Open Access is an initiative that aims to make scientific research freely available to all. To date our community has made over 100 million downloads. It’s based on principles of collaboration, unobstructed discovery, and, most importantly, scientific progression. As PhD students, we found it difficult to access the research we needed, so we decided to create a new Open Access publisher that levels the playing field for scientists across the world. How? By making research easy to access, and puts the academic needs of the researchers before the business interests of publishers.
We are a community of more than 103,000 authors and editors from 3,291 institutions spanning 160 countries, including Nobel Prize winners and some of the world’s most-cited researchers. Publishing on IntechOpen allows authors to earn citations and find new collaborators, meaning more people see your work not only from your own field of study, but from other related fields too.
Brief introduction to this section that descibes Open Access especially from an IntechOpen perspective
Want to get in touch? Contact our London head office or media team here
Our team is growing all the time, so we’re always on the lookout for smart people who want to help us reshape the world of scientific publishing.
Home > Books > Environmental Management in Practice
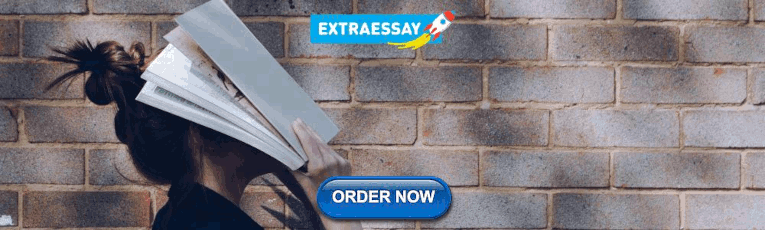
The Effects of Paper Recycling and its Environmental Impact
Submitted: 24 November 2010 Published: 05 July 2011
DOI: 10.5772/23110
Cite this chapter
There are two ways to cite this chapter:
From the Edited Volume
Environmental Management in Practice
Edited by Elzbieta Broniewicz
To purchase hard copies of this book, please contact the representative in India: CBS Publishers & Distributors Pvt. Ltd. www.cbspd.com | [email protected]
Chapter metrics overview
12,953 Chapter Downloads
Impact of this chapter
Total Chapter Downloads on intechopen.com

Total Chapter Views on intechopen.com
Overall attention for this chapters
Author Information
Iveta čabalová *.
- Technical University in Zvolen,Faculty of Wood Sciences and Technology, Slovakia
František Kačík
Anton geffert *, danica kačíková *.
*Address all correspondence to:
1. Introduction
It is well known the paper production (likewise the other brands of industry) has enormous effects on the environment. The using and processing of raw materials has a variety of negative effects on the environment.
At the other hand there are technologies which can moderate the negative impacts on the environment and they also have a positive economical effect. One of these processes is the recycling, which is not only the next use of the wastes. The main benefit of the recycling is a double decrease of the environment loading, known as an environmental impact reducing. From the first view point, the natural resources conserves at side of the manufacturing process inputs, from the second view point, the harmful compounds amount leaking to the environment decreases at side of the manufacturing process outputs.
The paper production from the recycled fibers consumes less energy; conserves the natural resources viz. wood and decreases the environmental pollution. The conflict between economic optimization and environmental protection has received wide attention in recent research programs for waste management system planning. This has also resulted in a set of new waste management goals in reverse logistics system planning. Pati et al. (2008 ) have proposed a mixed integer goal programming (MIGP) model to capture the inter-relationships among the paper recycling network system. Use of this model can bring indirectly benefit to the environment as well as improve the quality of waste paper reaching the recycling unit.
In 2005, the total production of paper in Europe was 99.3 million tonnes which generated 11 million tonnes of waste, representing about 11% in relation to the total paper production. The production of recycled paper, during the same period, was 47.3 million tonnes generating 7.7 million tonnes of solid waste (about 70% of total generated waste in papermaking) which represents 16% of the total production from this raw material ( CEPI 2006 ).
The consumption of recovered paper has been in continuous growth during the past decades. According to the Confederation of European Paper Industries (CEPI), the use of recovered paper was almost even with the use of virgin fiber in 2005. This development has been boosted by technological progress and the good price competitiveness of recycled fiber, but also by environmental awareness – at both the producer and consumer ends – and regulation that has influenced the demand for recovered paper. The European paper industry suffered a very difficult year in 2009 during which the industry encountered more down-time and capacity closures as a result of the weakened global economy. Recovered paper utilisation in Europe decreased in 2009, but exports of recovered paper to countries outside CEPI continued to rise, especially to Asian markets (96.3%). However, recycling rate expressed as “volume of paper recycling/volume of paper consumption” resulted in a record high 72.2% recycling rate after having reached 66.7% the year before ( Fig. 1 ) ( Hujala et al. 2010 ;CEPI 2006; European Declaration on Paper Recycling 2010; Huhtala& Samakovlis 2002 ; CEPI Annual Statistic 2010).

European paper recycling 1995-2009 in million tonnes (European Declaration on Paper Recycling 2006 – 2010, Monitoring Report 2009 (2010) (www.erpa.info)
Recycling is not a new technology. It has become a commercial proposition since Matthias Koops established the Neckinger mill, in 1826, which produced white paper from printed waste paper. However, there were very few investigations into the effect of recycling on sheet properties until late 1960's. From then until the late 1970's, a considerable amount of work was carried out to identify the effects of recycling on pulp properties and the cause of these effects ( Nazhad 2005 ; Nazhad& Paszner 1994 ). In the late 1980's and early 1990's, recycling issues have emerged stronger than before due to the higher cost of landfills in developed countries and an evolution in human awareness. The findings of the early 70's on recycling effects have since been confirmed, although attempts to trace the cause of these effects are still not resolved ( Howard &Bichard 1992 ).
Recycling has been thought to reduce the fibre swelling capability, and thus the flexibility of fibres. The restricted swelling of recycled fibres has been ascribed to hornification, which has been introduced as a main cause of poor quality of recycled paper ( Scallan&Tydeman 1992 ). Since 1950's, fibre flexibility among the papermakers has been recognized as a main source of paper strength. Therefore, it is not surprising to see that, for over half a century, papermakers have supported and rationalized hornification as a main source of tensile loss due to drying, even though it has never been fully understood ( Sutjipto et al. 2008 ).
Recycled paper has been increasingly produced in various grades in the paper industry. However, there are still technical problems including reduction in mechanical strength for recycled paper. Especially, chemical pulp-origin paper, that is, fine paperrequires a certain level of strength. Howard & Bichard (1992 ) reported that beaten bleachedkraft pulp produced handsheets which were bulky and weak in tensile and burst strengthsby handsheet recycling. This behaviour could be explained by the reduction in re-swelling capability or the reduction in flexibility of rewetted pulp fibers due to fiber hornification and, possibly, by fines loss during recycling processes, which decrease both total bondingarea and the strength of paper ( Howard 1995 ; Nazhad&Paszner 1994 ; Nazhad et al. 1995 ; Khantayanuwong et al.2002 ; Kim et al. 2000 ).
Paper recycling is increasingly important for the sustainable development of the paper industry as an environmentally friendly sound. The research related to paper recycling is therefore increasingly crucial for the need of the industry. Even though there are a number of researches ascertained the effect of recycling treatment on properties of softwood pulp fibres ( Cao et al. 1999 ; Horn 1975 ; Howard&Bichard 1992 ; Jang et al. 1995 ), however, it is likely that hardwood pulp fibres have rarely been used in the research operated with recycling treatment. Changes in some morphological properties of hardwood pulp fibres, such as curl, kink, and length of fibre, due to recycling effects also have not been determined considerably. This is possibly because most of the researches were conducted in the countries where softwood pulp fibres are commercial extensively ( Khantayanuwong 2003 ). Therefore, it is the purpose of the present research to crucially determine the effect of recycling treatment on some important properties of softwood pulp fibres.
2. Alterations of pulp fibres properties at recycling
The goal of a recycled paper or board manufacturer is to make a product that meets customers΄ specification and requirements. At the present utilization rate, using recycled fibres in commodity grades such as newsprint and packaging paper and board has not caused noticeable deterioration in product quality and performance ( Čabalová et al. 2009 ). The expected increase in recovery rates of used paper products will require a considerable consumption increase of recycled fibres in higher quality grades such as office paper and magazine paper. To promote expanded use of recovered paper, understanding the fundamental nature of recycled fibres and the differences from virgin fibres is necessary.
Essentially, recycled fibres are contaminated, used fibres. Recycled pulp quality is, therefore, directly affected by the history of the fibres, i.e. by the origins, processes and treatments which these fibres have experienced.
McKinney (1995) classified the history into five periods:
fibre furnish and pulp history
paper making process history
printing and converting history
consumer and collection history
recycling process history.
To identity changes in fibre properties, many recycling studies have occurred at laboratory. Realistically repeating all the stages ofthe recycling chain is difficult especially when including printing and deinking. Some insight into changes in fibre structure, cell wall properties, and bonding ability is possible from investigations using various recycling procedures, testing methods, and furnishes.
Mechanical pulp is chemically and physically different from chemical pulp then recycling effect on those furnishes is also different. When chemical fibres undergo repeated drying and rewetting, they are hornified and can significantly lose their originally high bonding potential ( Somwand et al. 2002 ; Song & Law 2010 ; Kato & Cameron 1999 ; Bouchard & Douek 1994 ; Khantayanuwong et al. 2002 ; Zanuttini et al. 2007 ; da Silva et al. 2007 ). The degree of hornification can be measured by water retention value (WRW) ( Kim et al. 2000 ). In contrast to the chemical pulps, originally weakermechanical pulps do not deteriorate but somewhat even improve bonding potential during a corresponding treatment. Several studies( Maloney et al. 1998 ; Weise 1998 ; Ackerman et al. 2000 ) have shown good recyclability of mechanical fibres.
Adámková a Milichovský (2002 ) present the dependence of beating degree ( SR –Schopper-Riegler degree) and WRV from the relative length of hardwood and softwood pulps. From their results we can see the WRV increase in dependence on the pulp length alteration is more rapid at hardwood pulp, but finally this value is higher at softwood pulps. Kim et al. (2000 ) determined the WRV decrease at softwood pulps with the higher number of recycling (at zero recycling about cca 1.5 g/g at fifth recycling about cca 1.1 g/g).Utilisation of the secondary fibres to furnish at paper production decrease of the initial need of woody raw (less of cutting tress) but the paper quality is not significantly worse.
2.1. Paper recycling
The primary raw material for the paper production is pulps fibres obtaining by a complicated chemical process from natural materials, mainly from wood. This fibres production is very energy demanding and at the manufacturing process there are used many of the chemical matters which are very problematic from view point of the environment protection. The suitable alternative is obtaining of the pulp fibres from already made paper. This process is far less demanding on energy and chemicals utilisation. The paper recycling, simplified, means the repeated defibring, grinding and drying, when there are altered the mechanical properties of the secondary stock, the chemical properties of fibres, the polymerisation degree of pulp polysaccharidic components, mainly of cellulose, their supramolecular structure, the morphological structure of fibres, range and level of interfibres bonds e.g.. The cause of above mentioned alterations is the fibres ageing at the paper recycling and manufacturing, mainly the drying process.
At the repeat use of the secondary fibres, it need deliberate the paper properties alter due to the fiber deterioration during the recycling, when many alteration are irreversible. The alteration depth depends on the cycle’s number and way to the fibres use. The main problem is the decrease of the secondary pulp mechanical properties with the continuing recycling, mainly the paper strength ( Khantayanuwong et al. 2002 ; Jahan 2003 ; Hubbe & Zhang 2005 ; Garg & Singh 2006 ; Geffertová et al. 2008 ; Sutjipto et al. 2008 ). This decrease is an effect of many alterations, which can but need not arise in the secondary pulp during the recycling process. The recycling causes the hornification of the cell walls that result in the decline of some pulp properties. It is due to the irreversible alterations in the cells structure during the drying ( Oksanen et al. 1997 ; Kim et al. 2000 ; Diniz et al. 2004 ).
The worse properties of the recycled fibres in comparison with the primary fibres can be caused by hornification but also by the decrease of the hydrophilic properties of the fibres surface during the drying due to the redistribution or migration of resin and fat acids to the surface ( Nazhad& Paszner 1994 ; Nazhad 2005 ). Okayama (2002 ) observed the enormous increase of the contact angle with water which is related to the fiber inactivation at the recycling. This process is known as „irreversible hornification“.
Paper recycling saves the natural wood raw stock, decreases the operation and capital costs to paper unit, decrease water consumption and last but not least this paper processing gives rise to the environment preservation (e.g. 1 t of waste paper can replace cca 2.5 m 3 of wood).
A key issue in paper recycling is the impact of energy use in manufacturing.Processing waste paper for paper and board manufacture requires energy that isusually derived from fossil fuels, such as oil and coal. In contrast to the productionof virgin fibre-based chemical pulp, waste paper processing does not yield a thermalsurplus and thus thermal energy must be supplied to dry the paper web. If,however, the waste paper was recovered for energy purposes the need for fossil fuelwould be reduced and this reduction would have a favourable impact on the carbondioxide balance and the greenhouse effect. Moreover, pulp production based onvirgin fibres requires consumption of round wood and causes emissions of air-pollutingcompounds as does the collection of waste paper. For better paper utilization, an interactive model, the Optimal Fibre Flow Model, considersboth a quality (age) and an environmental measure of waste paper recycling was developed ( Byström&Lönnstedt 1997 ).
2.1.1. Influence of beating on pulp fibres
Beating of chemical pulp is an essential step in improving the bonding ability of fibres. The knowledge complete about beating improves the present opinion of the fibres alteration at the beating. The main and extraneous influences of the beating device on pulps were defined.The main influences are these, each of them can be improve by the suitable beating mode, but only one alteration cannot be attained. Known are varieties of simultaneous changes in fibres, such as internal fibrilation, external fibrilation, fiber shortening or cutting, and fines formation ( Page 1989 ; Kang & Paulapuro 2006a ; Kang & Paulapuro 2006c ).
Freeing and disintegration of a cell wall affiliated with strongswelling expressed as an internal fibrilation and delamination. The delamination is a coaxial cleavage in the middle layer of the secondary wall.It causes the increased water penetration to the cell wall and the fibre plasticizing.
External fibrillation and fibrils peeling from surface, which particularly or fully attacks primary wall and outside layers of secondary walls.Simultaneously from the outside layers there arecleavage fibrils, microfibrils, nanofibrils to the macromolecule of cellulose and hemicelluloses.
Fibres shortening in any place in any angle-wise across fibre in accordance with loading, most commonly in weak places.
Concurrently the main effects at the beating also the extraneous effects take place, e.g. fines making, compression along the fibres axis, fibres waving due to the compression. It has low bonding ability and it influences the paper porosity,stocks freeness ( Sinke&Westenbroek 2004 ).
The beating causes the fibres shortening, the external and internal fibrillation affiliated with delamination and the fibres plasticizing. The outside primary wall of the pulp fibre leaks water little, it has usually an intact primary layer and a tendency to prevent from the swelling of the secondary layer of the cell wall. At the beating beginning there are disintegrated the fibre outside layers (P and S1), the fibrilar structure of the fibre secondary layer is uncovering, the water approach is improving, the swelling is taking place and the fibrillation process is beginning. The fibrillation process is finished by the weaking and cleavaging of the bonds between the particular fibrils and microfibrils of cell walls during the mechanical effect and the penetration into the interfibrilar spaces, it means to the amorphous region, there is the main portion of hemicelluloses.
Češek& Milichovský (2005 ) showed that with the increase of pulp beating degree the standard rheosettling velocity of pulp decreases more at the fibres fibrillation than at the fibres shortening.
Refining causes a variety of simultaneous changes in the fiber structure, such as internal fibrillation, external fibrillation and fines formation. Among these effects, swelling is commonly recognized as an important factor affecting the strength of recycled paper ( Kang & Paulapuro 2006d ).
Scallan & Tigerstrom (1991 ) observed the elasticity modulus of the long fibres from kraft pulp during the recycling. Flexibility decrease was evident at the beating degree decrease ( SR), and also with the increase of draining velocity of low-yield pulp.

Alteration of the breaking length of the paper sheet drying at the temperature of 80, 100 a 120°C during eightfold recycling
The selected properties of the pulp fibres and the paper sheets during the process of eightfold recycling at three drying temperatures of 80, 100, 120°C.
From the result on Fig. 2 we can see the increase of the pulp fibres active surface takes place during the beating process, which results in the improve of the bonding and the paper strength after the first beating. It causes also the breaking length increase of the laboratory sheets. The secondary fibres wear by repeated beating, what causes the decrease of strength values ( Table 1 ).
The biggest alterations of tear index ( Fig. 3 ) were observed after fifth recycling at the bleached softwood pulp fibres. The first beating causes the fibrillation of the outside layer of the cell wall, it results in the formation of the mechanical (felting) and the chemical bonds between the fibres. The repeated beating and drying dues, except the continuing fibrillation of the layer, the successive fibrils peeling until the peeling of the primary and outside secondary layer of the cell wall. It discovers the next non-fibriled layer S2 (second, the biggest layer of the secondary wall) what can do the tear index decrease. The next beating causes also this layer fibrillation, which leads to the increase of the strength value ( Fig. 3 , Tab. 1 ).Paper strength properties such as tensile strength and Scott bond strength were strongly influenced by internal fibrillation; these could also be increased further by promoting mostly external fibrillation ( Kang & Paulapuro 2006b ).
The course of the breaking length decrease and the tearing strength increase of the paper sheet is in accordance with the results of Sutjipto et al. (2008 ) at the threefold recycling of the bleached (88% ISO) softwood pulps prepared at the laboratory conditions, beated on PFI mill to 25 SR.

Tear index alteration of the paper sheets drying at the temperature of 80, 100 a 120°C, during eightfold recycling
Song & Law (2010 ) observedkraft pulp oxidation and its influence on recycling characteristics of fibres, the found up the fibre oxidation influences negatively the tear index of paper sheets.Oxidation of virgin fibre prior to recycling minimized the loss of WRV and sheet density.
The beating causes the fibres shortening and fines formation which is washed away in the large extent and it endeds in the paper sludges. This waste can be further processed and effective declined.
Within theEuropean Union several already issued and other foreseendirectives have great influence on the waste managementstrategy of paper producing companies. Due to the large quantities ofwaste generated, the high moisture content of the wasteand the changing composition, some recovery methods,for example, conversion to fuel components, are simplytoo expensive and their environmental impact uncertain.The thermal processes, gasification and pyrolysis, seem tobe interesting emerging options, although it is still necessaryto improve the technologies for sludge application.Other applications, such as the hydrolysis to obtain ethanol,have several advantages (use of wet sludge and applicabletechnology to sludges) but these are not welldeveloped for pulp and paper sludges. Therefore, at thismoment, the minimization of waste generation still hasthe highest priority ( Monte et al. 2009 ).
2.1.2. Drying influence on the recycled fibres
Characteristic differences between recycled fibres and virgin fibres can by expected. Many of these can by attributed to drying. Drying is a process that is accompanied by partially irreversible closure of small pores in the fibre wall, as well as increased resistance to swelling during rewetting. Further differences between virgin and recycled fibres can be attributed to the effects of a wide range of contaminating substances ( Hubbe et al. 2007 ). Drying, which has an anisotropic character, has a big influence on the properties of paper produced from the secondary fibres.During the drying the shear stress are formatted in the interfibrilar bonding area. The stresses formatted in the fibres and between them effect the mechanical properties in the drying paper. The additional effect dues the tensioning of the wet pulp stock on the paper machine.
During the drying and recycling the fibres are destructed. It is important to understand the loss of the bonding strength of the drying chemical fibres. Dang (2007 ) characterized the destruction like a percentage reduction of ability of the water retention value (WRV) in pulp at dewatering.
Hornification = [(WRV 0 -WRV 1 )/WRV 0 ]. 100 [%],
WRV 0 –is value of virgin pup
WRV 1 –the value of recycled pulp after drying and reslushing.
According to the prevailing concept, hornification occurs in the cell wall matrix of chemical fibres. During drying, delaminated parts of the fiber wall, i.e., cellulose microfibrils become attached as Fig. 4 shows ( Ackerman et al. 2000 ).

Changes in fiber wall structure ( Weise &Paulapuro 1996 )

Shrinkage of a fiber cross section ( Ackerman et al. 2000 )
Hydrogen bonds between those lamellae also form. Reorientation and better alignment of microfibrils also occur. All this causes an intensely bonded structure. In a subsequent reslushing in water, the fiber cell wall microstructure remains more resistant to delaminating forces because some hydrogen bonds do not reopen. The entire fiber is stiffer and more brittle ( Howard 1991 ). According to some studies ( Bouchard &Douek 1994 ; Maloney et al. 1998 ), hornification does not increase the crystallinity of cellulose or the degree of order in the hemicelluloses ofthe fiber wall.

The drying model of Scallan ( Laivins&Scallan 1993 ) suggests that hornification prevents the dry structure in A from fully expanding to the wet structure in D. Instead, only partial expansion to B may be possible after initial drying creates hydrogen bonds between the microfibrils( Kato & Cameron 1999 )
Weise & Paulapuro (1996 ) did very revealing work about the events during fiber drying. They studied fiber cross section of kraft fibers in various solids by Confocal Laser Scanning Microscope (CLSM) and simultaneously measured hornification with WRV tests. Irreversible hornification of fibers began on the degree of beating. It does not directly follow shrinkage since the greatest shrinkage of fibers occurs above 80 % solids content. In Figs. 4 and 5 , stage A represented wet kraft fiber before drying. In stage B, the drainage has started tocause morphological changes in the fiber wall matrix at about 30 % solids content. The fiber wall lamellae start to approach each other because of capillary forces. During this stage, the lumen can collapse. With additional drying, spaces between lamellae continue shrinking to phase C where most free voids in the lamellar structure of the cell wall have already closed. Toward the end of drying in stage D, the water removal occurs in the fine structure of the fiber wall. Kraft fiber shrink strongly and uniformly during this final phase of drying, i.e., at solid contents above 75-80 %. The shrinkage of stage D is irreversible.
At a repeated use of the dried fibres in paper making industry, the cell walls receive the water again. Then the opposite processes take place than in the Fig. 4 and 5 . It show Scallan´s model of the drying in Fig. 6 .
The drying dues also macroscopic stress applied on paper and distributed in fibres system according a local structure.
2.1.3. Properties of fibres from recycled paper
The basic properties of origin wet fibres change in the drying process of pulp and they are not fully regenerated in the process of slushing and beating.
The same parameters are suitable for the description of the paper properties of secondary fibres and fibres at ageing as well as for description of primary fibres properties. The experiences obtained at the utilisation of waste paper showed the secondary fibres have very different properties from the origin fibres. Next recycling of fibres causes the formation of extreme nonhomogeneous mixture of various old fibres. At the optimum utilisation of the secondary fibres it need take into account their altered properties at the repeated use. With the increase number of use cycles the fibres change irreversible, perish and alter their properties. Slushing and beating causes water absorption, fibres swelling and a partial regeneration of properties of origin fibres. However the repeated beating and drying at the multiple production cycles dues the gradual decrease of swelling ability, what influences a bonding ability of fibres. With the increase of cycles number the fibres are shortened. These alterations express in paper properties. The decrease of bonding ability and mechanical properties bring the improving of some utility properties. Between them there is higher velocity of dewatering and drying, air permeability and blotting properties improve of light scattering, opacity and paper dimensional stability.
The highest alterations of fibres properties are at the first and following three cycles. The size of strength properties depends on fibres type ( Geffertová et al. 2008 ).
Drying influences fibres length, width, shape factor, kinks which are the important factors to the strength of paper made from recycled fibres. The dimensional characteristics are measured by many methods, known is FQA (Fiber Quality Analyser), which is a prototype IFA (Imaging Fiber Analyser) and also Kajaani FS-200 fibre-length analyser. They measure fibres length, different kinks and their angles. Robertson et al. (1999 ) show correlation between methods FQA and Kajaani FS-200. A relatively new method of fibres width measurement is also SEM (Scanning Electron Microscope) ( Bennis et al. 2010 ). Among devices for analyse of fibres different properties and characteristics, e.g. fibres length and width, fines, various deformations of fibres and percentage composition of pulp mixture is L&W Fiber Tester (Lorentzen & Wettre, Sweden). At every measurement the minimum of 20 000 fibres in a sample is evaluated. On Fig. 7 there is expressed the alteration of fibres average length of softwood pulps during the eightfold recycling at the different drying temperature of pulp fibres.

Influence of recycling number and drying temperature on length of softwood pulps

Influence of recycling number and drying temperature on width of softwood pulps
The biggest alteration were observed after first beating (zero recycling), when the fibres average length decrease at the sheet drying temperature of 80°C about 17%, at the temperature of 100°C about 15.6% and at the temperature of 120°C about 14.6%.
After the first beating the fibres average width was markedly increased at the all temperatures dues to the fibrillation influence. The fibres fibrillation causes the fibre surface increase. Following markedly alteration is observed after fifth recycling, when the fibres average width was decreased. We assume the separation of fibrils and microfibrils from the cell walls dues the separation of the cell walls outside layer, the inside nonfibriled wall S2 was discovered and the fibres average width decreased. After the fifth recycling the strength properties became worse, mainly tear index ( Fig. 3 ).
The softwood fibres are longer than hardwood fibres, they are not so straight. The high value of shape factor means fibres straightness. The biggest alterations of shape factor can be observed mainly at the high drying temperatures. The water molecules occurring on fibres surface quick evaporate at the high temperatures and fibre more shrinks. It can result in the formation of weaker bonds between fibres those surfaces are not enough near. At the beginning of wet paper sheet drying the hydrogen bond creates through water layer on the fibres surface, after the drying through monomolecular layer of water, finally the hydrogen bond results after the water removal and the surfaces approach. It results in destruction of paper and fibre at the drying.
Chemical pulp fines are an important component in papermaking furnish. They can significantly affect the mechanical and optical properties of paper and the drainage properties of pulp ( Retulainen et al. 1993 ). Characterizing the fines will therefore allow a better understanding of the role of fines and better control the papermaking process and the properties of paper. Chemical pulp fines retard dewatering of the pulp suspension due to the high water holding capacity of fines. In the conventional method for characterizing the role of fines in dewatering, a proportion of fines is added to the fiber furnish, and then only the drainage time. Fines suspension is composed of heterogeneous fines particles in water. The suspension exhibits different rheological characteristics depending on the degree of interaction between the fines particles and on their hydration ( Kang & Paulapuro 2006b ).
From Fig. 9 we can see the highest formation of fines were after seventh and eight recycling, when the fibres were markedly weakened by the multiple using at the processes of paper making. They are easier and faster beating (the number of revolution decreased by the higher number of the recycling).

Influence of recycling process and drying temperature on pulp fines changes
The macroscopic level (density, volume, porosity, paper thickness) consists from the physical properties very important for the use of paper and paperboard. They indirectly characterize the three dimensional structure of paper ( Niskanen 1998 ). A paper is a complex structure consisting mainly of a fibre network, filler pigment particles and air. Light is reflected at fibre and pigment surfaces in the surface layer and inside the paper structure. The light also penetrates into the cellulose fibres and pigments, and changes directions. Some light is absorbed, but the remainder passes into the air and is reflected and refracted again by new fibres and pigments. After a number of reflections and refractions, a certain proportion of the light reaches the paper surface again and is then reflected at all possible angles from the surface. We do not perceive all the reflections and refractions (the multiple reflections or refractions) which take place inside the paper structure, but we perceive that the paper has a matt white surface i.e. we perceive a diffuse surface reflection. Some of the incident light exists at the back of the paper as transmitted light, and the remainder has been absorbed by the cellulose and the pigments. Besides reflection, refraction and absorption, there is a fourth effect called diffraction. In other contexts, diffraction is usually the same thing as light scattering, but within the field of paper technology, diffraction is only one aspect of the light scattering phenomenon. Diffraction occurs when the light meets particles or pores which are as large as or smaller then the wavelength of the light, i.e. particles which are smaller than one micrometer (μm). These small elements oscillate with the light oscillation and thus function as sites for new light sources. When the particles or pores are smaller than half of the light wavelength the diffraction decreases. It can be said that the light passes around the particle without being affected ( Pauler 2002 ).
The opacity, brightness, colouring and brilliance are important optical properties of papers and paperboards. For example the high value of opacity is need at the printing papers, but opacity of translucent paper must be lower. The paper producer must understand the physical principles of the paper structure and to determine their characteristics composition. It is possible to characterize nondirect the paper structure. The opacity characterizes the paper ability to hide a text or a figure on the opposite side of the paper sheet. The paper brightness is a paper reflection at a blue light use. The blue light is used because the made fibers have yellowish colour and a human eye senses a blue tone like a white colour.The typical brightness of the printing papers is 70 – 95% and opacity is higher than 90% ( Niskanen 1998 ).
3. Paper ageing
The recycled paper is increasingly used not only for the products of short term consumption (newspaper, sanitary paper, packaging materials e.g.), but also on the production of the higher quality papers, which can serve as a culture heritage medium. The study of the recycled papers alterations in the ageing process is therefore important, but the information in literature are missing.
The recycling is also another form of the paper ageing. It causes the paper alterations, which results in the degradation of their physical and mechanical properties. The recycling causes a chemical, thermal, biological and mechanical destruction, or their combination ( Milichovský 1994 ; Geffertová et al. 2008 ).The effect of the paper ageing is the degradation of cellulose, hemicelluloses and lignin macromolecules, the decrease of low molecular fractions, the degree of polymerisation (DP) decrease, but also the decline of the mechanical and optical properties ( El Ashmawy et al. 1974 ; Valtasaari & Saarela 1975 ; Lauriol et al. 1987a ,b,c; Bansa 2002 ; Havermans 2003 ; Dupont & Mortha 2004 ; Kučerová & Halajová, 2009 ; Čabalová et al. 2011 ).Cellulose as the most abundant natural polymer on the Earth is very important as a renewable organic material. The degradation of cellulosebasedpaper is important especially in archives and museums where ageing in various conditions reduces the mechanical properties and deteriorates optical quality of stored papers, books and other artefacts. The low rate of paper degradation results in the necessity of using accelerating ageing tests. The ageing tests consistin increasing the observed changes of paper properties, usually by using different temperature, humidity, oxygen content and acidity, respectively. Ageing tests are used in studies of degradation rate and mechanism. During the first ageing stages—natural or accelerated—there are no significant variations in mechanical properties: degradation evidence is only provided by measuring chemical processes. Oxidation induced by environmental conditions, in fact, causes carbonyl and carboxyl groups formation, with great impact on paper permanence and durability, even if mechanical characteristics are not affected in the short term ( Piantanida et al. 2005 ). During the degradation two main reactions prevail – hydrolysis of glycosidic bonds and oxidation of glucopyranose rings. As a result of some oxidation processes keto- and aldehyde groups are formed. These groups are highly reactive; they are prone to crosslinking, which is the third chemical process of cellulose decay ( Bansa 2002 , Calvini & Gorassini 2006 ).
At the accelerated paper ageing the decrease of DP is very rapid in the first stages of the ageing, later decelerates. During the longer time of the ageing there was determined the cellulose crosslinking by the method of size exclusion chromatography (SEC) ( Kačík et al. 2009 ). The similar dependences were obtained at the photo-induced cellulose degradation ( Malesic et al. 2005 ).
An attention is pay to the kinetic of the cellulose degradation in several decades, this process was studied by Kuhn in 1930 and the first model of the kinetic of the cellulose chains cleavage was elaborated by Ekenstam in 1936.This model is based on the kinetic equation of first-order and it is used to this day in modifications for the watching of the cellulose degradation in different conditions. Hill et al. (1995 ) deduced a similar model with the

Alterations of DP (degree of polymerisation) of cellulose fibres due to recycling and ageing at the pulp fibres drying temperature of 80°C, 100°C a 120°C.
contribution of the zero order kinetic. Experimental results are often controversial and new kinetic model for explanation of cellulose degradation at various conditions was proposed ( Calvini et al. 2008 ). The first-order kinetic model developed by these authors suggests that the kinetics of cellulose degradation depends upon the mode of ageing. An autoretardant path is followed during either acid hydrolysis in aqueous suspensions or oven ageing, while the production of volatile acid compounds trapped during the degradation in sealed environments primes an autocatalytic mechanism. Both these mechanisms are depleted by the consumption of the glycosidic bonds in the amorphous regions of cellulose until the levelling-off DP (LODP) is reached.
At the accelerated ageing ofnewspaper ( Kačík et al. 2008 ), the cellulose degradation causes the decrease of the average degree of polymerisation(DP). The DP decrease is caused by two factors in accordance with equation
DP = LODP + DP01.e -k1.t + DP02.e -k2.t ,
where LODP is levelling-off degree of polymerisation. There is a first factor higher and quickdecreasing during eight days and a second factor is lower and slow decreasing and dominant aftereight days of the accelerating ageing in the equation. The number of cleavaged bonds can be welldescribed by equation
DP 0 /DP t – 1 = n 0 .(1-e -k.t ),
where n 0 is an initial number of bonds available for degradation. The equation of the regression function is in accordance with Calvini et al. (2007 ) proposal, the calculated value (4.4976) is in a good accordance with the experimentally obtained average values of DP 0 a DP 60 (4.5057). The DP decreased to cca 38% of the initial value and the polydispersity degree to 66% of the initial value. The decrease of the rate constant with the time of ageing was obtained also by next authors ( Emsley et al. 1997 ; Zervos & Moropoulou 2005 ; Ding & Wang 2007 ). Čabalová et al. (2011 ) observed the influence of the accelerated ageing on the recycled pulp fibres, they determined the lowest decrease of DP at the fibres dried at the temperature of 120°C ( Fig. 10 ).
The simultaneous influence of the recycling and ageing has the similar impact at the drying temperatures of 80°C (decrease about 27,5 %) and 100°C (decrease about 27.6%) in regard of virgin pulp, lower alterations were at the temperature of 120°C (decrease about 21.5%). The ageing of the recycled paper causes the decrease of the pulp fiber DP, but the paper remains good properties.
4. Conclusion
The recycling is a necessity of this civilisation. The paper manufacturing is from its beginning affiliated with the recycling, because the paper was primarily manufactured from the 100 % furnish of rag. It is increasingly assented the trend of the recycled fibers use from the European and world criterion. The present European papermaking industry is based on the recycling.
The presence of the secondary fibres from the waste paper, their quality and amount is various in the time intervals, the seasons and the regional conditions. It depends on the manufacturing conditions in the paper making industry of the country.
At present the recycling is understood in larger sense than the material recycling, which has a big importance from view point of the paper recycling. Repeatedly used fibres do not fully regenerate their properties, so they cannot be recycled ad anfinitum. It allows to use the alternative possibilities of the paper utilisation in the building industry, at the soil reclamation, it the agriculture, in the power industry.
The most important aim is, however, the recycled paper utilisation for the paper manufacturing.
Acknowledgments
This work was financed by the Slovak Grant Agency VEGA (project number 1/0490/09).
- 11. CEPI (Confederation of European Paper Industries). 2006 Special Recycling 2005 Statistics- European Paper Industry Hits New Record in Recycling. 27.02.2011, Available from: http://www.erpa.info/images/Special_Recycling_2005_statistics.pdf
- 12. CEPI (Confederation of European Paper Industrie). 2010 Annual Statistic 2009. 27.02.2011, Available from: http://www.erpa.info/download/CEPI_annual_statistics%202009.pdf
- 18. European Declaration on Paper Recycling 2006 2010 , Monitoring Report 2009 (2010), 27.02. 2011, Available from: http://www.erpa.info/images/monitoring_report_2009.pdf
© 2011 The Author(s). Licensee IntechOpen. This chapter is distributed under the terms of the Creative Commons Attribution-NonCommercial-ShareAlike-3.0 License , which permits use, distribution and reproduction for non-commercial purposes, provided the original is properly cited and derivative works building on this content are distributed under the same license.
Continue reading from the same book
Published: 05 July 2011
By Patrícia Carla Giloni-Lima, Vanderlei Aparecido d...
3360 downloads
By Estibaliz Aranzabe, Arrate Marcaide, Marta Hernaiz...
3768 downloads
By André Lermontov, Lidia Yokoyama, Mihail Lermontov...
4686 downloads
Thank you for visiting nature.com. You are using a browser version with limited support for CSS. To obtain the best experience, we recommend you use a more up to date browser (or turn off compatibility mode in Internet Explorer). In the meantime, to ensure continued support, we are displaying the site without styles and JavaScript.
- View all journals
- My Account Login
- Explore content
- About the journal
- Publish with us
- Sign up for alerts
- Open access
- Published: 01 September 2021
Impact of shredding degree on papermaking potential of recycled waste
- Aneta Lipkiewicz 1 ,
- Edyta Małachowska 1 , 2 ,
- Marcin Dubowik 1 &
- Piotr Przybysz 1 , 2
Scientific Reports volume 11 , Article number: 17528 ( 2021 ) Cite this article
3486 Accesses
2 Citations
1 Altmetric
Metrics details
- Engineering
- Environmental sciences
- Materials science
The properties of paper products depend on the structure of the cellulose fibres therein. Although fibre properties in virgin pulps can be modified by a refining process, this is more difficult in pulp from recovered fibre, particularly waste from office shredders that tend to shorten fibres during shredding. The shorter fibres in shredded paper make it difficult to easily reconstitute them into high-quality paper products. Moreover, because of high energy usage during the recycling process and transportation inefficiencies, there is a need to determine how to responsibly shred paper to alleviate this environmental burden. With this in mind, the influence of initial fibre length on the tensile properties of paper was investigated. Changes in initial fibre length significantly influenced many pulp and paper properties. It was found that cutting the paper into pieces with an area less than 25 mm 2 caused significant changes in the important morphological parameters of the fibres and a sharp decrease in the tensile properties of the reconstituted paper.
Similar content being viewed by others
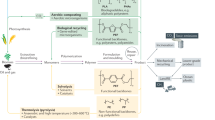
Bioplastics for a circular economy
Jan-Georg Rosenboom, Robert Langer & Giovanni Traverso
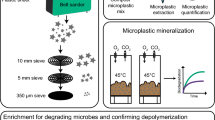
Rapid biodegradation of microplastics generated from bio-based thermoplastic polyurethane
Marco N. Allemann, Marissa Tessman, … Ryan Simkovsky
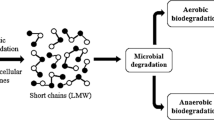
Recent advances in biodegradable polymers for sustainable applications
Aya Samir, Fatma H. Ashour, … Mohamed Bassyouni
Introduction
Wastepaper, for both ecological and economic reasons, is a good raw material for the production of paper or cardboard. Paper recycling reduces the use of wood, and thus, helps preserve forest resources, saves energy, reduces littering, the amount of waste going to landfills, air pollution, and wastewater generation, and instils ecological attitudes in society.
However, the properties of fibres in wastepaper can deteriorate not only during processing, but also at the collection stage due to shredding, which can cause excessive shortening of the fibres. In addition to fibre bonding 1 , fibre length and strength are basic factors influencing the tensile and structural properties of paper products 2 , 3 , 4 . Fibre and pulp properties also affect the cost of producing paper products. Hence, the ability to control fibre properties during the recycling stage is a determining factor in effective quality control and the cost of paper production from waste paper.
In industrial practice, the fibres are shortened as a direct result of the fibre refining process or by high-shear processing of the fibrous suspension in the refining zone 5 , 6 . Therefore, the process of pulp refining has a direct influence on fibre properties, and consequently the properties of the final product 7 , 8 , 9 . Through refining, the properties of the refined pulp can be modified to obtain paper with the desired properties. The refining process, aside from affecting paper properties, also has a decisive impact on the unit energy consumption in this process 10 , 11 , 12 , 13 . Owing to the increasing global growth of the market for paper products 14 , 15 , it is extremely important to minimise the unit energy consumption in this process and optimise the development of useful properties of the paper during processing.
Changes taking place in the structure of the refined fibres during the refining process determine how the pulp behaves during web formation and the basic properties of the paper that is produced 16 , 17 . Fibre shortening has a direct negative impact on the dynamic properties of paper, including its tear resistance 18 , 19 . Often, refining is consciously carried out to improve the conditions of web forming and improve its transparency.
When paper is thrown into shredders, the objective is to destroy documents; however, the process also unconsciously shortens the fibres. Paper shredders should facilitate the preparation of pulped materials for further production, rather than render the paper useless. Cut fibres in the shredded paper make it difficult to carry out easy reconstitution into high-quality paper products. Moreover, most recycling centres do not handle small strips or bits of paper. Large-scale recycling facilities use large screens to dry pulped paper on, and finely shredded paper is not well retained and can fall through the screens. Reports claim that the utilisation or recycling of shredded paper is much more problematic than that of mixed unshredded paper. The Environmental Paper Network, a worldwide association of 140 civil society groups and NGOs concerned with the sustainability of pulp and paper practices suggests shredding paper only when necessary 20 , especially since destruction also increases the bulk density of the paper, reducing its transportation efficiency. The office waste problem is particularly significant because of the high amount generated. For example, Japan has a paper collection rate of around 81.6% 21 , which is higher than that of other countries. However, this high collection rate is mainly constituted by a high recycling rate for paper grades such as cardboard and newspapers. The collection rate for office paper and shredded paper remains low (less than 60%) 21 because office paper, on which confidential information is often printed, is generally disposed of. In U.S. offices, 50% of business waste is composed of paper. Offices use approximately 12.1 trillion sheets of paper per year, and paper accounts for 25% of landfill waste and 33% of municipal waste. It was found that each tonne of recycled paper allows for 64% energy savings, 58% water savings, and 60 pounds less air pollution 22 . Security issues aside, one should consider how to efficiently destroy documents while still allowing fibres to be efficiently used in further processing, which will enable the above savings; this paper attempts to address this issue.
Paper destruction categories are assigned based on the standard German Deutsches Institut für Normung (DIN) classification for paper shredding machines. DIN 66,399 classifications, in which ‘P’ refers to ‘Paper-Based’ material, are based on the size and type of particle (Table 1 ).
The aim of this study is to examine the effect of the surface area of shredded particles on paper properties. The study therefore estimates the extent to which waste paper can be shredded while still producing a high-quality product. Pulp samples with different initial particle sizes treated under constant papermaking conditions were used for this purpose.
Materials and methods
Sample preparation.
Industrial air-dried and bleached kraft pine pulp in the form of sheets (Arctic Paper Kostrzyn S. A.) was used in this study. In order to keep all other parameters constant, samples of the pulp were cut manually into squares of different areas (1–400 mm 2 ) to reduce and diversify the fibre length.
Hand-cut samples were compared with strips from shredding machines (destroyed in accordance with DIN 66399). The following shredders were used for the tests: Kobra 240.1 S2 ES (for strips with P-3 specific security levels), HSM Shredstar S5 (for strips with P-4 specific security levels), HSM Securio C18 (for strips with P-5 specific security levels), and HSM Securio B26 (for strips with P-6 and P-7 specific security levels). All cutting processes in the shredders were performed without the addition of oil.
Production of paper sheets and analysis of pulp and paper properties
Sheets of paper from the cut samples were produced under laboratory conditions from rewetted pulp samples (22.5 g dry weight samples were soaked in water for 24 h) that were subjected to disintegration using a laboratory JAC SHPD28D propeller pulp disintegrator (Danex, Katowice, Poland) for 23.000 revolutions, according to ISO 5263-1 (2004). The disintegrated pulps were concentrated to a dry weight content of 10% and refined in a JAC PFID12X PFI mill (Danex, Katowice, Poland) under standard conditions [ISO 5264-2 (2011)]. All the samples were refined for a constant time of 120 s. After the model pulp recycling processes, including refining, the following properties of the pulps were evaluated:
Schopper-Riegler freeness parameter (SR) was measured using a Schopper–Riegler apparatus (Danex, Katowice, Poland) in accordance with PN-EN ISO 5267-1 (2002);
The water retention value (WRV) was determined according to ISO 23714 (2014);
The dimensions of the fibre parameters were measured according to ISO 16065-2 (2016) using a Morfi Compact Black Edition apparatus (Techpap, Grenoble, France).
In the next step, sheets of paper were formed in a Rapid-Koethen apparatus in accordance with PN-EN ISO 5269-2 (2007). Each paper sheet had a basis weight of 80 g/m 2 (according to ISO 536:2012). Only sheets with basis weights between 79 and 81 g/m 2 were used for further investigation. The sheets were conditioned for 24 h at a relative humidity of 50 ± 2% and a temperature of 23 ± 1°C [ISO 187 (1990)] before determining their properties. The properties of the paper sheets were examined as follows. A ZwickRoell Z005 TN ProLine tensile testing machine (Zwick-Roell, Ulm, Germany) was used to measure the mechanical properties of the paper in accordance with PN-EN ISO 1924-2 (2010). The roughness and air permeability were measured using a Bendtsen apparatus (Messmer Buchel, Veenendaal, The Netherlands).
The average degree of polymerisation (DP) of cellulose in each pulp was determined using the viscometric method described in ISO 5351 (2010).
Results and discussion
In industrial conditions, the freeness index of pulp is a commonly used parameter to assess the degree of refining of pulp based on how easily it dewaters. The dewatering of pulp on a paper machine screen is a very useful indicator in industrial practice; therefore, in this study, the effect of the initial fibre length on changes in this indicator was examined. Table 2 shows that the freeness of the refined pulp decreases as the initial fibre length increases, which is attributed to the decreasing amount of fine material in the pulp, in line with the current state of knowledge 23 , 24 , 25 , 26 , 27 , 28 . It is assumed that a freeness index of about 30°SR is optimal for most papermaking properties 29 , 30 . However, obtained results do not indicate that a freeness of ~ 30°SR necessarily achieves a maximum tensile strength (Table 2 ). This confirms that there is no straightforward relationship between freeness and paper properties. Therefore, the freeness of the pulp is not useful to compare the papermaking potential of pulp with different initial parameters.
The impact of initial fibre length on internal fibrillation, one of the basic effects of refining 31 , 32 , 33 , 34 , 35 , was also studied. Progress in achieving internal fibrillation of refined fibres is commonly assessed based on an increase in their swelling 36 , 37 , usually measured by the WRV 38 , 39 , 40 . The analysis in Table 2 indicates that the WRV increases as the initial fibre length decreases, reaching a maximum value of 214.5%. This increase in fibre swelling is accompanied by an increase in the density of the paper, which in turn increases the resistance of the paper to air permeability (Table 2 ), consistent with previous studies 8 , 41 , 42 , 43 .
The initial fibre length did not affect the DP of the produced pulps. The DP was 931 ± 0.89 regardless of the initial dimensions of the samples tested. This confirms previous findings in the literature that mechanical treatment has little effect on the DP of cellulose 44 , 45 .
Table 3 and Fig. 1 show the morphological characteristics of the fibres of the examined pulps. The fibre length for the refined pulps is characterised by lower values compared to the unrefined pulps, which confirms that one of the basic effects of refining is fibre shortening 46 , 47 , 48 . It should be noted that the use of mean weighted or mean geometric fibre length eliminates the influence of the fines fraction on the analysis result 49 , 50 .
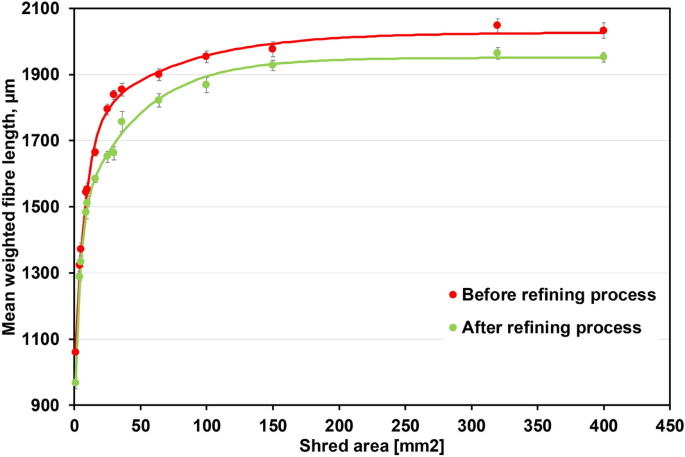
Average fibre length dependency on the cut surface area of samples (before and after model pulp recycling process including refining).
The results presented in the Table 3 show that the examined parameter values of fibres and pulps (mean fibre width, mean fibre coarseness, macro fibrillation index, broken fibre content, and fine content) tend to decrease with decreasing length of the initial fibres, and consequently, the mean weighted fibre length increases. However, an initial sample length greater than 5 mm does not significantly affect the examined fibre properties and fine content. It is therefore likely that a strip width of 5 mm is the limit above which significant changes in the pulp do not occur. The results are similar before and after the refining process (Fig. 1 ).
Microscopic images of the refined pulps, recorded using a Morfi Compact Black Edition camera, are shown in Fig. 2 . The decrease in fibre length after the model pulp recycling process is proportional to the decrease in the dimensions of the pre-cut pulp samples. The most significant fibre shortening is noticed for the 1 × 1 mm sample. There is no significant difference in fibre dimensions for the 10 × 10 mm samples and the reference sample (Fig. 2 ). Therefore, it is possible to shred paper in a shredder to a specific level of fragmentation without fear of excessive shortening of the fibres, which would make the production of high-quality paper more difficult.
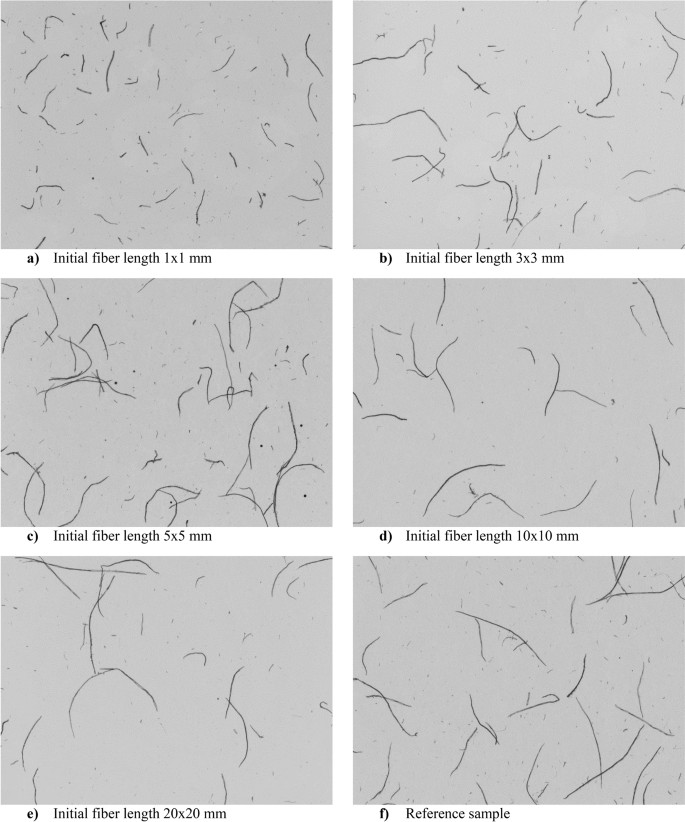
Microscopic images of tested fibrous materials.
According to previous findings, fibre length has a significant impact on the paper stretch index 51 , and excessive fibre shortening and a high fines content cause the paper product to become rigid and reduce its deformability 49 , 52 , 53 . Our results, however, indicate that the stretch of the examined papers is similar, irrespective of the fibre length and fines fraction content (Table 4 ), in contrast to previously reported results. However, the results listed in Table 4 show that fibre length exerts a significant impact on the dynamic tensile properties of paper 54 , 55 , 56 . Importantly, in the case of fibre properties (Table 3 and Fig. 1 ), changes in the area of the shredded samples above 25 mm 2 did not significantly affect the tensile paper properties (Table 4 ). Based on this, it can be concluded that samples can be cut at 5 mm or larger without significant shortening of the fibres and no significant changes in pulp and paper properties. Therefore, the paper shredding provides useful wastepaper when performed in devices up to class P-6.
Research has shown that the fines fraction produced from fibres is responsible for slowing pulp-dewatering in the forming section of a paper machine 57 , 58 . The results obtained are fully consistent with those of earlier studies, in that the pulps with the highest fines content also have the highest SR freeness values (Table 2 ).
The air permeability of paper decreases as the SR freeness level increases 59 , 60 , 61 , 62 , in agreement with previous results. The pulps characterised by lower average fibre length, and therefore, have improved barrier properties to gases even though their tensile properties are reduced (Table 4 ).
The roughness of paper increased with increasing initial fibre length, in agreement with previous results 34 , 61 , 63 , 64 . Therefore, the best smoothness results (230 mL/min) were obtained for paper produced from the pulp with the lowest fibre length. From the data provided, it can be concluded that this paper would likely have the best printability.
Microscopic images of the paper sheets, recorded using a Keyence VHX-6000 microscope equipped with a VH-Z100UR lens, are presented in Fig. 3 . The fibres in the reference pulp (Fig. 3 a) appear undamaged. The paper obtained from samples cut into 5 × 5 mm pieces (Fig. 3 b) shows both undamaged fibres and cut fibres. This observation clearly indicates that initial shortening of fibres damages the fibre structure to some extent, with an effect on average fibre length. However, these are local symptoms of shortening to a certain size. The vast majority of the fibres remain intact, as in the virgin pulp. Therefore, it can be concluded that shortening of fibres can be tolerated to a certain extent if the overall change to the fibre mixture is small.
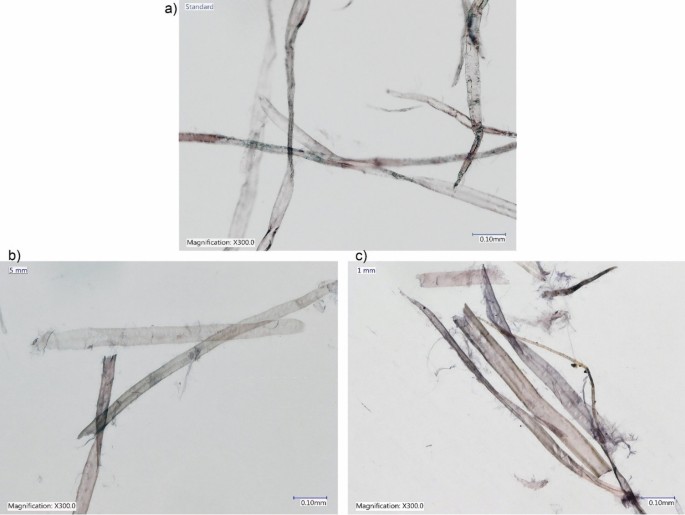
Microscopic images of paper sheets derived from ( a ) reference and ( b , c ) selected refined pulps produced from the tested fibrous materials.
An image from the sample with an initial size of 1 × 1 mm shows many damaged fibres (Fig. 3 c), i.e., disintegration into finer material. Therefore, excessive fragmentation of the fibrous material causes considerable damage to the fibrous fraction, and hence, deteriorates the potential of this fraction, which ultimately results in less desirable paper properties.
Based on the results obtained, the degree to which the shortened pieces of office waste paper can be converted into high-quality paper without any issues that reduce the value of the finished product can be predicted to a certain extent. From an ecological point of view, it is necessary to consider at the very least the issue of pulp freeness, and in turn, the energy needed for dewatering of the pulp. Excessive shortening of the paper samples worsens their dewatering capacity, as confirmed by the obtained results (Table 2 ). Therefore, the practice seeks to maintain a compromise and reduction of the refining range. Achieving efficiency in energy usage is considered the most cost-effective way to reduce CO 2 emissions 65 . Therefore, by producing waste office paper without undue fragmentation in shredder (if data security issues need not be considered), the properties of recycled paper products can be improved and the energy consumption can be reduced concurrently. Thus, the recycling of shredded paper can be carried out in a more ecological, environmentally friendly, and economic manner.
Conclusions
It was found in this study that the initial fibre length affects paper properties, the morphological characteristics of fibres, and the fine content of pulp, which in practice affects the cost of paper production. With other papermaking conditions held constant, paper samples produced from pulps with different initial fibre lengths showed various tensile properties. It is important to note that cutting paper into pieces with an area higher than 25 mm 2 in the shredding process does not significantly influence the properties of pulp or the tensile properties of paper made from the pulp. Cutting samples into pieces smaller than 25 mm 2 , however, causes significant changes in the most important morphological parameters of the fibres and a sharp decrease in the dynamic and static strength properties of the paper with decreasing size of the shredded paper. Such a level of cutting is therefore unprofitable from a technological and an economic point of view because it required difficult pulp-dewatering processes and thus involves increased costs. The obtained results are therefore of great practical value because they demonstrate that the method of shredding paper in the shredder determines the processing potential of this pulp and the papermaking utility of the product. These conclusions can serve as a guide on how to responsibly shred paper, as well as to efficiently recycle fibres to manage biomass consumption.
Data availability
The datasets generated during and/or analysed during the current study are available from the corresponding author on reasonable request.
Campbell, W. B. The Cellulose-Water Relationship in Papermaking (Dept Of Interior, Forest Service Bulletin, 1933).
Google Scholar
Przybysz, K. & Wandelt, P. Pulp quality control system Part 3 Fiber strength. Przeglad Pap. 61 , 283–286 (2005).
Horn, R. A. Morphology of Wood Pulp Fiber from Softwoods and Influence on Paper Strength. Research Paper FPL-242 (U.S. Department of Agriculture, 1974).
Joutsimo, O., Wathén, R. & Tamminen, T. Effects of fiber deformations on pulp sheet properties and fiber strength. Pap. Puu-Pap. Tim. 87 , 392–397 (2005).
CAS Google Scholar
Kerekes, R. & Senger, J. J. Characterizing refining action in low-consistency refiners by forces on fibres. J. Pulp Pap. Sci. 32 , 1–8 (2006).
Karlström, A. & Eriksson, K. Fiber energy efficiency. Part 2: Forces acting on the refiner bars. Nord. Pulp Pap. Res. J. 06 , 332–343 (2014).
Article Google Scholar
Zeng, X., Retulainen, E., Heinemann, S. & Fu, S. Fibre deformations induced by different mechanical treatment and their effect on zero-span strength. Nord. Pulp Paper Res. J. 27 , 335–342 (2012).
Article CAS Google Scholar
Joutsimo, O. & Asikainen, S. Effect of fiber wall pore structure on pulp sheet density of softwood kraft pulp fibers. BioRes. 8 , 2719–2737 (2013).
Tingjie, C. et al. Effect of refining on physical properties and paper strength of pinus massoniana and china fir cellulose fibers. BioRes. 11 , 7839–7848 (2016).
Laine, C., Wang, X. S., Tenkanen, M. & Varhimo, A. Changes in the fiber wall during refining of bleached pine kraft pulp. Holzforschung 58 , 233–240 (2004).
Gharehkhani, S. et al. Basic effects of pulp refining on fiber properties: A review. Carbohydr. Polym. 115 , 785–803 (2015).
Article CAS PubMed Google Scholar
El-Sharkawy, K., Haavisto, S., Koskenhely, K. & Paulapuro, H. Effect of fiber flocculation and filling design on refiner loadability and refining characteristics. BioRes. 3 , 403–424 (2008).
Kerekes, R. Energy and forces in refining. J. Pulp Pap. Sci. 36 , 10–15 (2010).
O’Rourke, D. Nongovernmental organization strategies to influence global production and consumption. J. Ind. Ecol. 9 , 115–128 (2005).
Holik, H. Handbook of Paper and Board 2nd edn. (Willey-VCH, 2013).
Book Google Scholar
Przybysz, K. Fibrillation of cellulose fibers. Przemysl Chem. 82 , 1149–1151 (2003).
Ferritsius, R. et al . Development of fibre properties in full scale HC and LC refining. in 2016 International Mechanical Pulping Conference, Jacksonville , 26–28 (2016).
Kane, M. W. Beating, fiber length distributions and tensile strength-part. Pulp Pap. Canada 60 , 308–359 (1959).
Hartman, R. R. Mechanical Treatment of Pulps for Property Development . PhD Dissertation, Institute of Paper Science and Technology (1984).
Constable, M. The paper shredder: Trails of law. Law Text Culture 23 , 276–293 (2019).
Japanese Paper Recycle, Paper Recycling Promotion Center http://www.prpc.or.jp/document/publications/japan/ .
Paper Recycling Facts, University of Southern Indiana https://www.usi.edu/recycle/paper-recycling-facts/ .
Chauhan, V. S., Kumar, N., Kumar, M. & Thapar, S. K. Weighted average fiber length: An important parameter in papermaking. Taiwan Lin Ye Ke Xue 28 , 51–65 (2013).
Wangaard, F. F. & Woodson, G. E. Fiber length–fiber strength, interrelationship for slash pine and its effect on pulp–sheet properties. Wood Sci. 5 , 235–240 (1973).
Perng, Y. S., Wang, I. C., Cheng, Y. L. & Chen, Y. C. Effects of fiber morphological characteristics and refining on handsheet properties. Taiwan Lin Ye Ke Xue 24 , 127–139 (2009).
Choi, E. Y. & Cho, B. U. Effect of beating and water impregnation on fiber swelling and paper properties. J. Korea TAPPI 45 , 88–95 (2013).
Pruden, B. The effect of fines on paper properties. Pap. Technol. 46 , 19–26 (2005).
Kibblewhite, R. P. Interrelations between pulp refining treatments, fibre and pulp fines quality, and pulp freeness. Pap. Puu-Pap. Tim. 57 , 519–526 (1975).
Olejnik, K. Effect of the free swelling of refined cellulose fibres on the mechanical properties of paper. Fibres Text. East. Eur. 20 , 113–116 (2012).
Sundblad, S. Predictions of Pulp and Paper Properties Based on Fiber Morphology . Master Thesis in Macromolecular Materials, KTH Vetenskap Och Konst, Stockholm, Sweden (2015).
Retulainen, E. The Role of Fibre Bonding in Paper Properties (National Technical Information Service, Espoo, 1997).
Hietanen, S. E. K. Fundamental aspects of the refining process. Pap. Puu-Pap. Tim. 72 , 158–170 (1990).
Wang, X., Maloney, T. & Paulapuro, H. Fibre fibrillation and its impact on sheet properties. Pap. Puu-Pap. Tim. 89 , 148–151 (2007).
Lindqvist, H. et al. The effect of fibre properties, fines content and surfactant addition on dewatering, wet and dry web properties. Nord. Pulp Pap. Res. J. 27 , 104–111 (2012).
Article MathSciNet CAS Google Scholar
Kekäläinen, K., Illikainen, M. & Niinimäki, J. Morphological changes in never-dried kraft fibers under mechanical shearing. Cellulose 19 , 879–889 (2012).
Heymer, J. O., Olson, J. A. & Kerekes, R. The role of multiple loading cycles on pulp in refiners. Nord. Pulp Pap. Res. 26 , 283–287 (2018).
Vishtal, A. & Retulainen, E. Boosting the extensibility potential of fibre networks: A review. BioRes. 9 , 7933–7983 (2014).
Cheng, Q., Wang, J., McNeel, J. & Jacobson, P. Water retention value measurements of cellulosic materials using a centrifuge technique. BioRes. 5 , 1945–1954 (2010).
Scallan, A. M. & Carles, J. The correlation of the water retention value with the fibre saturation point. Sven Papperstidning 75 , 699–703 (1972).
Bäckström, M., Kolar, M. & Htun, M. Characterisation of fines from unbleached kraft pulps and their impact on sheet properties. Holzforschung 62 , 546–552 (2008).
Ferreira, P. J., Matos, S. & Figueiredo, M. M. Size characterization of fibres and fines in hardwood kraft pulps. Part. Part. Syst. Charact. 16 , 20–24 (1999).
Ciesielski, K. & Olejnik, K. Application of neural networks for estimation of paper properties based on refined pulp properties. Fibres Text. East. Eur. 5 , 126–132 (2014).
Paavilainen, L. Importance of particle size: fibre length and fines: for the characterization of softwood kraft pulp. Pap. Puu-Pap. Tim. 72 , 516–526 (1990).
Hai, L. V., Park, H. J. & Seo, Y. B. Effect of PFI mill and Valley beater refining on cellulose degree of polymerization, alpha cellulose contents, and crystallinity of wood and cotton fibers. J. Korea TAPPI 45 , 27–33 (2013).
Wathén, R. Studies on Fiber Strength and its Effect on Paper Properties . Dissertation for the degree of Doctor of Science in Technology, KCL Communications 11, Helsinki University of Technology (2006).
Motamedian, H. R., Halilovic, A. E. & Kulachenko, A. Mechanisms of strength and stiffness improvement of paper after PFI refining with a focus on the effect of fines. Cellulose 26 , 4099–4124 (2019).
Nordström, B. & Hermansson, L. Effect of fiber length on formation and strength efficiency in twin-wire roll forming. Nord. Pulp Pap. Res. 32 , 119–125 (2017).
Biermann, C. J. Refining and Pulp Characterization. Handbook of Pulping and Papermaking 138–139 (Academic Press, 1996).
Jang, H. F. & Seth, R. S. Determining the mean values for fibre physical properties. Nord. Pulp Pap. Res. J. 19 , 372–378 (2004).
Bajpai, P. The Pulp and Paper Industry. Pulp and Paper Industry: Emerging Waste Water Treatment Technologies 23–25 (Elesiver, 2017).
Fišerová, M., Gigac, J. & Balberčák, J. Relationship between fibre characteristics and tensile strength of hardwood and softwood kraft pulps. Cell. Chem. Technol. 44 , 249–253 (2010).
Johansson, A. Correlations Between Fibre Properties and Paper Properties . Master Thesis in Pulp Technology, KTH Vetenskap Och Konst (2011).
Sjöberg, J. & Höglund, H. Refining system for sack paper pulp: Part 1 HC refining under pressurised conditions and subsequent LC refining. Nord. Pulp Pap. Res. 20 , 320–328 (2005).
Larsson, P. T., Lindström, T., Carlsson, L. A. & Fellers, C. Fiber length and bonding effects on tensile strength and toughness of kraft paper. J. Mater. Sci. 53 , 3006–3015 (2018).
Article ADS CAS Google Scholar
Watson, A. J. & Dadswell, H. E. Influence of fibre morphology on paper properties. Part 1: fibre length. Appita J. 14 , 168–178 (1961).
Horn, R. A. Morphology of Pulp Fiber from Hardwoods and Influence on Paper Strength . USDA Forest Service, Research Paper FPL 312, Forest Products Laboratory, 1–10 (1978).
Seth, R. S. The measurement and significance of fines. Pulp Pap. Canada 104 , 41–44 (2003).
Odabas, N., Henniges, U., Potthast, A. & Rosenau, T. Cellulosic fines: properties and effects. Prog. Mater. Sci. 83 , 574–594 (2016).
Sirviö, J. & Nurminen, I. Systematic changes in paper properties caused by fines. Pulp Pap. Canada 105 , 39–42 (2004).
Bossu, J. et al. Fine cellulosic materials produced from chemical pulp: The combined effect of morphology and rate of addition on paper properties. Nanomaterials 9 , 321 (2019).
Article PubMed Central CAS Google Scholar
Niskanen, K. (ed.) Paper Physics, Papermaking Science and Technology, Book 16 (Finnish Paper Engineers Association and TAPPI, 1998).
Maloney, T. C., Todorovic, A. & Paulapuro, H. The effect of fiber swelling on press dewatering. Nord. Pulp Pap. Res. 13 , 285–291 (1998).
Fischer, W. J. et al. Pulp fines-characterization, sheet formation, and comparison to microfibrillated cellulose. Polymers 9 , 366–378 (2017).
Park, J. Y., Melani, L., Lee, H. & Kim, H. J. Effect of pulp fibers on the surface softness component of hygiene paper. Holzforschung 74 , 497–504 (2020).
Jonsson, D. K. et al. Energy at your service: Highlighting energy usage systems in the context of energy efficiency analysis. Energy Effic. 4 , 355–369 (2011).
Download references
Acknowledgements
This work was supported by the National Center of Research and Development in Poland (Project Number POIR.01.01.01-00-0084/17).
Author information
Authors and affiliations.
Natural Fibers Advanced Technologies, 42A Blekitna Str., 93-322, Lodz, Poland
Aneta Lipkiewicz, Edyta Małachowska, Marcin Dubowik & Piotr Przybysz
Institute of Wood Sciences and Furniture, Warsaw University of Life Sciences - SGGW, 159 Nowoursynowska Str., 02-787, Warsaw, Poland
Edyta Małachowska & Piotr Przybysz
You can also search for this author in PubMed Google Scholar
Contributions
A.L. conceived the experiment(s), A.L. and M.D. conducted the experiment(s), P.P., E.M. and A.L. analysed the results, M.D. literature review, E.M. writing—original draft preparation, E.M. writing—review and editing, P.P. funding acquisition. All authors reviewed the manuscript.
Corresponding author
Correspondence to Edyta Małachowska .
Ethics declarations
Competing interests.
The authors declare no competing interests.
Additional information
Publisher's note.
Springer Nature remains neutral with regard to jurisdictional claims in published maps and institutional affiliations.
Rights and permissions
Open Access This article is licensed under a Creative Commons Attribution 4.0 International License, which permits use, sharing, adaptation, distribution and reproduction in any medium or format, as long as you give appropriate credit to the original author(s) and the source, provide a link to the Creative Commons licence, and indicate if changes were made. The images or other third party material in this article are included in the article's Creative Commons licence, unless indicated otherwise in a credit line to the material. If material is not included in the article's Creative Commons licence and your intended use is not permitted by statutory regulation or exceeds the permitted use, you will need to obtain permission directly from the copyright holder. To view a copy of this licence, visit http://creativecommons.org/licenses/by/4.0/ .
Reprints and permissions
About this article
Cite this article.
Lipkiewicz, A., Małachowska, E., Dubowik, M. et al. Impact of shredding degree on papermaking potential of recycled waste. Sci Rep 11 , 17528 (2021). https://doi.org/10.1038/s41598-021-96325-4
Download citation
Received : 22 May 2021
Accepted : 05 August 2021
Published : 01 September 2021
DOI : https://doi.org/10.1038/s41598-021-96325-4
Share this article
Anyone you share the following link with will be able to read this content:
Sorry, a shareable link is not currently available for this article.
Provided by the Springer Nature SharedIt content-sharing initiative
By submitting a comment you agree to abide by our Terms and Community Guidelines . If you find something abusive or that does not comply with our terms or guidelines please flag it as inappropriate.
Quick links
- Explore articles by subject
- Guide to authors
- Editorial policies
Sign up for the Nature Briefing newsletter — what matters in science, free to your inbox daily.


An official website of the United States government
The .gov means it’s official. Federal government websites often end in .gov or .mil. Before sharing sensitive information, make sure you’re on a federal government site.
The site is secure. The https:// ensures that you are connecting to the official website and that any information you provide is encrypted and transmitted securely.
- Publications
- Account settings
Preview improvements coming to the PMC website in October 2024. Learn More or Try it out now .
- Advanced Search
- Journal List
- Polymers (Basel)

Waste Paper as a Valuable Resource: An Overview of Recent Trends in the Polymeric Composites Field
Daniel magalhães de oliveira.
1 Fatigue and Aeronautical Materials Research Group, Department of Materials and Technology, School of Engineering and Sciences, São Paulo State University (UNESP), Guaratinguetá 12516-410, SP, Brazil
Anne Shayene Campos de Bomfim
Kelly cristina coelho de carvalho benini, maria odila hilário cioffi, herman jacobus cornelis voorwald, denis rodrigue.
2 Department of Chemical Engineering and CERMA, Université Laval, Quebec, QC G1V0A6, Canada
This review focuses on polymeric waste-paper composites, including state-of-the-art analysis with quantitative and qualitative discussions. Waste paper is a valuable cellulose-rich material, produced mainly from office paper, newspaper, and paper sludge, which can be recycled and returned to paper production or used in a new life cycle. A systematic literature review found 75 publications on this material over the last 27 years, with half of those published during the last five years. These data represent an increasing trend in the number of publications and citations that have shown an interest in this field. Most of them investigated the physicomechanical properties of composites using different contents of raw waste paper or the treated, modified, and cellulose-extracted types. The results show that polyethylene and polypropylene are the most used matrices, but polylactic acid, a biodegradable/sourced polymer, has the most citations. The scientific relevance of waste-paper composites as a subject includes the increasing trend of the number of publications and citations over the years, as well as the gaps identified by keyword mapping and the qualitative discussion of the papers. Therefore, biopolymers and biobased polymers could be investigated more, as well as novel applications. The environmental impact in terms of stability and degradation should also receive more attention regarding sustainability and life cycle analyses.
1. Introduction
Our world faces sustainable development challenges due to the scarcity of natural resources and the environmental impacts of all human activities. The 2030 Agenda for Sustainable Development consists of a plan guided by 17 sustainable development goals (SDG) to improve people’s lives now and in the future in a global partnership. SDG number 12 (responsible consumption and production) aims to achieve sustainable development through changes in consumption and production patterns through the efficient management of natural resources and changes in waste disposal through prevention, reduction, recycling, and reuse [ 1 ]. In 2020, 59.7% of the total amount of consumed paper was recycled in the world, mainly in Europe (73.3%) and North America (68%) [ 2 ]. Moreover, waste paper is considered the most recycled packaging in Europe (82%), followed by metals (77.4%), glass (75.4%), and plastics (40.6%).
Cellulose, a natural polymer extracted mainly from Pinus or Eucalyptus , is the raw material for paper production [ 3 , 4 ]. Paper is widely used in various products and purposes, such as printing, copying, packaging, and hygiene [ 5 ]. Once used, waste papers, mainly as office paper (printers, photocopiers, or drafts), old newspaper, and sludge paper (a byproduct of paper production), can become fuel sources destined for landfills or recycling. However, an enormous amount of waste paper (WP) is underused or inappropriately discarded. Approximately 40.3% of this paper is consumed, leading to global environmental problems [ 6 ]. Therefore, over the last 100 years, several studies have sought alternatives to increase the reusing or recycling of waste paper. Some examples are the production of valuable compounds, such as bioethanol [ 7 , 8 ] and activated carbon [ 9 , 10 ], as well as a filler in polymeric composites [ 11 , 12 ].
Natural fiber polymeric composites are increasingly used to manufacture more sustainable, resistant, and lighter materials with good specific properties and performance over a wide range of applications [ 13 ]. Because of their low cost, good performance, and ecofriendly attributes, waste paper from vegetal sources emerges as a potential substitute for (or combination with) synthetic fibers [ 14 ]. Several works reported that waste paper could be used as a filler for polymeric composites in the form of paper sheets for laminated composites [ 15 ], paper particles for injection molding [ 16 ], treated paper [ 17 ], modified with coupling agents [ 12 ], and cellulose extracted from the paper [ 18 ]. Their use improves the physicomechanical properties of the polymers and follows the environmental concepts of the 2030 Agenda (SDG).
This review aims to report and discuss what has been performed in terms of waste-paper valorization concerning polymeric composite applications. For this purpose, a systematic review was conducted using the two primary databases: Scopus and Web of Science. The analysis includes the number of publications, years, countries, keywords mappings, and the most cited documents. Furthermore, the leading composite polymers were identified, for which a bibliographic review was discussed under the document’s primary results, novelty, and findings. Finally, the openings for future works are given to guide the research and development of these composites and determine the gaps in the scientific literature about waste-paper polymeric composites.
2. Waste Paper: A Cellulose-Rich Material
The paper production life cycle includes the extraction of the raw material from the natural resource ( pinus and eucalyptus reforestation trees) or the raw material from the recycled waste paper: postconsumer-collected ( Figure 1 ) [ 19 ]. The life cycle is closed and environmentally correct when paper recycling is included in the system. The raw material is transformed into a pulp that passes through a Kraft chemical process to remove lignin, followed by a bleaching process to remove other amorphous components, such as hemicellulose and the remaining lignin. Then, the paper production can be diverse, including office paper, newspaper, packaging, toilet paper, and cardboard. After the end-of-life of paper products, the waste is collected for landfill and incineration (initially) or recycling (more recently). Then, the recycled paper is sorted and returned into the “paper cycle” to produce a recycled pulp for paper production. Figure 1 shows the paper production cycle considering the paper recycling coming back for paper production, which should be achieved three-four times [ 20 ]. However, recycled paper can also be used in a new product life cycle, such as in composite materials or in producing valuable compounds (upcycling).

Paper production life cycle.
Table 1 presents the typical chemical composition of different types of waste paper, such as office paper, newspaper, and sludge paper. Among these, office paper is the most cellulose-rich waste-paper product due to its pulping (chemical processing), which removes most of the amorphous compounds. In contrast, newspaper generally goes through a different pulping process (mechanical or chemical/mechanical) in which a lower-strength paper is produced [ 19 ]. Paper sludge is a byproduct, including solid waste from pulp and paper production [ 21 ], generating waste paper with diverse chemical compositions.
Chemical composition of different kinds of waste paper. 1
1 Due to the inaccuracy of the chemical composition methods, the total of components for each sample does not always add up to 100%.
Waste paper represents an old subject but still provides possible new developments. Recent articles reported waste paper uses for aerogels production finding different possibilities, such as spongy aerogels with oil absorption properties [ 27 ], superhydrophobic aerogel as a thermal insulating cooler for building fields [ 28 ], and an adsorbent aerogel to remove organic pollutants from wastewater (phenol and 2-chlorophenol) [ 29 ]. Additionally, the waste paper was converted to bioethanol [ 30 ], biodiesel [ 31 ], and biogas [ 32 ] through the action of micro-organisms. Other works synthesized the valuable compounds from waste paper, such as the biopolymer polyhydroxyalkanoate (PHA) by anaerobic digestion [ 33 ] and graphene from a carbonization process [ 34 , 35 ]. Furthermore, carboxymethyl cellulose (CMC) [ 36 ] and hydroxypropyl cellulose (HPC) [ 37 ] were synthesized via alkaline and ether reactions, while cyanoethyl cellulose (CEC) was synthesized via an alkaline reaction with acrylonitrile [ 38 ]. Packaging materials were also developed from waste paper alone with antimicrobial properties [ 39 ] or were mixed with other raw materials, such as silver nanoparticles [ 40 ] and sugar cane stalk + adhesives [ 41 ].
In addition to the applications mentioned above, the polymeric composites field has grown due to environmental issues and greater possibilities of using raw waste paper, treated waste paper, or cellulose-extracted waste paper, by varying the concentration and mixing methodology with different polymers (composites), as well as other fillers (hybrid systems). The following section will focus on polymer composites concerning the matrices used and the characterizations performed.
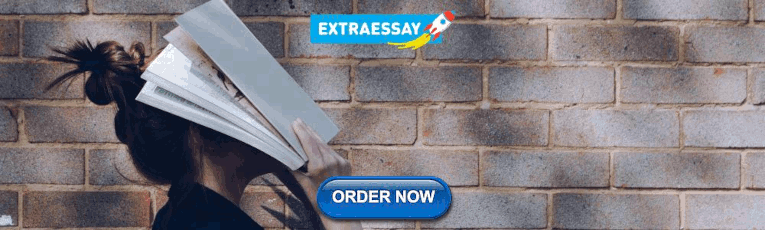
3. Waste Paper-Polymeric Composites
3.1. systematic review.
Systematic research was performed using the Scopus and Web of Science databases, considering only documents (journal articles) in English. The repeated documents were excluded. First, the research included the words “ waste paper ”, showing a total of 4231 documents over the last 100 years ( Table 2 ), discussing various applications, types of recycling, and the characterization of this residue. However, when the research was refined by combining the words “ waste paper ” and “ composite ”, the number decreased to 255 documents. The word “ polymer ” was not considered due to the different polymer names used in the abstract and title, such as polyethylene or polypropylene. Therefore, all the abstracts were reviewed, considering the ones related to the subject focusing on polymeric composites, leading to 75 documents.
Results of the systematic search in the Scopus and Web of Science databases.
The 75 publications span the last 27 years ( Figure 2 ). The data showed gaps along the timeline, but the subject has remained. Besides, an oscillation in publication numbers (increase and decrease) was observed over the years, but a general increasing trend was observed. The peak of publications was found in 2022 (incomplete year), followed by 2019, showing that this subject earned more attention in the recent scientific literature. Also, the number of publications was affected by the COVID-19 global pandemic in 2020 and 2021. Indeed, 50% of the volume of the documents was published over the last five years. Furthermore, the number of citations continuously increased over the years, becoming more relevant in 2006 as most were reported from Scopus, highlighting the scientific relevance of the subject.

Number of publications and citations per year for the 75 documents, according to Scopus and Web of Science (1995–2022).
Concerning geographic representation, 30 countries have published on the subject, with at least one from each of the five continents ( Figure 3 ). The most represented country is China (22), followed by India (10), the USA (5), Turkey (5), and Iran (4), while the other countries have three or fewer documents. All these countries have less than 100 citations in their published documents, but the USA has the most cited paper in the scientific literature ( Table 3 ). Also, collaborative research was identified among the countries sharing the same publication. For example, India with Ethiopia and Ireland [ 42 ], China with Switzerland [ 15 ], and Italy with Russia [ 43 ]. China has published on this subject over the last 20 years, while most countries have just started investigating the topic since half of the documents were published after 2017. Furthermore, over 50% of the world has not published on this subject yet since the publication list only includes 15% of the world’s countries. This indicates that the topic has started to be more widespread only recently.

Number of publications per country in the 75 documents, according to Scopus and Web of Science (1995–2022).
The five most cited documents in the 75 documents, according to Scopus (2012–2022).
1 Until 30 September 2022.
Keyword networking was performed using the software VOSviewer concerning the frequency and chronological time ( Figure 4 ). The most incident cluster is mechanical properties , followed by composite(s) , waste paper , and recycling . Regarding chronological time, the yellow clusters are the most recent ones, including recycling , wood , nanocrystalline cellulose , and flexural properties . This result indicates the relevance of recycling and mechanical properties topics (including flexural properties). Other properties needed to be identified, suggesting a gap in the literature that could be explored more in further research.

Keywords network in the overlay visualization mode, including frequency and chronological time from Scopus.
The five most cited documents ( Table 3 ) include articles published over ten years ago (1999, 2003, and 2006) from the USA, China, Iran, and India. The most important one (Huda et al. 2006) has two times more citations than the other four documents. Although it is not a recent article, it has been cited over the years until the present, confirming its influence and relevance in the literature (pioneering work).
Finally, it was possible to highlight the leading composites found in the 75 documents ( Table 4 ). Conventional thermoplastics, thermosetting polymers, elastomers, and foams were identified. The highest number of documents was found for commodities polymers: polyethylene (PE) and polypropylene (PP) (also found in the keyword network). However, the biodegradable/sourced polylactic acid (PLA) provided a higher number of citations from all the published documents (438), including the most cited article from 2006 ( Table 3 ) and more than six recent articles from the last five years ( Table 4 ). Concerning the other biopolymers, one publication was found on PLA and PBAT (poly(butylene adipate-co-terephthalate)), but none were reported for other biopolymers. Therefore, these data support the scientific relevance of biopolymers and waste-paper-composite topics, indicating a scientific gap for new publications in the field of biopolymers as composite matrices.
The main composites found in the 75 documents, according to Scopus and Web of Science.
Therefore, the subject has a low number of published documents (only 75) since it is a specific topic inside the outstanding waste-paper (WP) topic. So, there are apparent scientific gaps to be filled, highlighting several possibilities for new research on waste-paper-polymeric composites. The following section focuses on the different polymers used as matrices.
3.2. Main Polymers Used in WP Composites and Their Properties
Based on the systematic literature analysis presented above, it was possible to identify the main composite formulations discussed in the 75 documents. The following sections emphasize the main effects of adding WP to different polymers. A detailed discussion is included to support the systematic data found and better understand the gaps and prospects.
3.2.1. Polyethylene (PE) Composites
The pioneering work reporting the influence of maleic anhydride coupling agent (5 wt.%) on the mechanical properties of low-density PE (LDPE) blended with high-impact polystyrene (HIPS) filled with WP (30 wt.%) presented a higher tensile (42%) and impact strength (38%), as well as a better dispersion of the composite’s filler with the coupling agent [ 48 ]. Other works also reported the mechanical behavior of PE/WP composites besides their thermal and morphological-structural properties. LDPE grafted with a maleic anhydride coupling agent filled with WP (10–50 parts per hundred—phr) has shown increased tensile strength (88%) and stiffness (409%) for a composite with 30 phr WP compared to a grafted polymer. This is supported by morphological analyses showing good interfacial adhesion between the polymer/filler, with fewer voids and pull-out [ 49 ]. Moreover, an interesting recent work used PE with WP (from beverage packaging) to produce a compressed laminated composite panel to replace typical wooden panels such as OSB (oriented strand board) [ 50 ]. The mechanical results presented an improvement in tensile strength (400%), tensile modulus (15%), three-point bending strength (54%), and three-point bending modulus (22%) for the composite with 50 wt.% PE compared to the OBS panel. The authors concluded that this material could replace wooden panels following environmental concerns.
In addition, PE was filled with extruded WP and tested for photochemical behavior after exposure to UV irradiation for 100 h [ 51 ]. The results showed a photo-oxidative degradation on the materials, justified by the formation of carbonyl groups (C=O), mainly for the composites with a higher WP concentration (20–30 wt.%) and, consequently, a reduction in crystallinity degree, compared to the composites with a lower WP concentration (5–15 wt.%). Additionally, all the composites presented lower thermal stability after UV exposure (around 20% for the 30 wt.% composites). Even with this result, the authors concluded that these composites could be applied to a wide range of applications where transparency is not required. Moreover, recycled LDPE from packaging films was mixed with WP in an extruder, compression molded and characterized via thermal and rheological analyses [ 52 ]. The addition of 40 wt.% WP slightly improved the thermal degradation temperature compared to the matrix (3 °C), while the other composites (50 and 60 wt.%) presented a decrease (4.5 °C) compared to the neat matrix. On the other hand, the complex viscosity increased as the amount of filler increased, presenting a more viscous material and, consequently, higher shear-thinning behavior.
Two kinds of WP (water-treated sludge and ink-eliminated sludge) at different concentrations (20–60 wt.%) were mixed with high-density PE (HDPE) with and without wood flour (WF) (20–60 wt.%) and were then extruded and injected [ 46 ]. In this hybrid system, both cellulose-based fillers act as reinforcements to improve the flexural properties of the composite. A Higher WF concentration increased the composite’s water absorption and thickness swelling. However, HDPE with 60 wt.% ink-eliminated sludge (WP) and a maleic anhydride coupling agent (3 wt.%) and without WF provided better physicomechanical properties compared to the other composites. In another work, HDPE, WP, WF, maleic anhydride coupling agent (MAPE), and starch-derived polymer using different compositions were mixed in a turbo mixer and compression molded [ 53 ]. The authors concluded that the composites with 10 wt.% WP, 30 wt.% WF and 3 wt.% coupling agents provided the best mechanical results regarding tensile strength and hardness.
WP was also mixed with pure cellulose and HDPE, followed by injection molding. However, the fillers were initially modified with fatty and amide acid esters (plasticizer), an aminosilane coupling agent, and a maleic anhydride coupling agent. The better interfacial adhesion between the components led to improved mechanical properties and moisture resistance, such as tensile strength for a composite modified with a maleic anhydride coupling agent (20%) [ 54 ]. Recycled HDPE was mixed and injected with WP deinking sludge. The results showed that adding the filler improved the crystallinity degree of the composites compared to the polymer since the filler acted as a nucleating agent [ 55 ]. In addition, a composite with 12.5 wt.% WP presented a higher tensile strength and stiffness than 5 and 20 wt.%, indicating that an optimum occurred, representing a balance between reinforcement and defects (dispersion, interface) with increasing filler content.
Novel research tested WP (5 wt.%) and chopped basalt (5 wt.%) in HDPE as a replacement for HDPE double-wall greenhouse glazing [ 43 ]. The injected composites showed a slight increase in melting temperature (4 °C) and tensile properties (8.2% and 11.4% in tensile strength and modulus, respectively) compared to the neat HDPE. They provided typical HDPE plastic behavior in the tensile test. This was considered an advantage since the material could be exposed to more extreme weather conditions, such as wind, snow, and rain, where plastic deformation, instead of fragile behavior, is required. Furthermore, a composite with HDPE, a 3 wt.% maleic anhydride coupling agent, and 40 wt.% WP (copy paper and poster paper) coated with CaCO 3 was compressed and tested for water absorption with different CaCO 3 concentrations (2.3, 4.6, 6.6, and 9.2%) [ 56 ]. After 14 days of water immersion, the composite with 9.2% CaCO 3 provided the best behavior by decreasing its water absorption (from 5.3% to 2.5%) and thickness swelling (from 2.7% to 0.5%), indicating that calcium carbonate might be a good option (available and low cost) to improve the water-resistance of the HDPE/WP composites.
A recent study used HDPE and PP as matrices filled with WP from postage envelope waste (5–15 wt.%). The materials were extruded and injection molded into bars and discs. They found that the composites had increased dielectric losses: 40% for HDPE and 30% for the PP composites as the filler content increased since cellulosic fillers have polar OH groups compared to nonpolar polymers [ 57 ]. Another study used Xuan-WP from China as a filler for recycled PE/red mud composites. The composites were molded in a plate vulcanizing machine, and the results showed an improvement in the flexural strength (43%) but lower tensile strength (16%), especially with a higher (60 wt.%) WP content, while increasing the crystallinity degree of the composites [ 58 ]. This comes from the Xuan-WP containing minerals (27 wt.%) and organic particles (63 wt.%), mainly calcite, whewellite, and cellulose.
A novel piece of work developed a foam-compressed composite made of HDPE/WP using azodicarbonamide as a chemical blowing agent. The melt viscosity decreased, while the cell number increased (smaller cell sizes) as the blowing agent content (1–8 phr) increased. In contrast, a higher WP content led to higher melt viscosity, reducing the cell number and increasing the cell size [ 62 ]. Furthermore, HDPE/WP-injected composites were tested with different coupling agents: vinyltriethoxysilane (A151), vinyltrimethoxysilane (A171), and γ-methacryloxy propyl trimethoxy silane (KH570) [ 63 ]. A composite with 35 wt.% WP provided the best mechanical performance in terms of the improved tensile strength (19%), for which the modifier addition (3 wt.%), mainly A171 and KH570, generated a slight improvement not only in the mechanical properties but also in water absorption and thermal properties.
Finally, newspaper waste was tested as a WP filler (sheets) for HDPE (films)-laminated composites made from a hot-pressing process and characterized in a three-article series. The first one evaluated the relationship between flexural strength and composite density, as well as water absorption and porosity concerning WP content [ 15 ]. The flexural strength and density showed a linear correlation with maximum values of 99.4 MPa and 1.4 g/cm 3 , respectively, highlighting the influence of density on the mechanical properties of the composites. Water absorption was also correlated to porosity because the pores/voids in WP-filled HDPE are known to facilitate water penetration. The second work studied the influence of stair-like and vertical splicing on the properties of the HDPE/WP-laminated composites, in which the stair-like splicing provided the optimum physicomechanical behavior as the tensile strength increased (62% for 0° stacking direction to 11.1% for 90°) [ 59 ]. In contrast, the flexural properties decreased because of the poor interaction at the splicing position. The last paper focused on modifying the WP filler with stearic acid to improve the water resistance of the final composites [ 60 ]. The treatment was found to be effective in improving the composite’s water resistance, related to the esterification bonds between the WP hydroxyl groups and stearic acid carboxyl groups. All these interactions improved the tensile strength of the wet samples as the stearic acid concentration increased.
Table 5 presents an overview of the works published on WP-based PE composites for a quick reference and comparison of their properties.
Main mechanical properties found in the PE composites.
1 maleic anhydride graft polyethylene. 2 silane coupling agent.
3.2.2. Polypropylene (PP) Composites
The effect of coupling agents on the properties of PP/WP was investigated in several works. Maleic anhydride grafted onto PP (MAPP) was compared with ethylene diamine dilaurate (EDD) as coupling agents in PP/WP composites that were extruded, and compression molded [ 12 ]. The results showed that EDD (2 wt.%) performed better by producing higher ductility (68%), flexural strength (19%), and impact strength (37%) but decreased the tensile modulus (10%) and water resistance (12%), with a similar tensile strength when compared to the same amount of MAPP. Another work investigated MAPP, stearic acid, and titanate as coupling agents in PP/WP composites that were extruded and injected [ 66 ]. It was found that MAPP generated the optimum interfacial interaction leading to a higher tensile strength (10%) and crystallization rate compared to the other compatibilizers. Moreover, MAPP (5 wt.%), as a coupling agent, was reported to increase the tensile strength (13%), flexural strength (70%), and impact strength (90%) compared to a composite without a coupling agent [ 45 , 68 ].
In addition, PP filled with WP, WF, and cellulose was hot-pressed and evaluated regarding water absorption. As expected, increasing the filler content (15–35 wt.%) increased the water absorption for all composites [ 44 ], but PP/WP presented the highest value, while PP/cellulose presented a higher water resistance. Furthermore, PP/WP (ink-eliminated sludge) was compared to PP filled with CaCO 3 , with both extruded and injection molded, showing that both fillers acted as nucleating agents in PP crystallization [ 67 ]. However, WP influenced the composite more since the melting and crystallization temperatures were higher for PP/WP than PP/CaCO 3 . The mechanical strength was better (about 20%) for PP with 30 wt.% WP compared to PP/CaCO 3 with the same content.
A recycled PP mixed with WP as old newspaper (ON) and old magazines (OMs) was compression molded and showed the most significant properties and interfacial adhesion with 30 wt.% filler. However, WP-ON presented the highest mechanical properties for flexural strength (25%) [ 71 ]. Recycled PP filled with WP as newspaper (WP-N) was compared with better quality and more expensive filler: cellulose with a special bleaching pretreatment [ 69 ]. The results showed an improvement in tensile strength (26% and 56%) and stiffness (47% and 16%) for WP-N and cellulose, respectively, compared to recycled PP. At the same time, the thermal properties behaved similarly, with an increase in crystallinity degree for both the fillers. The authors concluded that cellulose performed better, but WP-N was more economically viable. In another work, recycled PP was mixed and hot-pressed with printed and unprinted WP to determine the effect of the ink on the material properties [ 70 ]. The presence of ink generated better interfacial interaction between the polymer and the filler due to its iron oxide content, thus improving the composite’s mechanical strength (tensile 37.9% and flexural 17.8%), tensile modulus (38.5%), and water resistance (25.5%).
An exciting work produced virgin and recycled PP filled with WP (from newspaper), nanoclay, and a coupling agent, for which the materials were put in a mixer rotating followed by injection molding [ 72 ]. The thermal and mechanical properties were slightly higher for the composites than the virgin PP composites. Nevertheless, the addition of nanoclay (2.5 wt.%) increased the thermal degradation temperature of the composites (32%), tensile strength (11%), and elastic modulus (23%) for PP/WP. The authors concluded that despite the slight decrease in properties for recycled PP, the values were sufficient for environmentally friendly applications, such as food utensils and automotive interior parts. In addition, PP was used with WP (newspaper) and glass fiber (GF) for outdoor applications in which the panels were hot-pressed. Water absorption and thickness swelling increased with filler content because the poor interaction between the materials generated a high number of voids/porosity facilitating water absorption [ 73 ]. However, higher water resistance with GF addition can open the door for wet locations, such as bathrooms and outside decks.
Another work evaluated the effect of four fillers (waste wood, kenaf core, waste jute, and WP newspaper) as reinforcement for injected PP composites to replace wood-plastic composites (WPC) [ 75 ]. The results indicated that any fillers could replace wood in the composites concerning mechanical properties. However, WP provided the best balance of properties. For example, WP improved flexural and tensile strength by over 25%. However, a more recent recycled PP and WP were produced to compare with cardboard or WF for 3D printing applications [ 64 ]. The composites were first extruded, and the specimens were 3D-printed to evaluate the physicomechanical properties. The recycled PP composites were compared to virgin PP composites, in which PP/WP (5–20 wt.%) did not improve the thermal and mechanical properties. But the addition of 10 wt.% WP in recycled PP generated a slight increase in the thermal stability (1.4 °C), glass transition temperature (36%), and tensile elastic modulus (25%), as well as a decrease in crystallinity degree (15%), and tensile strength (80%). Unfortunately, there was no conclusion regarding the feasibility of the material specified for 3D printing applications.
Conventional melt processing was replaced by solid-state shear pulverization (SSSP) via twin-screw extrusion to produce a PP/WP composite (15 wt.%) [ 65 ]. The composites were produced with different specific energy inputs (E p ) to investigate their influence on filler size and dispersion. The results showed that medium to high E p (14–35 kJ/g) provided a better filler dispersion, leading to an improved tensile elastic modulus (70 %), crystallization temperature (6%), and crystallinity degree (4%) at E p = 14 kJ/g, compared to neat PP. Moreover, the cost of the composite was estimated to be lower than the neat PP, with both produced by SSSP. Another work investigated the thermomechanical performance of PP/WP composites made by injection, indicating that WP addition increased the stiffness and energy absorption capacity while decreasing the tensile strength and ductility [ 76 ]. However, 30 wt.% composites presented similar values to the neat PP, and 10 wt.% composites were suitable for nonstructural applications and for being more environmentally friendly by reducing the amount of synthetic material. Finally, a vintage article investigated the influence of WP particle size on the mechanical properties of PP composites with and without a MAPP wax coupling agent mixed by a K-mixer [ 77 ]. It was concluded that particle size did not influence mechanical strength, but MAPP provided an improvement of 26%.
Table 6 presents an overview of the works published on WP-based PP composites for a quick reference and comparison of their properties.
Main mechanical properties found in the PP composites.
1 ethylene diamine dilaurate. 2 maleic anhydride graft polypropylenes.
3.2.3. Poly(Lactic acid) (PLA) Composites
PLA/WP composites (5–15 wt.%), with and without a silane coupling agent, were investigated as filaments for 3D printing [ 80 ]. The thermal results indicated a decrease in the thermal stability of the composites. However, the stability was still enough for 3D printing (190–210 °C), with a significant increase in crystallinity degree (134%). The tensile strength and ductility of the composites were improved with the addition of a silane coupling agent. Moreover, WP addition enhanced the melt flow properties of the composites, presenting higher shear-thinning behavior and fluidity than other well-known fillers, such as wood and cellulose nanocrystals.
Three sequential works from the same authors evaluated the influence of WP addition on PLA composites, as well as the influence of filler modifiers. The PLA/WP composites were compared with PLA/wheat straw and PLA/bamboo composites and showed optimum thermomechanical performance [ 11 ]. Furthermore, PLA with 20 wt.% WP and compatibilized with γ-(2,3-propylene oxide) propyltrimethylsilane (KH560) presented higher tensile strength (14%) and water resistance than the other composites. In subsequent work, nanocrystalline cellulose (NCC) was prepared from WP and mixed with PLA resulting in a composite with higher mechanical properties than neat PLA, such as tensile (8.2%), flexural (13.1%) and impact strength (35.9%) at 3 wt.% NCC [ 78 ]. Then, WP was mixed with a PLA/NCC composite and showed improved mechanical properties and water absorption compared to neat PLA, but this was still lower than PLA/NCC. According to the authors, the interfacial adhesion must be improved to produce higher mechanical properties in the composites, which were tested in more recent work. The influence of different coupling agents, such as γ-methacryloxypropyltrimethoxy silane (KH570), isopropyl tri(dioctylpyrophosphate) titanate, sodium hydroxide, poly-ethylene glycol 6000 (PEG6000), and a composite silane (KH570/PEG6000) was evaluated for PLA/NCC/WP composites [ 79 ]. From the microscopy images, it was possible to conclude that all the coupling agents provided interfacial interaction between the polymer and the fillers, enhancing the material’s properties by different degrees depending on the modifier. For example, the composites modified by KH570 presented higher thermal stability, while KH570/PEG6000 provided a higher tensile strength. Therefore, the best coupling agent depends on the properties required for the composite application.
The most cited article in the systematic analyses investigated PLA + WP (newspaper) and PLA + chopped glass fiber composites concerning their physicomechanical properties [ 16 ]. The main results showed an improvement in PLA/WP stiffness compared to neat PLA, identified by the increase in the tensile modulus, flexural modulus, and storage modulus. However, when considering PLA/glass fiber, the composites presented a slight reduction in almost all properties, except for glass transition temperature and crystallinity degree, which showed higher values in the PLA/WP composite. This little difference led the author to conclude that PLA/WP composites can replace PLA/GF composites in some applications, depending on the required properties.
A novel study evaluated the use of poly(butylene adipate-co-terephthalate) (PBAT) to improve the thermomechanical performance of PLA/WP composites [ 81 ]. PBAT addition (10–40 wt.%) promoted the impact strength (290%), thermal stability (4.1%), and crystallinity degree (10%) of the composites, compared to neat PLA. Furthermore, a coupling agent was added to improve the mechanical properties, leading to an optimum for PLA/WP with 20 wt.% PBAT and MAPLA/KH560 as compatibilizers. This result highlights the improvement of PLA performance by WP and PBAT for its use in nonconventional PLA applications that are different from packaging and 3D filaments. Another work evaluated the effect of treatment time (the filler went through a beating machine) and filler content on the properties of PLA/WP (corrugated paper) composites. As expected, WP addition (5–30 wt.%) increased the mechanical properties of the composite compared to neat PLA, such as their tensile (5–22%) and flexural (5–50%) strengths, while decreasing thermal stability (3–24%). The composite with 25 wt.% and 30 min of beating time provided the optimum mechanical performance, for which the authors concluded that this material could solve the environmental issues related to paper recycling [ 82 ].
Table 7 presents an overview of the works published on WP-based PLA composites for a quick reference and comparison of their properties.
Main mechanical properties found in the PLA composites.
1 silane coupling agent. 2 poly-ethylene glycol 6000.
3.2.4. Rubber Composites
Rubber/WP (newspaper) composites were reported with enhanced mechanical properties compared to rubber/silica composites [ 17 ]. The composites were tested with natural rubber (NR) and butadiene acrylate copolymer rubber (NBR), with 20, 40, and 60% of the filler untreated and treated with sodium silicate and magnesium chloride. The results showed that rubber/WP composites with 40% WP provided the optimum mechanical properties, such as enhanced tensile strength (47.4%) and ductility (5.1%) compared to the silica composites. Moreover, the rubber/treated WP provided the best mechanical performance, especially for NR. Corn husk was used as a second filler for the rubber/WP composites to produce low-cost and low-weight composites with improved properties [ 84 ]. The results reported an improvement in composite wear resistance and water resistance as the corn husk content increased (2, 4, 6, 8, and 10 wt.%), which is associated with the hydrophobic nature of the corn husk. However, lower contents (4–8 wt.%) generated higher flexural properties. Rattan fibers (untreated and treated with KOH) were also investigated as a filler for NR/WP (pulp) composites and cassava starch/WP (pulp) composites. The results showed that cassava starch/WP/rattan composites provided higher flexural properties (~18%), while NR/WP/rattan presented a higher water resistance (~10%) [ 86 ]. The treatment improved the flexural properties while reducing the water resistance of all composites. Overall, the composites made with NR and WP provided the most outstanding water resistance without any treatments or other fillers (lower cost and easier to produce).
The fatigue life of two natural rubbers having 0 and 50 mole% epoxidations (SMR L and ENR 50) filled with WP (sludge) showed that increasing the WP content (10–40%) decreased the fatigue life of the composites. However, ENR 50 provided longer fatigue life [ 87 ]. Additionally, a maleated natural rubber coupling agent was used to increase the fatigue life of the composites by up to 14% at 30% WP and 22% at 10% WP.
Natural rubber was filled with WP (newspaper) that was modified with magnetite to generate radiation shielding, resulting in higher conductivity and mechanical properties than the neat matrix [ 88 ]. The NR/WP composites also included paraffin wax and boron carbide (B 4 C), which improved radiation shielding. The optimum was obtained at 42% modified WP, 18% paraffin wax, and 20% B 4 C. In recent work, NR + barium sulfate + WP composites were developed as a radiation attenuation material and were applied in X-ray shielding [ 85 ]. Prototypes with a 0.25 mm thickness were produced, showing good dispersion of the barium sulfate in the rubber matrix, and influencing the absorption of incident X-rays. Moreover, the maximum voltage of the X-ray beam for protection was 80 kV.
Table 8 presents an overview of the works published on WP-based rubber composites for a quick reference and comparison of their properties.
Main mechanical properties found in the rubber composites.
1 maleic anhydride natural rubber. 2 kilocycles.
3.2.5. Epoxy Composites
The first published work reported epoxy resin, phenolic resin, and WP (newspaper) composite laminates produced via prepreg, for which the mechanical performance was evaluated and compared to PP/WP [ 92 ]. The mechanical strength and modulus produced a decreasing trend as the filler content increased (0.3–0.7 wt.%), but the ductility was enhanced by 155% for the PP/WP 0.6 w.t% composite. The mechanical properties of the PP/WP composites were similar, such as tensile strength (56 MPa) for epoxy/phenolic/WP compared to 53 MPa for the PP/WP composites (for the same concentration). Another work produced laminate composites based on epoxy + WP (paper sheets) + woven jute, varying the stacking sequence and the layer content [ 91 ]. The WP composites provided the best mechanical properties compared to the jute composite and hybrid WP/jute composites, while the filler combinations (WP/jute) increased the stiffness of the composites. Electronic microscopy and acoustic emission analysis provided information on the failure mode of the composites during tensile and flexural tests.
Epoxy resin + WP composites were mixed with dammar natural resin (60–80%) and WP as paper sheets before and after shredding [ 90 ]. The results indicated that the tensile strength and modulus decreased with increasing dammar content. At the same time, the composites based on the WP sheets provided higher strength compared to the neat epoxy resin. The random distribution of the filler generated a lack of uniformity in the composite, where the tensile response was nonlinear for the shredded WP compared to linear for the WP sheets. Moreover, the damping properties of the material vibration were evaluated, showing an increase with enhanced dammar content, mainly for the composite with 80% dammar and shredded WP. The authors concluded that these hybrid composites based on shredded WP could be applied in the medical field as a material for fracture or sprain immobilization products. In contrast, hybrid composites based on WP sheets could be applied in the automotive industry for indoor products.
A recent work focusing on the environmental concerns caused by waste plastics developed a composite material from waste LDPE, WP, and epoxy resin [ 61 ]. Three formulations were evaluated, keeping the epoxy content (40%) but varying the WP (20–30%) and LDPE (30–40%). The results indicated that 20% WP and 40% LDPE improved tensile strength (17%) and water resistance (70%), while 25% WP and 35% LDPE improved flexural properties (15%) and stiffness (145%). Another work investigated the surface printability of the epoxy or polyester + WP (sludge) or cardboard waste composite plate [ 89 ]. The prints were made with water, solvent- and UV-based inks for a single color (cyan). The solvent-based and UV-based inks provided permanent surface adhesion, mostly observed for the WP composites, because of better ink adhesion than the cardboard composites. Epoxy/WP composites presented higher density than the polyester-based and cardboard-based composites, for which the density value was most significant for the solvent-based ink print.
Table 9 presents an overview of the works published on WP-based epoxy composites for a quick reference and comparison of their properties.
Main mechanical properties found in epoxy composites.
3.2.6. Polyester Composites
It was reported that a polyester resin was mixed with WP as newspaper and kraft, with and without biaxially knitted glass fiber, in which the WP-kraft composite presented higher tensile strength (29%), ductility (109%) and stiffness (8.5%) but a similar impact strength to the WP-newspaper composite [ 95 ]. As expected, the knitted glass fiber composite significantly improved both composites’ mechanical properties, such as WP-kraft composite tensile strength (133%). The authors stated that the WP-kraft behavior was related to its hydrophilic nature, promoting better adhesion with the polyester resin. The polyester resin and WP-as-newspaper (25, 33, and 48%) laminate composites were also produced via hand lay-up as a low-cost raw reinforcement [ 94 ]. The mechanical results showed that the tensile strength increased as the amount of WP increased in the fiber’s direction (44.5 MPa for the WP 25% composite and 68.6 MPa for the WP 48% composite). In contrast, tensile strength decreased as the amount of WP increased in the cross direction (22.9 for the 25% WP composite and 19.1 for the 48% WP composite).
Water swelling properties were investigated in polyester/WP composites (25, 34, and 50 wt.%), indicating that water absorption and thickness swelling increased as the amount of WP increased [ 93 ]. Moreover, the mechanical performance of dry and wet composites was tested, showing that all the mechanical properties were lower for wet composites, being more significant for the 50 wt.% WP composites with a reduction of 40% in tensile strength and 50% in stiffness. Another work from the same authors evaluated the jute addition on polyester/WP laminate composites [ 47 ]. They reported improved mechanical properties regarding the polyester/WP composite, mainly for the composite with two layers of jute and one layer of WP in contrast to the two layers of WP and one layer of jute (~20% enhancement for tensile and flexural strength).
Table 10 presents an overview of the works published on WP-based polyester composites for a quick reference and comparison of their properties.
Main mechanical properties found in the polyester composites.
3.2.7. Polyurethane (PU) Composites
PU/WP composites have only been reported recently. The first work reported PU and polyester mixed with WP and rice hulls, considering 80 v / v % of filler from which the composite plates were produced by compression molding [ 96 ]. The results showed that PU/WP presented the best water resistance performance. Moreover, PU/WP provides the highest mechanical properties compared to the other composites and neat PU. Compared to neat PU, PU/WP has a higher tensile strength (550%), stiffness (5000%), and hardness (12.5%), indicating that the flexible elastomeric PU became stiffer with the filler addition. The following article extracted cellulose nanocrystals from WP (WP-CNC) and filled waterborne PU composites to produce a transparent film via sonication after PU synthesis in-situ during PU synthesis [ 98 ]. The interaction among the hydrogen bonds between PU and WP-CNC was stronger for in-situ PU/WP-CNC than for sonicated PU/WP-CNC. Thermal stability was also improved for all the composites but sonicated PU/WP-CNC presented the most significant value. The authors concluded that both composites are applicable in medical and biological areas.
Another work studied waterborne PU mixed with cellulose nanocrystals (CNCs) from WP to produce membrane composites with two soaking times in water (20 s and 5 min) [ 97 ]. The CNCs were of the same quality as commercial cellulose but with higher thermal stability. Consequently, PU/WP-CNC composite membranes presented higher thermal stability than PU/commercial cellulose, for which the longer soaking time influenced better thermal properties. Additionally, a newer work compared WP-CNCs with microcrystalline cellulose and cellulose from waste cotton as reinforcement for PU composites [ 99 ]. The cellulose from WP provided a higher aspect ratio, crystallinity degree, and thermal stability than other cellulose sources. The significant interaction between PU and WP-CNC improved the composites’ thermal properties and stiffness.
Table 11 presents an overview of the works published on WP-based PU composites for a quick reference and comparison of their properties.
3.2.8. Polyvinyl Alcohol (PVA) Composites
PVA was filled with WP, wood dust, and sisal fiber keeping WP (25 wt.%) and PVA (10 wt.%) concentrations constant but varying the wood dust (20–40 wt.%) and sisal (25–45 wt.%) contents [ 42 ]. The density decreased as the amount of sisal fiber increased. At the same time, the flexural strength was optimum at 30 wt.% wood and 35 wt.% sisal. The water absorption result indicated that a higher volume of sisal caused more significant water absorption. However, the most water-resistant composite was 30 wt.% wood and 35 wt.% sisal, as with the flexural results.
A second work investigated the effect of WP filler on epoxy resin, PP, and PVA composites regarding water absorption performance. In this case, injection molding and casting produced two types of PVA (GF 4–86 and 4–88) [ 74 ]. The results showed that epoxy/WP (3 wt.%), PP/WP/MAPP (30 wt.% and 4 wt.%), and casting/molded 4–88 PVA/WP (30 wt.%) provided lower moisture content, mainly for the PP and PVA composites. The authors concluded that molded 4–88 PVA/WP was the best composite with the optimum production method, good interfacial adhesion between the polymer/filler, and high crystallinity degree.
Table 11 presents an overview of the works published on WP-based PVA composites for a quick reference and comparison of their properties.
3.2.9. Other Composites
Although conventional, well-known, and general polymeric composites have already been discussed, other synthetic and natural polymers were noticed at least once in the literature. Most of them were recently studied and published, being the reference for future research. One interesting recent work reviewed the novelty of cellulose-based materials, including WP as a rich-cellulose source, mostly applied to polymeric composites to improve their properties [ 100 ].
Some works reported some results on composites made from cellulose (WP-extracted). The starch-based composite was filled with nanocellulose from WP and commercial nanocellulose, from which the mechanical properties increased as the filler content increased (5–20 wt.%). However, the values were lower than for the starch-based commercial nanocellulose composites [ 18 ]. Nanocellulose from WP was also mixed with a guar gum film composite, indicating that the 4 wt.% nanocellulose composites provided the highest mechanical behavior with tensile strength (172%) and elongation (101%), compared to the neat guar gum film but stiffness (154%) was better for the 10 wt.% nanocellulose composite [ 22 ]. In another work, the cellulose from WP was mixed with chitosan and methyl red to obtain a composite film. The cellulose was successfully tested as a substrate for a colorimetric sensor. It indicates that these composite films could be used to detect food spoilage [ 101 ]. Furthermore, a novel work used cellulose from WP as a filler for a polypyrrole/graphene composite for supercapacitor electrodes. The cellulose addition promoted a higher specific capacitance (318%), power density, and energy density than neat polypyrrole, being suitable as an electrolyte tank [ 102 ].
Carboxymethyl cellulose and sodium alginate were mixed with WP to develop a biodegradable film to replace conventional packaging films with good mechanical properties and water vapor permeability [ 103 ]. Additionally, cassava starch was used with WP/bamboo and WP/rice husk. The composites with increased WP content presented a lower density and higher compression strength, suitable for construction blocks [ 104 ]. Composites based on maleated PVA, natural rubber graft cassava starch, modified cassava starch, and natural rubber/cassava starch filled with WP/sugar cane stalk were compared using different contents [ 41 ]. The impact strength and hardness increased as the polymers increased, while the swelling ratio decreased, concluding that mixed natural rubber/cassava starch composite provided the best physicomechanical performance.
Polyethylene terephthalate-1,4-cyclohexanedimethanol ester (PETG) was also filled with WP modified with an alkyl-ketene-dimer (AKD) and silane coupling agents (KH 550, 560, and 570). The optimum filler content was found to be 10 wt.%, and KH 550 was the most efficient for improving the composite’s performance by enhancing the mechanical properties and water resistance [ 105 ]. Moreover, a superabsorbent composite was studied using polyaspartic acid (PASP) with WP and 2-acrylamide-2-methyl-1-propanesulfonic acid graft with copolymerized acrylic acid. The results showed that the composite presented a high water absorbance, water retention, acid/base resistance, and salt resistance, leading to an adaptation in different environmental conditions [ 106 ].
To complete this review, Table 11 presents an overview of the works published on WP-based PU, PVA, and others composites for a quick reference and comparison of their properties.
Main mechanical properties found in the PU, PVA, and other composites.
1 silane coupling agent.
4. Prospects
The studies included in this review used WP in different ways. Therefore, future works should still investigate new polymeric matrices different from conventional synthetic polymers, for which the composite materials will cause minimal or no environmental impact. Nowadays, several discussions on evaluating the environmental impacts, environmental footprint, and circular economy are included in any new development. Although a life cycle assessment (LCA) of the end-of-life of WP was published [ 107 , 108 ], none were found for WP composites. Some studies stated that WP composites are environmentally friendly materials but use many synthetic and/or virgin polymers. At the same time, no report was found on their impacts during and after their lifetime. Investigating composites’ end-of-life (via LCA), such as recycling and degradation, would be highly valuable. In addition, recycled and biobased polymers must be tested, especially to account for biodegradable biopolymers to resolve some of the environmental issues.
WP was reported to be a raw material for PHA synthesis. Future works could be carried out using PHA from WP in composites filled with WP, leading to an integrated biodegradable material with 100% materials from WP. Also, PHBV could be used in WP composites and PU foams. WP, as a cellulose-rich material, could positively affect PU foams’ stiffness and porous structure in terms of cell size and density. Biobased PU should be a priority and NR for more elastic applications.
Finally, new applications should be considered for WP composites to support material characterization. Three-dimensional printing is an outstanding and costly technology based on commercial filaments from PP, PLA, or acrylonitrile-butadiene-styrene (ABS). These filaments can be filled with natural fibers to obtain positive effects. Therefore, WP composites could be made based on PP or PLA filaments, influencing the material cost and performance.
5. Conclusions
The recent trends in polymeric composites were revised and critically discussed. A systematic review was performed using the two most important databases in the field. A total of 75 documents were found and discussed, highlighting their main conclusions and novelties concerning WP composite properties and application possibilities. These data provided valuable quantitative information about the number of documents, countries, keywords, and citations, indicating the scientific relevance of the subject and the gaps for future research.
The systematic bibliographic review showed that petro-based PP and PE had been vastly reported with WP filler with good physicomechanical properties depending on the filler content. In contrast, PLA is a biobased polymer but presented fewer publications with much higher citations, highlighting the scientific relevance of the PLA/WP composites. The keyword analysis showed that mechanical properties and recycling are the most frequent clusters, which were found in the discussion of the papers ( Section 3.2 ).
Therefore, WP is a valuable cellulose-rich material that can be used for several applications, positively affecting the composite field. It is generally used as a reinforcement to improve mechanical properties or as a filler for enhancing water resistance, rheological properties, and thermal properties. Although several works have already been published, there are some new possibilities to fill the gaps observed in this review, and this should be a source of many works in the near future.
Acknowledgments
The authors would like to acknowledge Université Laval and São Paulo State University for their administrative and technical support.
Funding Statement
This research was funded by Fundação de Amparo à Pesquisa do Estado de São Paulo (FAPESP), grant: 2019/02607-6 and 2020/02361-4 and Coordenação de Aperfeiçoamento de Pessoal de Nível Superior-Brazil (CAPES), finance code, 001, and grant number, 88887.495399/2020-00.
Author Contributions
Conceptualization, D.M.d.O. and A.S.C.d.B.; methodology, D.M.d.O. and A.S.C.d.B.; validation, K.C.C.d.C.B., M.O.H.C. and H.J.C.V.; formal analysis, H.J.C.V. and D.R.; investigation, D.M.d.O. and A.S.C.d.B.; resources, D.M.d.O. and A.S.C.d.B.; data curation, D.M.d.O. and A.S.C.d.B.; writing—original draft preparation, D.M.d.O.; writing—review and editing, A.S.C.d.B., K.C.C.d.C.B., M.O.H.C., H.J.C.V. and D.R.; visualization, D.M.d.O. and K.C.C.d.C.B.; supervision, D.R. and H.J.C.V.; project administration, D.M.d.O.; funding acquisition, D.M.d.O. All authors have read and agreed to the published version of the manuscript.
Conflicts of Interest
The authors declare no conflict of interest.
Disclaimer/Publisher’s Note: The statements, opinions and data contained in all publications are solely those of the individual author(s) and contributor(s) and not of MDPI and/or the editor(s). MDPI and/or the editor(s) disclaim responsibility for any injury to people or property resulting from any ideas, methods, instructions or products referred to in the content.
Advertisement
Recycling Efficiencies in Japan’s Administrative Regions: Findings from Network Data Envelopment Analysis
- Original Paper
- Published: 20 May 2023
- Volume 4 , pages 1–21, ( 2024 )
Cite this article
- Jin-Li Hu ORCID: orcid.org/0000-0002-7337-2935 1 ,
- Satoshi Honma 2 &
- Tzu-Min Chang 1
204 Accesses
Explore all metrics
Recycling is an essential part of circular economy. This research constructs a two-stage waste generation and recycling activity model, selecting Japan as a case study object to explore its recycling efficiencies through this model. Japan’s regional recycling efficiency is assessed in two stages: waste collection as stage 1 and the treatment and process of the recycling waste as stage 2. We adopt a network data envelopment analysis (DEA) model by Tone and Tsutsui (2009) to measure the recycling efficiencies of 47 administrative regions in Japan, taking in account multiple inputs and outputs from 2013 to 2017. The empirical results indicate that the efficiency of stage one (waste collection) performs worse than that of stage two (treatment and process of recyclables). The metropolitan regions consistently outperform the rural regions, because the metropolitan regions perform better in stage one (waste collection). Local governments should improve the waste collection by co-working with local communities and volunteer groups. All regions perform relatively more efficiently in stage 2 (waste processing).
This is a preview of subscription content, log in via an institution to check access.
Access this article
Price includes VAT (Russian Federation)
Instant access to the full article PDF.
Rent this article via DeepDyve
Institutional subscriptions
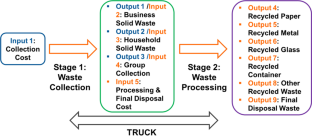
Similar content being viewed by others
Measuring the waste footprint of cities in japan: an interregional waste input–output analysis.
Makiko Tsukui, Shigemi Kagawa & Yasushi Kondo
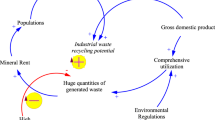
Measuring the recycling potential of industrial waste for long-term sustainability
Qudsia Kanwal, Xianlai Zeng & Jinhui Li
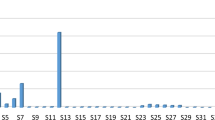
Identifying key areas for circular economy: a waste collection input–output analysis in Vietnam
Yen Thi Ta, Tuyet Thi Anh Nguyen & Nam Hoang Nguyen
Data Availability
Available based on reasonable requests.
The classification here is for convenience only. Rural municipalities exist even in large metropolitan areas.
Although Honma and Hu [ 23 ] also evaluate efficiency for recycling, their data is municipality-level. Hence, we compare our results with Ichinose et al. [ 14 ].
References
Allwood JM (2014) Squaring the circular economy: the role of recycling within a hierarchy of material management strategies. Handbook of recycling: state-of-the-art for practitioners, analysts, and scientists. Elsevier, pp 445–477
Google Scholar
Li D, Wang MQ, Lee C (2020) The waste treatment and recycling efficiency of industrial waste processing based on two-stage data envelopment analysis with undesirable inputs. J Clean Prod 242:118279. https://doi.org/10.1016/j.jclepro.2019.118279
Article Google Scholar
Sun J, Li G, Wang Z (2019) Technology heterogeneity and efficiency of China’s circular economic systems: a game meta-frontier DEA approach. Resour Conserv Recycl 146:337–347. https://doi.org/10.1016/j.resconrec.2019.03.046
Tsai TH (2008) The impact of social capital on regional waste recycling. Sustain Dev 16(1):44–55. https://doi.org/10.1002/sd.326
Article MathSciNet Google Scholar
Nakano M, Managi S (2012) Waste generations and efficiency measures in Japan. Environ Econ Policy Stud 14:327–339. https://doi.org/10.1007/s10018-012-0038-2
Ministry of the Environment Japan (2014) History and current state of waste management in Japan. Tokyo. Retrieved from https://www.env.go.jp/en/recycle/smcs/attach/hcswm.pdf . Accessed 18 Nov 2020
Bongers A, Casas P (2022) The circular economy and the optimal recycling rate: a macroeconomic approach. Ecol Econ 199:107504. https://doi.org/10.1016/j.ecolecon.2022.107504
Aarikka-Stenroos L, Kokko M, Pohls EL (2023) Catalyzing the circular economy of critical resources in a national system: case study on drivers, barriers, and actors in nutrient recycling. J Clean Prod 397:136380. https://doi.org/10.1016/j.jclepro.2023.136380
Article CAS Google Scholar
Forastero ÁG (2023) Resources, conservation & recycling advances circular economy in Andalusia: a review of public and non-governmental initiatives. J Clean Prod 397:136380. https://doi.org/10.1016/j.rcradv.2023.200133
Shah MU, Rezai R (2023) Public-sector participation in the circular economy: a stakeholder relationship analysis of economic and social factors of the recycling system. J Clean Prod 400:136700. https://doi.org/10.1016/j.jclepro.2023.136700
Lahcen B, Eyckmans J, Rousseau S, Dams Y, Brusselaers J (2022) Modelling the circular economy: introducing a supply chain equilibrium approach. Ecol Econ 197:107451. https://doi.org/10.1016/j.ecolecon.2022.107451
Tripathy A, Bhuyan A, Padhy RK, Mangla SK, Roopak R (2023) Drivers of lithium-ion batteries recycling industry toward circular economy in industry 4.0. Comput Ind Eng 179:109157
Wang D, Ponce P, Zhang Y, Ponce K, Tanveer M (2022) The future of industry 4.0 and the circular economy in Chinese supply chain: in the era of post-COVID-19 pandemic. Oper Manag Res 15:342–356. https://doi.org/10.1007/s12063-021-00220-0
Ichinose D, Yamamoto M, Yoshida Y (2013) Productive efficiency of public and private solid waste logistics and its implications for waste management policy. IATSS Res 36:98–105. https://doi.org/10.1016/j.iatssr.2013.01.002
Callan SJ, Thomas JM (2001) Economies of scale and scope: a cost analysis of municipal solid waste services. J Land Public Util E 77(4):548–560. https://doi.org/10.2307/3146940
Bohm RA, Folz DH, Kinnaman TC, Podolsky MJ (2010) The costs of municipal waste and recycling programs. Resour Conserv Recycl 54:864–871. https://doi.org/10.1016/j.resconrec.2010.01.005
Hu JL, Chang TP, Kao CH (2008) Four-in-one waste recycling performance of local governments in Taiwan. J Resour Energy Dev 5(2):83–94. https://doi.org/10.3233/RED-120052
Marques RC, da Cruz NF, Carvalho P (2012) Assessing and exploring (in)efficiency in Portuguese recycling systems using non-parametric methods. Resour Conserv Recycl 67:34–43. https://doi.org/10.1016/j.resconrec.2012.07.005
Rogge N, De Jaeger S (2012) Evaluating the efficiency of municipalities in collecting and processing municipal solid waste: a shared input DEA-model. Waste Manag 32(10):1968–1978. https://doi.org/10.1016/j.wasman.2012.05.021
Article PubMed Google Scholar
Crociata A, Mattoscio N (2015) Output-orientated data envelopment analysis for measuring recycling efficiency: an application at Italian regional level. Environ Educ Res 22(4):551–570. https://doi.org/10.1080/13504622.2015.1015494
Chang DS, Liu W, Yeh LT (2013) Incorporating the learning effect into data envelopment analysis to measure MSW recycling performance. Eur J Oper Res 229(2):496–504. https://doi.org/10.1016/j.ejor.2013.01.026
Wu H, Shi Y, Xia Q, Zhu W (2014) Effectiveness of the policy of circular economy in China: a DEA-based analysis for the period of 11th five-year-plan. Resour Conserv Recycl 83:163–175. https://doi.org/10.1016/j.resconrec.2013.10.003
Honma S, Hu JL (2021) Cost efficiency of recycling and waste disposal in Japan. J Clean Prod 284:125274. https://doi.org/10.1016/j.jclepro.2020.125274
Gennitsaris S, Sagani A, Sofianopoulou S, Dedoussis V (2023) Integrated LCA and DEA approach for circular economy-driven performance evaluation of wind turbine end-of-life treatment options. Appl Energy 339:120951. https://doi.org/10.1016/j.apenergy.2023.120951
Djordjević B, Maitra R, Ghosh B (2023) Environmental efficiency assessment of Dublin Port using two-stage non-radial DEA model. Marit Transp Res 4:100078. https://doi.org/10.1016/j.martra.2022.100078
Yang H, Zhang X, Liu B, Huang Y (2023) Evaluation of green low-carbon innovation development efficiency: an improved two-stage non-cooperative DEA model. J Clean Prod 400:136662. https://doi.org/10.1016/j.jclepro.2023.136662
Tone K, Tsutsui M (2009) Network DEA: a slacks-based measure approach. Eur J Oper Res 197(1):243–252. https://doi.org/10.1016/j.ejor.2008.05.027
Tone K (2001) A slacks-based measure of super-efficiency in data envelopment analysis. Eur J Oper Res 143(1):32–41. https://doi.org/10.1016/S0377-2217(01)00324-1
Seiford LM, Zhu J (1999) Profitability and marketability of the Top 55 US commercial banks. Manage Sci 45:1270–1288. https://doi.org/10.1287/mnsc.45.9.1270
Peteraf MA (1993) The cornerstones of competitive advantage: a resource-based view. Strateg Manag J 14(3):179–191. https://doi.org/10.1002/smj.4250140303
Honma S, Hu JL (2018) A meta-stochastic frontier analysis for energy efficiency of regions in Japan. J Econ Struct 7:21. https://doi.org/10.1186/s40008-018-0119-x
Chifari R, Lo Piano S, Matsumoto S, Tasaki T (2017) Does recyclable separation reduce the cost of municipal waste management in Japan? Waste Manage 60:32–41. https://doi.org/10.1016/j.wasman.2017.01.015
Mann HB, Whitney DR (1947) On a test of whether one of two random variables is stochastically larger than the other. Ann Math Statist 18(1):50–60. https://doi.org/10.1214/aoms/1177730491
Iyer ES, Kashyap RK (2007) Consumer recycling: role of incentives, information, and social class. J Consum Behav 6(1):32–47. https://doi.org/10.1002/cb.206
Shah A, Yu Z, Tanveer M, Ali W, Saleem AR (2023) Effect of product assortment, internet of things, order fulfillment, green on purchase intention through the mediating role of shopping assistance. J Adv Manuf Syst 22(1):123–147. https://doi.org/10.1142/S0219686723500075
Lu LC, Chiu SY, Chiu YH, Chang TH (2022) Three-stage circular efficiency evaluation of agricultural food production, food consumption, and food waste recycling in EU countries. J Clean Prod 343:130870. https://doi.org/10.1016/j.jclepro.2022.130870
Zhang L, Du X, Chiu YH, Pang Q, Wang X, Yu Q (2022) Measuring industrial operational efficiency and factor analysis: a dynamic series-parallel recycling DEA model. Sci Total Environ 851:158. https://doi.org/10.1016/j.scitotenv.2022.158084
Yamamoto M, Kinnaman TC (2022) Is incineration repressing recycling? J Environ Econ Manage 111:102593. https://doi.org/10.1016/j.jeem.2021.102593
Download references
Acknowledgements
We thank an editor and two anonymous referees of this journal, seminar participants at annual meetings of the Taiwan Economic Association and Asian Association of Environmental and Resource Economics for their valuable comments.
The first two authors gratefully acknowledge financial support from Taiwan’s Ministry of Science and Technology (MOST108-2410-H-009–039) and the Japan Society for the Promotion of Science (JSPS) KAKENHI Grant Number 19K01659, respectively.
Author information
Authors and affiliations.
Institute of Business and Management, National Yang Ming Chiao Tung University, 118, Sec. 1, Chung-Hsiao W. Rd., Taipei City, 10044, Taiwan
Jin-Li Hu & Tzu-Min Chang
School of Political Science and Economics, Tokai University, Kanagawa, Japan
Satoshi Honma
You can also search for this author in PubMed Google Scholar
Contributions
Conceptualization, J.L.H. and S.H.; methodology, J.L.H.; software, J.L.H. and T.M.C.; validation, J.L.H. and S.H.; formal analysis, J.L.H, S.H., and T.M.C.; investigation, T.M.C. and M.Y.C.; resources, J.L.H.; data curation, T.M.C.; writing—original draft preparation, T.M.C.; writing—review and editing, J.L.H. and S.H.; visualization, S.H. and T.M.C.; supervision, J-L.H. and S.H.; and project administration, J.L.H. All authors have read and agreed to the published version of the manuscript.
Corresponding author
Correspondence to Jin-Li Hu .
Ethics declarations
Ethics approval and consent to participate, consent for publication, competing interests.
The authors declare no competing interests.
Rights and permissions
Springer Nature or its licensor (e.g. a society or other partner) holds exclusive rights to this article under a publishing agreement with the author(s) or other rightsholder(s); author self-archiving of the accepted manuscript version of this article is solely governed by the terms of such publishing agreement and applicable law.
Reprints and permissions
About this article
Hu, JL., Honma, S. & Chang, TM. Recycling Efficiencies in Japan’s Administrative Regions: Findings from Network Data Envelopment Analysis. Circ.Econ.Sust. 4 , 1–21 (2024). https://doi.org/10.1007/s43615-023-00274-1
Download citation
Received : 13 November 2022
Accepted : 07 May 2023
Published : 20 May 2023
Issue Date : March 2024
DOI : https://doi.org/10.1007/s43615-023-00274-1
Share this article
Anyone you share the following link with will be able to read this content:
Sorry, a shareable link is not currently available for this article.
Provided by the Springer Nature SharedIt content-sharing initiative
- Recycling efficiency
- Slacks-based measure (SBM)
- Network SBM-DEA
- Waste management
- Waste collection
- Find a journal
- Publish with us
- Track your research
What can be recycled? Your guide to recycling paper, plastic, glass, aluminum and more.

According to the Environmental Protection Agency, almost 94 tons of municipal solid waste were recycled and composed in 2018 – about 32%. But there's also the looming issue of contamination: The material collected for recycling that is not recyclable. About 17% of community-collected recycling is contaminated , a 2020 Recycling Partnership report found.
Earth Day is in just a few weeks making it a timely month to learn about recycling. Here are some tips to keep handy the next time you're throwing out a container, piece of paper or odd household item.
What is recycling?
Recycling is collecting and reusing material that would otherwise be thrown away. In the U.S., this happens in a three-part process:
- Collection: Recyclable materials are gathered by individuals or businesses and sent away
- Processing: Recyclables are sorted, cleaned and prepared for a facility
- Remanufacturing: Recyclables are made into new products at a plant or facility
Where does recycling go?: Inside the plastics problem in the U.S.
Does recycling actually work?
Recycling has important environmental and community benefits. Outside of reducing landfill waste, recycling prevents pollution and further greenhouse gas emissions because discarded goods can be made into new ones.
Recycled steel saves 60% of production energy and recycled plastics save 70% of production energy, according to the National Institute of Health's Environmental Management System.
Unfortunately, much of the burden of recycling falls on the consumer who is responsible for interpreting labels and figuring out what to throw in the bin. The U.S. doesn't have a federal recycling program, leaving towns to decide on local recycling measures, including the types of plastics they are able to collect and recycle. And because many of the items that end up in the recycling stream aren't actually recyclable, the contamination will often go to the landfill.
In 2016, about half the plastic waste collected in the U.S. was shipped internationally, but somewhere between 25-75% of it was inadequately managed, a Science Advances study found. Only 9% of all plastic waste ever created has been recycled.
How2Recycle is trying to change this. Born out of environmental nonprofit GreenBlue, How2Recycle partners with companies to provide standardized labels that show consumers how to recycle the packaging.
"The recycling system in the U.S. is fragmented and complex and has much room for improvement," How2Recycle Director Karen Hagerman wrote in an email to USA TODAY. "A national approach needs to be paired with efforts to move towards consistency of materials and formats accepted and processed, which would increase the accuracy of labels and further reduce consumer confusion."
How to recycle
Here’s a general guide to what can and can’t be recycled according to the EPA. Your state or city may have different recycling guidelines ,make sure to check these beforehand so your recycling is accepted.
"A lot of contamination comes from good intentions," Hagerman said. "We want to believe that the material we're disposing of could go to better use if they are recycled."
In general, paper needs to be dry and free of food scraps in order to be recyclable. You do not need to remove staples, labels or stickers from paper products – this is done in the recycling process.
Usually recyclable:
- Pizza boxes (even if they have grease on them)
- Mail (even with plastic windows)
- Cardboard boxes and containers
- Cardboard roll from toilet paper
- Paper with ink on it
- Cardboard tubes from toilet paper or paper towel
Usually not recyclable :
- Hygiene or sanity products (tissues, napkins, wipes, paper towels)
- Toilet paper
- Waxed paper
- Shredded paper
- Sticky notes or stickers
- Plastic-coated paper
Sometimes recyclable:
- Wrapping paper: Gift wrap with shiny or laminated coats cannot be recycled
- Takeout containers: As long as food scraps and residue are cleaned off
- Brown paper bags: As long as they are free of food scraps and don’t have a glossy, plastic coat
- Shredded paper: It depends on your local recycling program, but it’s less likely to get a new life at a recycling facility because of its shortened paper fibers
Plastics are trickier because there are so many different types used to make household goods. Plastic containers usually have a triangle with a resin number somewhere on the packaging that shows how they were made. Compare this symbol to your local recycling guidelines to find out if it’s eligible for recycling in your community.
Note these two types of plastic that typically cannot be recycled in household bins:
- Plastic bags, wraps and films (recyclable but only through participating programs like retail and grocery stores)
- Styrofoam (usually not recyclable, though some places accept it)
You cannot recycle compostable plastics, which disrupt the recycling stream.
Glass food and beverage containers are an important part of the recycling process because they can be reused several times and are a cheaper way to make new glass.
Glass of different colors and types can be mixed together, as long as you separate the glass from other materials like metal or plastic caps. You should not include broken glass in your recycling practices, which can harm workers and machinery.
Aluminum cans and foil can both be recycled as long as they do not contain food residue. According to the EPA, you do not need to crush aluminum cans before recycling because they can even be more difficult to sort at single-stream recycling facilities.
Paper, glass, plastic and aluminum aren't the only things that can be recycled. Here’s a guide to some other common household waste and whether you can throw it in the recycling bin:
- Batteries: Can be recycled but should not go in household garbage or recycling bins. Instead, drop batteries off at local collection points .
- Electronics: Can be dropped off at specific collection sites to be recycled or donated
- Metal: Check your state or city for local metal recycling programs
- Food: Cannot be recycled, but can be composted at home or at dropoff sites
- Yard trimmings: Cannot be recycled, but can be composted at home or at dropoff sites
- Used oil: Should not be disposed of in the drain because of its toxicity, but can be recycled at a local facility to be reused
- Paint: Cannot be recycled and is harmful to pour down the drain or throw away in the trash. Look for local donation sites or household hazardous waste facilities.
- Light bulbs: Cannot be recycled and is harmful to throw away in the trash. Check local recycling facilities or retail stores with recycling programs.
- Barometers and thermometers: Some can be considered household hazardous waste, so avoid tossing them in the trash. Instead, check household hazardous waste or local recycling facilities.
- Dirty diapers: Flush solid waste down the toilet, then place the diaper in the trash
- Clothes and shoes: Check local charities and donation sites, including retail stores
How and where to recycle in your city:
The U.S. does not have a federal recycling program, so guidelines are locally specific. To search how and where to recycle in your community, use Earth911’s recycling database or Keep America Beautiful’s “I Want to Be Recycled” and filter by zip code and type of material.
Hagerman's recommendations for recycling go beyond your household bins:
"Be conscious of what you buy – reducing consumption and looking for reusable options are also effective solutions, as is choosing products with overall lower environmental impacts," she said.
Don't recycle those books!: Here's where you can donate near you
Just Curious for more? We've got you covered
USA TODAY is exploring the questions you and others ask every day. From "What is a hybrid car?" to "How much caffeine is dangerous?" to "What is the smallest continent?" , we're striving to find answers to the most common questions you ask every day. Head to our Just Curious section to see what else we can answer for you.
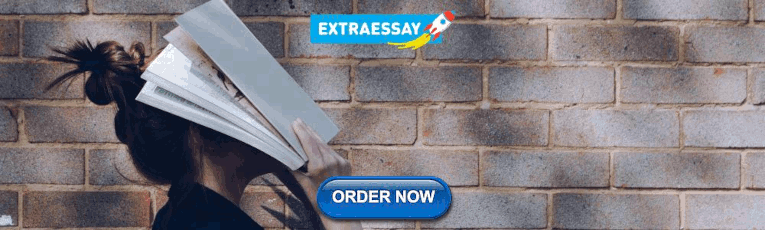
IMAGES
VIDEO
COMMENTS
The research related to paper recycling is therefore increasingly crucial for the need of the industry. ... For example the high value of opacity is need at the printing papers, but opacity of translucent paper must be lower. The paper producer must understand the physical principles of the paper structure and to determine their characteristics ...
1. Introduction. Paper recycling is one of the most well-established recycling schemes applied to waste materials today. Recycled paper is an integral part of paper and pulp production, with estimated utilisation for recycling in Europe of about 72% in 2012 (an increase of 20% from 2000) (CEPI, 2013a).In addition to recycled paper being an important raw material for the paper industry (CEPI ...
basis for further research in relation to pa per characteristics and paper recycling. The 157 The 157 substances identified in Step 2 are grouped in th e following according to their chemical ...
The waste paper recycling market was valued at US$ 37,529.60 m illion in 2018 and is ex pected to grow at. a CAGR of 4.7% from 2019 to 2027 to rea ch US$ 56,140.38 million by 2027. [10 ...
Tokyo 108-0023, Japan. 2 School of Environment and Society, Tokyo Institute of Technology, 3-3-6 Shibaura, Minato-ku, Tokyo 108-0023, Japan. * Correspondence: [email protected] or tsuchimoto ...
Offices use approximately 12.1 trillion sheets of paper per year, and paper accounts for 25% of landfill waste and 33% of municipal waste. It was found that each tonne of recycled paper allows for ...
Abstract. Recycling is a commonly acknowledged strategy to reduce the environmental impacts linked to primary resource exploitation. Large regional variations can be observed in recycling processes' parameters, like efficiency, energy mix and treatment of rejects. Life-cycle assessment (LCA) is widely used to evaluate the environmental ...
The corresponding figure for office paper production based on chemical pulp is for alternative 1 (virgin fibres): 2 tons of wood, 5 GJ of electricity and, after collection and energy production, 9 GJ of heat. If instead the office paper is recycled (alternative 2) the need of wood is 0.3 ton, electricity, 4.4 GJ and heat, 8 GJ.
2. Waste Paper: A Cellulose-Rich Material. The paper production life cycle includes the extraction of the raw material from the natural resource (pinus and eucalyptus reforestation trees) or the raw material from the recycled waste paper: postconsumer-collected (Figure 1) [].The life cycle is closed and environmentally correct when paper recycling is included in the system.
Target (1) in this research and development project was to increase recycling and reduce the production of waste. The driver (1) was legislation and the aim to decrease environmental impacts. The project reached the expected results (1); waste to landfill dramatically decreased and reuse increased. Figure 6.
Recycling is an international, peer-reviewed, open access journal on the recycling and reuse of material resources, including circular economy published bimonthly online by MDPI.. Open Access — free for readers, with article processing charges (APC) paid by authors or their institutions.; High Visibility: indexed within Scopus, ESCI (Web of Science), FSTA, Inspec, AGRIS, and other databases.
In recent months, both the solid waste industry press and mainstream media in the United States (including Fortune, the New York Times, Wall Street Journal, and the Washington Post) have called attention to the growing 'ills' of recycling (Davis, 2015; Groden, 2015; Whelan, 2015).In short, the common theme of these articles is that recycling in the USA has stalled and the situation is dire.
whether it's choosing paper over other materials, recycling or reusing paper products to help reduce waste altogether," Hansan added. The 2021 Consumer Recycling Habits survey is part of P+PB's broader initiatives on the benefits of paper recyclability, with sustainability messaging at the center. To learn more
Explore the latest full-text research PDFs, articles, conference papers, preprints and more on PAPER RECYCLING. Find methods information, sources, references or conduct a literature review on ...
The goal of this study was to assess the impact of the introduction of various waste management methods on the amount of greenhouse gas emissions from these activities. The assessment was carried out on the example of the Russian waste management sector. For this purpose, three scenarios had been elaborated for the development of the Russian waste management sector: Basic scenario, Reactive ...
Note that, a review of secondary studies is denoted as tertiary study. Present work contributes to the literature by providing an ample and organised view of the existing TRSC secondary research works. In this paper, we analyse review papers on TRSC through a systematic review process under a structured framework.
Recycling is an essential part of circular economy. This research constructs a two-stage waste generation and recycling activity model, selecting Japan as a case study object to explore its recycling efficiencies through this model. Japan's regional recycling efficiency is assessed in two stages: waste collection as stage 1 and the treatment and process of the recycling waste as stage 2. We ...
What cannot be reused directly, but can be recycled or recovered such as paper, plastic and mental, should be maximized for its value through recycling (Kurniawan et al., 2021c). Berlin charges every household a waste disposal fee based on the number and size of their trash bins, and the frequency of waste collection service ( Fig. S11 ).
In this experiment the best pulp was obtained at a ratio of 100 gram paper and 4 liters of water. The grammage value of the paperboard was 315.58 gm/m 2 , bulk was 2.535x10 -06 m 3 /gm., moisture ...
Here's a beginner's guide to recycling paper, plastic, glass, aluminum and more. Solar eclipse guide 😎 How to test them 👓 SC, Ala. sites look back Betty Ford honored
Scenario 6 with anaerobic digestion has a slightly higher EP compared to composting. In all scenarios studied, the impact from both paper production and recycling makes the largest contributions to EP due to the volume of wastewater and added chemicals. 3.2. Sensitivity analysis results. The results of two sensitivity analyses are shown in Fig. 6.
Battery recycling grants go toward research, collection U.S. Department of Energy identifies 17 projects related to battery recycling that will receive a combined $62 million in funding. "Recycling used batteries reduces demand for new materials and allows our domestic industry to produce at lower costs," says the U.S. Department of Energy.
while 27 tonnes MSW - municipal solid waste was. generated in 2013 alone; Recycling helps conserve natural resources, whereas, the office paper, recycled can save 27,300 liters of. water, 18 trees ...
The research mentioned in the statement focuses on investigating a theoretical method for calculating the residence-times distribution function (RTDF) in a periodically driven, bistable system subject to noise recycling. This situation deviates from a Markovian process due to the recycling lag, making it challenging to determine the RTDF using traditional two-state models. In this paper, the ...
Different microbial activities were also employed for the effective reduction of PW (ORA, 2015, Connor, 2014; Rahimi and García, 2017).PW recycling got momentum during the last few decades (De Weerdt et al., 2020).It was found that pyrolysis is a popular technique which is largely used because of lowering harmful emissions and lower carbon footprint of plastic goods (Shome, 2020).
The authors declare that they have no known competing financial interests or personal relationships that could have appeared to influence the work reported in this paper. Acknowledgments. This research did not receive any dedicated external financing. The authors express their sincere thanks to Mr. Peter Jones for his work reviewing the manuscript.