- Search Search Please fill out this field.
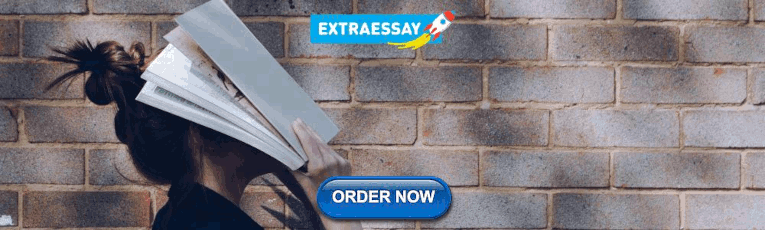
What Is Six Sigma?
Understanding six sigma, the 5 steps of six sigma.
- Lean Six Sigma
- Certification and Belt Rankings
The Bottom Line
- Corporate Finance
What Is Six Sigma? Concept, Steps, Examples, and Certification
Adam Hayes, Ph.D., CFA, is a financial writer with 15+ years Wall Street experience as a derivatives trader. Besides his extensive derivative trading expertise, Adam is an expert in economics and behavioral finance. Adam received his master's in economics from The New School for Social Research and his Ph.D. from the University of Wisconsin-Madison in sociology. He is a CFA charterholder as well as holding FINRA Series 7, 55 & 63 licenses. He currently researches and teaches economic sociology and the social studies of finance at the Hebrew University in Jerusalem.
:max_bytes(150000):strip_icc():format(webp)/adam_hayes-5bfc262a46e0fb005118b414.jpg)
Investopedia / Zoe Hansen
Six Sigma is a set of techniques and tools used to improve business processes. It was introduced in 1986 by engineer Bill Smith while working at Motorola. Six Sigma practitioners use statistics, financial analysis, and project management to identify and reduce defects and errors, minimize variation, and increase quality and efficiency.
The five phases of the Six Sigma method, known as DMAIC, are defining, measuring, analyzing, improving, and controlling.
Key Takeaways
- Six Sigma is a quality-control methodology that businesses use to significantly reduce defects and improve processes.
- The model was developed by a scientist at Motorola in the 1980s.
- Companies often use the Six Sigma model to increase efficiency and boost profits.
- Six Sigma practitioners can earn certifications modeled on the color belts used in martial arts.
Six Sigma is based on the idea that all business processes can be measured and optimized.
The term Six Sigma originated in manufacturing as a means of quality control. Six Sigma quality is achieved when long-term defect levels are below 3.4 defects per million opportunities (DPMO).
Six Sigma has since evolved into a more general business concept, focusing on meeting customer requirements, improving customer retention, and improving and sustaining business products and services. Among its best-known proponents was the longtime General Electric CEO Jack Welch .
Six Sigma certification programs confer belt rankings similar to those in the martial arts, ranging from white belt to black belt.
The Six Sigma method uses a step-by-step approach called DMAIC, an acronym that stands for Define, Measure, Analyze, Improve, and Control. According to Six Sigma adherents, a business may solve any seemingly unsolvable problem by following these five steps.
A team of people, led by a Six Sigma expert, chooses a process to focus on and defines the problem it wishes to solve.
The team measures the initial performance of the process, creating a benchmark, and pinpoints a list of inputs that may be hindering performance.
Next the team analyzes the process by isolating each input, or potential reason for any failures, and testing it as the possible root of the problem.
The team works from there to implement changes that will improve system performance.
The group adds controls to the process to ensure it does not regress and become ineffective once again.
What Is Lean Six Sigma?
Lean Six Sigma is a team-focused managerial approach that seeks to improve performance by eliminating waste and defects while boosting the standardization of work. It combines Six Sigma methods and tools and the lean manufacturing/ lean enterprise philosophy, striving to reduce the waste of physical resources, time, effort, and talent while assuring quality in production and organizational processes. Any use of resources that does not create value for the end customer is considered a waste and should be eliminated.
Six Sigma Certification and Belt Rankings
Individuals can obtain Six Sigma certification to attest to their understanding of the process and their skills in implementing it. These certifications are awarded through a belt system similar to karate training. The belt levels are:
- White belt : Individuals with a white belt have received some instruction in the basics of Six Sigma, but have not yet gone through any formal training or certification program. This gives them enough knowledge to become team members.
- Yellow belt : This level can be attained after several training sessions, and equips participants with the knowledge to lead small projects and assist managers who hold more advanced belts.
- Green belt : To achieve this level, individuals take a more comprehensive course that prepares them to become project leaders.
- Black belt : After reaching the green belt level, participants can move on to black belt certification, preparing them for leadership roles in larger and more complex projects.
People with black belts can become masters and champions. Someone with a master black belt is considered an expert and strong leader with excellent problem-solving skills. A champion is a lean Six Sigma leader trained in maximizing profits through the elimination of waste and defects.
These certifications, and the courses required to obtain them, are offered by a variety of companies and educational institutions and can differ from one to another.
Real-World Examples of Six Sigma
Six Sigma is used by many companies, local governments, and other institutions. Here are two examples of how Six Sigma improved operational efficiency, saved money, and increased customer satisfaction.
Microsoft (MSFT) is one of the largest software producers in the world. It used Six Sigma to help eradicate defects in its systems and data centers and systematically reduce IT infrastructure failures.
The company first established standards for all of its hardware and software to create a baseline measurement for detecting defects. It then used root-cause analysis, including collecting data from past high-priority incidents, server failures, and recommendations from product group members and customers, to pinpoint potential problem areas.
Large amounts of data were collected on a daily and weekly basis from various servers. The incidents were prioritized based on how severely the defects affected the business and the company's underlying services. Data analysis and reporting identified the specific defects, after which remediation steps for each defect were established.
As a result of Six Sigma, Microsoft says it improved the availability of its servers, boosted productivity, and increased customer satisfaction.
Ventura County, California, Government
Ventura County, California, credited the use of Lean Six Sigma for a savings of $33 million. The county government began to use the program in 2008 and has trained more than 5,000 employees in the methodology. The county says the savings are due in part to the introduction of more efficient new systems and the elimination of unnecessary, but time-consuming, steps from its prior processes.
For example, the VC Star newspaper reported in 2019 that the county saved "$51,000 with an appointments system that reduced labor costs and rates for maintenance of county vehicles [and] almost $400,000 annually by implementing a new system to track employee leaves of absence."
How Can You Get Six Sigma Certification?
You can receive Six Sigma certification through private companies, associations, and some colleges. Keep in mind, though, that there is no single governing body that standardizes the curriculum. This means that courses can vary based on where you take them.
Can You Get Six Sigma Certification Online?
Yes, many of the universities and organizations that offer Six Sigma certification have both classroom and online offerings.
What Is the Basic Difference Between Six Sigma and Lean Six Sigma?
Lean Six Sigma uses the Six Sigma methodology (define, measure, analyze, improve, control) with the specific goal of eliminating waste in a company's, or other organization's, processes or use or materials—that is, making it "leaner." It derives in part from the principles of lean manufacturing.
Six Sigma has become a widely used quality-improvement methodology in both the private and public sectors. Anyone who wishes to learn it can take courses that lead to various levels of certification.
ASQ. " What Is Six Sigma? "
Purdue University. ' Six Sigma Belt Level Rankings ."
Microsoft. " Microsoft Announces Accelerator for Six Sigma ."
VC Star . " Efficiency Program Rooted in Car Business Drives $33 Million in Government Savings ."
:max_bytes(150000):strip_icc():format(webp)/creative-businesswoman-brainstorming--reviewing-flow-chart-hanging-on-brick-wall-in-office-728759387-795f4c055fda4475acc9bdafb7f9999d.jpg)
- Terms of Service
- Editorial Policy
- Privacy Policy
- Your Privacy Choices
Six Sigma for Beginners
By Kate Eby | May 29, 2017 (updated August 9, 2022)
- Share on Facebook
- Share on LinkedIn
Link copied
For at least a century, the industrial world has striven for ever greater efficiency in production and higher quality in output. The quest was defined by people like Shewhart and Taylor in the early 20th century, and hasn’t stopped as theories and methods for improvement are posited, reviewed, tested, and implemented. One of the most influential methods expounded in the last 35 years is Six Sigma. Originally formulated in manufacturing, the methodology is now practiced in fields such as healthcare and finance, in Fortune 500 companies all over the world.
In this article, we’ll explain Six Sigma, its origins in American manufacturing and development, what tools it uses, and how you can train to become certified to practice Six Sigma. Plus, experts explain the benefits that Six Sigma can offer you and your company.
What Is Six Sigma?
When practiced well, Six Sigma can be a powerful tool. As consultant Jennifer Williams says , “I have not found an industry that could not benefit from Six Sigma.”
Six Sigma is a set of methods and tools for business process improvement and quality management. Six Sigma aims to improve quality by finding defects, determining their cause, and improving processes to increase the repeatability and accuracy of process results. By improving efficiency and decreasing defects, the quality and timeliness of product delivery improves, and with it, ideally, employee enthusiasm and confidence--and the company’s bottom line.
With the aim of achieving near perfect ouput, Six Sigma employs statistical methods to detect problems and improve processes. Data-driven improvement projects are executed with specific steps in a defined sequence and with specific improvement goals in mind, called value targets. Teams with in-depth knowledge of the Six Sigma methodology are established to sponsor, manage, and complete the project.
“Six Sigma is a methodology and set of tools that help us measure what we do and then improve what we do. It really can work in any industry and in any type of business because everywhere we have a process, we can study it, measure it, and try to make it better,” says Kimberly McAdams, a Six Sigma Master Black Belt and Principal with FireFly Consulting .
This popular methodology, which gained a foothold in American business in the 1980s, is now a worldwide practice. Proponents of Six Sigma tout its advantages, including reduced waste, improved understanding of customer requirements, reduced production time, and a cost savings of up to 50 percent .
What Is Lean Six Sigma?
A variation on the Six Sigma framework marries Lean Management principles with Six Sigma methodologies. Lean Management seeks to reduce waste and thereby production cycle time, whereas Six Sigma focuses on reducing variation among deliverables. As some see it, Six Sigma focuses on finding and fixing defects after the fact, while Lean tries to prevent defects from occurring in the first place. At its best implementation, Lean is introduced first to increase efficiency, and then Six Sigma methods are applied for fine-tuning. Manufacturing, healthcare, finance, IT, and other fields use Lean Six Sigma.
Sermin Vanderbilt is Founder of Lean and Six Sigma World Conference and President of the American Quality Institute . According to her, “Six Sigma is getting it right every time or most of the time, 99.9 percent of the time. Almost every organization does need Six Sigma. Six Sigma is about accuracy. Lean is about cutting the costs, cutting time, so they go hand in hand.”
In short, what is Six Sigma? In the words of perhaps its most famous proponents, Jack Welch, “Six Sigma is a quality program that, when all is said and done, improves your customer’s experience, lowers your costs, and builds better leaders.”
Project Management Guide
Your one-stop shop for everything project management
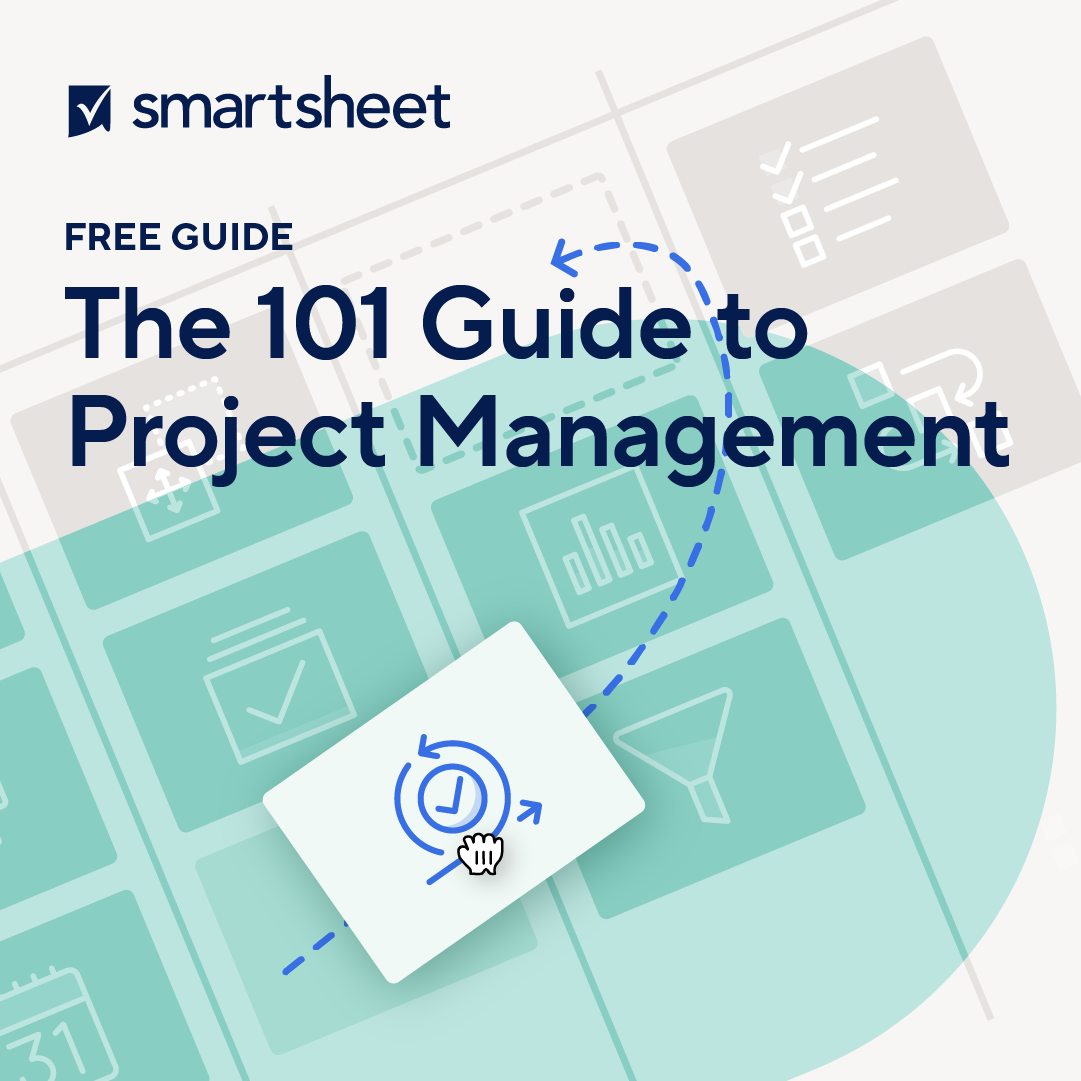
Ready to get more out of your project management efforts? Visit our comprehensive project management guide for tips, best practices, and free resources to manage your work more effectively.
View the guide
History of Six Sigma
Although the term sigma (with a lowercase s) was used as far back as the 1920s in statistical process control, Motorola first named Six Sigma as a quality goal in 1984. The previous 60 years of quality improvement theory, including Total Quality Management and Zero Defects helped develop the formal methods known today.
Over time, Motorola realized that they could apply many of the tools and methods used to achieve fewer defects in parts manufacturing to other aspects of business. In the years that followed, other large companies such as Allied Signal also adopted the methodology. But Six Sigma attained true star status in the late 1990’s when GE’s chairman and CEO, Jack Welch, proclaimed phenomenal savings as a result of of Six Sigma.
ISO (International Organization for Standardization) published its first certification for Six Sigma in 2011, but no single governing Six Sigma organization publishes the definitive body of knowledge. Companies, institutions of higher learning, and consulting companies may offer standards and training that differ slightly.
The 2000s saw Lean Manufacturing , with an emphasis on reducing waste and improving process flow, combined with Six Sigma principles to form Lean Six Sigma. This framework offers organizations methodologies for streamlining processes and then detecting and removing defects and inefficiencies.
Six Sigma: What’s In a Name?
Six Sigma derives from statistical process modeling in manufacturing. A sigma is a measure of standard deviation, abbreviated as small s, or the Greek letter, σ. Something that is within +/-6s, Six Sigma, from the centerline of a control chart was created by a process that is considered well controlled. In other words, there is little deviation from the standard and is within tolerance. Six Sigma is sometimes written as 6σ. Motorola trademarked the name in the 1990s with capital letters.
Six Sigma Processes
In practical terms, a Six Sigma process produces 99.99966% of all deliverables, called opportunities, free of defects. Essentially, the process produces 3.4 defects per million opportunities (DPMO). You can also think of Sigma levels as how far a process or deliverable deviates from perfection. An important concept is to think of sigma defects as not meeting customer expectations. Aiming for Six Sigma level, you have a high probability of producing items that are well within specification. Several Sigma levels exist, each of which indicates the number of allowed defects per million and thus the level of maturity of a process, as is indicated in the table that follows.
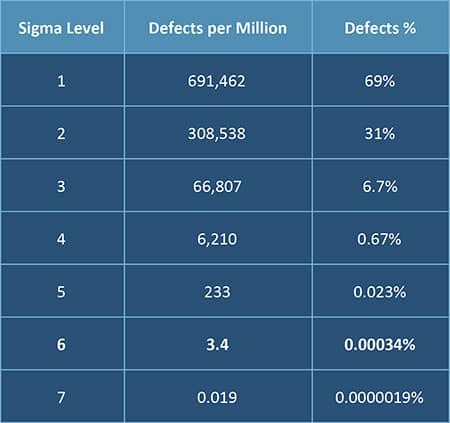
Six Sigma level processes may not always be necessary to a business or they may not be good enough. McAdams explains, “In many cases, Six Sigma is really good quality and in other cases, it’s not. I came from the semiconductor industry and in most cases we needed much higher than a Six Sigma level performance.” On the other hand, business and finance environments may be fine with 2 Sigma processes. “It’s an improvement if you can move a process from a 2 Sigma to a 4 Sigma,” McAdams says. “It’s just always about reducing errors and reducing waste in what you do.”
Some theoreticians also consider that processes deteriorate over time in a 1.5 Sigma shift. Statistically, this means that the process will deviate 1.5 Sigma from the centerline of a control chart.
What Are the Benefits of Six Sigma?
As a new methodology, Six Sigma focussed on measurable goals, especially financial goals. You can achieve the goals through data-driven decisions, based on statistical processes, and not hypotheses.
“Control charts have been around for almost 100 years, but being able to take a methodology, really define a problem up front, find what a customer needs, and then start using these business and statistical tools to really dig in, that’s what helped Six Sigma become so powerful,” says McAdams.
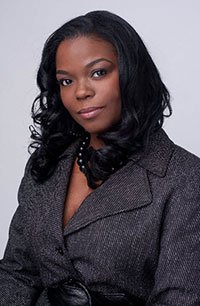
“Data is fun,” asserts Jennifer Williams a Six Sigma Master Black Belt with an MBA and President and CEO of Integrity Business Consulting . “With data, you say, whoa, I didn’t know that this was happening, and it just paints a whole other picture. There’s nothing like giving data-driven decisions or recommendations.”
Indeed, many companies credit Six Sigma with earning them substantial savings. For example, Motorola touts a savings of $17 billion. Although the initial results of work with Six Sigma at GE were less promising, between 1995 and 2000, Six Sigma processes are said to have saved the company $12 billion. Over 50 percent of Fortune 500 companies use Six Sigma and credit the methodology with savings of over $400 billion in the past two decades.
Six Sigma is usually a practice that large corporations use, and some consider that the methodology requires significant adaptation for small organizations. In addition, formal certification may be prohibitively expensive for small companies, especially for more advanced certifications.
However, experts also see the advantages of Six Sigma for all organizations. “I would say that smaller companies need Lean and Six Sigma more than larger companies because they need to be so much more competitive to stay in business,” asserts Vanderbilt.
Although Six Sigma did originate in manufacturing, business and service industries have also realized its benefits as well. “What makes it a little more challenging sometimes, is that we can’t visualize the virtual, electronic processes, and so actually, in the end, the tools become even more important in that environment,” says McAdams. In manufacturing, you can go to the production floor and view the assembly line and time the processes. “A lot of our processes in the business world are happening over email and other electronic communications. But in some cases, it actually makes it easier to time, if we have good data coming from those systems.”
Williams adds that if you started out practicing Six Sigma in manufacturing, applying it to non-manufacturing, such as finance, requires some adjustments in thinking. Instead of putting a part down a conveyer belt, it’s handing off information from one department to another department or within the same department. “It’s following that value stream and seeing where the bottlenecks are, seeing the delays, and asking are we waiting? Is there overproduction? Are we over processing. We still can tie those quality improvement concepts to information or data.” Further, she adds, “I have not found an industry that could not benefit from Six Sigma.”
What Are the Six Sigma Principles?
Depending on where you look, you’ll find some slight variation on Six Sigma principles. In general, these are the thoughts that guide the approach.
- Continuous efforts to achieve stable and predictable process results are crucial to business success.
- Manufacturing and business processes have characteristics that can be defined, measured, analyzed, improved, and controlled (see DMAIC below).
- Achieving sustained quality improvement requires commitment from the entire organization, including and perhaps especially upper and middle management.
- All processes can be defined and analyzed in detail, and therefore improved: if you control the inputs, you can control the outputs.
- Continual evaluation is crucial. Stop what you’re doing and consider what went right or wrong.
- Eliminating variation saves money and reduces defect
The Six Sigma Methodologies
The principles of Six Sigma are executed through methodologies, or roadmaps to improvement, like a workflow. Two main methodologies are DMAIC and DMADV.
DMAIC , pronounced duh-may-ick , focuses on incrementally improving existing processes. It is the most widely known methodology and the one most associated with Six Sigma. Here’s a breakdown of the acronym:
D: Define customer needs, requirements, and project goals.
M: Measure the key aspects of the current process. According to McAdams, “This is when you start to understand your process and collect data on it.”
A: Analyze data. “You really dig into what types of errors occur and where they occur so you can target the big ones. It’s always looking at that 80/20 rule . Let’s see if we can find 20 percent of the reasons that give us 80 percent of the defects and let us reduce those,” says McAdams.
I: Improve processes. Test and verify that the improvements work.
C: Control future implementations of the processes to ensure that errors don’t creep in again.
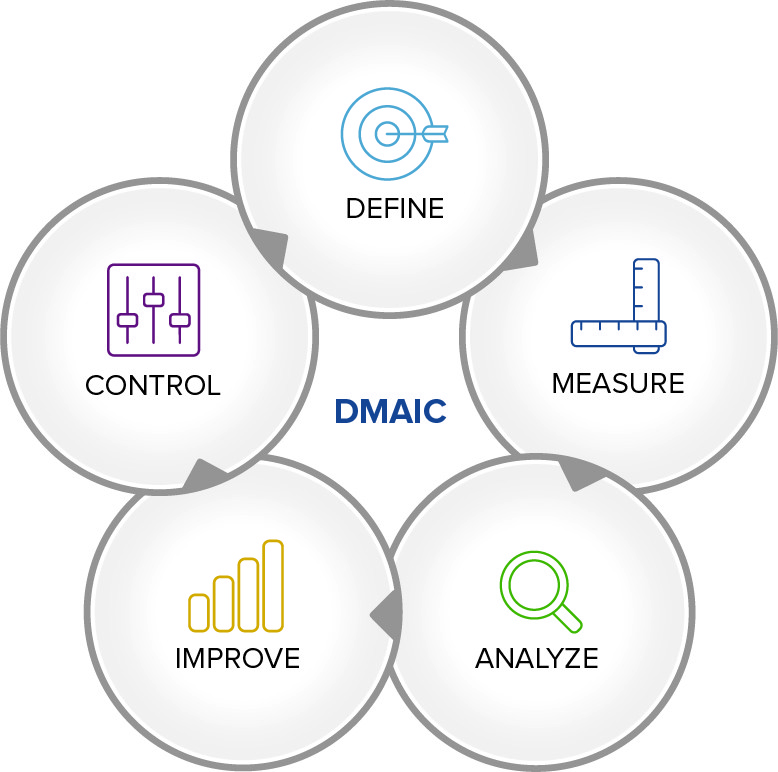
Download DMAIC Roadmap Template
Excel | Word
DMADV , pronounced duh-mad-v , focuses on optimizing new products or processes to Six Sigma standards. Here’s a breakdown of the acronym:
D: Define customer or company goals.
M: Measure CTQs (characteristics that are Critical To Quality), measure product capabilities, production process capability, and risks.
A : Analyze data from your measurements.
D: Design the new process based on the analysis in the previous step.
V: Verify the design through a pilot run, implement the new process, and hand off to the process owner.
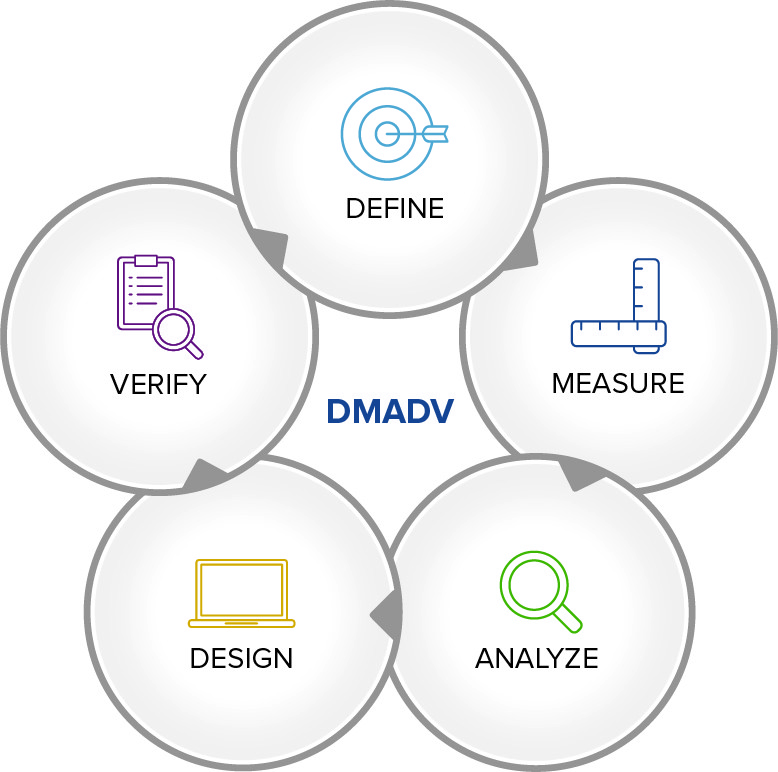
Download DMADV Roadmap Template
Excel | Word
An emerging methodology, particularly associated with Lean Six Sigma, is DFSS (Design for Six Sigma), with an emphasis on determining from the beginning what the customer wants and ensuring that defects and inefficiencies are anticipated and eliminated at the design phase of a process.
Analysis Tools
During the phases of these methodologies, Six Sigma practitioners use various existing tools to measure and analyze process and outcomes. A partial list of the most mentioned tools is as follows:
- Control charts
- Root Cause Analysis
- CTQ Tree (Critical to Quality)
- Statistical process control
- Process mapping
- ANOVA gauge R&R (analysis of variance gauge repeatability and reproducibility)
- Pareto charts
- Value Stream Mapping
- Business Process Mapping or Checksheet
- Cause and effects diagram or fishbone diagram or Ishikawa diagram
- Taguchi method
Who Makes It Happen? The Belts of Six Sigma
Execution of the Six Sigma methods relies on a team of trained practitioners sourced from throughout the company hierarchy. Management aligns the right projects with the right people and ensures that they can achieve goals and sustain success. The production team employs the methods to create a good result, and all participants must have Six Sigma training. Six Sigma borrows from the martial arts the concepts of belts to designate a level of methodological mastery.
- Executive Leadership: The CEO and other executive staff establish the vision for the Six Sigma implementation at the organization level, and support management.
- Champions: The executive leadership from upper management selects the Champions. They ensure that all departments in an organization work together to implement Six Sigma, and to mentor Black Belts.
- Master Black Belts: Champions select the Master Black Belts, who advise on Six Sigma practice for programs. Master Black Belts also train and mentor Black Belts and Green Belts, and identify potential Six Sigma projects for the company.
- Black Belts: Master Black Belts supervise Black Belts, who are responsible for executing the Six Sigma methodology for specific projects. Their sole focus is the statistical analysis and the correct execution of Six Sigma methodology.
- Green Belts: Guided by Black Belts, Green belts are employees who implement Six Sigma recommendations as part of their regular duties. They may also lead projects part of the time.
- Yellow Belts: Yellow Belts have a basic knowledge of Six Sigma, but they may be either new to the methodology or need only a basic understanding as, for example, a Champion or an Executive. Yellow Belts may participate in projects by finishing such tasks as creating process maps, and working on smaller improvement efforts within larger projects.
- White Belts: New to Six Sigma concepts, White Belt certification takes only a few hours, and typically does not include testing.
Training and Certifications for Six Sigma Belts
Many training organizations offer Six Sigma certification, although no one official body of training knowledge or certification exists. Different schools and individual companies may offer their own variations. Some training institutions and consultancies do band together to provide a version that they accept. The Council for Six Sigma Certification , for example, accredits Six Sigma trainers to guarantee their curriculum meets a basic standard. The International Association for Six Sigma Certification (IASSC) provides certifications for Lean Six Sigma.
Training can be in a classroom, onsite, self-paced, online, or a combination of all. Certificates are awarded upon successful completion of a written exam, which may be taken online or on paper.
Aside from being a workplace requirement, a Six Sigma certification presents well on a resume, and can garner as much in salary as an MBA. Learn more about Six Sigma certifications by reading What You Need to Know About Six Sigma Certifications and Belts .
Formal training may not be necessary. “You don’t need the Belts to implement it,” says Sermin. “You just need to have the philosophy and the belief that you need Lean and Six Sigma to be competitive.” Training can be as simple as reading a basic Six Sigma book and deciding to focus on efficiency and to trim waste.
Six Sigma Glossary
Here are some common terms beyond those already mentioned in this article that all Six Sigma practitioners use.
5 Whys - An information gathering technique for exploring cause and effect.
7 Wastes - A Japanese concept describing how a business might waste resources. It is described by the acronym TIMWOOD, which stands for Transportation, Inventory, Motion, Waiting, Overprocessing, Overproduction, and Defects.
Acceptance, and Acceptable Quality Level (ACL) - This term refers to the acceptance of the product as meeting quality standards, or acceptance, or agreement with, a proposed action.
Activity Report - A report that tracks tasks, responsibilities, schedules, and duration.
Affinity Diagram - A diagram that captures the result of brainstorming activities, often used during the Improve phase of Six Sigma.
Analysis - A review and study of the data captured during the Measure phase.
ANOVA, ANCOVA, MANOVA, MANCOVA - The advanced statistical methods for comparing data.
Balanced Scorecard - A tool for aligning strategic elements and communicating strategy to the company.
Black Noise/White Noise - Elements that are always unpredictable and elements that are unpredictable, but will be eliminated with further information, respectively.
Business Improvement Campaign - An endeavour to improve processes throughout a company, not just on the manufacturing floor.
Business Process Management - An endeavour to improve workflow and flexibility throughout a company.
Cause-Effect Diagram - An Ishikawa diagram or fishbone diagram.
Checksheet - Also referred to as a frequency distribution or frequency distribution analysis. A tool held over from Total Quality Management. A simple chart used for collecting data over time in many instances to learn where problems occur. This chart helps to show the larger pattern of behavior, rather than making assumptions about the circumstances in which problems occurred.
Critical To Quality (CTQ) - An essential element that contributes to the success or quality in a process.
Defect - A failure to meet customer specifications or expectations, a failure within a process, or a physical defect.
Design For Six Sigma (DFSS) - Along with DMADV, DFSS focuses on listening to the customer to get the processes right before defects occur.
Define, Measure, Analyse Improve, Control, Improve (DMAIC) - The Six Sigma methodology for finding and fixing defects in a process.
Define, Measure, Analyze, Design, Verify (DMADV) - Similar to DFSS.
DPMO - An acronym that stands for Defects Per Million Opportunities.
Just-In-Time (JIT) - Just-In-Time is a production method that aims to minimize stock levels by producing products just in time for customer purchase.
Kaizen - A Japanese philosophy focusing on continuous improvement of process and people. The concept also influences Lean Thinking.
Materials Requirements Planning (MRP) - A methodology for optimizing material levels with production and delivery schedules.
Pareto - An analysis that looks for the 20 percent of activities that generate 80 percent of the benefits, or the 20 percent of problems that cause 80 percent of waste.
Plan, Do, Check, Act (PDCA) - The Total Quality Management method, and the precursor to DMAIC. Acknowledged as a foundational method in ISO 9000.
Process - Describes a workflow, or describes how Six Sigma is implemented.
Process Mapping - Including flow charting and value stream mapping, this is the process of creating a graphical representation of how things work
QxA=E - Quality multiplied by acceptance equals effectiveness. This equation originated in the Six Sigma program at GE.
Soft Skills - People skills, rather than statistical or process skills. The ability to influence people, build teams, communicate, empathize, and so forth.
Stakeholder - Internal and external customers, team members implementing a Six Sigma process and solution.
Tollgates - The review periods between Six Sigma stages.
Total Quality Management (TQM) - One of the original management systems, TQM teaches that every employee, management to janitor, is responsible for quality deliverables and a quality work experience.
X's/Big X's - The possible causes of the problem or the big Y.
Y's/Big Y's - The little aspects of a solution that serve the big Y, or main customer requirement.
Value Target - The financial goal for a Six Sigma project
Criticisms of Six Sigma
Nothing is perfect and Six Sigma has come under various criticisms. Some criticize what they see as the Black Belt industry, wherein it’s all too easy for anyone to hang up a shingle and start selling training and certifications. Others, such as the quality guru Joseph Juran felt that Six Sigma was, in effect, old wine in new bottles, that the principles were old and had simply been repackaged with fancy belts for certifications.
McAdams says that nothing is a panacea and success derives from a good implementation. “Just like any business methodology it’s sometimes practiced well and sometimes not so well. What it doesn’t really do, is fix the business strategy. A good strategy still needs to be in place. But the data that you can get from a good Six Sigma program and good projects can help you focus a business strategy. But, no, it’s not the end-all solution to saving a business.”
How Six Sigma Practitioners Use Smartsheet
Empower your people to go above and beyond with a flexible platform designed to match the needs of your team — and adapt as those needs change.
The Smartsheet platform makes it easy to plan, capture, manage, and report on work from anywhere, helping your team be more effective and get more done. Report on key metrics and get real-time visibility into work as it happens with roll-up reports, dashboards, and automated workflows built to keep your team connected and informed.
When teams have clarity into the work getting done, there’s no telling how much more they can accomplish in the same amount of time. Try Smartsheet for free, today.
Discover why over 90% of Fortune 100 companies trust Smartsheet to get work done.
Table of Contents
What is six sigma, what is lean six sigma, the 5 key principles of six sigma, the six sigma methodology, the six sigma process of business transformation, six sigma techniques, the six sigma tools, six sigma levels, what are the six sigma career choices and salary prospects, six sigma learning resources, what is six sigma: everything you need to know about it.
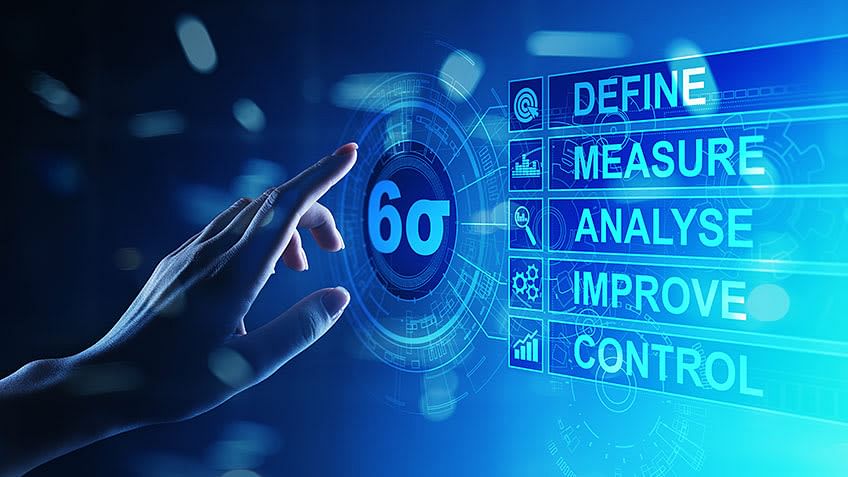
Reviewed and fact-checked by Sayantoni Das
The term "Six Sigma" refers to a statistical measure of how far a process deviates from perfection. A process that operates at six sigma has a failure rate of only 0.00034%, which means it produces virtually no defects. Six Sigma was developed by Motorola in the 1980s, and it has since been adopted by many other companies around the world, including General Electric, Toyota, and Amazon. It is used in industries such as manufacturing, healthcare, finance, and service industries to improve customer satisfaction, reduce costs, and increase profits.
Check out this video to know more about Six Sigma:
Six Sigma is a set of methodologies and tools used to improve business processes by reducing defects and errors, minimizing variation, and increasing quality and efficiency. The goal of Six Sigma is to achieve a level of quality that is nearly perfect, with only 3.4 defects per million opportunities. This is achieved by using a structured approach called DMAIC (Define, Measure, Analyze, Improve, Control) to identify and eliminate causes of variation and improve processes.
Six Sigma is a disciplined and data-driven approach widely used in project management to achieve process improvement and minimize defects. It provides a systematic framework to identify and eliminate variations that can impact project performance.
The etymology is based on the Greek symbol "sigma" or "σ," a statistical term for measuring process deviation from the process mean or target. "Six Sigma" comes from the bell curve used in statistics, where one Sigma symbolizes a single standard deviation from the mean. If the process has six Sigmas, three above and three below the mean, the defect rate is classified as "extremely low."
The graph of the normal distribution below underscores the statistical assumptions of the Six Sigma model . The higher the standard deviation, the higher is the spread of values encountered. So, processes, where the mean is minimum 6σ away from the closest specification limit, are aimed at Six Sigma.
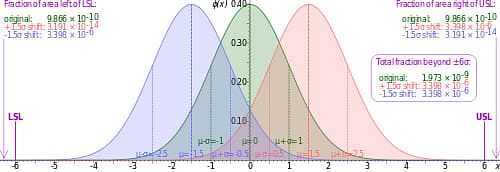
Credit: Cmglee , via Wiki Creative Commons CC BY-SA 3.0
Become a Quality Management Professional
- 10% Growth In Jobs Of Quality Managers Profiles By 2025
- 11% Revenue Growth For Organisations Improving Quality
Certified Lean Six Sigma Green Belt
- 4 hands-on projects to perfect the skills learnt
- 4 simulation test papers for self-assessment
Post Graduate Program in Lean Six Sigma
- Joint Post Graduate Program Certificate from UMass Amherst and KPMG in India
- Receive UMass Amherst Alumni Association Membership
Here's what learners are saying regarding our programs:
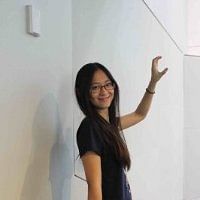
Xueting Liu
Mechanical engineer student at sargents pty. ltd. ,.
A great training and proper exercise with step-by-step guide! I'll give a rating of 10 out of 10 for this training.
Ekuh Arrey Etta
The class was terrific. The teaching method was unique and extraordinary.
Lean Six Sigma is a methodology that combines two powerful process improvement techniques: Lean and Six Sigma.
Lean focuses on minimizing waste and maximizing efficiency by identifying and eliminating non-value-adding activities. This involves streamlining processes, reducing defects, improving quality, and optimizing resources to deliver more value with less effort.
On the other hand, Six Sigma is a statistical approach to process improvement that aims to reduce variation and defects by using data-driven decision making. It involves defining, measuring, analyzing, improving, and controlling processes to achieve consistent and predictable results.
By combining the strengths of these two methodologies, Lean Six Sigma provides a comprehensive approach to process improvement that can be applied to any industry or sector. It is widely used in manufacturing, healthcare, finance, and service industries to improve efficiency, reduce costs, and enhance customer satisfaction.
The concept of Six Sigma has a simple goal – delivering near-perfect goods and services for business transformation for optimal customer satisfaction (CX).
Goals are achieved through a two-pronged approach:
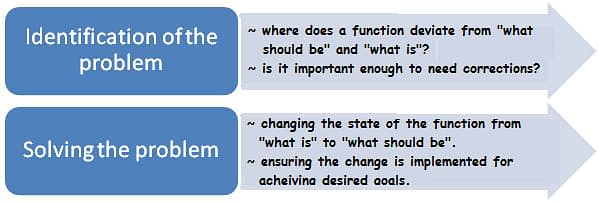
Six Sigma has its foundations in five key principles:
Focus on the Customer
Measure the value stream and find your problem, learn six sigma and get upto usd 114600 pa.
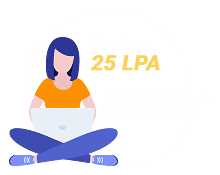
Get Rid of the Junk
Keep the ball rolling, ensure a flexible and responsive ecosystem.
Read More: Post Covid, Maria Camila Iacono wanted to move to a better position and decided she needed to boost her resume. Choosing our Lean Six Sigma Green Belt Certification Course , she not only got a new job offer, but she also got a 20% hike! Check out Iacono’s experience with her course and her journey in her Simplilearn Six Sigma Reviews .
The two main Six Sigma methodologies are DMAIC and DMADV. Each has its own set of recommended procedures to be implemented for business transformation.
DMAIC is a data-driven method used to improve existing products or services for better customer satisfaction. It is the acronym for the five phases: D – Define, M – Measure, A – Analyse, I – Improve, C – Control. DMAIC is applied in the manufacturing of a product or delivery of a service.
DMADV is a part of the Design for Six Sigma (DFSS) process used to design or re-design different processes of product manufacturing or service delivery. The five phases of DMADV are: D – Define, M – Measure, A – Analyse, D – Design, V – Validate. DMADV is employed when existing processes do not meet customer conditions, even after optimization, or when it is required to develop new methods. It is executed by Six Sigma Green Belts and Six Sigma Black Belts and under the supervision of Six Sigma Master Black Belts. We'll get to the belts later.
The two methodologies are used in different business settings, and professionals seeking to master these methods and application scenarios would do well to take an online certificate program taught by industry experts.
Operations Manager or Auditor? Your Choice
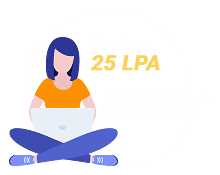
Although what is Six Sigma uses various methods to discover deviations and solve problems, the DMAIC is the standard methodology used by Six Sigma practitioners. Six Sigma uses a data-driven management process used for optimizing and improving business processes. The underlying framework is a strong customer focus and robust use of data and statistics to conclude.
The Six Sigma Process of the DMAIC method has five phases:
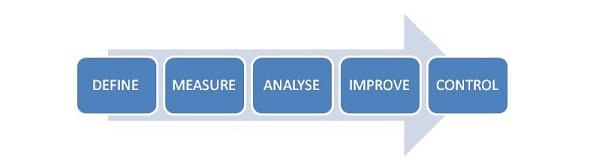
Each of the above phases of business transformation has several steps:
The Six Sigma methodology also uses a mix of statistical and data analysis tools such as process mapping and design and proven qualitative and quantitative techniques, to achieve the desired outcome.
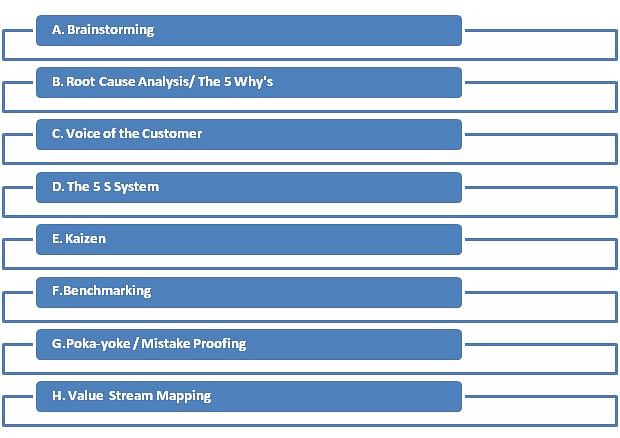
Fig: Key Six Sigma Techniques in use
Brainstorming
Brainstorming is the key process of any problem-solving method and is often utilized in the "improve" phase of the DMAIC methodology. It is a necessary process before anyone starts using any tools. Brainstorming involves bouncing ideas and generating creative ways to approach a problem through intensive freewheeling group discussions. A facilitator, who is typically the lead Black Belt or Green Belt, moderates the open session among a group of participants.
Root Cause Analysis/The 5 Whys
This technique helps to get to the root cause of the problems under consideration and is used in the "analyze" phase of the DMAIC cycle.
In the 5 Whys technique, the question "why" is asked, again and again, finally leading up to the core issue. Although "five" is a rule of thumb, the actual number of questions can be greater or fewer, whatever it takes to gain clarity.
Voice of the Customer
This is the process used to capture the "voice of the customer" or customer feedback by either internal or external means. The technique is aimed at giving the customer the best products and services. It captures the changing needs of the customer through direct and indirect methods. The voice of the customer technique is used in the "define' phase of the DMAIC method, usually to further define the problem to be addressed.
The 5S System
This technique has its roots in the Japanese principle of workplace energies. The 5S System is aimed at removing waste and eliminating bottlenecks from inefficient tools, equipment, or resources in the workplace. The five steps used are Seiri (Sort), Seiton (Set In Order), Seiso (Shine), Seiketsu (Standardize), and Shitsuke (Sustain).
Kaizen (Continuous Improvement)
The Kaizen technique is a powerful strategy that powers a continuous engine for business improvement. It is the practice continuously monitoring, identifying, and executing improvements. This is a particularly useful practice for the manufacturing sector. Collective and ongoing improvements ensure a reduction in waste, as well as immediate change whenever the smallest inefficiency is observed.
Benchmarking
Benchmarking is the technique that employs a set standard of measurement. It involves making comparisons with other businesses to gain an independent appraisal of the given situation. Benchmarking may involve comparing important processes or departments within a business (internal benchmarking), comparing similar work areas or functions with industry leaders (functional benchmarking), or comparing similar products and services with that of competitors (competitive benchmarking).
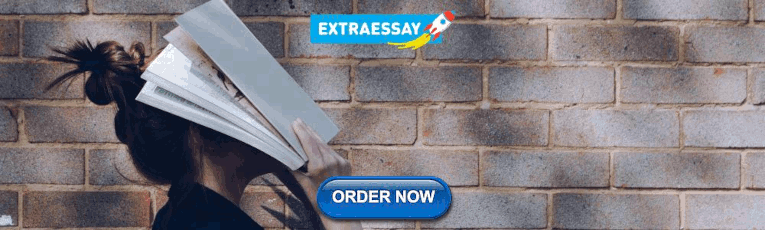
Poka-yoke (Mistake Proofing)
This technique's name comes from the Japanese phrase meaning "to avoid errors," and entails preventing the chance of mistakes from occurring. In the poka-yoke technique, employees spot and remove inefficiencies and human errors during the manufacturing process.
Value Stream Mapping
The value stream mapping technique charts the current flow of materials and information to design a future project. The objective is to remove waste and inefficiencies in the value stream and create leaner operations. It identifies seven different types of waste and three types of waste removal operations.
- Cause and Effect Analysis
- Pareto Chart
- Check Sheet
- Scatter Plot
- Control Chart
The Six Sigma training levels conform to specified training requirements, education criteria, job standards, and eligibility.
This is the simplest stage, where:
- Any newcomer can join.
- People work with teams on problem-solving projects.
- The participant is required to understand the basic Six Sigma concepts.
Yellow Belt
Here, the participant:
- Takes part as a project team member.
- Reviews process improvements.
- Gains understanding of the various methodologies, and DMAIC.
Green level
This level of expertise requires the following criteria:
- Minimum of three years of full-time employment.
- Understand the tools and methodologies used for problem-solving.
- Hands-on experience on projects involving some level of business transformation.
- Guidance for Black Belt projects in data collection and analysis.
- Lead Green Belt projects or teams.
Black Level
This level includes the following:
- Minimum of three years of full-time employment
- Work experience in a core knowledge area
- Proof of completion of a minimum of two Six Sigma projects
- Demonstration of expertise at applying multivariate metrics to diverse business change settings
- Leading diverse teams in problem-solving projects.
- Training and coaching project teams.
Master Black Belt
To reach this level, a candidate must:
- Be in possession of a Black Belt certification
- Have a minimum of five years of full-time employment, or Proof of completion of a minimum of 10 Six Sigma projects
- A proven work portfolio, with individual specific requirements, as given here , for instance.
- Have coached and trained Green Belts and Black Belts.
- Develop key metrics and strategies.
- Have worked as an organization's Six Sigma technologist and internal business transformation advisor.
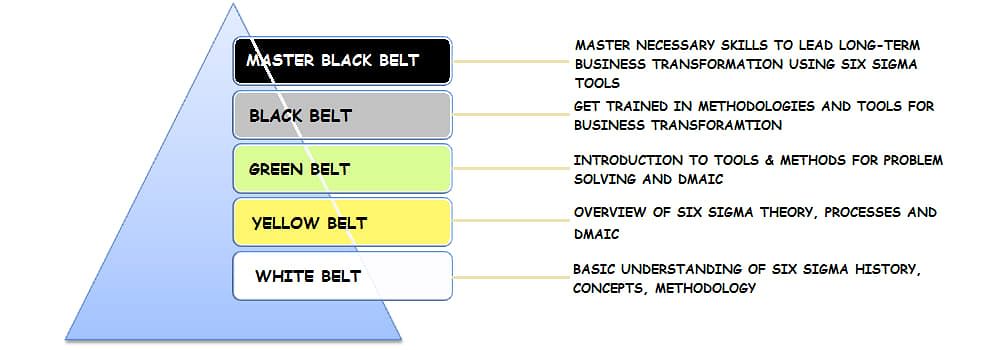
Fig: The five-tiered levels of Six Sigma Certification
Six Sigma is widely adopted by many industries such as manufacturing, healthcare, finance, and retail, and offers a range of career opportunities with attractive salary prospects. Here are some career choices and salary prospects in Six Sigma:
- Six Sigma Consultant: A Six Sigma consultant advises organizations on process improvements, identifies areas for cost savings, and develops strategies for implementation. The average salary for a Six Sigma consultant is around $96,000 per year.
- Six Sigma Project Manager: A Six Sigma project manager oversees Six Sigma projects, manages project teams, and ensures successful implementation of process improvements. The average salary for a Six Sigma project manager is around $107,000 per year.
- Six Sigma Black Belt : A Six Sigma Black Belt is responsible for leading Six Sigma projects, training team members, and ensuring sustained process improvements. The average salary is around $110,000 per year.
- Six Sigma Master Black Belt: It is the highest level of Six Sigma certification and is responsible for leading organizational Six Sigma initiatives, coaching and mentoring Six Sigma Black Belts and Green Belts, and driving business transformation. The average salary for a Six Sigma Master Black Belt is around $140,000 per year.
- Quality Manager: A Quality Manager ensures that an organization's products or services meet customer expectations, industry standards, and regulatory requirements. Six Sigma certification can be valuable for this role, and the average salary for a Quality Manager is around $91,000 per year.
Overall, Six Sigma offers various career opportunities with competitive salary prospects. Individuals with Six Sigma certification can expect higher salaries and better job prospects than those without certification.
So whether you are a graduate in any stream, an engineer, or an MBA professional, if you want to enhance your career prospects and salary gains, then make sure to get certified in Six Sigma courses. Begin with a Green Belt and climb your way up to Master Black belt to command your salary. As a fresher, you can start learning Six Sigma principles by enrolling into Simplilearn's Green Belt certificate program , and then avail the higher certificate levels as you gain work and project experience.
1. How Can You Get Six Sigma Certification?
Understanding the Management Philosophy of Your Organization, selecting between Six Sigma and Lean Six Sigma, determining which Level Suits You, learning about the Tests Associated with it, Enrolling in a Training Course, and obtaining Your Certification are the steps to obtaining Six Sigma Certification.
2. What Does Six Sigma Mean?
Six Sigma is a quality improvement methodology for businesses that counts the number of flaws in a process and aims to systematically fix them. Businesses utilize it to get rid of flaws and enhance any of their procedures in an effort to increase earnings.
3. What Is the Difference Between Six Sigma and Lean Six Sigma?
Lean and Six Sigma vary primarily in that Lean frequently affects all aspects of an organization rather than being solely focused on production. These two strategies are combined by Lean Six Sigma to produce a potent toolkit for dealing with waste reduction.
4. What Are the Steps of Six Sigma?
Six Sigma's five steps adhere to a methodology known to business insiders as DMAIC. The words "define, measure, analyze, enhance, and control" are all spelled out in this acronym.
5. What is Lean Six Sigma?
Lean Six Sigma is a method for improving performance by systematically removing waste and reducing variation that relies on a collaborative team effort. Increased performance and decreased process variation contribute to defect reduction and improvements in profits, employee morale, and product or service quality.
6. What is continuous improvement?
Continuous improvement (also known as "rapid improvement") is a Lean improvement technique that aids in workflow optimization. The Lean method of working allows for efficient workflows that save time and money, allowing you to cut down on wasted time and effort.
7. What is Lean Six Sigma Yellow Belt?
A Certified Lean Six Sigma Yellow Belt from the Council for Six Sigma Certification (CSSC) is someone who has a basic understanding of Six Sigma but does not lead projects on their own. They are frequently in charge of creating process maps to support Six Sigma projects.
8. What is Lean Six Sigma Green Belt?
Six Sigma Green Belt is a certification course that provides you with hands-on experience with over 100 tools and techniques. These techniques are required for participation in DMAIC improvement projects. DMAIC is an acronym that stands for Define, Measure, Analyze, Improve, and Control.
9. What is Lean Six Sigma Black Belt?
A Lean Six Sigma Black Belt has a thorough understanding of all aspects of the Lean Six Sigma Method, including a high level of competence in the Define, Measure, Analyze, Improve, and Control (DMAIC) phases as defined by the IASSC.
10. What are the Five Key Six Sigma Principles?
The success of Six Sigma relies on five fundamental principles:Customer Focus, Data-Driven Analysis, Proactive Improvement, Cross-Functional Collaboration, and Thoroughness and Flexibility.
11. What are Six Sigma steps?
The Six Sigma Methodology consists of five stages driven by data — Define, Measure, Analyze, Improve, and Control (DMAIC).
12. What is Six Sigma with an example?
Six Sigma is a data-driven methodology used to improve processes by minimizing defects and variations. For example, a manufacturing company may use Six Sigma to reduce the number of defective products produced by optimizing their production process.
13. What are Six Sigma tools?
14. what is the six sigma formula.
Utilizing the equation Y = f(x) aids in identifying cause and effect relationships within a project, enabling performance measurement and the discovery of areas for enhancement.
Our Quality Management Courses Duration And Fees
Explore our top Quality Management Courses and take the first step towards career success
Recommended Reads
Free eBook: Guide to the Six Sigma Certifications
Lean Six Sigma Black Belt (LSSBB) Certification
Top Six Leadership Skills That You Should Master for Workplace Success
Digital Transformation in Banking: Why Now, and How?
Six Sigma Green Belt Salary: Top Paying Countries and Industries
25 Digital Marketing Skills To Master
Get Affiliated Certifications with Live Class programs
- PMP, PMI, PMBOK, CAPM, PgMP, PfMP, ACP, PBA, RMP, SP, and OPM3 are registered marks of the Project Management Institute, Inc.

- Certified Six Sigma Green Belt (CSSGB)
- Certified Six Sigma Black Belt (CSSBB)
- Certified Six Sigma Master Black Belt (CSSMBB)
- Certified Six Sigma Champion (CSSC)
- Certified Six Sigma Deployment Leader (CSSDL)
- Certified Six Sigma Yellow Belt (CSSYB)
- Certified Six Sigma Trainer (CSSTRA)
- Certified Six Sigma Coach (CSSCOA)
- Register Your Six Sigma Certification Program
- International Scrum Institute
- International DevOps Certification Academy
- International Organization for Project Management (IO4PM)
- International Software Test Institute
- International MBA Institute
- Your Blog (US Army Personnel Selected Six Sigma Institute)
- Our Industry Review and Feedback
- Our Official Recognition and Industry Clients
- Our Corporate Partners Program
- Frequently Asked Questions (FAQ)
- Shareable Digital Badge And Six Sigma Certifications Validation Registry (NEW)
- Recommend International Six Sigma Institute To Friends
- Introducing: World's First & Only Six Sigma AI Assistant (NEW)
- Your Free Six Sigma Book
- Your Free Premium Six Sigma Training
- Your Sample Six Sigma Certification Test Questions
- Your Free Six Sigma Events
- Terms and Conditions
- Privacy Policy
What is Six Sigma Methodology? Detailed Guide to the Six Sigma Process
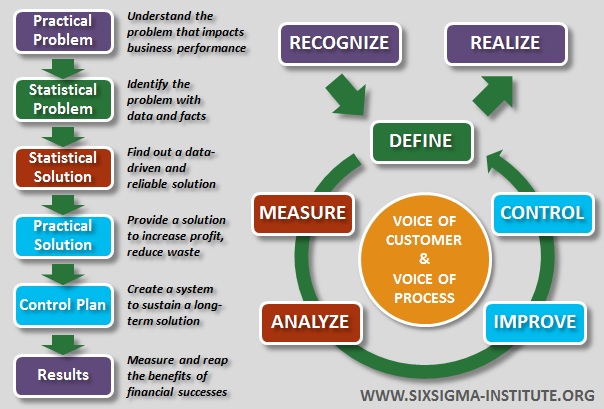
The key principles of the Six Sigma methodology include process improvement, reduction of variation, data-driven decision-making, and a focus on achieving 3.4 defects per million opportunities. By following the DMAIC approach (Define, Measure, Analyze, Improve, Control) and utilizing statistical tools, organizations can systematically improve their processes and enhance overall quality.
What is Six Sigma?
- A Business Strategy: Using Six Sigma Methodology, a business can strategize its plan of action and drive revenue increase, cost reduction and process improvements in all parts of the organization.
- A Vision: Six Sigma Methodology helps the Senior Management create a vision to provide defect free, positive environment to the organization.
- A Benchmark: Six Sigma Methodology helps in improving process metrics. Once the improved process metrics achieve stability; we can use Six Sigma methodology again to improve the newly stabilized process metrics. For example: The Cycle Time of Pizza Delivery is improved from 60 minutes to 45 minutes in a Pizza Delivery process by using Six Sigma methodology. Once the Pizza Delivery process stabilizes at 45 minutes, we could carry out another Six Sigma project to improve its cycle time from 45 minutes to 30 minutes. Thus, it is a benchmark.
- A Goal: Using Six Sigma methodology, organizations can keep a stringent goal for themselves and work towards achieving them during the course of the year. Right use of the methodology often leads these organizations to achieve these goals.
- A Statistical Measure: Six Sigma is a data driven methodology. Statistical Analysis is used to identify root-causes of the problem. Additionally, Six Sigma methodology calculates the process performance using its own unit known as Sigma unit.
- A Robust Methodology: Six Sigma is the only methodology available in the market today which is a documented methodology for problem solving. If used in the right manner, Six Sigma improvements are bullet-proof and they give high yielding returns.
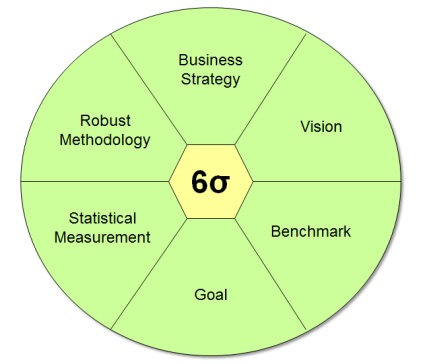
Six Sigma Methodology Fundamentals
First off, Six Sigma emphasizes the importance of defining customer requirements with precise clarity. Before embarking on any process improvement initiative, it’s vital to comprehend what customers value and expect from the products or services being delivered. Meeting these requirements is essential for customer satisfaction and loyalty.
Process Management and Improvement
Mapping and analyzing processes, implementing process changes.
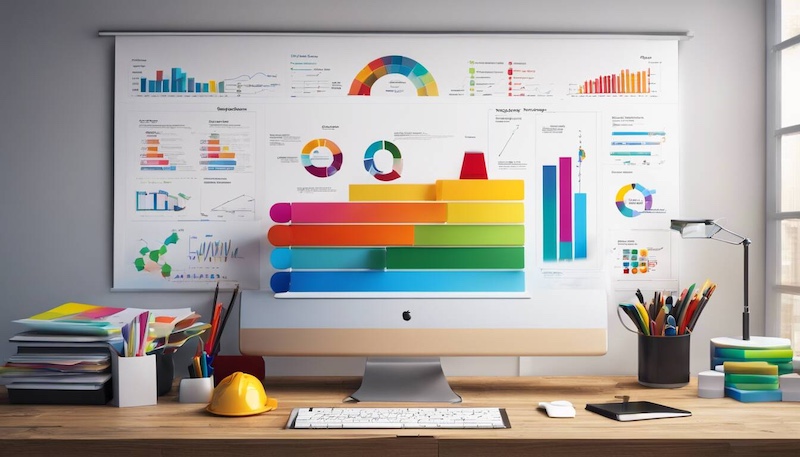
Statistical Analysis in Six Sigma
Effective measurement systems, defining key metrics, data collection and analysis.
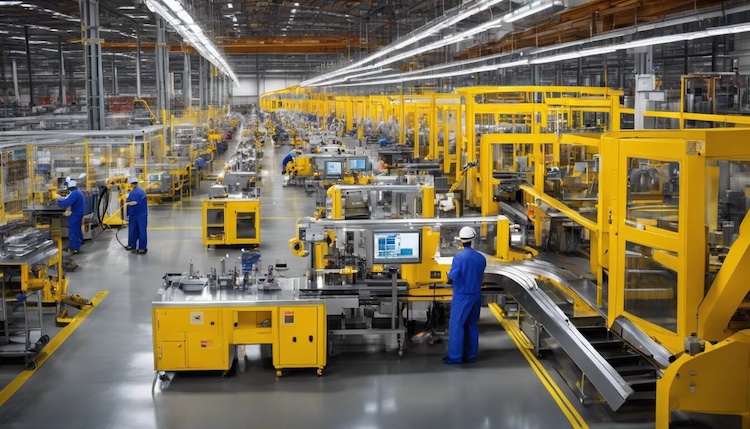
Incorporating Six Sigma Principles
When it comes to adopting Six Sigma principles within an organization, it's not just about implementing a new set of rules; it's about cultivating a philosophy of continuous improvement and quality excellence. This necessitates fostering a mindset where every employee in the organization is committed to making small changes that add up to significant improvement over time. The essence of Six Sigma lies in using data to drive decisions and focusing on meeting customer requirements.
Deployment of Six Sigma Tools
Use of statistical process control (spc), control charts and process mapping, failure mode and effects analysis (fmea).
The integrated approach offered by these tools plays a vital role in achieving significant enhancements in processes and products, ultimately driving business bottom-line by increasing profits and customer satisfaction. Combining these robust methods enables organizations to not only identify areas for improvement but also take concrete actions to enhance operational efficiency and deliver superior quality products or services.
Frequently Asked Questions About Six Sigma Methodology
Can you provide examples of successful implementation of six sigma methodology, what industries typically use six sigma methodology, how long does it typically take for an organization to fully adopt and implement six sigma methodology, are there any drawbacks or limitations to using six sigma methodology.
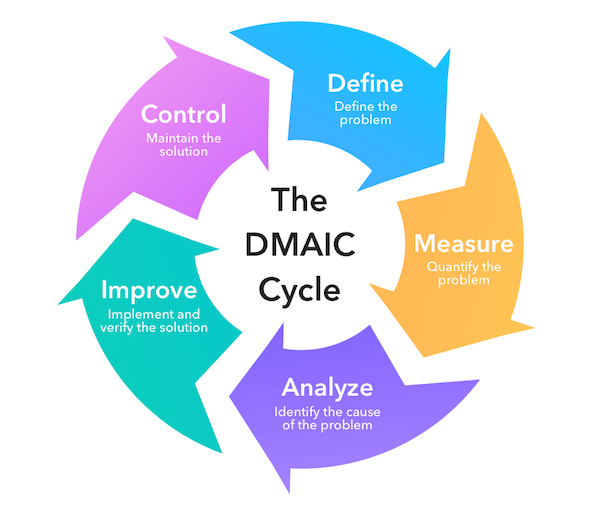
What are the key principles and tools used in six sigma methodology?
What are the benefits of implementing the six sigma methodology, what industries commonly use the six sigma methodology, who should be involved in the implementation of the six sigma methodology within an organization, where can i find online training courses for six sigma methodology, where can i find books or literature on advanced concepts of six sigma methodology, what is the difference between six sigma and lean six sigma, six sigma methodology recap.
In summary, Six Sigma methodology is a robust and data-driven approach designed to enhance process efficiency and minimize defects. Its core principles include defining, measuring, analyzing, improving, and controlling processes, providing organizations with a structured framework for continuous improvement. By focusing on statistical methods and strategic problem-solving, Six Sigma aims to achieve excellence in operations and customer satisfaction.
Your Six Sigma Training Table of Contents
We guarantee that your free online training will make you pass your six sigma certification exam.
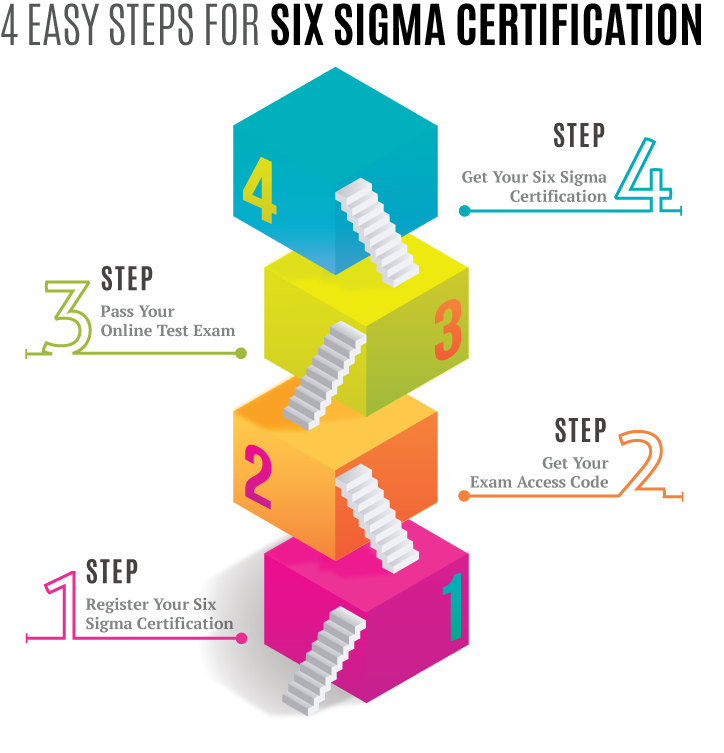
THE ONLY BOOK. YOU CAN SIMPLY LEARN SIX SIGMA.
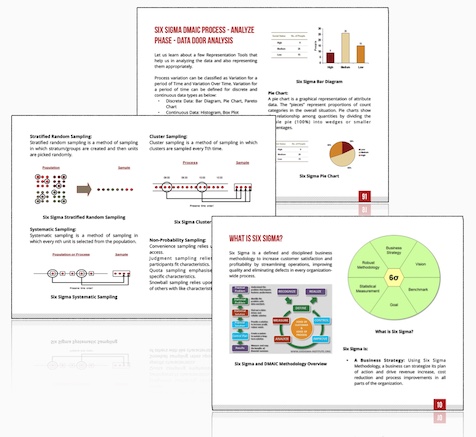
YOUR SIX SIGMA REVEALED 2ND EDITION IS NOW READY. CLICK BOOK COVER FOR FREE DOWNLOAD...
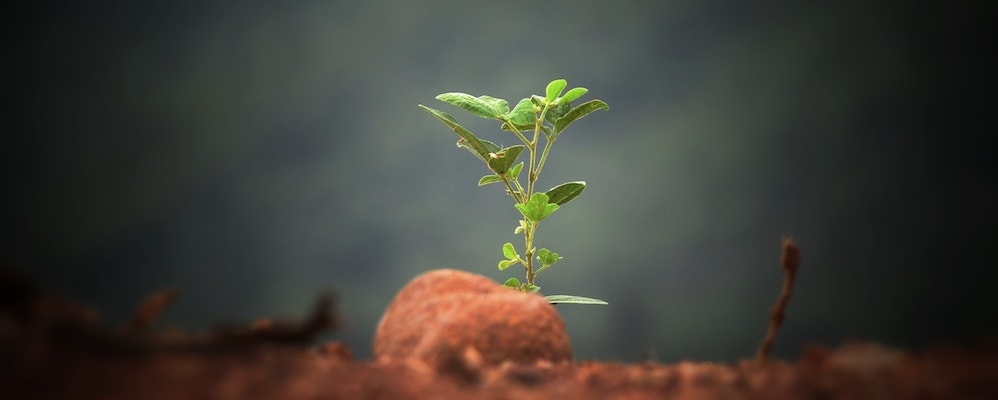
What Is Six Sigma?
Published: June 14, 2022 by Ken Feldman
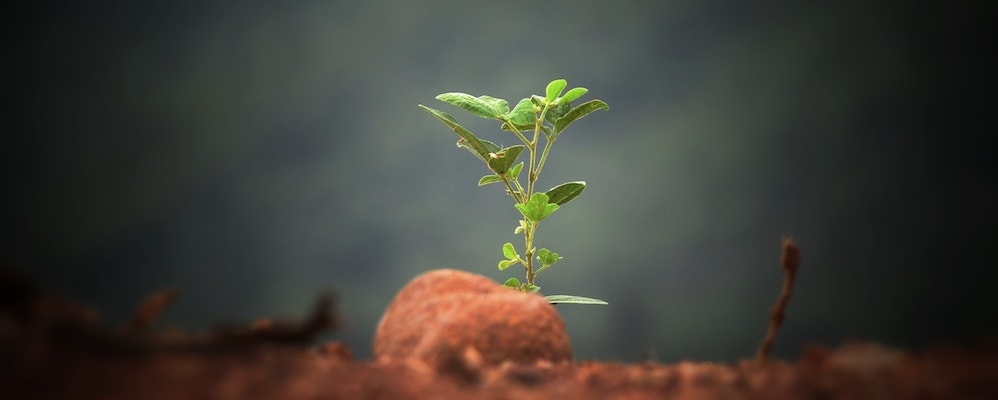
In 1959, there was a commercial for mints where a set of twin girls argued whether Certs was a candy mint or a breath mint. Today, there are similar arguments about what Six Sigma is. Some say it is a statistical symbol and metric. Others describe it as a management philosophy. And many claim it is an improvement methodology. They are all correct.
Six Sigma at many organizations simply means a measure of quality that strives for near perfection. Six Sigma is a disciplined, data-driven approach and methodology for eliminating defects (driving toward six standard deviations between the mean and the nearest specification limit) in any process — from manufacturing to transactional and from product to service.
We will get into all of these finer points of what Six Sigma is, but first, let’s take a trip down memory lane and review the early development and evolution of Six Sigma. The focus will be on the foundational elements, people, and companies. Six Sigma continues to evolve today.
1798 — Eli Whitney introduced the foundation for the assembly line.
1809 — One of the central pillars of statistical theory used in Six Sigma is the Normal Distribution, which was developed by the German mathematician Friedrich Gauss.
1913 — Henry Ford introduced his automobile assembly line and the concept of product standardization.
1924 — Dr. Walter A. Shewhart developed the control chart to better understand the difference between common and special cause variation. Shewhart also introduced the PDCA (Plan-Do-Check-Act) in 1929 which was made popular by Dr. W. Edwards Deming in the 1950s. PDCA served as the basis for the development of the Six Sigma methodology, DMAIC.
1950 — Dr. W. Edwards Deming, at the invitation of General McArthur, went to Japan to explain the application of statistical concepts in industrial processes.
1954 — Joseph Juran was invited to visit Japan to share his quality concepts.
1986 — Bill Smith, an engineer at Motorola along with several other people including Dr. Mikel Harry and CEO Bob Galvin, developed the idea and term Six Sigma to significantly reduce product defects. Smith is known as the Father of Six Sigma. Smith and Harry worked together to come up with a four-stage problem-solving approach: measure, analyze, improve, control (MAIC), which became a cornerstone for the Six Sigma process, later called DMAIC.
1987 — The Malcolm Baldrige National Quality Award was created to recognize U.S. organizations for performance excellence. Motorola was one of the three winners during this inaugural year.
1993 — Allied Signal, under the leadership of Larry Bossidy, adopted Six Sigma. Bossidy then tells his friend Jack Welch, the CEO of GE, about Six Sigma. Anecdotally, this took place during a golf game.
1994 — Dr. Mikel Harry, along with Mr. Richard Schroeder establish the Six Sigma Academy as the prime contractor for implementing Six Sigma at Allied Signal. They become a driving force for the expansion of Six Sigma.
1995 — General Electric started their Six Sigma journey in 1995 under the leadership of Jack Welch, the CEO. Dr. Mikel Harry trains the first wave of Master Black Belts at GE.
Today, you will see most organizations using Lean Six Sigma rather than the pure Six Sigma used by the early adopters of Six Sigma. Lean Six Sigma first emphasizes the use of Lean methodologies and tools to identify and remove waste and increase process velocity. Then Six Sigma methodologies and tools are used to identify and reduce or remove process variation and improve the process, all within the context of customer expectations and requirements.
Six Sigma as a statistical symbol and metric
Sigma (σ) is a Greek letter and symbol defining the standard deviation of a population. By adding and subtracting the value of three standard deviations to the mean or average of your data, you should encompass approximately 99.73% of your data, according to the Empirical Rule and relates to the Normal Distribution.
A process is often described as being Six Sigma if the closest specification is at least six standard deviations away from the mean. If your specification is that far away, then Six Sigma will be defined as a process having 3.4 defects per million opportunities (DPMO).
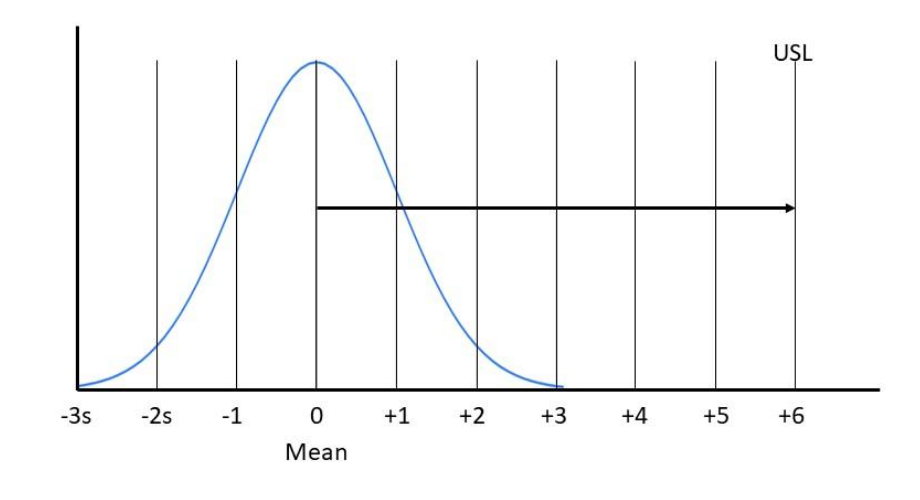
Six Sigma as a management philosophy
While there may be some differences in what principles to include to define Six Sigma as a philosophy, many agree that Six Sigma is based on the principles of:
- Everything is a process
- Customer focus
- Reduction of variation
- Data driven decision-making
- Continuous improvement of everything you do
Six Sigma as an improvement methodology
Unfortunately, a philosophy alone won’t create change or improvement in your organization. You will need to implement and execute a structured methodology driven by senior leadership commitment and engagement and widespread organizational involvement. This will encompass structure, definable roles, methods, and tools. Let’s look at each element.
The improvement in your organizational processes will primarily be a result of teams of employees executing improvement projects linked to key strategic, tactical, and operational improvement opportunities.
The structure of your Six Sigma deployment should include leadership commitment and engagement along with specialized resources to support and guide your teams in the use of specific Six Sigma tools and methodologies.
Definable roles
Dr. Mikel Harry is often credited with adapting the martial art concept of belt rankings to Six Sigma. The hierarchy of belts indicates the level of training, competency, and acquisition of skills. While different organizations may have different names and colors for the levels of expertise in Six Sigma, the following represents the most common levels of achievement with the Master Black Belt being the most advanced and White Belt being an introductory level. The Champion serves the role as a deployment leader.
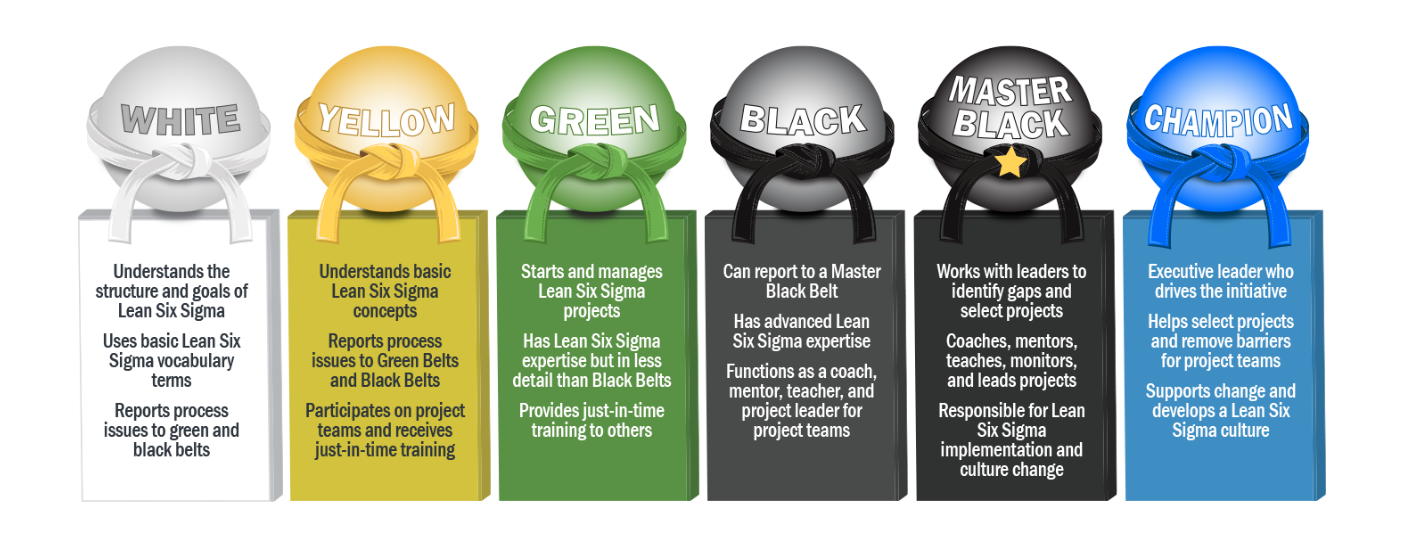
There are two broad categories of roles in your Six Sigma deployment. One involves the individuals responsible for the overall execution and eventual success of the program effort. The other main role is associated with the portfolio of improvement projects. Here is a description of the program roles:

Here are the project roles:

There are multiple methodologies in Six Sigma. Some are designed for continuous incremental improvements while others are for dramatic breakthrough change. The most common Six Sigma method is known as DMAIC. The graphic below shows this structured 5 stage sequential approach.
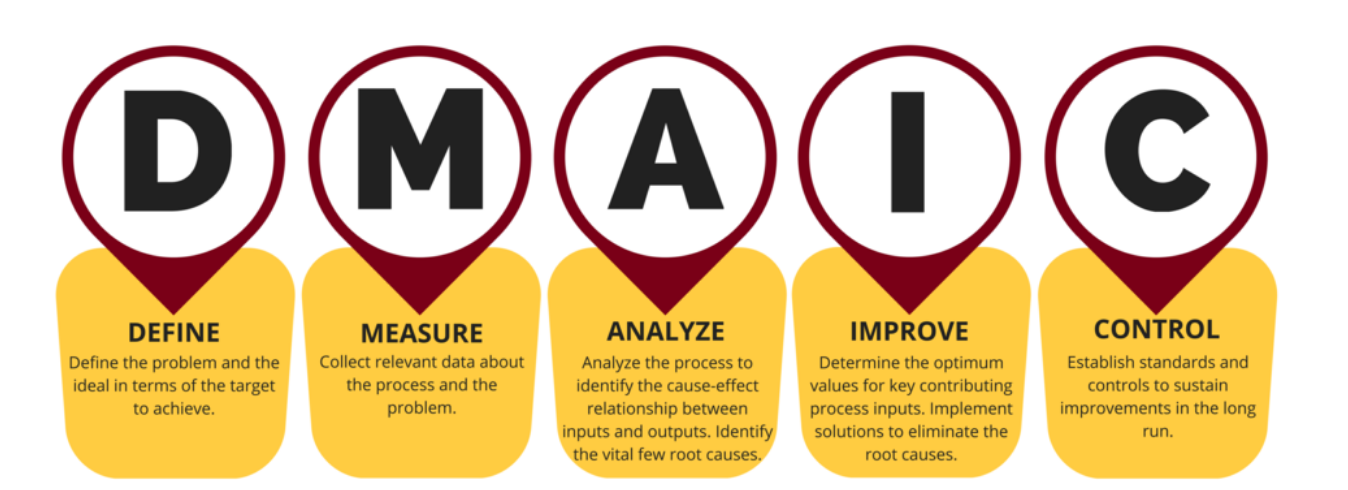
Your project team will follow the DMAIC stages while completing specific activities and deliverables. Most projects can be completed within 3 to 4 months of time depending on the complexity of the project and the time allocated to each stage.
There are similar methodologies and approaches for making more dramatic improvements or for situations where there are no existing processes. While the acronyms are different, the underlying activities and outcomes are quite similar. The more popular approaches are called DMADV (Define, Measure, Analyze, Design and Verify), DfSS (Design for Six Sigma) and DMEDI (Define, Measure, Explore, Develop, Implement).
Here is a comparison of DMAIC and DMEDI:

While there are almost more Six Sigma tool than a person can count, here are a few of the most common ones listed for each stage of DMAIC.
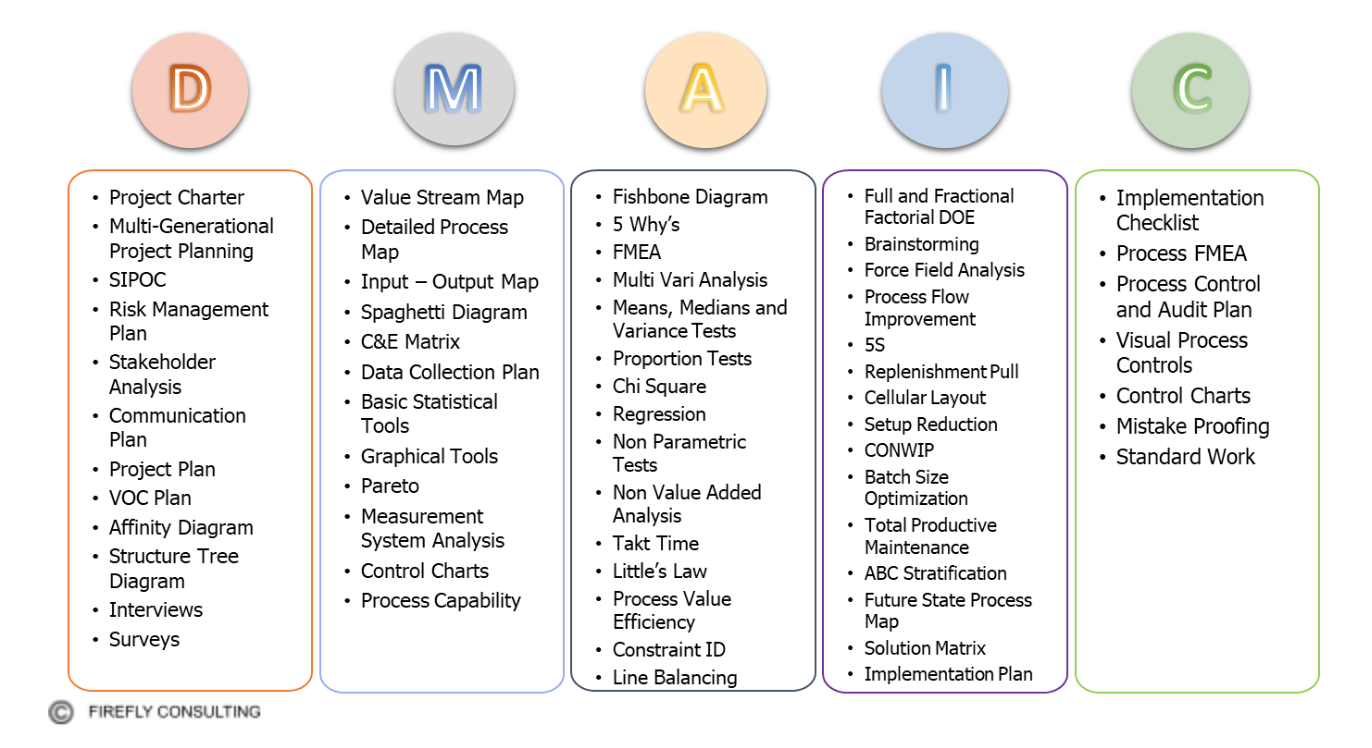
It is not expected that you use every tool for every project. Depending on the specifics of your project, you will select and use the most relevant ones.
Careers in Six Sigma
While you may see postings for employment in Six Sigma roles for a Deployment Champion, Master Black Belt (MBB) and Black Belt (BB), the most frequent will be for the MBB and BB. These are considered full time professional level positions. While you might see a required or recommended Green Belt (GB) as part of a more extensive list of job requirements, the GB is a part time role and is rarely a standalone job posting.
According to the website salary.com , as of May 2022, the salary ranges for a Master Black Belt range from $120,000 to $206,000 with a median salary of $162,700. The ranges for a Black Belt are listed as $92,000 to $145,000 with a median salary of $126,000. Salary ranges will vary widely depending on such factors as, education, certifications, additional skills, experience, and geographic location.
Benefits of Six Sigma for your organization
Many organizations have implemented Six Sigma and, while individual results may have varied, there are a core set of benefits which they all should have achieved. They are:
- Increased productivity, efficiency, and effectiveness
- Improved quality of product and services and a reduction in waste
- Reduced operating costs and process variation
- Higher customer satisfaction and competitive advantage
- Improved communication and employee engagement
Whether you call your improvement effort Six Sigma, Operational Excellence, Zero Defects, Total Quality Management, Continuous Improvement or any other name, the elements should be the same. Your purpose is to improve everything your organization does. Your approach should be structured, and data driven. Using DMAIC and other methodologies will provide the roadmap for your improvement journey.
You will need to have your senior leadership committed and engaged to have any chance for long term success. You will likely need expert resources. Whether you call them Master Black Belts, Black Belts or Green Belts isn’t as important as the skills they must have to help drive change throughout your organization.
Change won’t happen overnight. It took GE three years to “get it”. Yes, you will get early successes but remain patient because it might be 5 years before you see the transformation throughout your organization. Six Sigma works. The key is whether you and your organization can embrace it and make it work for you.
About the Author
Ken Feldman
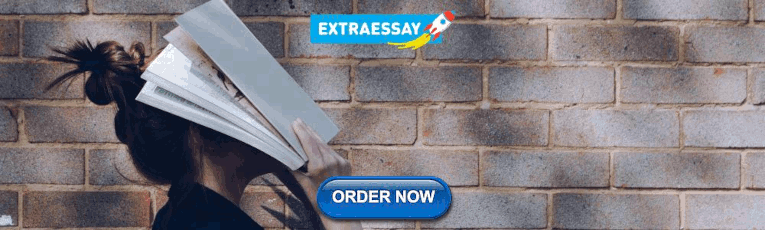
IMAGES
VIDEO