re looking for by emphasizing key skills needed for the role. For instance, a company that needs help with supply chain optimization may highly value your experience managing data in the Da Vinci Supply Chain Business Suite.
Here are some top warehouse management skills to give you some ideas.
9 top warehouse manager skills
- Da Vinci Suite
- OSHA Safety
- Process Improvement
- Employee Relations
- Excalibur WMS
- Oracle NetSuite
- Quality Control
Sample warehouse manager work experience bullet points
Your abilities to improve processes and manage data in top software like Oracle NetSuite will catch a warehouse hiring manager’s attention. That said, you’ll still need to show the impact of your decisions on a warehouse’s operations in past positions.
Ideally, you’ll want to include metrics every warehouse tries to optimize for within each example you list. For instance, you could explain how your new quality control measures helped reduce damaged shipments by 42%.
Keep these examples straightforward, like you’d do when explaining a new packaging protocol to employees, to ensure the details you’re trying to emphasize stand out.
Here are a few samples:
- Developed a new 2-month employee orientation system that helped reduce operational errors by 56%.
- Monitored monthly performance goals using Excalibur WMS and provided employee coaching as needed to ensure 97% of performance metrics were met.
- Introduced a new 6-point quality inspection process during distribution to reduce the number of damaged items in shipment by 45%.
- Operated pallet jacks and hand trucks to assist in loading/unloading during short-staffed timeframes to ensure 98% of deadlines were met.
Top 5 Tips for Your Warehouse Manager Resume
- You know that warehouse operations are fast-paced, with products always moving in and out of the facility. Optimize for success in the fast-paced hiring process by keeping to a one-page resume and concisely presenting your top skills in process improvement and team leadership.
- You’ll want to structure your resume like you would present performance data to company leaders. Keep it organized with clear headers, bullet points with key warehouse metrics, and easily readable 12-14 point font.
- You want to make your examples easy to read during quick reviews. For instance, a short sentence about how you implemented new space-saving techniques in packaging to reduce costs by 33% will go a long way.
- Want to make your management abilities stand out? Always quantify your impact in the examples you list. Anything from boosting storage efficiency to reducing product shrinkage during operations will help you stand out as the right warehouse management candidate.
- Action words like “monitored” or “reduced” will make your top achievements as a warehouse manager sound more engaging. For instance, you could explain how you “reduced product shrinkage during receiving by 47% by implementing new forklift safety procedures.”
Try to get creative about how you showcase your leadership skills. For instance, you could explain how you led a 16-person team during a seasonal distribution operation that resulted in packing and shipping 9,000 products on time ahead of Christmas.
Reverse chronological formatting is the best choice. You want to list your most recent experiences first since they’ll be the most relevant to your current team leadership skills, along with the use of top software like Excalibur WMS, which is frequently updated.
Keep it to three or four jobs. You’ll want to list your most recent positions and those that used the most relevant skills to tasks you’ll perform, like overseeing budgets or managing quality control processes.
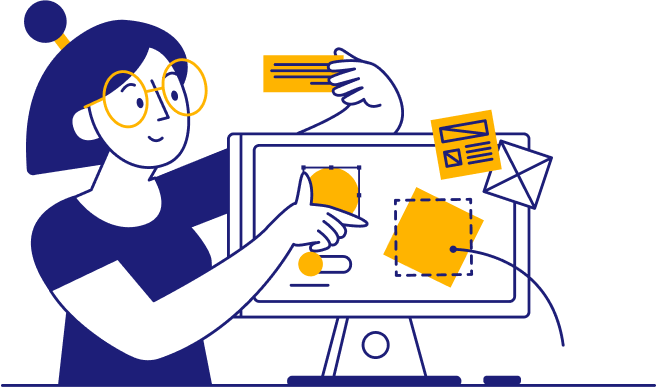

- Career Blog
Warehouse Manager Resume: Sample and Tips for 2024 Success
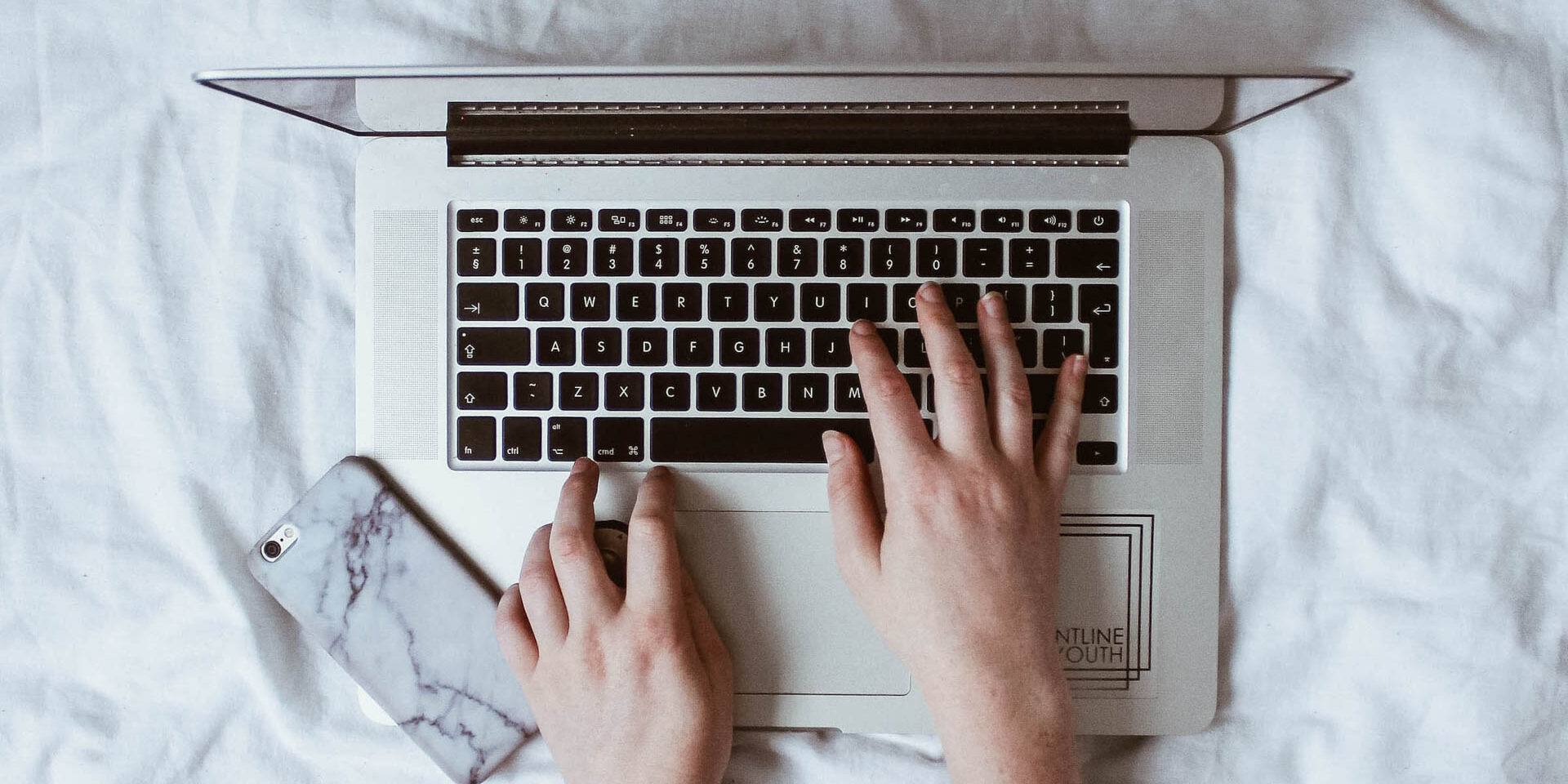
A Warehouse Manager is responsible for overseeing the daily operations of a warehouse, which includes receiving, storing, and distributing goods. They lead teams of workers and ensure that the warehouse is efficient, organized, and safe. Warehouse Managers also handle inventory management, quality control, and customer service.
A strong resume is crucial for Warehouse Manager positions, as it is often the first impression that a hiring manager will have of a candidate. A well-crafted resume can highlight a candidate’s relevant skills and experience, demonstrating their ability to effectively manage a warehouse and lead a team. It can also help candidates stand out amongst a pool of applicants and secure an interview.
Key Qualifications in a Warehouse Manager Resume
When it comes to crafting a winning resume as a warehouse manager, it’s important to highlight the specific qualifications that make you the best candidate for the job. In this section, we’ll discuss the key qualifications you should include on your resume and how to showcase them effectively.
A. Required education and certifications
Most warehouse manager positions require a high school diploma or equivalent, but some employers may prefer or require a bachelor’s degree in business, supply chain management, or a related field. Depending on the industry or company, there may also be specific certifications or licenses required, such as OSHA certifications or forklift operator certifications.
Make sure to clearly list your relevant education and certifications in your resume, including the specific institution where you received your degree, what type of degree it was, and the date of graduation. For certifications, include the certifying organization, the title of the certification, and the date it was earned.
B. Necessary skills and experience
In addition to education and certifications, a warehouse manager must have a strong set of skills and experience to successfully manage warehouse operations. Some of the necessary skills and experience include:

- Leadership and management skills
- Excellent communication skills
- Strong problem-solving and decision-making abilities
- Experience with logistics systems and software
- Knowledge of safety protocols and procedures
- Ability to manage and motivate a team of employees
- Familiarity with inventory management and quality control processes
When highlighting your skills and experience on your resume, focus on specific examples that demonstrate your ability to excel in these areas. For instance, instead of simply stating that you have leadership skills, give an example of how you effectively managed a team to achieve a specific goal.
C. Ability to manage warehouse systems
As a warehouse manager, you’ll be responsible for overseeing the day-to-day operations of all warehouse systems, including inventory management, shipping and receiving, and quality control. You’ll need to have a deep understanding of these systems and be able to lead your team in effectively managing them.
Your resume should highlight your experience with various warehouse systems and software, such as warehouse management systems (WMS), enterprise resource planning (ERP) software, and transportation management systems (TMS). It should also showcase your ability to analyze data and make informed decisions based on that data.
A successful warehouse manager resume should demonstrate your education, certifications, skills, and experience in a way that shows you have the ability to effectively manage warehouse systems and lead a team to success.
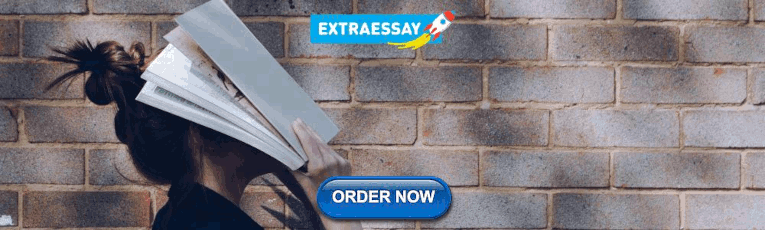
How to Highlight Achievements in your Resume
In order to stand out as a warehouse manager candidate, it’s important to highlight your achievements in your resume. Here are some tips on how to do so effectively.
A. The Importance of Quantifying your Achievements
One of the most effective ways to showcase your accomplishments is to quantify them. This means stating them in measurable terms such as percentages, dollar amounts, or numbers. Quantifying your achievements helps to demonstrate the impact of your work and makes it easier for hiring managers to understand the value you can bring to their organization.
Examples of quantified achievements for warehouse managers might include:
- Increased order fulfillment rate by 20% by implementing a new picking process.
- Reduced inventory costs by 15% through effective stock management practices.
- Saved the company $50,000 by negotiating better shipping rates with vendors.
- Improved warehouse safety record by reducing accidents by 30% through employee training and implementing new safety protocols.
When quantifying your achievements, be sure to include both the magnitude and time frame of the accomplishment. This helps to illustrate the scope of your impact and provides context for your accomplishments.
B. Examples of Accomplishments for Warehouse Managers
As a warehouse manager, your resume should showcase your ability to lead a team and drive operational success. Here are some examples of achievements that could be included in your resume:
- Streamlined warehouse operations, resulting in a 25% reduction in order processing times.
- Improved shipping and receiving times by implementing a new scheduling system, resulting in a 20% decrease in delivery delays.
- Developed and implemented a training program that led to a 10% increase in employee productivity.
- Implemented Lean manufacturing practices, resulting in a 15% reduction in waste and increased efficiency.
- Developed and maintained a strong safety culture, resulting in zero lost time accidents in the warehouse for over a year.
By highlighting these achievements in your resume, you can demonstrate your ability to deliver results and drive success in a warehouse management role. Just be sure to quantify your accomplishments where possible, and provide specific examples of how you have made an impact in your previous roles.
Structure of a Winning Warehouse Manager Resume
If you want to land a job as a warehouse manager, your resume needs to stand out from the competition. One way to achieve this is by structuring your resume in a way that showcases your skills, experience, and achievements effectively. Here are three essential tips for crafting a winning warehouse manager resume:
A. Choose the Right Format
One of the first things you need to consider when creating a resume is the format. There are several different formats to choose from, including chronological, functional, and combination.

A chronological format highlights your work history, starting with your most recent position and working backward. This type of format is best if you have a solid track record of job progression.
A functional format emphasizes your skills and achievements, rather than your work history. This type of format is ideal if you are changing careers or have gaps in your employment history.
A combination format blends elements of both chronological and functional formats. This type of format is suitable if you want to highlight both your work history and your skills.
Choose the format that best suits your background, experience, and the job you are applying for.
B. Organize Your Information Effectively
Once you have chosen the right format, the next step is to organize your information effectively. This means structuring your resume in a way that makes it easy for the hiring manager to find the information they need.
Start by including a brief summary or objective statement at the top of your resume. This should be a short paragraph that summarizes your skills and experience and highlights your most significant achievements.
Next, list your work experience in reverse chronological order, starting with your most recent position. For each job, include a brief description of your responsibilities and highlight your most significant achievements.
Make sure to include any relevant certifications or qualifications, as well as any relevant volunteer work or extracurricular activities.
C. Tips for Choosing the Right Keywords
Finally, one of the most important aspects of a winning warehouse manager resume is choosing the right keywords. Many companies now use applicant tracking systems (ATS) to screen resumes before they are even seen by a human hiring manager. These ATS systems use keywords to filter out resumes that don’t meet the job requirements.
To increase your chances of getting past the ATS screening process, make sure to include relevant keywords throughout your resume. These can include industry-specific terms, technical skills, and job titles.
Take the time to carefully read the job description and tailor your resume to match the keywords and requirements listed in the job posting.
By following these tips and structuring your warehouse manager resume effectively, you can increase your chances of landing the job and achieving success in your career.
Including Technical Skills in a Warehouse Manager Resume
As a Warehouse Manager, ensuring the smooth running of warehouse operations is your primary responsibility. To excel in this role, you need to possess a variety of technical skills that enable you to manage the warehouse effectively. Some of these key technical skills include:
A. Technical abilities needed for the role
Inventory Management: As a Warehouse Manager, you must track inventory levels, analyze data for forecasting, and develop strategies to improve overall inventory management.
Logistics and Supply Chain Management: To ensure timely delivery of goods to customers, you must be able to manage the movement of materials and goods in and out of the warehouse.
Familiarity with Warehouse Management Systems (WMS): A WMS is a critical software tool that enables you to manage and optimize warehouse operations. This includes inventory control, shipping, receiving, and order fulfillment.
Data Analysis: Warehouse operations generate a lot of data. As a Warehouse Manager, you need to be able to analyze this data to make sound decisions about inventory levels, product placement, and supply chain optimization.
B. Examples of technical skills in action
To demonstrate your technical skills on your resume, consider including examples of how you have used these skills in your previous roles.
Inventory Management: “Successfully implemented a new inventory control system that reduced waste and improved inventory accuracy by 20%.”
Logistics and Supply Chain Management: “Managed a team of drivers and warehouse staff to reduce delivery times by 30% and improve customer satisfaction by 15%.”
Warehouse Management Systems (WMS): “Expert in using SAP WMS to streamline warehouse operations, resulting in a 25% reduction in labor costs.”
Data Analysis: “Analyzed warehouse operations data to identify areas for improvement and implemented changes that resulted in a 10% increase in efficiency.”
C. Listing technical abilities on a resume
When including technical skills on your Warehouse Manager resume, ensure they are relevant to the position you are applying for. Use bullet points to outline your technical abilities, and give specific examples of how you have used these skills to benefit your previous employers.
Education and Certifications for Warehouse Managers
Warehouse managers are responsible for overseeing the day-to-day operations of a warehouse, including inventory management, order fulfillment, and shipping and receiving. To be successful in this role, it is important for warehouse managers to have the right education and certifications.
A. Associates, Bachelor’s, and Master’s Degrees for Supply Chain
Education plays a critical role in preparing warehouse managers for their responsibilities. An associate’s degree in supply chain management or logistics can be a good starting point, providing a solid foundation of knowledge and skills around warehouse operations, transportation, and inventory management. A bachelor’s degree in supply chain management or similar field can help warehouse managers take on more responsibilities and advance their careers. A master’s degree in supply chain management, logistics, or business administration can provide the most comprehensive education and set individuals apart from their peers.
B. Certifications for Warehouse Managers
Certifications can also help warehouse managers demonstrate their expertise and knowledge in specific areas. Some valuable certifications for warehouse managers include:
- Certified in Production and Inventory Management (CPIM)
- Certified Supply Chain Professional (CSCP)
- Certified Logistics Professional (CLP)
- Certified Warehousing and Distribution Professional (CWDP)
Obtaining these certifications can show hiring managers that a candidate has a solid understanding of warehouse operations, inventory management, logistics, and other key areas.
C. Hiring Managers Expectations
When it comes to hiring warehouse managers, there are certain expectations that hiring managers have. First and foremost, they want candidates who have a strong understanding of warehouse operations and can manage inventory effectively. Warehouse managers should also be able to work well under pressure, as warehouses can be fast-paced and demanding environments. Strong communication skills are also essential, as warehouse managers must coordinate with other departments, vendors, and customers.
It is also important for warehouse managers to have experience using warehouse management software, such as inventory management systems and shipping software. Familiarity with Lean and Six Sigma methodologies can also be beneficial.
Education and certifications can play a critical role in preparing warehouse managers for their roles. Hiring managers look for candidates with a strong understanding of warehouse operations, inventory management, and communication skills, as well as experience using warehouse management software. Obtaining a degree and certifications can set individuals apart and help them advance their careers in the warehouse management field.
Using Keywords to Optimize your Resume for ATS
Whether you’re applying for a warehouse manager position or any other job, it’s crucial to understand how to make your resume stand out to recruiters and hiring managers. One way to achieve this is by optimizing your resume for applicant tracking systems (ATS).
A. Understanding ATS
ATS is a software tool that many companies use to manage their recruitment process. Essentially, it’s a database that screens resumes before they’re ever seen by a human being. This means that your resume must be ATS-friendly if you want it to be considered for the position you’re applying for.
To ensure that your resume is ATS-friendly, it’s essential to understand how the software works. ATS uses algorithms to scan resumes and identify specific keywords and phrases that are relevant to the job posting. If your resume doesn’t include enough relevant keywords or if they’re not in the right place, the ATS may filter it out, even if you’re a strong candidate for the job.
B. Analyzing job postings for relevant keywords
The next step in optimizing your resume for ATS is to analyze the job posting and identify relevant keywords. Pay attention to how the company describes the position and what qualifications they’re looking for in a candidate. Look for any specific skills or experience that are mentioned multiple times and make a note of them.
It’s also a good idea to research the company’s industry and their competitors. Identify industry-specific jargon or buzzwords that may be relevant to the position.
Once you’ve identified the keywords, be strategic about where you place them in your resume. Place relevant keywords in the job title, summary, and work experience sections.
C. Incorporating keywords into your resume
When incorporating keywords into your resume, avoid stuffing them in unnaturally. Instead, focus on using them in a way that demonstrates your relevant skills and experience.
For example, instead of simply listing a keyword like “logistics” in your skills section, emphasize how you have implemented strong logistics strategies to drive efficiency and reduce costs.
Also, use synonyms and variations of the keywords to ensure that you’re covering all possible variations of the word. For instance, if the job posting mentions “supply chain management,” also include “SCM” in your resume.
Incorporating keywords into your resume takes time and effort, but it’s worth it to ensure that your application makes it past the ATS and into the hands of a hiring manager. By doing so, you increase your chances of being invited for an interview and ultimately landing your dream warehouse manager job.
Importance of Tailoring your Resume for the Position
When it comes to applying for a warehouse manager position, it is crucial to tailor your resume specifically to the job. This can significantly increase your chances of getting noticed by the hiring manager and landing the job. Here are three important steps to take:
A. Studying the job description before writing the resume
Before crafting your resume, take the time to thoroughly study the job description. This can provide insights into the responsibilities, requirements, and qualifications that the employer is seeking. By understanding these aspects of the job, you can better tailor your resume to showcase how you meet those needs. This is also a great opportunity to incorporate specific keywords and phrases into your resume that align with the job description.
B. Highlighting transferable skills
One way to stand out as a strong candidate for a warehouse manager position is to highlight your transferable skills. These are skills that you have developed in a previous role or experience that can be applied to the new position. For example, if you have experience managing a team in a different industry, that leadership and communication expertise can be valuable in a warehouse setting as well. By effectively showcasing your transferable skills, you can demonstrate your unique value to the employer.
C. Addressing gaps in employment or experience
If you have gaps in your employment history or experience that could be seen as a drawback for the warehouse manager position, it is important to address them in your resume. This can be done by highlighting any relevant volunteer work or continuing education courses you have completed during those gaps. Alternatively, you can focus on how the skills and experience you do have are relevant and valuable for the position, despite any gaps in your work history.
Tailoring your resume to the warehouse manager position is an essential step in standing out as a strong candidate. By studying the job description, highlighting transferable skills, and addressing gaps in employment or experience, you can effectively showcase your unique value to the employer and increase your chances of success.
Examples of Highly Effective Warehouse Manager Resumes
Here are three examples of highly effective warehouse manager resumes with explanations for each section:
Resume example #1
Name and Contact Information:
Include your full name, phone number, email address, and city and state where you reside.
Your objective statement should clearly state your purpose and career goals. Make sure it is concise and specific, and aligns with the position you are applying for.
Your summary should provide an overview of your skills and experience, and how they are relevant to the position you are applying for. This section should be brief, no more than three to four sentences.
List relevant skills that demonstrate your ability to excel in the role of a warehouse manager, such as inventory management, team leadership, logistics, and safety compliance.
Professional Experience:
List your professional experience in reverse chronological order, starting with your most recent or current position. For each job, include your job title, the name of the company, the dates you worked there, and your key responsibilities and achievements.
Education and Certifications:
Include your educational qualifications and any relevant certifications you hold, such as OSHA, Six Sigma, or Lean Six Sigma.
Resume example #2
Professional Summary:
Your professional summary should highlight your overall work experience, specific skills and abilities and how they can benefit the company. It should be brief, no more than three to four sentences.
List your most recent work experience first, including your job title, the name of the company, duration of employment and your key responsibilities and achievements. Quantify your accomplishments and provide specific details to show your impact.
List your core skills such as inventory management, logistics, team leadership, and safety compliance. Include any technical skills, such as experience with warehouse management software.
List your highest completed education credential and the institution that you attended.
Resume example #3
Write a three to four sentence statement that summarizes your experience and skills as related to the warehouse management profession. Personalize this statement to the company and/or job you are applying for.
List your professional experience in reverse chronological order. Include the name of the company, job title, and dates of employment. Focus on achievements and successes that demonstrate how you effectively managed warehouse operations.
List technical and transferable skills that demonstrate your ability to manage a warehouse, such as inventory control, team management, problem-solving and data analysis.
Common Mistakes to Avoid in a Warehouse Manager Resume
When it comes to creating a warehouse manager resume, there are a few common mistakes that can hinder your chances of success. In particular, there are three mistakes that you should avoid at all costs: using clichés or generic phrases, not quantifying achievements, and making typos or grammatical errors.
A. Using clichés or generic phrases
One of the biggest mistakes that warehouse managers make in their resumes is using clichés or generic phrases. These may seem like easy and straightforward ways to describe your skills and qualifications, but they do little to set you apart from other candidates.
When you use generic phrases like “detail-oriented,” “team player,” or “strong communicator,” you’re not providing any specific information about your experience or abilities. Instead of using these overused phrases, try to be more specific about your achievements and responsibilities. For example, instead of saying you’re a “team player,” describe a time when you successfully collaborated with a team to achieve a specific goal.
B. Not quantifying achievements
Another mistake that can hurt your warehouse manager resume is not quantifying your achievements. This means failing to provide specific numbers or metrics to demonstrate your impact in previous roles. When you quantify your achievements, you provide concrete evidence of your skills and abilities, which can make you a more attractive candidate.
For example, instead of simply stating that you “improved warehouse efficiency,” try to quantify your impact by saying something like, “Implemented new processes that reduced order processing time by 25%.”
C. Typos or grammatical errors
Finally, it’s crucial to avoid typos or grammatical errors in your warehouse manager resume. These mistakes can make you appear careless or unprofessional, which can hurt your chances of landing the job. Be sure to carefully proofread your resume multiple times and consider asking a friend or colleague to review it as well.
Creating a successful warehouse manager resume requires careful attention to detail and a focus on specific achievements and qualifications. Avoiding these common mistakes can help you stand out from other candidates and increase your chances of success.
Tips for Writing a Cover Letter for Warehouse Manager Position
As you apply for a Warehouse Manager position, it’s important to have a well-written, compelling cover letter to accompany your resume. Your cover letter should showcase your skills and experience, demonstrate your enthusiasm for the role, and set you apart from other candidates. Here are some tips to help you craft an effective cover letter that will impress potential employers.
A. Purpose of a cover letter
The main purpose of a cover letter is to introduce yourself to the hiring manager and explain why you are a great fit for the position. In the case of a Warehouse Manager role, your cover letter should highlight your experience managing inventory, coordinating logistics and supervising staff. Your cover letter should also include your key achievements in your past roles, especially those that align with the requirements of the job.
B. Formatting and content of a cover letter
Your cover letter should be one page or less and should be broken up into three sections: opening paragraph, summary paragraph, and closing paragraph. In the opening paragraph, you should introduce yourself and express your enthusiasm for the position. In the summary paragraph, you should highlight your qualifications and explain why you are the best fit for the job. Finally, in the closing paragraph, you should thank the hiring manager for their time and express your interest in scheduling an interview.
When it comes to the content of your cover letter, make sure to use specific examples and data to demonstrate your qualifications. Use language that is clear, concise, and assertive, and avoid cliches or empty statements.
C. Examples of cover letters for Warehouse Managers
Here are some examples of effective cover letters for Warehouse Manager positions:
Dear [Hiring Manager],
As soon as I saw the job posting for the Warehouse Manager position at [Company], I knew I had to apply. With over 5 years of experience in warehouse management, I’m confident that I have the skills and expertise necessary to excel in this role.
One of my proudest achievements in my previous role as Warehouse Supervisor was implementing a new inventory tracking system that resulted in a 20% decrease in inventory loss. I’m also skilled in staff management and scheduling, and have experience coordinating logistics across multiple locations.
I’d love the opportunity to discuss my qualifications further and learn more about this exciting opportunity. Thank you for your time and consideration.
Sincerely, [Your Name]
I’m excited to apply for the Warehouse Manager position at [Company], as I believe my skills and experience make me a strong fit for this role. With 7 years of experience in warehouse management, I’ve developed a deep understanding of logistics and inventory management.
In my previous role at [Company], I implemented a new performance measurement system that helped increase efficiency by 15%. I’m also skilled in managing and training staff, and am committed to maintaining a safe and productive work environment.
Related Articles
- Forklift Operator: Job Description, Salary, and Skills
- Event Specialist: Job Description and Responsibilities
- Cardiologist Career Overview & Opportunities for 2023
- Soft Skills: What Are They? [2023 Edition]
- Navigating Salary Expectations in Job Applications in 2023
Rate this article
0 / 5. Reviews: 0

More from ResumeHead
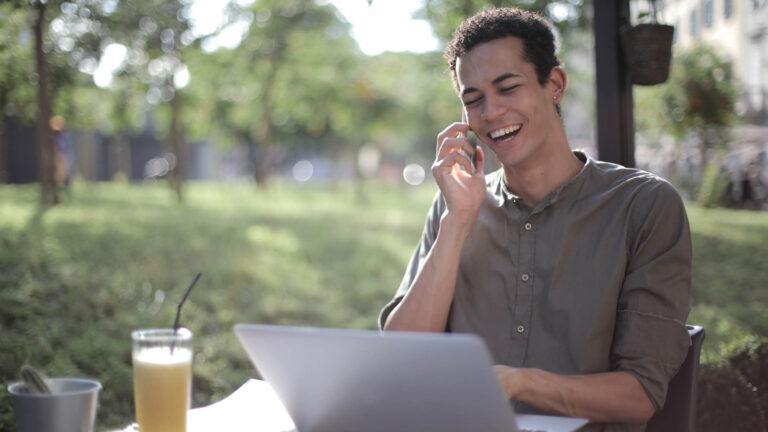
- Resume Builder
- Resume Templates
- Resume Formats
- Resume Examples
- Cover Letter Builder
- Cover Letter Templates
- Cover Letter Formats
- Cover Letter Examples
- Career Advice
- Interview Questions
- Resume Skills
- Resume Objectives
- Job Description
- Job Responsibilities
- FAQ’s
Warehouse Manager Resume Examples
A strong resume is essential for job seekers looking to secure a warehouse manager position. Writing a good resume requires an understanding of the job and a clear idea of what you have to offer. This guide will provide you with a well-crafted warehouse manager resume writing template and examples to help you create a resume that best promotes your experience and qualifications. With the right approach and guidance, you can create a resume that stands out from the competition and puts you in a better position to land the job.
If you didn’t find what you were looking for, be sure to check out our complete library of resume examples .
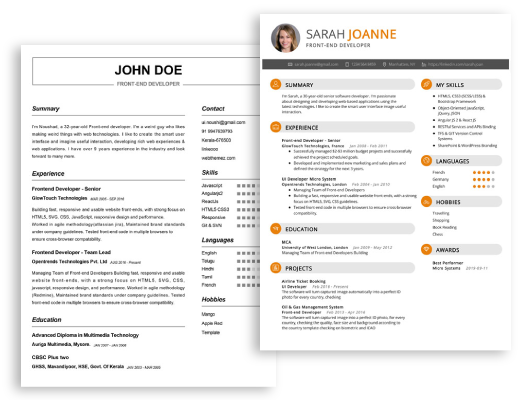
Start building your dream career today!
Create your professional resume in just 5 minutes with our easy-to-use resume builder!
Warehouse Manager
123 Main Street | Anytown, USA 99999 | Phone: (123) 456-7890 | Email: [email protected]
A highly organized and detail- oriented warehouse manager with 5+ years of experience in logistics and inventory management. Adept at working with staff to create productive and efficient warehouse operations, and to ensure accurate inventory of goods and services. Experienced in managing staff, scheduling shifts, and overseeing cycle counts.
Core Skills :
- Logistics/Inventory Management
- Warehouse/Distribution Center Operations
- Staff Supervision
- Time Management
- Quality Control/Safety
- Problem Solving
- Teamwork/Leadership
- Documentation/Data Entry
Professional Experience :
Eagle Logistics – Warehouse Manager, 2016- Present
- Manage the activities of staff to ensure the efficient and cost- effective operation of the warehouse
- Train, motivate, and evaluate warehouse personnel, and assign duties to promote efficient workflow
- Maintain accurate records of inventory and materials, both electronically and on paper
- Monitor warehouse operations to ensure compliance with company policies, procedures, and safety regulations
- Ensure all schedules and deadlines are met and orders are fulfilled accurately
- Assess and resolve issues related to warehouse operations, staffing, and safety
ABC Logistics – Warehouse Supervisor, 2013- 2016
- Supervised staff and oversaw all warehouse operations, including receiving, shipping, storage, and distribution
- Developed and enforced warehouse policies and procedures
- Promoted safety in the workplace and ensured all safety regulations were followed
- Coordinated and scheduled staff and managed inventory levels
- Facilitated communications between staff and management, ensuring issues and concerns were addressed
Education : Bachelor of Science in Logistics and Supply Chain Management, ABC University, 2013
Create My Resume
Build a professional resume in just minutes for free.
Warehouse Manager Resume with No Experience
A highly motivated and detail- oriented individual with a strong desire to learn and grow in the warehouse management field. Possesses excellent organizational and communication skills, coupled with a passion for helping others. Desires to obtain a warehouse manager position to demonstrate the ability to streamline operations and increase efficiency.
- Strong organizational and communication skills
- Ability to work independently and in a team environment
- Proficient in Microsoft Office programs (Word, Excel, PowerPoint)
- Knowledge of basic warehouse safety
- Knowledge of inventory management systems
Responsibilities :
- Maintaining warehouse operations by organizing and controlling inventory
- Monitoring stock levels and making necessary adjustments
- Assisting in the selection and training of warehouse employees
- Preparing and submitting reports on inventory and warehouse operations
- Ensuring compliance with company policies and procedures
- Ensuring proper maintenance of warehouse equipment and supplies
Experience 0 Years
Level Junior
Education Bachelor’s
Warehouse Manager Resume with 2 Years of Experience
Highly organized and extremely dedicated Warehouse Manager with 2 years of professional experience. Possesses an up- to- date knowledge of inventory control procedures, stocking techniques and OSHA regulations. Skilled in data entry, shipping and receiving, and supervising a team of 10 warehouse employees. Committed to providing excellent customer service and creating an efficient and safe warehouse environment.
- Supervisory Experience
- Inventory Control
- OSHA Compliance
- Stocking and Shipping
- Safety Procedures
- Organizational Skills
- Customer Service
- Supervised and trained 10 warehouse staff in safety procedures, product knowledge and inventory control.
- Assisted in the design and implementation of new warehouse operations.
- Maintained a safe and clean environment in accordance with OSHA regulations.
- Monitored and updated inventory levels on a daily basis.
- Ensured accuracy and quality of delivered products.
- Maintained accurate and up- to- date records of orders, shipments and deliveries.
- Coordinated with other departments to ensure on- time delivery of products.
- Identified and resolved issues that arise during warehouse operations.
- Collaborated with sales staff to ensure customer satisfaction.
Experience 2+ Years
Warehouse Manager Resume with 5 Years of Experience
Highly experienced Warehouse Manager with more than 5 years of experience managing the day- to- day operations of busy warehouses. Adept at coordinating teams of workers and maintaining inventory accuracy. Expert in merchandise control and inspections, as well as supervising loading and unloading of goods. Experienced in implementing best practices to increase efficiency and reduce costs.
- Inventory Management
- Vendor Management
- Personnel Management
- Distribution Systems
- Quality Assurance
- Product Scheduling
- Process Improvement
- Safety Protocols
- Managing day- to- day warehouse operations including personnel, inventory and distribution
- Supervising and coordinating the loading and unloading of goods
- Monitoring employee performance and providing feedback
- Utilizing lean principles to identify and implement process improvements for increased efficiency
- Developing and enforcing safety protocols to ensure a safe working environment
- Maintaining accurate inventory levels and quality control of goods
- Developing and managing vendor relationships to ensure timely delivery of goods
- Developing product schedules to meet customer demands and maximize warehouse utilization
Experience 5+ Years
Level Senior
Warehouse Manager Resume with 7 Years of Experience
Highly motivated and organized Warehouse Manager with over 7 years of experience in warehouse operations. Possess excellent multitasking skills, the ability to prioritize tasks, and a comprehensive understanding of all warehouse management processes. Possess excellent communication and problem- solving abilities, and a strong commitment to creating a safe and efficient work environment.
- Knowledge of warehouse operations
- Understanding of inventory management systems and processes
- Office software proficiency
- Ability to lift heavy loads
- Excellent communication, organizational, and problem- solving skills
- Ability to work both independently and collaboratively
- Expertise in leading, training, and motivating staff
- Ability to troubleshoot and find solutions
- Oversee daily operations of the warehouse, including monitoring staff performance, maintaining inventory levels, and ensuring safety and security
- Develop and implement warehouse management strategies to maximize efficiency
- Monitor and analyze warehouse data to identify and address any issues that may arise
- Develop and enforce safety and quality standards for staff, visitors, and goods
- Monitor inventory levels to ensure accuracy and prompt delivery of goods
- Maintain a log of all goods coming in and out of the warehouse
- Establish and manage effective relationships with suppliers and vendors
- Train and motivate staff to achieve warehouse goals and objectives
- Manage and coordinate all warehouse staff to ensure all tasks are completed in a timely and efficient manner.
Experience 7+ Years
Warehouse Manager Resume with 10 Years of Experience
An experienced Warehouse Manager with 10 years of expertise in warehouse operations and logistics management. Highly experienced in inventory and quality control, supply chain management, and customer service. Proficient in national and international logistics, staff training, and strategic planning. Committed to cost effective and efficient operations to drive exceptional customer service and business growth.
- Logistics Management
- Inventory & Quality Control
- Supply Chain Management
- Strategic Planning
- Staff Training
- Cost Optimization
- Developed and implemented logistics strategies that increased productivity and improved customer service
- Managed warehouse operations, including staff training, inventory control, and quality assurance
- Developed and implemented warehouse policies, procedures, and systems to ensure accuracy and efficiency
- Monitored stock levels and reordered supplies as needed
- Analyzed data to identify areas for improvement and cost optimization
- Ensured compliance with safety regulations and company policies
- Collaborated with various departments to ensure successful order fulfillment
- Coordinated with vendors and suppliers to ensure timely delivery of goods
Experience 10+ Years
Level Senior Manager
Education Master’s
Warehouse Manager Resume with 15 Years of Experience
Warehouse Manager with 15 years of experience and expertise in logistics, inventory control, and asset management. A passionate team player with excellent organizational and problem- solving skills who is highly skilled in overseeing all aspects of day- to- day warehouse operations. Possesses strong leadership capabilities to direct, motivate, and mentor staff, while also possessing excellent communication skills to maintain positive relationships with vendors and customers alike.
- Warehouse Management
- Asset Management
- Forklift Operation
- Communication
- Managed the day- to- day warehouse operations and supervised warehouse staff.
- Deployed efficient logistics and inventory control systems to ensure accuracy and cost- effectiveness.
- Oversaw the receiving, stocking, and shipping of both incoming and outgoing products.
- Monitored warehouse inventory levels and placed orders as needed.
- Ensured the timely delivery of orders and ensured the proper handling and storage of goods.
- Managed the maintenance and upkeep of warehouse equipment and assets.
- Trained and supervised new warehouse staff.
- Developed and implemented quality assurance measures to ensure the safe and efficient operation of the warehouse.
- Implemented safety protocols to maintain a safe and hazard- free working environment.
Experience 15+ Years
Level Director
In addition to this, be sure to check out our resume templates , resume formats , cover letter examples , job description , and career advice pages for more helpful tips and advice.
What should be included in a Warehouse Manager resume?
A Warehouse Manager is responsible for managing the day-to-day operations of a warehouse and overseeing workflow. To make a successful Warehouse Manager resume, you must include your experience in inventory control, shipping and receiving, and handling of materials. Here are some other details to include in your Warehouse Manager resume:
- Work Experience: Include a section that lists your previous jobs and the roles you held. Be sure to include how long you held each role and the specific accomplishments you achieved in each role.
- Education: List your relevant degrees, certifications or diplomas in this section.
- Skills: Include a section that highlights the technical skills you possess such as knowledge of computer systems, advanced warehouse software, and familiarity with safety protocols.
- Leadership: Summarize any experiences or accomplishments in which you demonstrated leadership skills.
- Interpersonal Skills: List any experiences that demonstrate your ability to work well with others and interact effectively with customers and staff.
- Organizations: If you are a member of any professional associations, include them here.
By including this information in your resume, you will be better positioned to land a job as a Warehouse Manager. Be sure to craft your resume in a way that will be attractive to potential employers and highlight the experience and skills needed for the job.
What is a good summary for a Warehouse Manager resume?
A Warehouse Manager resume should provide a concise summary of the candidate’s ability to optimize warehouse operations, manage staff, and ensure efficiency. It should emphasize the candidate’s organizational and communication skills, problem-solving abilities, and experience with inventory and distribution. The summary should also showcase the individual’s track record of improving operations, increasing efficiency, and developing successful teams. Additionally, the summary should demonstrate the candidate’s core competencies relevant to warehouse management, including knowledge of safety regulations and the ability to quickly adjust to changing operations. Ultimately, the summary should convince the reader that this is the ideal candidate for the job.
What is a good objective for a Warehouse Manager resume?
A Warehouse Manager is responsible for overseeing the day-to-day operations of the warehouse, such as staff management, order fulfillment, inventory control, and safety regulations. A good objective for a Warehouse Manager resume should focus on these key areas of responsibility. Here are some potential objectives for a Warehouse Manager resume:
- To use my strong organizational and management skills to ensure efficient and effective operations of the warehouse
- To implement innovative inventory control methods that increase productivity and accuracy
- To ensure compliance with industry standards and safety regulations
- To develop and maintain excellent relationships with vendors and customers
- To motivate and mentor warehouse staff, ensuring the highest quality of customer service
- To monitor and track warehouse performance metrics, providing timely and relevant data to management
- To create and implement cost-saving strategies that reduce expenses and increase efficiency
- To utilize my knowledge and experience to provide optimal warehouse management and ensure customer satisfaction.
How do you list Warehouse Manager skills on a resume?
Warehouse Managers are responsible for overseeing the day-to-day operations of warehouses. They are tasked with maintaining the safe and efficient running of warehouses, as well as handling the organizational and administrative side of the job. As such, employers look for candidates who possess the right skill set and experience to successfully manage the warehouse.
If you are applying for a Warehouse Manager role, your resume should include a section that highlights the relevant skills and experience that make you a good fit for the job. Here are some of the most common skills and qualifications to include in your Warehouse Manager resume:
- Leadership: Warehouse Managers are responsible for leading a team of employees and ensuring that they are working efficiently and collaboratively. Highlight any managerial experience you have and demonstrate your ability to motivate and manage a team.
- Organizational Skills: Warehouse Managers must be able to stay organized and plan ahead to ensure that warehouses run efficiently. Showcase your organizational skills by highlighting any experience you have in planning and coordinating activities.
- Inventory Management: Warehouse Managers must be able to keep track of inventory and manage stock levels. Showcase any relevant experience in inventory management and demonstrate your ability to accurately track and monitor stock.
- Problem-Solving: Warehouse Managers must be able to solve problems quickly and efficiently. Showcase any problem-solving experience you have and demonstrate your ability to think on your feet and make decisions.
- Computer Skills: As technology advances, many warehouses are beginning to rely on computerized systems to manage inventory and other tasks. Include any experience you have with relevant software and hardware, such as WMS (Warehouse Management Systems) and scanners.
- Safety Knowledge: Warehouse Managers must be aware of all safety regulations and procedures in order to keep employees and warehouses safe. Demonstrate your knowledge of safety regulations by highlighting any relevant certifications or experience you have.
By highlighting the above skills
What skills should I put on my resume for Warehouse Manager?
A Warehouse Manager is a critical role in any organization, responsible for overseeing the efficient receipt, storage, and dispatch of a range of goods. When applying for a Warehouse Manager role, it is important to demonstrate that you possess the skills and qualifications necessary to excel in the role. Here are some of the skills you should consider putting on your resume for a Warehouse Manager role:
- Knowledge of Inventory Management: Warehouse Managers need to understand the principles and techniques of inventory management, including planning, organizing, controlling, and scheduling.
- Leadership and Team Management: Warehouse Managers need to be able to motivate and lead a team of workers to ensure that tasks are completed efficiently and effectively.
- Problem-Solving Skills: Warehouse Managers need to be able to quickly identify and address any issues that arise in the warehouse, and come up with creative solutions.
- Time Management: Warehouse Managers need to be able to prioritize tasks and manage their time in order to ensure that tasks are completed on time and to the highest standards.
- Knowledge of Warehouse Systems and Equipment: Warehouse Managers need to understand the equipment and systems used in the warehouse, and be able to effectively use them to maximize efficiency.
- Attention to Detail: Warehouse Managers need to be highly detail-oriented, as even small mistakes can lead to costly delays and disruptions.
- Communication Skills: Warehouse Managers need to be able to communicate effectively with workers, suppliers, and customers.
By including these skills on your resume, you can show hiring managers that you have what it takes to be a successful Warehouse Manager.
Key takeaways for an Warehouse Manager resume
The warehouse manager role is an important one in any organization, and having a strong resume is essential to landing the job. To ensure your resume stands out, here are a few key takeaways to consider:
- Highlight your safety and compliance knowledge: Warehouse managers must have an in-depth understanding of OSHA regulations and the ability to maintain a safe and compliant warehouse environment. Be sure to highlight any key certifications or qualifications related to safety and compliance.
- Demonstrate your knowledge of inventory management systems: Warehouse managers must be proficient in inventory management systems, such as WMS and ERP. Highlight any experience you have with these systems, as well as any other relevant software or tools you have used.
- Showcase your problem-solving skills: Warehouse managers must be able to quickly identify and resolve any problems that arise in the warehouse. Detail any successes you have had in problem solving, and any strategies you have used to improve efficiency or reduce costs.
- Demonstrate your leadership abilities: Warehouse managers need to be able to manage multiple teams and ensure all tasks are completed on time. Detail any managerial or leadership roles you have had in the past and provide examples of how you have motivated and organized teams.
By highlighting these key takeaways in your warehouse manager resume, you can ensure that your resume stands out from the competition. Good luck!
Let us help you build your Resume!
Make your resume more organized and attractive with our Resume Builder
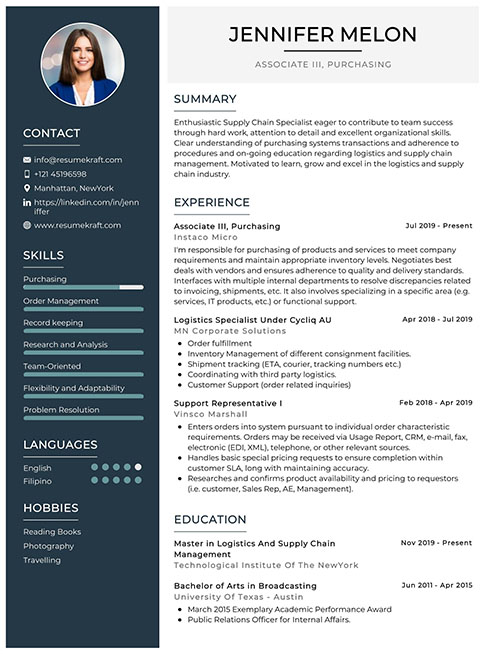
- • Overhauled inventory management system, reducing on-hand inventory costs by 20% while ensuring 99% order accuracy across multiple SKUs.
- • Implemented a forklift training program, certifying 30+ employees and enhancing workplace safety.
- • Managed national and international ecommerce order processing, resulting in a 15% year-over-year increase in customer satisfaction rates.
- • Spearheaded the integration of UPS and FedEx shipping systems, enhancing tracking capabilities and reducing average shipping times by 25%.
- • Controlled the operations for two busy warehouses, coordinating a team of 50+ to ensure seamless daily activities.
- • Developed comprehensive reporting mechanisms that improved decision-making for stock replenishment and resource allocation.
- • Managed daily operations for shipping and receiving, increasing throughput by 30% within the first year.
- • Reduced inventory discrepancies by 40% through the implementation of a new inventory tracking system.
- • Directed ecommerce order fulfillment, achieving a 98% on-time shipping rate.
- • Coordinated with multiple customers and SKUs to enhance order processing efficiency.
- • Fostered an environment of continuous team engagement and development, leading to a 10% decrease in staff turnover.
- • Led a team of 20+ in inventory management, successfully handling over 5,000 SKUs.
- • Innovated reporting techniques that produced a 15% reduction in overstocked items.
- • Oversaw a system upgrade that improved stock check efficiency by 35%.
- • Improved layout and workflow of the warehouse, boosting worker productivity by 20%.
5 Warehouse Operations Manager Resume Examples & Guide for 2024
Your warehouse operations manager resume should clearly demonstrate your ability to efficiently manage inventory and logistics. Highlight your experience with warehouse management systems and your ability to optimize storage solutions. Additionally, ensure your resume showcases your strong leadership skills and proven track record of improving operational workflows. Detail your experience in training staff, overseeing safety protocols, and implementing cost-reduction strategies to solidify your expertise.
All resume examples in this guide
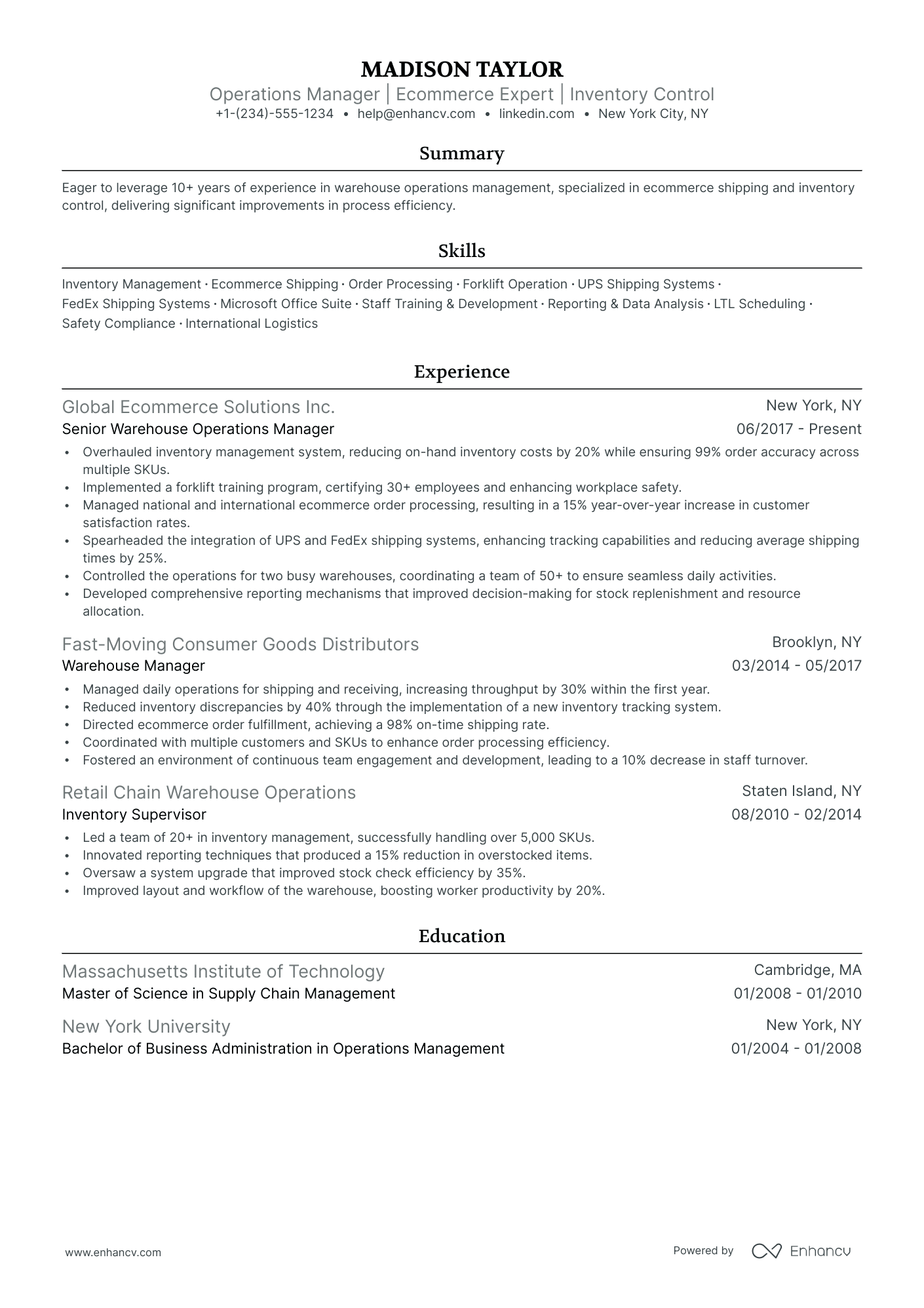
Traditional
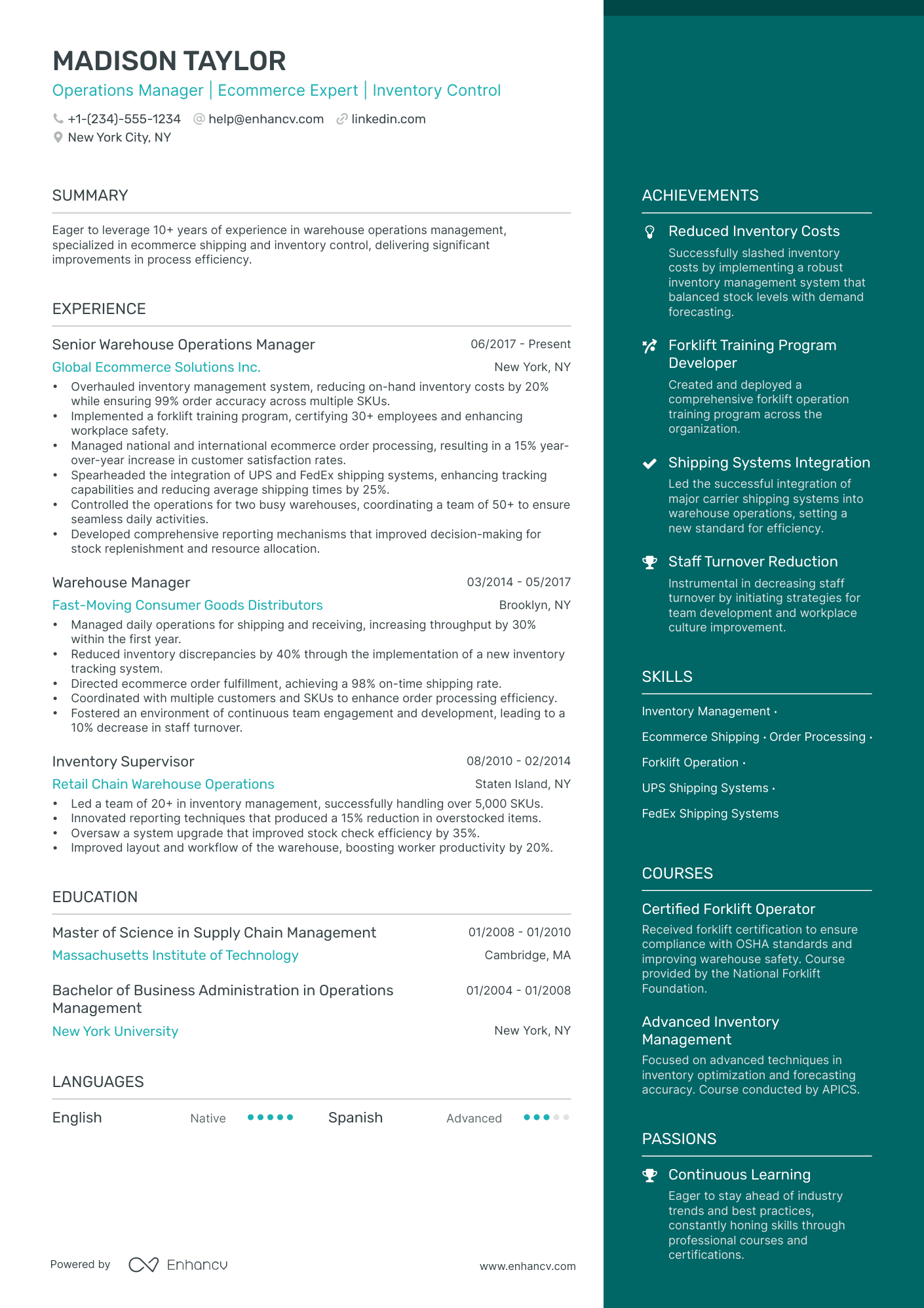
Resume Guide
Resume Format Tips
Resume Experience
Skills on Resume
Education & Certifications
Resume Summary Tips
Additional Resume Sections
Key Takeaways
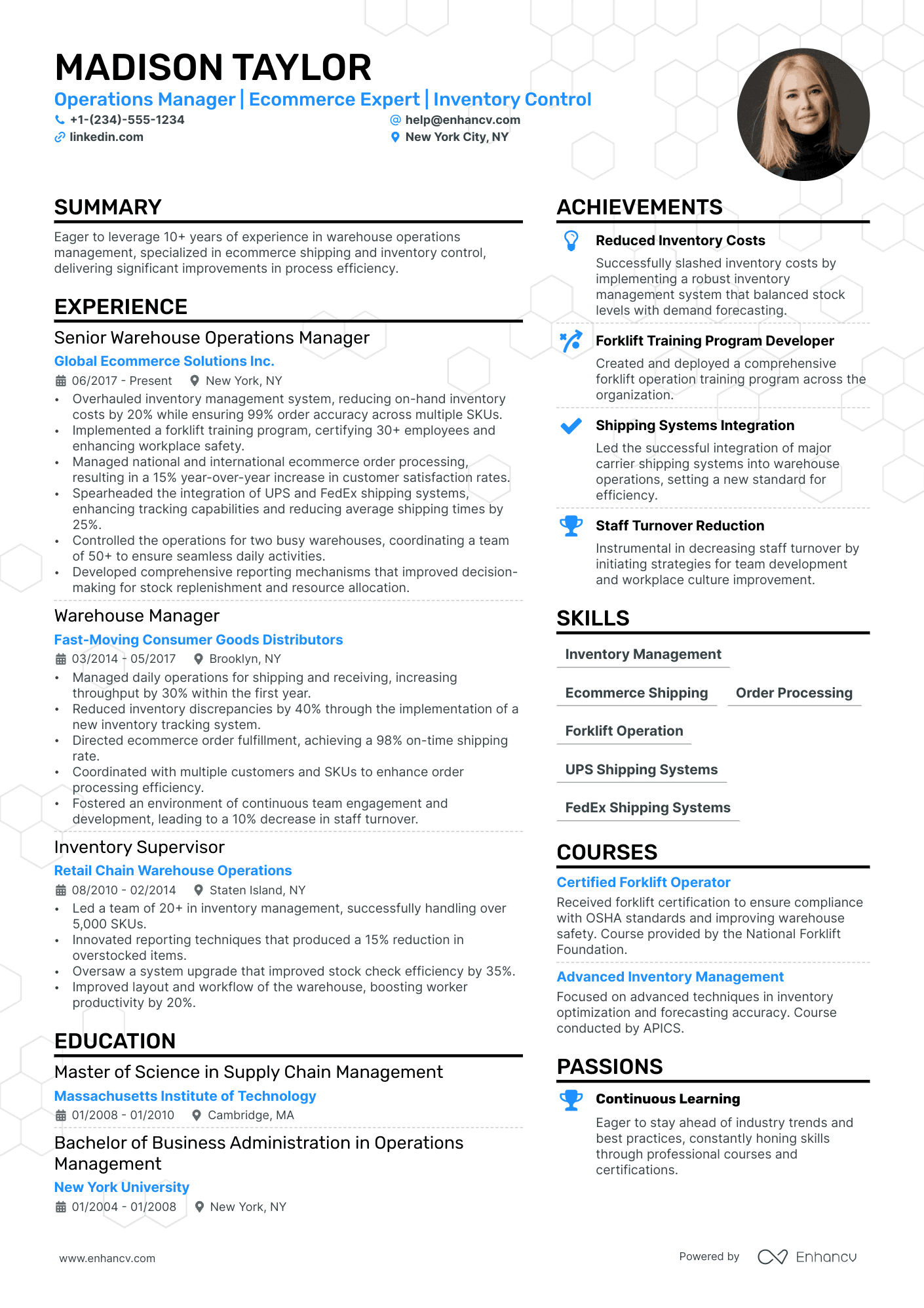
As a warehouse operations manager, one specific resume challenge you may face is effectively demonstrating your ability to streamline processes to increase efficiency and reduce costs. Our guide offers tailored strategies and language tips to help you succinctly convey your achievements and the impact of your management skills, ensuring your resume stands out to potential employers.
- Which sections do you need to include in your resume to meet recruiters' requirements;
- How to write your warehouse operations manager resume experience section - even if you have don't have little to no work experience;
- Real-life professional examples to guide you how to write the most important warehouse operations manager resume sections;
- Adding even more sections so your warehouse operations manager resume stands out with professionalism and your personality.
We've also selected some of the best (and most relevant) resume guides for the warehouse operations manager role you're applying for:
- Shift Manager Resume Example
- Category Manager Resume Example
- Venue Manager Resume Example
- Agile Business Analyst Resume Example
- Strategy Consultant Resume Example
- Healthcare Operations Manager Resume Example
- Servicenow Business Analyst Resume Example
- Hotel Operations Manager Resume Example
- Commodity Manager Resume Example
- Configuration Manager Resume Example
Creating the best warehouse operations manager resume format: four simple steps
The most appropriate warehouse operations manager resume format is defined by precision and a systematic approach. What is more, it should reflect upon how your application will be assessed by recruiters. That is why we've gathered four of the most vital elements to keep in mind when designing your resume:
- It's all about presenting how your experience or skills align with the job. Use the reverse-chronological resume format , if your expertise is relevant to the warehouse operations manager role. Otherwise, select the functional skill-based resume format or the hybrid resume format to shift the focus to your skill set.
- Resume header - make sure you've filled out all relevant (and correct) information, like your contact details and link to your portfolio.
- Resume length - unless you've over a decade of applicable expertise in the field, stick with a one-page resume format. If you'd like to present more of your professional experience, go up to two pages.
- Resume file - submit your warehouse operations manager resume in a PDF format to ensure all information stays in the same place.
Upload & Check Your Resume
Drop your resume here or choose a file . PDF & DOCX only. Max 2MB file size.
List your educational qualifications and certifications in reverse chronological order.
Warehouse Operations Manager resume sections to answer recruiters' checklists:
- Header to help recruiters quickly allocate your contact details and have a glimpse over your most recent portfolio of work
- Summary or objective to provide an overview of your career highlights, dreams, and goals
- Experience to align with job requirements and showcase your measurable impact and accomplishments
- Skills section/-s to pinpoint your full breadth of expertise and talents as a candidate for the Warehouse Operations Manager role
- Education and certifications sections to potentially fill in any gaps in your experience and show your commitment to the industry
What recruiters want to see on your resume:
- Proven experience in warehouse management, including inventory control, order fulfillment, and distribution processes.
- Proficiency in warehouse management systems (WMS) and other industry-related software.
- Demonstrable skills in leadership and team management to effectively oversee warehouse personnel.
- Knowledge of health and safety regulations specific to warehouse operations.
- Experience with logistics and supply chain management, ensuring the efficient flow of goods in and out of the warehouse.
Advice for your warehouse operations manager resume experience section - setting your application apart from other candidates
Your resume experience section needs to balance your tangible workplace achievements with job requirements.
The easiest way to sustain this balance between meeting candidate expectations, while standing out, is to:
- Select really impressive career highlights to detail under each experience and support those with your skills;
- Assess the job advert to define both the basic requirements (which you could answer with more junior roles) and the more advanced requirements - which could play a more prominent role through your experience section;
- Create a separate experience section, if you decide on listing irrelevant experience items. Always curate those via the people or technical skills you've attained that match the current job you're applying for;
- Don't list experience items from a decade ago - as they may no longer be relevant to the industry. That is, unless you're applying for a more senior role: where experience would go to demonstrate your character and ambitions;
- Define how your role has helped make the team, department, or company better. Support this with your skill set and the initial challenge you were able to solve.
Take a look at how real-life warehouse operations manager professionals have presented their resume experience section - always aiming to demonstrate their success.
- Directed a team of 50+ staff in the end-to-end warehouse operations, driving a 30% increase in efficiency through the implementation of a new WMS.
- Successfully negotiated a 10% cost reduction in shipping contracts with major carriers, thereby bolstering profit margins.
- Led the establishment of a cross-docking system that reduced average inventory holding times by 25%, thus enhancing product turnover rates.
- Overhauled the warehouse layout using lean principles, improving the picking routes and reducing order assembly times by 15%.
- Developed a comprehensive employee training program that improved retention by 20% and increased productivity by 35%.
- Implemented an IoT-based asset tracking system, decreasing lost inventory incidents by 40% through real-time monitoring.
- Managed all facets of warehouse operations, spearheading a team-building initiative that cut overtime costs by 20% while elevating morale.
- Championed a zero-accident workplace initiative for 2 years straight, by fostering strict adherence to safety protocols and continuous training.
- Collaborated with the procurement department to align purchasing with inventory needs, substantially reducing overstock by 22%.
- Strategically managed an average of 2000 SKUs, resulting in a perfect delivery record for Q4 2019 through optimized inventory control.
- Introduced RF scanning technology which increased the accuracy of shipments to 99.8%, positively impacting customer satisfaction.
- Coordinated with sales and marketing teams to ensure the warehouse's alignment with seasonal promotional strategies, enhancing the on-time shipping rate by 15%.
- Spearheaded a successful inventory reconciliation project that accounted for previously misplaced stock valued at over $500,000.
- Initiated a successful program to cross-train employees in multiple roles, increasing workforce flexibility and filling a 10% labor gap during peak seasons.
- Integrated sustainable practices into warehouse operations, which led to a 20% decrease in energy costs within the first year.
- Orchestrated a strategic partnership with supply chain vendors to streamline operations, thereby cutting lead times by 14%.
- Pioneered the adoption of a predictive analytics model to anticipate stock needs, minimizing surplus inventory levels by 24%.
- Crafted and executed a comprehensive disaster recovery plan, ensuring business continuity during unexpected supply chain disruptions.
- Initiated a tech-forward strategy, introducing autonomous mobile robots to the warehouse, cutting picking time by 50% while doubling order capacity.
- Streamlined the returns process, effectively reducing processing time by 30% and improving stock availability for resale.
- Collaborated on the development of a custom predictive stocking application, boosting accuracy in demand forecasting by 35%.
- Managed stringent quality control measures, which saw a significant reduction in customer complaints about shipping errors by 98%.
- Piloted a warehouse automation project that included installing conveyor systems and advanced sorting machinery, increasing package handling capacity by 40%.
- Devised and implemented a dynamic slotting algorithm leading to a 20% improvement in pick-path efficiency and a 15% reduction in labor costs.
Quantifying impact on your resume
- Mention the percentage by which you successfully reduced operational costs through strategic planning.
- Indicate the precise number of warehouse staff you managed or trained, showing your leadership and organizational capacity.
- Highlight the exact amount of inventory you were responsible for to demonstrate your ability to handle significant assets.
- Discuss any increase in efficiency or productivity under your management, with specific percentage improvements.
- Detail the number of successful warehouse projects led or contributed to, providing a sense of your project management skills.
- Quantify any reductions in lead times due to process improvements you implemented, showing your focus on optimizing operations.
- Illustrate the scale of operations by citing the square footage of warehouse space you have overseen.
- Share the volume or value of orders processed per period under your supervision to convey the magnitude of your experience.
Action verbs for your warehouse operations manager resume
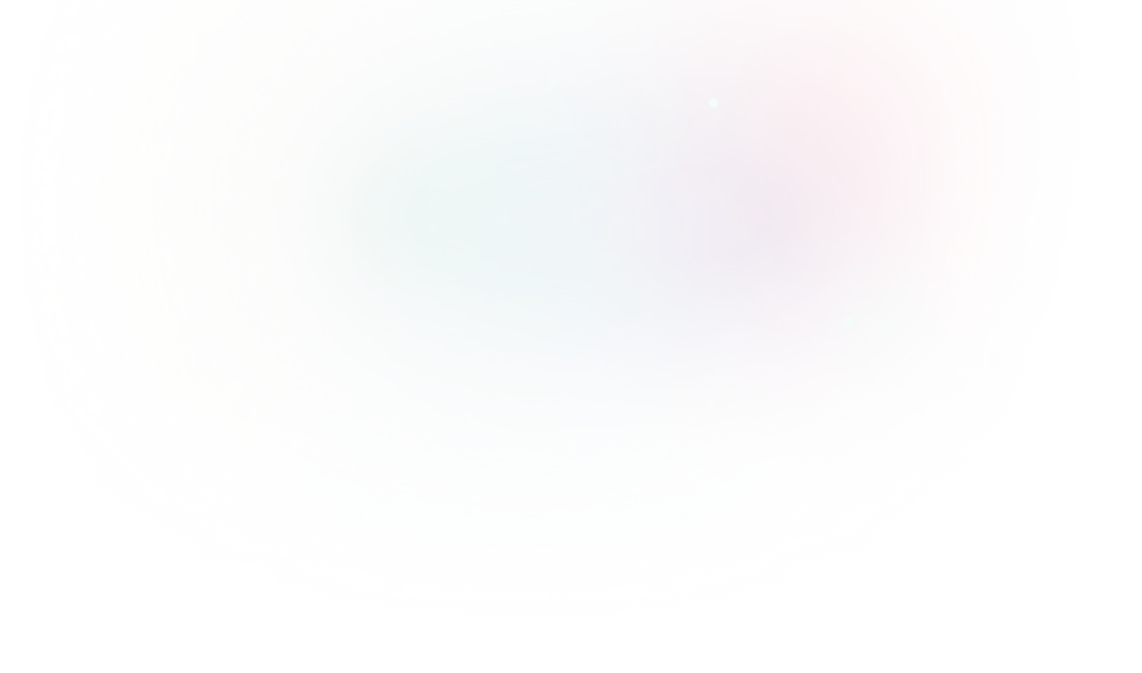
How to shift the focus from your warehouse operations manager resume experience section to your professional profile
If you're at the start of your career journey or transitioning industries, you might be concerned about the lack of professional experience while crafting your warehouse operations manager resume.
How can you effectively present your warehouse operations manager resume experience section under these circumstances?
Rather than a traditional, extensive experience section, demonstrate your expertise through:
- Emphasizing your education. Your academic background might impress recruiters, especially if it includes recent, industry-relevant knowledge;
- Creating a compelling objective statement. The first few sentences of your resume should map out your motivations and career aspirations, offering insight into your goals;
- Highlighting your transferable skills. For example, if you've honed communication skills through volunteering, illustrate on your warehouse operations manager resume how these can benefit a potential employer;
- Detailing your technical background in certifications and skills sections. As a recent graduate, your technological foundations might be particularly attractive to employers looking to develop these skills further.
It's important to remember that employers sometimes prefer candidates with less experience but who are a better cultural fit for their organization.
Recommended reads:
- How To Include Your Relevant Coursework On A Resume
- Perfecting the Education Section on Your Resume
Always remember that your warehouse operations manager certifications can be quantified across different resume sections, like your experience, summary, or objective. For example, you could include concise details within the expertise bullets of how the specific certificate has improved your on-the-job performance.
Warehouse Operations Manager resume skills: the essential hard skills and soft skills checklist
Ultimately, your Warehouse Operations Manager resume should hint to recruiters that you possess an array of talents that are indispensable to the role.
For example, listing the technologies and software you're apt at using (or your hard skills) and how you apply them in your day-to-day responsibilities would ensure you meet the technical requirements of the role.
But is this enough to ensure that you make a good impression on recruiters?
Go a step further by detailing the soft skills or personality traits you've attained thanks to your work and life experience.
The best way to balance hard skills and soft skills on your Warehouse Operations Manager resume is by:
- Highlighting up to three of your most noteworthy career accomplishments in a separate section.
- Listing at least one hard skill and one soft skill you've used to solve a particular challenge or problem.
- Feature niche skills and technologies that would help you stand out amongst candidates.
- Think back on the social impact your efforts have had towards improving the work environment - were you able to always maintain a professional ethic, while enhancing the team culture? Write about your contribution to the role, department, or organization itself as a metric of success.
The skills section of your resume provides you with plenty of opportunities to detail your technical and personal traits.
All you have to do is select the talents that best fit your application and expertise. Make note of some of the most prominent hard and soft skills across the industry from our list:
Top skills for your warehouse operations manager resume:
Inventory Management
Supply Chain Management
Warehousing Operations
Logistics Planning
Shipping and Receiving
Safety Compliance
Warehouse Management Systems
Materials Handling
Forecasting
Quality Control
Team Management
Problem Solving
Adaptability
Decision Making
Communication
Strategic Thinking
Attention to Detail
Time Management
Conflict Resolution
Qualifying your relevant certifications and education on your warehouse operations manager resume
In recent times, employers have started to favor more and more candidates who have the "right" skill alignment, instead of the "right" education.
But this doesn't mean that recruiters don't care about your certifications .
Dedicate some space on your resume to list degrees and certificates by:
- Including start and end dates to show your time dedication to the industry
- Adding credibility with the institutions' names
- Prioritizing your latest certificates towards the top, hinting at the fact that you're always staying on top of innovations
- If you decide on providing further information, focus on the actual outcomes of your education: the skills you've obtained
If you happen to have a degree or certificate that is irrelevant to the job, you may leave it out.
Some of the most popular certificates for your resume include:
The top 5 certifications for your warehouse operations manager resume:
- Certified Supply Chain Professional (CSCP) - Association for Supply Chain Management (ASCM)
- Certified in Production and Inventory Management (CPIM) - Association for Supply Chain Management (ASCM)
- Certified Logistics, Transportation and Distribution (CLTD) - Association for Supply Chain Management (ASCM)
- Professional Designation in Supply Chain Management (PSCM) - Institute for Supply Management (ISM)
- Certified Warehouse Logistics Professional (CWLP) - International Warehouse Logistics Association (IWLA)
- How to List Expected Graduation Date on Your Resume
- Should I Put In An Incomplete Degree On A Resume?
Writing the warehouse operations manager resume summary or objective: achievements, keywords, dreams, and more
Deciding on whether to include a resume summary or resume objective should entirely depend on your career situation.
If you have:
- Plenty of relevant achievements you'd like to bring recruiters' focus to, make use of the resume summary. Ensure each of your achievements is quantified with concrete proof (e.g. % of cases solved).
- Less applicable experience, utilize the resume objective. Within the objective include a few noteworthy, past successes, followed up by your professional dreams.
As a bonus, you could define in either your warehouse operations manager resume summary or objective what makes you the perfect candidate for the role.
Think about your unique hard and soft skills that would make your expertise even more important to the job.
These warehouse operations manager professionals have completely covered the formula for the ideal resume introduction:
Resume summaries for a warehouse operations manager job
- Seasoned Warehouse Operations Manager with over 15 years of robust experience in streamlining distribution systems for major logistics companies. Renowned for implementing cost-saving inventory management techniques and a record for reducing shipment processing times by 25% while maintaining accuracy and quality standards.
- Result-oriented professional with a decade of experience in manufacturing and keen to transition into warehouse operations management. Expertise in production workflow optimization and equipped with a Six Sigma Green Belt, ready to drive efficiency improvements in warehouse settings.
- Former retail manager aiming to leverage 8 years of inventory control and team leadership into the warehouse operations sector. Skills in strategic planning and employee training combined with a commitment to elevating operational processes within fast-paced warehouse environments.
- With 10 years of experience managing high-volume warehouses for an international retail chain, I have honed my abilities in logistics coordination and workforce management, achieving a 98% accuracy rate in inventory tracking and a 20% increase in order-picking efficiency.
- Recently certified in Warehouse Management Systems, I am eager to apply a fresh perspective and cutting-edge practices to enhance inventory management and distribution logistics. My objective is to lead a dynamic team to new levels of productivity and customer satisfaction.
- Ambitious and quick-learning individual with a background in customer service seeking to apply my problem-solving and organizational skills in a warehouse operations management context. I am enthusiastic about mastering supply chain logistics and contributing to a team's success through diligent work and continuous improvement.
Other warehouse operations manager resume sections to support your expertise and skills
Recruiters are always on the lookout for that warehouse operations manager candidate who brings about even more value to the role.
This can be either via their personality or additional accreditations they have across the industry.
Add to your resume any of the four sections that fit your profile:
- Projects for your most impressive, cutting-edge work;
- Awards or recognitions that matter the most;
- Publications further building up your professional portfolio and accreditations;
- Hobbies and interests to feature the literature you read, how you spend your time outside of work, and other personality traits you deem may help you stand out .
Key takeaways
We trust that this Enhancv guide has been informative and useful. To summarize the essential points:
- Opt for a simple and readable format, focusing more on your warehouse operations manager achievements rather than just duties;
- Emphasize your accomplishments in the warehouse operations manager experience section over mere responsibilities;
- If lacking relevant experience, utilize various resume sections like education and volunteering to demonstrate your suitable skill set;
- Never overlook the significance of pertinent higher education, training, and certifications;
- Incorporate diverse sections in your resume to highlight not just your skills expertise but also your personality.
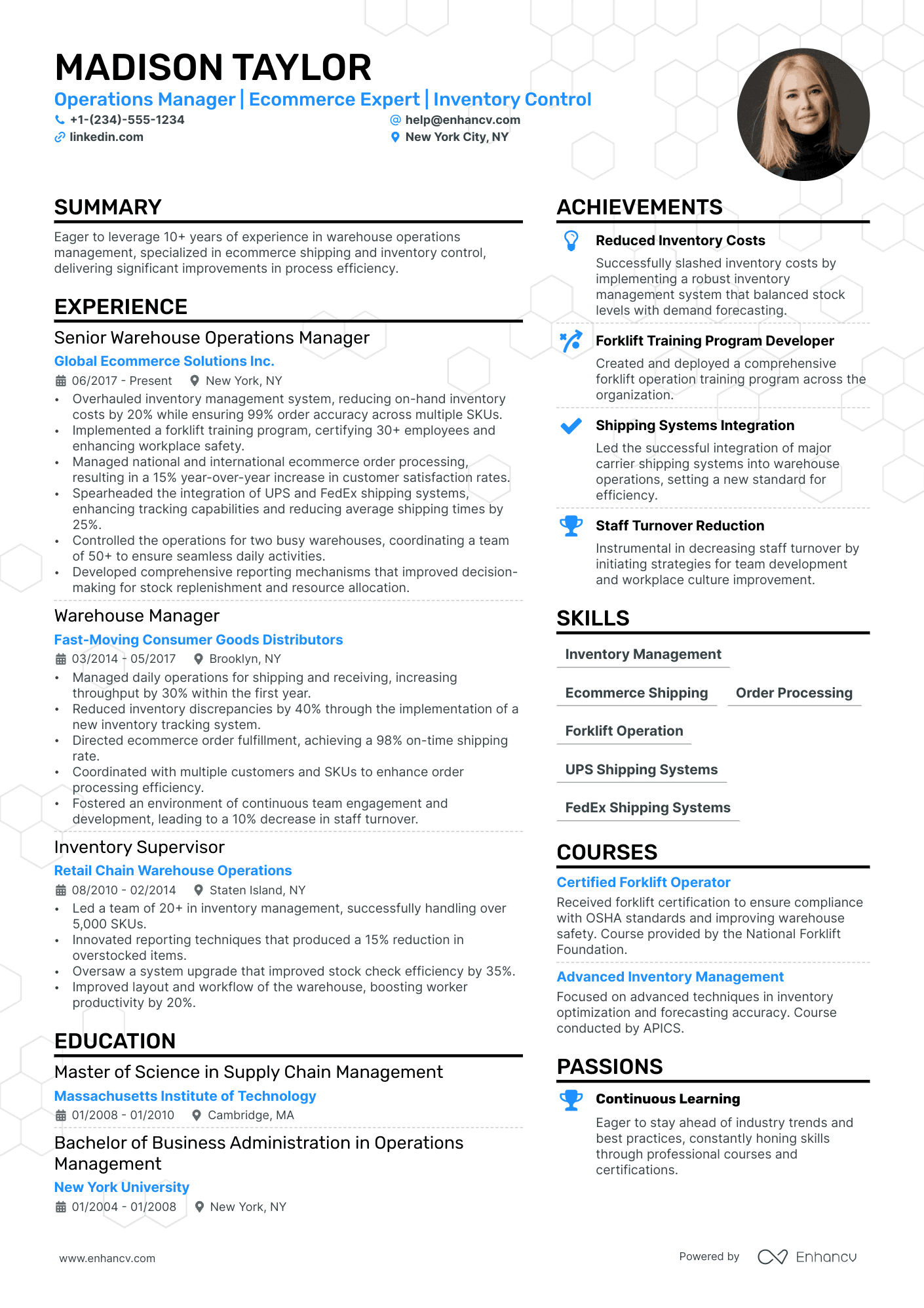
Looking to build your own Warehouse Operations Manager resume?
- Resume Examples
Solutions Architect Interview Questions
A guide to types of resumes: best formats, tips & examples, how to craft & tell a resume story behind your work success, how to list ged on your resume, cover letter vs. resume –what's the difference, does a cv include a cover letter.
- Create Resume
- Terms of Service
- Privacy Policy
- Cookie Preferences
- Resume Templates
- AI Resume Builder
- Resume Summary Generator
- Resume Formats
- Resume Checker
- Resume Skills
- How to Write a Resume
- Modern Resume Templates
- Simple Resume Templates
- Cover Letter Builder
- Cover Letter Examples
- Cover Letter Templates
- Cover Letter Formats
- How to Write a Cover Letter
- Resume Guides
- Cover Letter Guides
- Job Interview Guides
- Job Interview Questions
- Career Resources
- Meet our customers
- Career resources
- English (UK)
- French (FR)
- German (DE)
- Spanish (ES)
- Swedish (SE)
© 2024 . All rights reserved.
Made with love by people who care.
- Warehouse Operations Manager Resume Example
Resume Examples
- Common Tasks & Responsibilities
- Top Hard & Soft Skills
- Action Verbs & Keywords
- Resume FAQs
- Similar Resumes
Common Responsibilities Listed on Warehouse Operations Manager Resumes:
- Develop and implement warehouse operations systems and processes to maximize efficiency and accuracy
- Monitor and analyze warehouse operations and performance metrics to identify areas of improvement
- Manage and coordinate daily warehouse operations, including receiving, storage, order fulfillment, and shipping
- Ensure compliance with safety regulations and company policies
- Oversee the maintenance and repair of warehouse equipment
- Develop and maintain relationships with vendors and suppliers
- Monitor inventory levels and order supplies as needed
- Train and supervise warehouse staff
- Develop and implement strategies to reduce costs and improve efficiency
- Monitor and report on warehouse KPIs
- Create and maintain detailed records and reports of warehouse operations
Speed up your resume creation process with the AI-Powered Resume Builder . Generate tailored achievements in seconds for every role you apply to.
Warehouse Operations Manager Resume Example:
- Implemented a new inventory management system, resulting in a 25% reduction in stockouts and a 15% increase in inventory accuracy.
- Developed and executed a safety training program, resulting in a 50% decrease in workplace accidents and injuries.
- Reduced shipping costs by 20% by negotiating new contracts with carriers and optimizing shipping routes.
- Managed a team of 20 warehouse staff, achieving a 95% on-time delivery rate and a 98% order accuracy rate.
- Implemented a new order picking process, resulting in a 30% increase in productivity and a 20% reduction in labor costs.
- Developed and executed a cost-saving initiative, resulting in a 10% reduction in overall warehouse expenses.
- Developed and implemented a new warehouse layout, resulting in a 40% increase in storage capacity and a 25% reduction in order fulfillment time.
- Reduced inventory carrying costs by 15% by optimizing inventory levels and implementing a just-in-time (JIT) inventory system.
- Implemented a new quality control process, resulting in a 20% reduction in product defects and a 10% increase in customer satisfaction ratings.
- Inventory management
- Warehouse layout optimization
- Safety training and compliance
- Team management and leadership
- Shipping and logistics coordination
- Order picking and fulfillment
- Cost reduction and budgeting
- Quality control and assurance
- Just-in-time inventory systems
- Contract negotiation
- Process improvement and implementation
- Customer satisfaction and service
- Time management and prioritization
- Data analysis and reporting
- Staff training and development
Top Skills & Keywords for Warehouse Operations Manager Resumes:
Hard skills.
- Inventory Management
- Supply Chain Management
- Warehouse Management Systems (WMS)
- Lean Six Sigma Methodologies
- Quality Control and Assurance
- Safety and Compliance Regulations
- Logistics and Transportation Management
- Budgeting and Cost Control
- Performance Metrics and KPIs
- Process Improvement and Optimization
- Team Management and Leadership
- Vendor and Supplier Management
Soft Skills
- Leadership and Team Management
- Communication and Presentation Skills
- Collaboration and Cross-Functional Coordination
- Problem Solving and Critical Thinking
- Adaptability and Flexibility
- Time Management and Prioritization
- Decision Making and Strategic Planning
- Conflict Resolution and Negotiation
- Attention to Detail and Accuracy
- Analytical and Data-Driven Thinking
- Safety and Compliance Awareness
Resume Action Verbs for Warehouse Operations Managers:
- Streamlined
- Implemented
- Coordinated
- Standardized
- Facilitated
- Consolidated
Generate Your Resume Summary
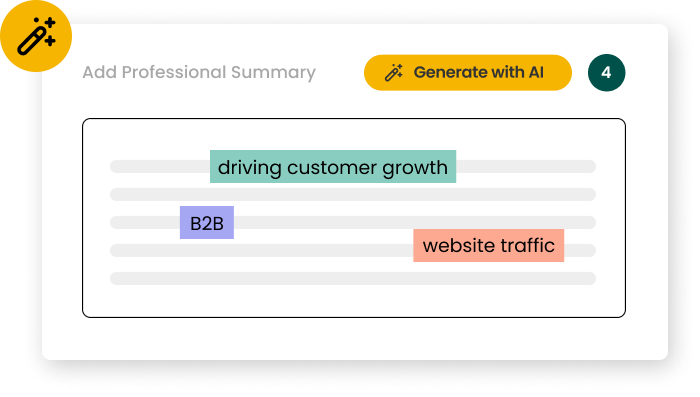
Resume FAQs for Warehouse Operations Managers:
How long should i make my warehouse operations manager resume, what is the best way to format a warehouse operations manager resume, which keywords are important to highlight in a warehouse operations manager resume, how should i write my resume if i have no experience as a warehouse operations manager, compare your warehouse operations manager resume to a job description:.
- Identify opportunities to further tailor your resume to the Warehouse Operations Manager job
- Improve your keyword usage to align your experience and skills with the position
- Uncover and address potential gaps in your resume that may be important to the hiring manager
Complete the steps below to generate your free resume analysis.
Related Resumes for Warehouse Operations Managers:
Logistics operations manager, regional operations manager, assistant operations manager, distribution operations manager, transportation operations manager, retail operations manager, senior operations manager, branch operations manager.
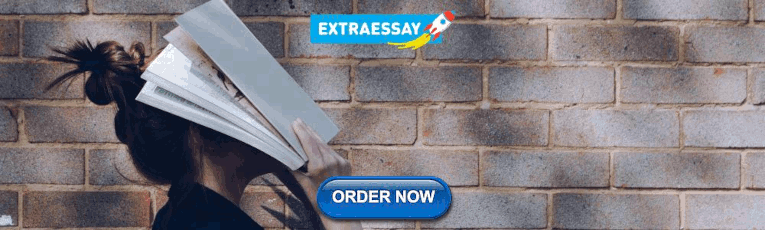
IMAGES
VIDEO
COMMENTS
Template 2 of 4: Warehouse Operations Manager Resume Example. As the name suggests, this operations manager is in charge of the daily operations of a warehouse. Your tasks may include, ensuring the distribution plan is effectively realized, tracking inventory, overseeing the dispatching of inventory, etc.
Warehouse Manager Resume Examples & Samples. Responsible for all Plant Warehouse department performance (Safety, Quality, Service, Employee Morale, Cost) Inventory value of $8MM of raw ingredients and packaging materials. 15MM pounds of bulk raw ingredients. 3,000 pallets of raw ingredients and packaging materials.
2. Include warehouse manager-related keywords in your resume. Pepper relevant warehouse manager keywords throughout your resume. Resume keywords show recruiters that you're familiar with the terminology used in the warehouse management field.. Including keywords from the job description catches the recruiters' attention, because doing so demonstrates your interest in the job when you ...
Good example: " Experienced Warehouse Manager with over 10 years of experience in managing and leading teams in the efficient storage and distribution of goods. Achieved a 15% increase in warehouse efficiency and a 20% reduction in costs. Proven ability to develop and implement strategies to optimize productivity and ensure safety standards ...
Use the following examples to help craft your warehouse manager resume: Entry-level warehouse manager resume sample John Doe Auburn, New York 555-555-0122 [email protected] Professional summary To secure an entry-level position as a Warehouse Manager and use my organizational and problem-solving skills to ensure smooth operations of the warehouse.
Start Building. 1. Craft an outstanding profile with a summary of your warehouse manager qualifications. Your profile summary as a warehouse manager should be concise, compelling, and tailored to the specific job you're applying for. Remember to keep your profile summary concise, usually within three to five sentences.
Lake Charles, LA 70612. 555-555-5555. [email protected]. Professional Summary. Efficient warehouse manager with over 10 years of experience in warehouse operations to meet continuous internal and customer needs. Well-coordinated and decisive leader with expertise in team building and performance optimization.
Warehouse Managers play a vital role in the supply chain management process and handle a variety of goods, from food to manufacturing parts. Usual work activities listed on a Warehouse Manager resume example include liaising with customers and suppliers, recruiting and training staff, monitoring service quality, motivating team leaders, and ...
Vadalyn. March 2015-April 2019. Served as a warehouse manager for 100,000 sq. ft. facility. Oversaw and coached 12 warehouse staff, improving efficiency by 45% through automation and improvements. Implemented warehouse-wide kanban system for FIFO management of all kits and parts. Slashed kitting time by 30%.
Here are the parts of any complete warehouse manager resume example: The resume header. The resume summary (aka profile or personal statement) The employment history section. The resume skills section. The education section. Most warehouse manager applicants will want to keep their resume to one page in length.
Warehouse Manager Resume: Examples of Summaries for a Resume Good Example. Organized warehouse manager with 5+ years of experience in coordinating warehouse operations and 9+ years of experience working in a warehouse environment. Reduced overall operating costs by 15% through improved logistics management. Achieved 99.8% on-time delivery of ...
3 Warehouse Manager Resume. Examples That Work in 2024. Stephen Greet February 5, 2024. Every warehouse operation needs a strong leader to ensure the company's policies and vision are achieved. You ensure operations succeed by overseeing and optimizing receiving, storage, and distribution processes with expert care.
The five (plus) definite sections your resume for a warehouse manager job should include are: Header with your headline, contact details, and/or a preview of your work. Summary (or objective) to pinpoint how your success aligns with the role. Experience with bullets of your most relevant achievements in the field.
This guide is equipped with practical examples and tips tailored for the warehouse manager position that will help you create an outstanding resume. 1. Open with a professional summary. The resume's opening statement introduces the candidate's qualifications for the role.
A Warehouse Manager is responsible for overseeing the daily operations of a warehouse, which includes receiving, storing, and distributing goods. They lead teams of workers and ensure that the warehouse is efficient, organized, and safe. Warehouse Managers also handle inventory management, quality control, and customer service. A strong resume is crucial for Warehouse Manager positions, as it ...
Pause for a sec and review our comprehensive Warehouse Manager Resume samples and resume write up below. We have selected examples, types, templates, and job description content to assist you in creating a top-notch resume document. Warehouse Managers work in distribution centers, storage facilities, and factories.
Warehouse Manager Resume Examples. John Doe. Warehouse Manager. 123 Main Street | Anytown, USA 99999 | Phone: (123) 456-7890 | Email: [email protected]. A highly organized and detail- oriented warehouse manager with 5+ years of experience in logistics and inventory management.
Here are some examples of quantified accomplishments in warehouse manager/supervisor resume: Led a team of 5 handlers in a 5,000 sq. ft. warehouse. Scheduled production jobs and ensured on-time delivery, maintained high customer satisfaction rate for 3 straight years. 📌 Tip 3: Craft an ATS-friendly Resume.
We've also selected some of the best (and most relevant) resume guides for the warehouse operations manager role you're applying for: Shift Manager Resume Example. Category Manager Resume Example. Venue Manager Resume Example. Agile Business Analyst Resume Example. Strategy Consultant Resume Example.
Here are a few bullet points listing skills for a warehouse manager that you can consider adding to your resume: Communication skills. Supply chain management. Operations management. Inventory control. Forklift operation. Warehouse operations. Process improvement. Warehouse inventory tracking.
Common Responsibilities Listed on Warehouse Operations Manager Resumes: Develop and implement warehouse operations systems and processes to maximize efficiency and accuracy. Monitor and analyze warehouse operations and performance metrics to identify areas of improvement. Manage and coordinate daily warehouse operations, including receiving ...
Warehouse Manager Resume Examples. Warehouse managers are tasked with supervising all activities that take place in a warehouse. They work to make sure all departments are working efficiently to get the job done. Success comes down to the Warehouse Manager's ability to be organized. Can you say the same thing about your Warehouse Manager resume?